What Is Plastic Molding?
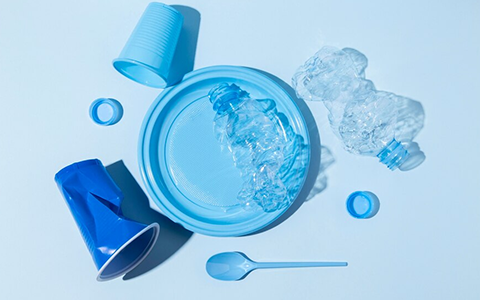
Every day, people come across various items made from plastic. They consume water from plastic water bottles without giving a second thought of how they are produced or made. Most people are unaware of different types of plastic molding. The following sections give a comprehensive guide to plastic molding.
Plastic molding refers to the process or mechanism of transforming plastic mold or granules into a definite solid shape. In other words, it means the creation of plastic objects into a final proper shape.
Simple molding or plastic molding is done using variations in heat and pressure. This dual combo of different heat and pressure levels results in the formation of various types of plastic objects, appliances, and products.
In the whole process, a frame called mold is placed. This cavity mold is the central object for shaping the plastic. The mold is designed based on the design of the final product. This mold is used multiple times to create numerous exact copies of the final product without quality defects.
A person can witness the result of the rigorous plastic molding in daily products or items like automotive parts, plastic toy cars, bottle caps, housing articles, machinery parts, agricultural products, and the list goes on.
There are various types of plastic molding varying on the basis of expenses, benefits, usage, heat requirements, etc. There is micro injection molding as well as molding on large scale. The evolution of plastic molding techniques has provided ease to manufacturers.
The History Of Plastic Molding
The history & evolution of plastic molding is impressive in how it was traditionally used. It can be traced back to the late 1800s when people required billiard balls made of plastic. Before that time, the players used to play the game using ivory billiard balls.
John Wesley Hyatt started making the plastic balls by putting celluloid material into a round-shaped mold. Later, he and his brother replaced this manual injection process with an automated machine, giving better efficiency to the molding process.
This was the first molding machine that included a standard plunger used for forcing the plastic into the mold using heat. Later in 1946, a person named James Hendry introduced the screw injection molding machine, which is commonly used presently.
Apart from these machines, rotational molding had its roots in 1855 when Britishers utilized heat and rotatory movement to make metal shells. This rich history is of molding. Plastic was introduced in the molding process in the 1950s used for manufacturing plastic doll heads.
Since then, various improvements and upgrades in technology have given new dimensions to plastic molding. Vivid plastic molding types have given manufacturers the convenience of trying new things with plastic injection molding. Whether it is medical equipment or a hollow toy, plastic molding is found everywhere.
What Are The Types Of Plastic Molding Process
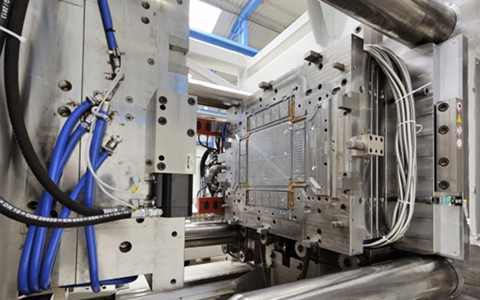
There are numerous plastic molding techniques. The following section gives a detailed overview of different types of plastic molding processes.
Injection Molding
Injection molding is one of the most basic molding processes, which is done by pushing the heated and molten plastic material into a mold using high pressure. After sticking to the mold, it is allowed to cool down and come out as a sturdy plastic object. The mold-making process is easier to follow in this case.
Application & Common Products
This molding technique is usually found in producing high-volume plastic products. There are different sizes of injection mold depending on the manufacturer’s needs. The most common products of this process are:
- Wire spools
- Packaging
- Bottle caps
- Automotive parts and components
- Toys
- Pocket combs
- Musical instruments and related components
- One-piece chairs and small tables
- Storage containers
- Mechanical parts like gears, etc.
Advantages
- It is a pocket-friendly option as the cost per part of the injection molding machine is significantly less.
- The manufacturer can make the same products repeatedly without any noticeable defects.
- It works very fast, maximizing productivity and minimizing one production cycle.
- It gives the molder more patterns and colors to print on the object.
- It gives an eco-friendly option as it incurs minimal wastage of plastic and other resources.
Disadvantages
- The tools needed for the injection molding process have high initial investment due to design and model requirements. Apart from this, high investment is needed for labor, material, etc.
- Designing and research can be time-consuming. It may take around five to six months to reach from the production concept to the designing stage.
- The designing of large injection molds needs high detailing.
Blow Molding
There are several famous molding techniques like cleanroom injection molding among many others. One of these is blow molding used for carving or producing hollow plastic objects. The resultant objects usually have a consistent thickness and possess unique shapes. In this process, the plastic material is injected into the mold using hot air that blows the material shaping it like a balloon.
The mold gives the balloon the desired shape. The after-process remains the same, i.e., cooling and removing the object from the mold. The technique is very effective as one production cycle consumes at most two minutes.
Application & Common Products
This technique is suitable for producing hollow objects in large quantities. The most commonly found products from this process include:
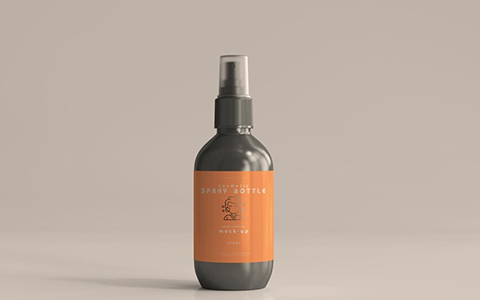
- Cooling system overflow containers
- Windshield washer fluid bottles
- Medical spray, water bottles, and items like medical plastic injection
- Hollow lightweight toys
- Oil storage and distribution containers
- Plastic bat or ball
Advantages
- An essential benefit of this technique is that it can prudence large volumes in quick succession.
- Many plastic applications have been derived from this technique, providing excellent scope for the technique.
- The machinery used in the processing is cheaper as compared to other machines.
- It reduces human errors as there is more automation involved in the process.
Disadvantages
- The machines require extreme quantities of petroleum for running smoothly. With decreasing supply, it can be a huge downside.
- This technique is not an environmentally-friendly option.
- They have limited uses as compared to their counterparts.
Compression Molding
Compression molding is a widely used technique where the manufacturer keeps the heated plastic material in a heated metallic mold. The mold is then closed to tighten the material, which is then cooled and expelled. The whole heating process is known as curing.
Application & Common Products
It is commonly used for replacing or exchanging metallic components with plastic parts. Moreover, it is best used for small components with high volumes. The most popular products of compression molding are mentioned below.
- Car tires
- Automotive parts
- Rubber tires
- Handles
- Electrical components
- Rubber gaskets or seals
Advantages
- The process is very straightforward and easy to follow.
- It does not require complex tools and machines to work.
- It is a decent technique to produce thick items.
- It is a pocket-friendly option while producing for short-term requirements.
Disadvantages
- There might be massive costs incurred on functions post molding.
- This technique has a comparatively slower processing time.
- It is not a good option for producing objects with complex designs.
Extrusion Molding
Extrusion molding is a molding technique that uses a unique die in place of mold to extract a full-fledged plastic object. The hot plastic material is made to go through the custom die, which determines the shape of the final item.
Application & Common Products
There is a limited scope of making products through extrusion molding. A person can find extrusion blow molding products having a consistent length throughout the body. Some of these products are listed below.
- Pipe/tubing
- Process of weatherstripping
- Fencing
- Deck railings
- Window frames
- Plastic films and sheeting
- Thermoplastic coatings
- Wire insulation
Advantages
- The cost of running extrusion molding machines is comparatively lesser than other molding techniques.
- This technique uses the cross-section function, which adds to the flexibility of using this molding process.
- After extruding the plastic material from the die, the molten material remains hot. It implies that a person can modify the shape or material even after the whole process.
Disadvantages
- The ejected plastic material tends to expand after the process. This makes the accuracy of the product size questionable. A person cannot predict the expansion degree easily.
- There is not a broad spectrum of products extrusion molding produces.
- The initial investment in setting up types of machinery for this technique is high.
Rotational Molding
Also known as rotomolding, rotational molding is a renowned molding process that involves forcing liquid material or resin into the metallic mold under extremely hot conditions. An oven is responsible for rotating the material, which stops once the inner portion of the mold is packed with resin.
Application & Common Products
This technique is appropriate for producing even-walled hollow products. There are numerous products made using this process, some shown below.
- Bulk containers
- Recycling bins
- Storage tanks
- Road cones
- Car parts & components
- Marine buoys
- Pet houses
- Kayak hulls
- Playground slides
Advantages
- Tools used in rotational molding are made of inexpensive materials like aluminum; therefore, the tooling cost in this process is low.
- As mentioned earlier, the technique results in even-walled products. Therefore, the chances of quality defects are much lower.
- There is minimal wastage during and after the process, as the materials can be re-used for further processing.
Disadvantages
- The time taken to complete one production cycle is very high.
- The cost of raw material used in this technique is also expensive.
- The products might result in quality defects due to the repeatability of metal used in rotomold.
- A manufacturer might incur high labor costs.
Thermoforming
This process is known for producing various high-demand items like laboratory consumables, industrial products, etc. In this molding technique, a thin sheet (thermoplastic) is heated to a certain level and gradually transformed into the desired shaped mold. This plastic sheet is very flexible in terms of vivid options in styles, patterns, and colors. It can also create 3D objects using unique mold designs. There are many benefits of using thermoforming, mentioned in subsequent sections.
Application & Common Products
Thermoforming is widely used for making plastic products of daily use like disposable cups, glasses, etc. Some of these products are listed below.
- Humidifiers
- Bus and train seats
- Computers and television cabinets
- Trunk liners
- Glove compartments
- Spoilers and hatchback window louvers
- Door panels
- Guards
- Window air conditioners
- Humidifiers
- Aircraft seat backing and armrests
Advantages
- The usage and scope of thermoforming are massive. It is used in various industries like transportation, interior designing, recreation, funeral making, etc.
- The technique is simpler as compared to other processes.
- Thermoforming yields premium quality products in a short span of time.
Disadvantages
- It can make products incorporating only thin-walled designs.
- People might experience uneven thickness in products.
- The plastic requirement is higher than other techniques.
- It falls on the expensive side of different molding types.
Casting
Casting refers to pushing or injecting liquid material into a mold, then hardened and ejected. The primary process in casting is the cooling function. It is the central part of obtaining the desired shaped item.
Application & Common Products
One of the most significant reasons for using this technique is to create highly complex plastic items which are otherwise typical to produce. A person can find various products made through casting, such as:
- Machine tool beds
- ships’ propellers
- Recreational vehicles
- Monitors
- Medical and surgical devices
- Traffic lights
- Trigger guards
- Industrial equipment
- Electrical housings
Advantages
- The most crucial benefit of casting is that it can produce complex-shaped plastic products.
- They can make products of any size, whether they are small or large.
- There is less wastage involved in the whole manufacturing process.
- As a result of minimal wastage, there is a significant reduction in overall cost.
Disadvantages
- The finishing or perfection level of the products is not always up to the mark.
- If a person is producing products on a large scale using this technique, it might be costly.
- Quality defects are easily noticeable (if any).
Spin Casting

In spin casting, the mold is round disc-shaped which rotates at the center with the liquid or plastic material in the cavity mold. It moves in a centrifugal motion at a constant speed till the material hardens. In this process, the mold is built of rubber. The motion is employed using the force of inertia. There is total quality assurance during this process.
Application & Common Products
Spin casting is a useful technique to create complicated items. The most popular plastic products made using the spin casting technique are named hereunder.
- Industrial products
- Decorative and novel items
- Fashion accessories
- Metals like pewter, zinc alloys, etc.
- Fishing tackle components
- Belt buckles
- Pins
- Emblems
- Medallions
- Trophies
- Assorted souvenirs
Advantages
- Products made through this casting type last longer than those made from other processes.
- It is the best choice for making detail-oriented products.
- It enables the manufacturer to create a product prototype faster.
- It carries a great cost advantage.
Disadvantages
- Successful execution of this technique requires skilled laborers.
- The product coverage is limited in spin casting.
- Massive investment is required in the whole manufacturing process.
Transfer Molding
Often confused with extrusion molding, transfer molding is the pressurizing of plastic material into the mold by initially passing through a compartment or chamber. It is more complicated than extrusion molding.
Application & Common Products
This type of molding is generally used for polymers and materials like Neoprene, epoxy, silicone, polyurethane, etc. There are numerous products made through this molding, some shown as follows.
- Integrated circuits
- Plugs
- Connectors
- Pins
- Coils
- Studs
- Electronics
Advantages
- It produces the final products in quick succession. The production cycle is shorter than other techniques.
- It has a great capacity to produce complicated plastic products which are difficult to manufacture using compression molding.
- It provides consistency throughout the process.
- The accuracy of products is incredible in this technique.
Disadvantages
- As compared to compression molding, this technique is more expensive.
- Although the overall productivity and production speed are impressive, it lags behind various injection mold techniques in the production cycle.
- Skilled labor is essential in this molding; therefore, recruitment can be time-consuming.
- There is a lot of manual work done throughout the manufacturing process. As a result, there are high chances of human errors.
Laminating
Laminating is a familiar process whereby two surfaces or packaged items are integrated with a solid binding agent. In other words, it helps in creating multi-layered plastic items. The strength is provided with the help of a special adhesive. This binding can enhance the overall look of the object. People use various types of lamination depending on their needs.
Application & Common Products
The most common products made through laminates are listed below.
- MDF
- Plywood
- Particle board
- Wooden furniture
- Wall panels
- Flooring
Advantages
- It provides more durable product options than other techniques.
- It safeguards products against scratches, marks, tears, dirt, etc.
Disadvantages
- They are sensitive to water damage. They are not water-resistant.
- It requires careful processing which can otherwise lead to warping.
Matrix Molding
Matrix molding is a unique technique that involves the material to adjust between the design prototype and a hard shell created initially. This technique is usually employed to make complicated shapes or patterns.
Application & Common Products
The most widely found products of matrix molding are:
- Glass objects
- Ceramic parts
- Medical devices and consumables
Advantages
- It can lead to the creation of products of complex shapes.
- They are used in many industries; therefore, has greater acceptability.
Disadvantages
- The assembly of technology requires a lot of time.
FRP Molding
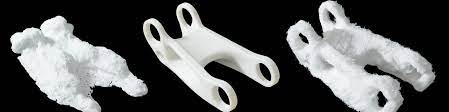
Fiber Reinforced Plastic involved in this type of molding refers to the rigid material comprising various individual fibers. The source of this FRP is polymer matrix such as epoxy, etc. It is obtained from various techniques like compression molding, wet layup, chopper gun, autoclave, filament winding, etc.
Application & Common Products
FRP molding is primarily used to strengthen the final product. It gives additional metallic strength. The most commonly found applications of this process are shown hereunder:
- Luxury automobiles
- Guardrails
- Signboards
- Drainage systems
- Bridge decks
- Business office furniture
- Household appliances
- Swimming pools
- Rain gutters
- Bathroom equipment
- Floating causeways
Advantages
- The efficiency rate is incredible while working with this molding process.
- The resin or shell composition can be modified according to the manufacturer’s needs.
- The products delivered are of rich quality.
Disadvantages
- Molding costs are very high in the FRP process.
- They are suitable for specific designed patterns or products.
- Although they give enormous strength to the product, they lack transverse strength.
Is Plastic Injection Molding Right For You?
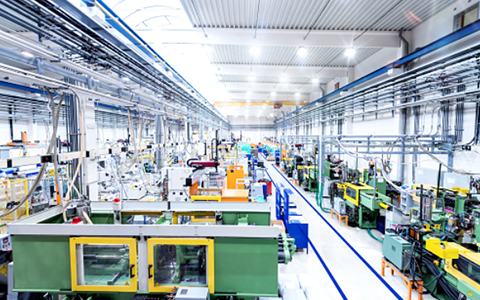
Many people think whether plastic molding is an appropriate option for them or not. If the injection molding material selection is done accurately, plastic molding is the right option for you. There are various reasons that indicate plastic injection molding is highly beneficial for you.These are outlined below.
- By using plastic molding, a person can produce plastic products ranging from small to large. They can create a small toy to a heavy appliance without much effort.
- Most molding techniques involve machinery and automation. As a result, there are lower labor costs incurred in the whole cycle.
- Different plastic injection molding techniques can produce a wide array of products. It caters to numerous industries like automotive, medical, aerospace, recreational, etc.
- There is minimal wastage in the injection molding process, contributing to eco-friendliness.
Factors That Need To Consider Before Plastic Injection Molding
There are various factors a person should consider while selecting a plastic injection molding company. Some of these factors are highlighted as follows.
- The designs and patterns of plastic products are very crucial nowadays. A person should know the expertise of the injection molding company in designing a product before finalizing them.
- Another crucial factor is the team’s production capacity and cycle time. It will help understand the approximate time required for dispatching a certain number of products.
- The techniques used for production are also a vital factor to consider. The most sophisticated technologies mean better expertise and fast delivery of products.
- It is better to ask for demo products in order to get an idea about product quality.
Where To Find A Proper Plastic Injection Molder For Medical Device Manufacturing?
The medical and pharmaceutical industry is a major buyer of plastic products. Plastic injection molding plays a massive role in determining the quality of treatment patients receive. Therefore, a proper medical molding company is necessary to ensure better quality products for the medical sector.
The most suitable injection molders are the ones that match their production standards with the industry-accepted norms. Apart from this, they should have minimal wastage and low cost. If you’re on the lookout for such services, contact SeaskyMedical now, and get the best services.