The cleanroom is the place that provides you with a protected area with airborne particulates. It has an area enclosed with several filters such as HEPA and ULPA mixture. These filters result from scientific research and circulate the outside air by removing excessive pollutants. This filter protects an area with microbes, dust, contaminants, aerosols, and other pollutants.
The cleanroom environment is usually necessary for medical organizations, pharmaceutical inventories, and scientific laboratories. On some platforms, cleanrooms are useful for electronic appliances and designed by effective cleanroom injection molding technology. The cleanroom effectively uses medically charged filters to protect against hazardous environmental influences. The filter in the cleanroom works on the various stages with the help of these filters.
Source:Unsplash
The cleanroom is the place designed for the retention of environmental microbial particles and dust particles. It levels and controls the variables like humidity, temperature, and airflow. It has the classified levels to protect the rooms from certain alien agents. Such a cleanroom environment can cover areas of different types and volumes. It assists in many streams and departments. What cleanroom defines its properties by the benefits and efficacies?
How does the cleanroom work?
The cleanroom can remove the airborne microbial, microscopic chemicals, and several hazardous pollutants. The working system of the cleanroom includes the proper cross air ventilation through the effective filter system. The filter system of the cleanroom has the HEPA and ULPA, which have the laminar and turbulent nature of the airflow system.
The laminar and turbulent phase airflow system works with a constant stream pushing the air downwards after filtration. The laminar airflow system is fixable across the ceiling area to provide constant filtration evenly throughout the room. It supports the unidirectional airflow from the filters.
The airflow system of the cleanrooms works, balancing the adequate amount of clean and fresh air with constant airflow with downstream air returning process. The horizontal designs of cleanrooms use the downstream airflow. When the airflow is in the vertical type of rooms, the returning of air uses the lower walls through the perimeter zones.
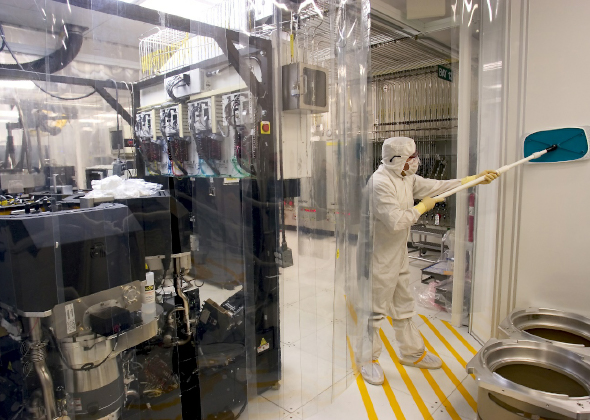
The outside air passes through the filter system attached to the cleanrooms. The filters have the technology of HEPA (highly efficient particulate air) and ULPA (ultra-low particulate air) technology. These filters clean the air as per their properties and specifications. The clean air is ejected into the cleanroom environment by an external force. The polluted air flows back to the environment through registers, or the filtration process continues according to the requirements.
The filtration process through the HEPA and ULPA depends on the ISO class of cleanrooms. The airflow velocity, pressure, direction, and type of air depend upon the class of cleanrooms. The HEPA filters provide their best performance in the ISO class 2-9 which cleans the pollutants of 0.3 to larger sizes. The ULPA filter performs best with the ISO class, which cleans the pollutants of ultra-low sizes.
Types of cleanrooms:
There are many types of cleanrooms based on various needs and departments. Many areas have varying requirements and are set up for cleanrooms. The different departments and infrastructure have variable use of the air filters of cleanrooms. It is why the filters in the clean are variably designed to increase the efficacy and performance of air filters. It increases the scope of using cleanroom technology in variable places. Here is the categorized description of the types of cleanrooms on various platforms:
- Based on application:
The categorization of the cleanrooms starts with its application phases. The types of cleanrooms are distinctively beneficial while using the variable application. These applications belong to many different uses of practices. So, let’s discuss the cleanroom categorically with their application properties in various areas. Here are the mentions:
- Medical device cleanrooms:
Medical devices are highly sensitive to outside dirt and microscopic bacterial pollutants. It is the reason these devices need a cleanroom with higher efficiency and manufacture through a medical plastic injection base. It is necessary to maintain the productivity and performance of medical equipment. It also prevents the spread of the infection to the patient while undergoing any medical test or procedure.
Cleanroom for medical devices varies from ISO- 1 to 9, which varies according to the size of the room and ratio of the proliferation of bacterial and other airborne pollutants. The ISO standard is divided according to the level of clean room air cleanliness. The lower the ISO value, the higher the air cleanliness. ISO class 1 cleanliness is the strongest, which means that the particle size of the dust is less than 10/m3. Contamination from the air is preventable with the HEPA and ULPA technology in the medical device cleanrooms. These filters’ FFU (fan filtration unit) cleans the rooms with positive pressure and technology. It also ejects the unfiltered air back into the environment. The cleanrooms supporting the ISO 5-8 are most recommendable for medical device manufacturing.
- Pharmaceutical cleanrooms:
Manufacturing pharmaceuticals and pharmacy products need an air-controlled and clean environment. As these products relate to health care, their contact with any pollutant (natural and artificial) and microbes would react extensively. These industries practice their procedure from formulation, manufacturing, and packaging.
A Cleanroom environment is necessary at each stage of the pharmaceutical industry. Usually, the cleanrooms provide better assistance during the packaging of pharmaceutical products. It is necessary to prove the spread of human contamination, procedures, and equipment. All these contaminations travel in the air, needing removal before the packaging procedure. The standard of clean air as per the regulatory guideline of pharmaceuticals is ISO 14644.
Monitoring the cleanrooms is necessary with prior vigilance over the active walls and floors. The temperature control, humidity ratio, and air pressure need constant monitoring in the cleanroom facility. The HVAC system controls all these aspects of the cleanroom, which must balance. The human interference in the cleanroom environment must be with the PPE (personal protective equipment) kit.
- Medical research cleanrooms:
Medical research needs cleanroom technology involving procedures like experimentation, research, and certain developments. The medical understanding and research here include many such factors which may be affected by outside dirt, dust and microbial pollutants.
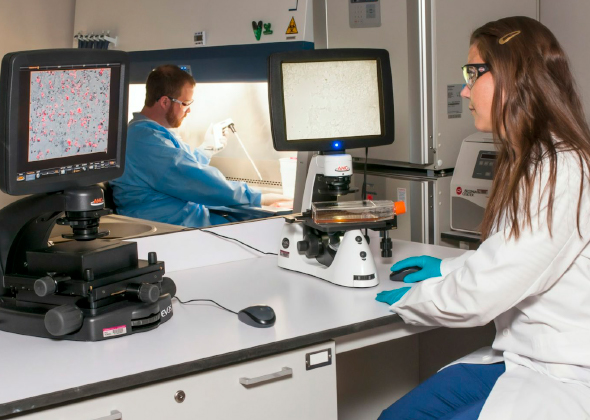
The environment of the medical research room has the strict requirement of biosafe surroundings. The people working here need assistive safeguarding from the future biopotential risks. These are unique from various types of cleanrooms requiring many precautions and preventions. The manufacturing of such a room involves micro injection molding, which processes it with small microbial details and designs.
The cleanroom environment in medical research and laboratories needs to be highly sterile and safe for microscopic agents. The medical room research undergoes many experiments that release toxic fumes and infectious elements. The cleanroom regulations maintain the purity in the surroundings and can remove such elements from the room.
The cleanrooms for medical research need to meet ISO Class 5-7. Such cleanrooms have the negative pressure to remove the excessive harmful contaminant to the rooms. It is necessary to maintain a suitable environment for medical procedures and experiments. The cleanroom facility is highly safe, secure and helpful for the employees working in such an environment.
- Based on construction:
The cleanroom categorization also involves their construction prototype and designing the base. The room’s design depicts the suitable area which defines what cleanroom is, its purpose and its best performing area. Many constructional prototypes and structure types are present, which variable departments adapt according to their preference and choices. The medical device parts, pharmacy and lab consumables suppliers have different cleanroom requirements than the research and experiment departments. Here is the explanation, which involves various structures and designs of cleanrooms with suitable categories:
- Modular cleanrooms:
Modular cleanrooms are the distinctive types of cleanrooms that offer freestanding environments and safety from harmful pollutants. These are the most durable and free-size cleanroom that covers the area with outside and automatic airborne contaminants. The modular cleanrooms have a robust design that has easy installation techniques.
The cleanroom environment in this design reduces this wastage and is highly efficient in controlling the infections by contaminants. It has robust design panels with easily configurable layouts. The modular cleanrooms are available with ULPA or HEPA filters which are highly beneficial in controlling airborne microbes and pollutants.
The design of the modular clean is compliant with the ISO standards and has the efficiency to scale the footprint in the cleanroom area. The modular cleanroom system follows the positive pressure system, which removes the contaminant repeatedly with effective filters.
- Softwall cleanrooms:
The Softwall cleanroom uses the technique to process and insulate the harmful dirt, microbial agents and toxic particles. Such types of cleanrooms are highly efficient in pharmaceutical, medical device and automotive departments. The design of the Softwall cleanroom is according to the area’s design, which needs filtration.
These cleanrooms have ceiling filters that possess the HVAC system, which provides excessive filtration with harmful aerosol chemicals and other airborne contaminants. The industrial platforms include such filters for their inventories and formulation rooms.
The structure of Softwall cleanrooms has steel and aluminum support, which maintains a strong, durable base of the cleanroom. The cleanroom environment provides constant protection and filtration with the help of ceiling filters covering the surroundings. Such rooms have the capability of customized designing, which reduces the overall cost according to the structure.
- Hardwall cleanrooms:
These cleanrooms provide high-scale integrity and durability to the cleanroom structure. The design of the Hardwall cleanroom has a rigid structure and modular vents for cross ventilation. The cleanroom equipment in the Hardwall type has a strong aluminum and steel structure. It also has the coating of PVC, acrylics and tempered glasses. It maintains the temperature, pressure, humidity and other such factors in the cleanroom.
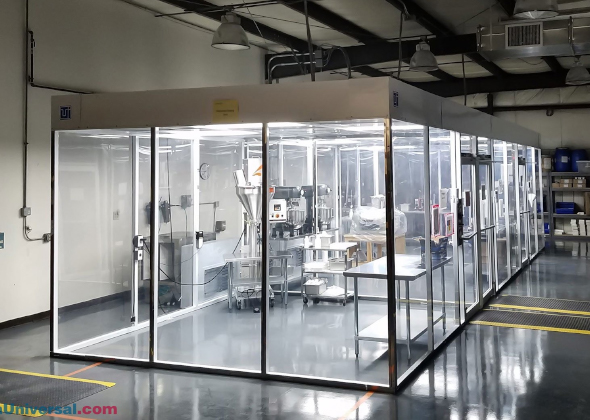
The Hardwall cleanrooms perform the laminar airflow, which prevents negative air pressure containment in the room. This type of cleanroom meets the standards and regulations of the ISO 5-6. According to the outside environment, it can maintain the constant pressure at different temperatures.
- Drywall cleanroom:
Drywall cleanrooms are conventional and most economical among all types of cleanroom range. This type of cleanroom implies its construction process by the traditional method. Due to these features, many industries and buildings adapt cleanroom technology for their inventories and warehouses.
It helps the cleanroom maintain the required temperature and moisture in the room. The effective filters of ULPA or HEPA filter the air constantly with the fan technology, which ejects the harmful particles out in the environment to clean the air. Such cleanrooms describe the reason why cleanrooms were invented.
- Based on the cleanroom class standards:
The cleanroom has its application categorization based on ISO standards. These standards have the inclusion of regulatory standards of cleanliness and safety. According to these standards, many types of cleanrooms have their design, functionality, and benefits. All the levels here define the air quality, ventilation pretties and filtration method in cleanrooms. The description of different levels of ISO defines the fact that what is cleanroom and its need for the structure:
- Class 100 cleanroom:
The class 100 cleanroom has essential control over various types and properties of natural, artificial pollutants. The cleanroom is very important in computers and technology for data recovery. This type provides cleanliness through HEPA filters and is efficient in trapping pollutants of the size of 0.3 microns. The cleanroom environment stabilizes temperature, electromagnetic interference, humidity and electric field in the surroundings. The room efficiently provides almost 99.93 percent of pollutant-free surroundings with this technology.
- Class 1000 cleanrooms:
Class 1000 is one of the cleanest types of cleanroom among all the present options. It achieves cleanliness by preventing approximately 1000 pollutants in each cubic meter. This class of cleanroom is available with the soft and hard wall structure. Such cleanrooms consist of a pre-wiring structure, and installation is very convenient. Due to this, they are highly efficient for medical devices, equipment and research laboratories. The class 1000 cleanroom is highly in demand for the medical device injection molding area.
- Class 10000 cleanrooms:
These cleanrooms consist of the HEPA filtration system with epoxy floors and airlock technology. The class 10000 cleanrooms prove their efficacy in the aerospace product development, cosmetic industry, pharmaceutical industry and medical devices. This cleanroom comprises the capability of cleaning approximately 10000 contaminants per cubic area of the room. The approx size of this filtration system is around 9-16 CFM per square foot to provide the expected cleanroom environment.
- Class 100000 cleanroom
These cleanrooms have advanced technology that cleans around 100000 particles cleaning per cubic foot in the interior portion of air. This cleanroom class has ISO standards 8 and contains HEPA filters to clean the air. The cleanroom can exchange air with purity and freshness approximately 20 times per hour. They have a modular design with soft walls and a high flexibility ratio. They are easy to expand and undergo convenient relocation and installation.
The basic structure of cleanroom:
The cleanroom comprises a structure that allows function collectivity to clean an area. All the components of this structure are highly important and are interdependent with each other. The function, efficiency and technology of any cleanroom depend upon the active sync of the components. Here is the categorized description of the structure of the cleanroom:
- Fan powered HEPA filter:
The high efficient filter system is one of the basic cleanroom requirements. The HEPA (high-efficiency particulate air) filter is the filtration system that cleans the air ejecting the harmful contaminants. The filtration system works on the principle of subtracting harmful chemicals like airborne microbial, microscopic chemicals and dust particles by rapid force of the fan. This filtration system removes approximately 99.97 percent of pollutants with the fan force. These filters can eradicate the air microbial and dust agent of the size of around 0.3 microns.
- Cleanroom ceiling panel:
The ceiling panel of the cleanroom is the basic component of many categories of cleanroom systems. To maintain the cleanroom environment, constant airflow, cross ventilation, and 360-degree air surroundings are necessary. The ceiling panels provide air filtration from all sides of the room with constant airflow. The ceiling panels are easy to install and designed according to the size of the room. These panels are rigid; robust, which makes them easy for relocation.
- Light fixture:
The lighting fixtures in the cleanroom environment do need any special structure. They get their fixation with the ceiling structure; they are positioned according to the aluminum or steel structure. Their position is in the center and adjacent sides in all cleaning rooms. The variant of lights is generally the LED panels that need minimum maintenance and are durable for long intervals. According to the room, most cleanrooms have these panels because of their energy-saving efficiency and a variant of available sizes.
- Flooring cover:
It is one of the essential components of the structure of the cleanroom. The cleanroom has variants of the flooring option with several materials. Epoxy resins, PVC, vinyl are the most common and efficient among popular options available. These materials are anti-bacterial, solvent-free, antistatic and ideal for insulation. These need very low maintenance for hygiene and can be easily cleaned, defining what is a cleanroom and it’s functioning. Various colors and designs are available with smooth matte finish options in the flooring within distinct sizes.
- Tube steel column:
The tube steel columns support the filtration system cleanroom setup. The tube steel columns hold up the alignment in the cleanroom process. The installation of such columns is very easy and convenient. They are available in variant materials like steel and aluminum. The column possesses the strength and functioning of the filtration system. The constant functioning of the process depends upon the tube steel column of the cleanroom system.
- Strip doors:
The strip doors are an essential part of the cleanroom facility. Many types of high-performance strip doers are present in the structure of cleanrooms. The strip doors can be designed according to the size and filtration system in the room. They are commonly available in polysim PVC material. These materials can retain high speed and antistatic properties. Various types of doors are used for pharmaceuticals, food industries, laboratories etc.
What equipment is in the cleanroom?
The cleanroom maintenance also depends on the types of equipment moving, transferring, and placement. The equipment has a huge impact on the precautionary measure and hygiene of the cleanroom environment. The medical consumables company has the infrastructure with the cleanrooms devices and equipment placement guide. Hence, here is the list of the equipment to use the cleanroom effectively:
- Automatic shoe cleaners:
The shoes are the generating cause of contaminants; they directly contact all types of dirt, dust, and pollutants. Therefore, the automatic shoe cleaner is very necessary for the cleanroom environment. These modern technology machines possess the quality of cleaning the shoes that accumulate unwanted contaminants. They are available in variable shapes and capacities. Many of them possess brushes and automotive sanitizers with auto vacuum technology. It helps the workers to balance the hygienic cycle in the cleanroom.
- Cleanroom pass-thru:
The pass-thru cabinets in the cleanroom area are an important part of maintaining the entire setup in many types of cleanrooms. They play a key role in balancing the hygiene and contaminant-free environment in the surroundings. It reduces the foot traffic and chances to increase the infections, which eventually may affect productivity. These systems are highly beneficial in the pharmaceutical and medical devices department. They need low maintenance power and are easy to clean.
- Containment hoods:
Many types of cleanroom hoods are available for cleanroom facility maintenance. These hoods work with several functionality and types. Fume and powder containment hoods are very common among all variants. They are simple devices that clean the user’s contaminants and elements. The device has complete ventilation and works on simple latch processing. Many designs, sizes and variants are available, which vary according to the pricing and size of the cleanroom.
- Particle counter:
The particle counter is a particle measuring system that is a highly safe and technologically smart device. The particle counter has essential sensors which maintain hygiene and cleanliness in the cleanroom environment. These are innovative and modern devices that are maintenance-free and work on basic operating conditions. They need a minimal power supply with variant operational modes in extended conditions.
- Desiccator cabinets:
The desiccator cabinets are dry boxes usable as the storage unit in the cleanroom facility. They possess the unique feature of an ultra nitro-flow system which maintains the accurate environment necessary for the product in the box. The desiccator’s cabinets have multiple chambers with spring latch doors with effective gaskets and airtight seals. The storage area has a clean, dry and moisture-free assembly in the boxes with ultra-low RH percentage.
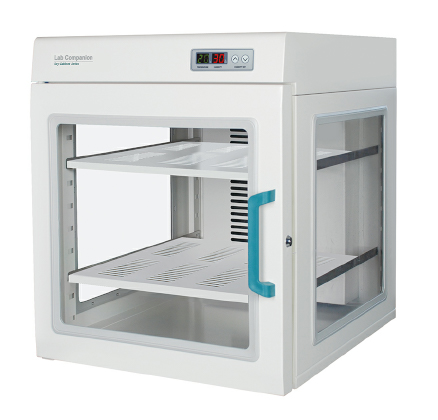
Advantages of cleanrooms:
Many businesses and infrastructures need various types of cleanrooms and facilities to maintain cleanliness. Cleanrooms are highly popular today as they need a very minimal and easy setup with low maintenance. Due to this, medical injection molding companies are innovating cleanroom designs in several sizes and appearances. Many advantages of the cleanrooms are according to their variants and the size of the surroundings. Here are some of the advantages of the cleanroom which are effective in maintaining the hygiene and pollution-free environment:
- The cleanroom construction is very convenient and includes easy installation and relocation. It motivates many small-scale businesses to install the cleanroom process in their inventories and warehouses.
- The prime advantage of the cleanroom is they offer a zero contamination facility in their area. Several types of pollutants, including aerosols, airborne microbial, microscopic dust and other chemical contaminants, can be trapped in the filtration system of the cleanroom.
- The cleanroom environment is extremely safe and secure for human health. It offers customization, which is usable in various industries in various types.
- Using the cleanroom is highly beneficial for increasing the productivity of product and machinery.
- The cleanroom technology is highly efficient and durable for long time use. These are also cost-effective, providing efficiency by increasing the profits of any business.
Cleanroom application:
The cleanroom application is very effective in many areas and departments. Here is the description regarding its effective application in variable fields:
- Medical Laboratories: The medical laboratories need a cleanroom facility as much experimentation, and research occur in this area. The cleanroom maintains the essential hygiene for such procedures.
- Aerospace Industry: Theaerospace industry uses the cleanroom facility to design and produce spare parts and machinery. It works relatively with this technology.
- Nanotechnology production: nanotechnology needs a highly safe environment from microbial dirt and pollutants. It becomes necessary for 360-degree cleanroom hygiene for development in this area.
- Optics and Lens: Manufacturing: the glass and lens might lose their effective tendencies with environmental dirt and chemical particles. The cleanroom maintains the temperature and pressure for the manufacturing of these lenses.
- Military Applications: The military equipment, machinery, and device also need the cleanroom to maintain their devices’ functioning. Cleanroom keeps it free from chemical pollutants and microscopic microbial.
- Microelectronics and semiconductors: The electronic devices need to be in a cleanroom area with a hygienic environment for best performance.
- Micromechanics: The experiments in micromechanics need a cleanroom environment for accurate results and values.
- Biotechnology: The biotechnology labs must also be free from airborne microbes and chemical pollutants for experimentation.
- Pharmaceutical production: Pharmaceutical production needs effective hygiene from pollutants for the drug formulations and packaging. The cleanroom provides such surroundings.
- Medical Devices manufacturing: The manufacturing of medical devices also needs cleanroom technology to avoid the harmful dirt and microbes.
- Sterile Compounding: The sterile compounding needs airtight surroundings with perfectly clean air for
- Food and Drink: These industries need a cleanroom facility to increase the productivity of the product’s durability.
- Isolation Rooms for Hospitals: The isolation wards in the hospitals need a hygienic and dirt-free environment for effective treatment and observation. Cleanroom provides this environment in these wards.
Cleanroom standards:
The cleanrooms are classified according to their ISO standards. . These standards are useful in variable sectors of industries. The cleanroom with accurate ISO levels provides effective results and performance. Here is the description of these details:
- Class ISO 1-6 – These ISO standard cleanrooms are considered the cleanest and most usable in medical devices rooms, research labs, and pharmaceutical formulations.
- Class ISO 7 – These are used for isolation wards for the hospitals and medical equipment manufacturing
- Class ISO 8 – These standards work effectively in the food industry, automotive industries, pharmaceutical inventories and packaging departments.
- Class ABCD- This class of cleanroom process is used for high-risk experiments and operations. They are generally used in sterile compounding methods.
- Class 10, 1000, 10000, 100000, 1000000- Class 100000 & 1000000 cleanroom is used for high-security areas in medical and research laboratories.
- Class FS209E- These are the international standards of using the cleanroom process in a particular area.
What are the cleanroom requirements?
There are some essential requirements for the need and maintenance of the cleanroom facility. The requirement modules decide the effectiveness of the cleanroom filtration. Here are the details:
- Humidity
- Excessive temperature
- Poor ventilation
- Polluted surrounding
- Excessive use of chemicals
Cleanroom rules that employees need to observe:
Cleanroom needs some essential regulations which need o followed for the safety and hygiene. Here is the list:
Do:
- cover face with the mask
- follow proper growing regulations
- entire cover hairs
- follow the personal hygiene
- leave personal belongings outside
Don’t:
- avoid eating and drinking
- restrict to use of perfumes and makeup
- avoid smoking before entering the cleanroom
Factors that could affect the cleanroom environment:
Several factors can affect the cleanroom environment and hygiene. Here is the list of certain factors which can affect the functionality of the cleanroom:
- Lighting system
- Temperature
- Size of the room
- Number of the people working in the room
- Cross ventilation
What does the cleanroom cost?
The average cost of the cleanroom installation is around 1500-2000 per square foot. This cost may vary according to the specification and additives with the cleanrooms. The specification includes wall and flooring material, lighting variants and capacity of the filtration unit.
Conclusion:
Cleanroom facility provides the scope to many businesses to increase their productivity and profits and maintains the levels of hygiene and safety in each department of research and technology, especially for the medical consumables (Learn:What Are the List of Medical Consumables) and device manufacturing. Hence, the cleanroom is integral to modern manufacturing and research infrastructure for effective growth and development.