Injection molding is a manufacturing procedure that is known for producing various types of parts for industrial applications at a reasonable price. There are wide materials that are compatible with injection molding procedure, and the molds are durable and last for a long time.
A reliable plastic molding company offers a one-stop service from product design and development to part manufacturing. In the injection molding procedure, there are some common defects that arise in different production stages. One such major issue is mold flashes which occur due to mold tooling issues.
What Is Molding Flash?
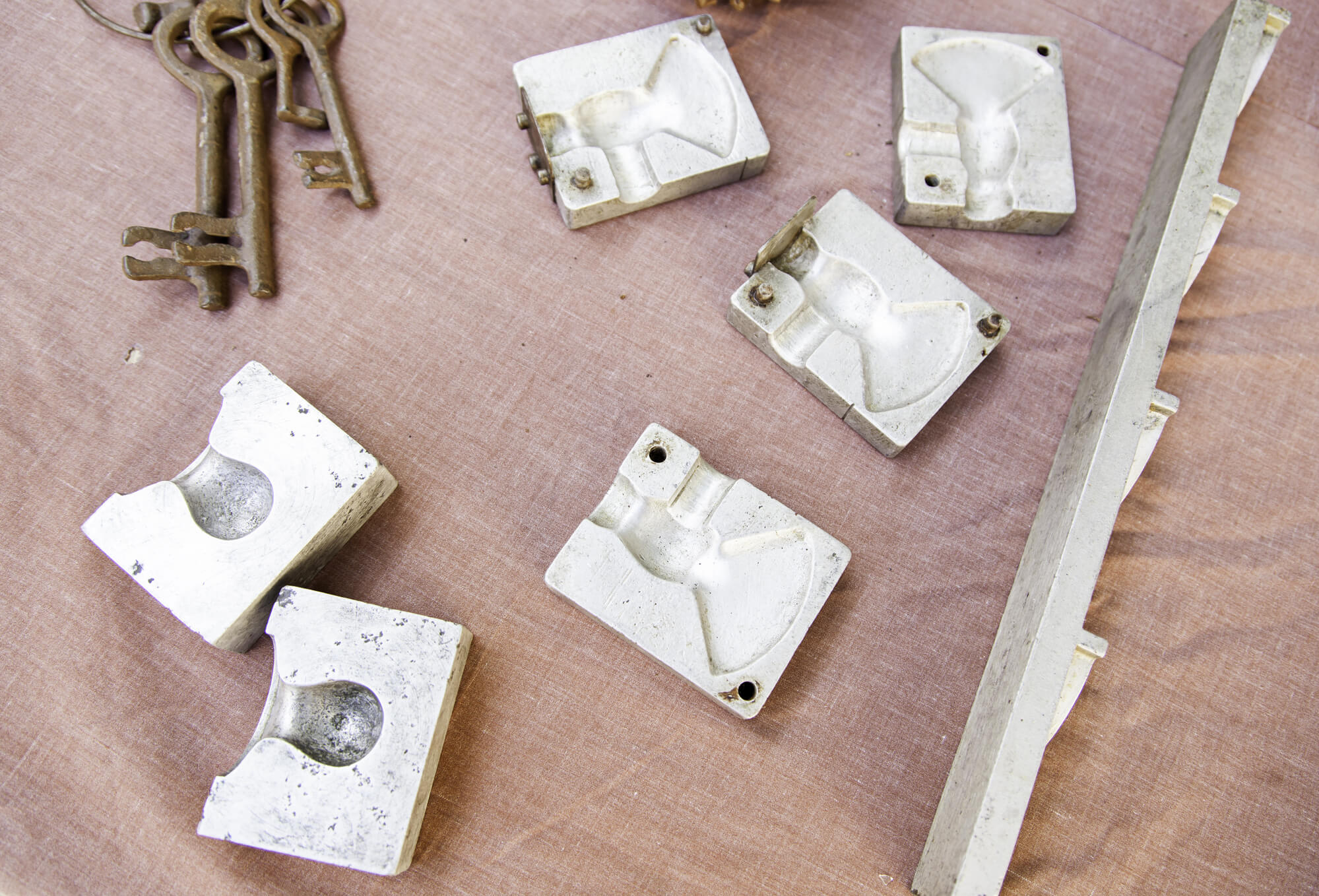
The extra plastic that develops on the surface of injection-molded products is known as mold flashing or injection mold flash. This excess substance is often driven out of the injection mold cavity near the parting line. Mold flash is the result of substance discharging into areas other than the designated flow pathways. The most common areas where flash often occurs are the area at the injector pin, parting surface, or between the tooling plates.
When creating the role of leverage, the edge mold flash will cause the edge burr to grow further. As a result, it results in a localized depression in the mold, which leads to the creation of a vicious cycle when the injection molding suddenly boosts. So, if a mold flash is discovered on the product surface during the clean room injection molding procedure, it needs to be cut right away.
What Causes Flash Defect In Injection Molding?
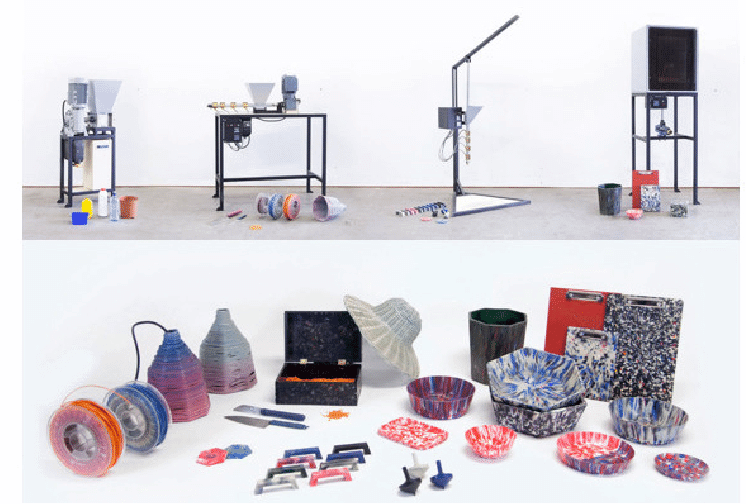
Flash defects can be linked to many reasons, such as divergences in the procedure, mold problems, material problems, machine issues, etc. Here are the major causes of flash defects in injection molding faced by medical injection molding companies.
- Equipment
When it comes to equipment, the flash defect can be caused due to excess residence time in the barrel, so it is best to opt for a 50% shot-to-barrel ratio. Another cause is very high injection pressure, so it is better to decrease the injection pressure and ensure there is a correctly lifted shutoff land surrounding the cavity’s perimeter.
Excessive barrel temperatures in the equipment also lead to flash defects. So, lessen the barrel temperature and put the profile fixed, so the substance is heated from the back of the barrel towards the front. Large machine cycle times also result in flash defects. If the machine’s real clamping force is not enough, flash defects will arise.
- Mold Tooling
If there is an inadequate parting line seal in the mold tooling, flash defects will occur. So, it is vital to check for an adequate parting line seal. Another reason for molding flash is improper venting, so make sure to vent the mold by grating slim pathways on the cavity’s shutoff region.
The improper mold supports also leads to flash issues, which is why ensuring that proper support is present is vital. If the length of the sprue bushing is very long, there will be a flash defect. So, the reliable medical device component manufacturer will decrease the sprue bushing length by grating the face back.
- Raw Materials
When it comes to the raw materials used in injection molding, if there is an inadequate flow rate, a flash will appear. So, it is better to use a substance with the stiffest flow that does not lead to non-fill. The excess mold lubricant is another reason for flash defects. The mold lubricant should be used in a medium and should be directly applied to the plastic pellets. Flash defects will also arise when the plastic viscosity is very low or high.
- Process
During the procedure, there will be flash issues if the injection pressure is very high or the injection speed is very quick. If the temperature of the nozzle, barrel, or mold is very high, the plastic viscosity is decreased, which enhances fluidity, leading to a flash. In addition, excess feeding also leads to flash defects.
Molding Flash During Injection Molding Phase
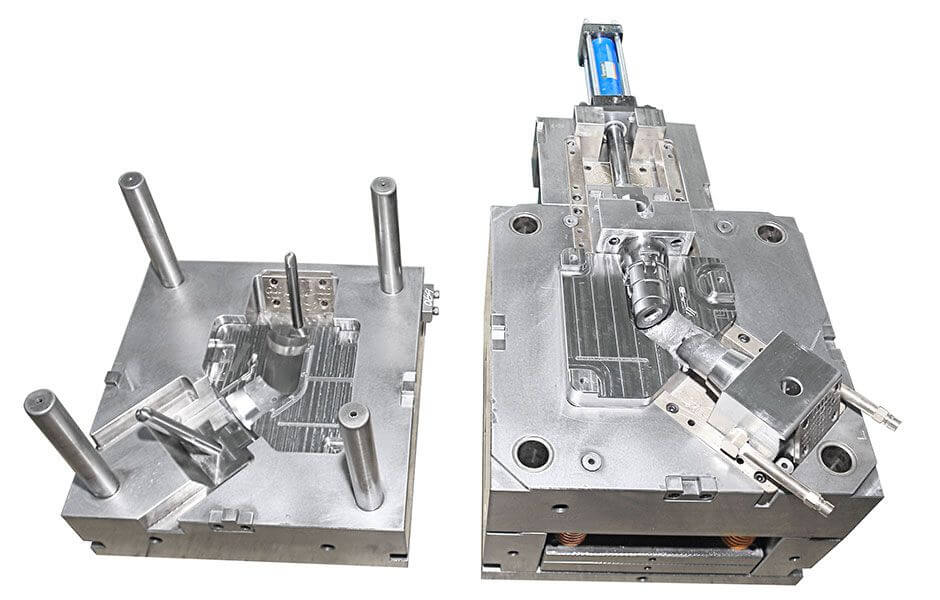
Below are the most common mold flash causes that occur during injection molding, which is the first injection stage.
- Parting Line Discrepancies
Dirt, impurities, dust, and residues prevent the mold from closing correctly, and they can be the primary cause of discrepancies in parting lines. Flashing can also result from mold cavities that are frayed out or aged that do not tightly match. These metal surfaces can become bent during the injection molding process due to the pressure placed on the mold plates. Parting line mismatches can also arise due to complicated part geometry designed by the medical plastics manufacturers.
- Inappropriate Venting
Flash is sometimes the result of inappropriate venting. In case the plastic is stiff, the vents in the mold might not have sufficient depth. Aged or damaged vents that do not adhere to the necessary tolerances might also result in mold flashing.
Molding Flash During Packing or Holding
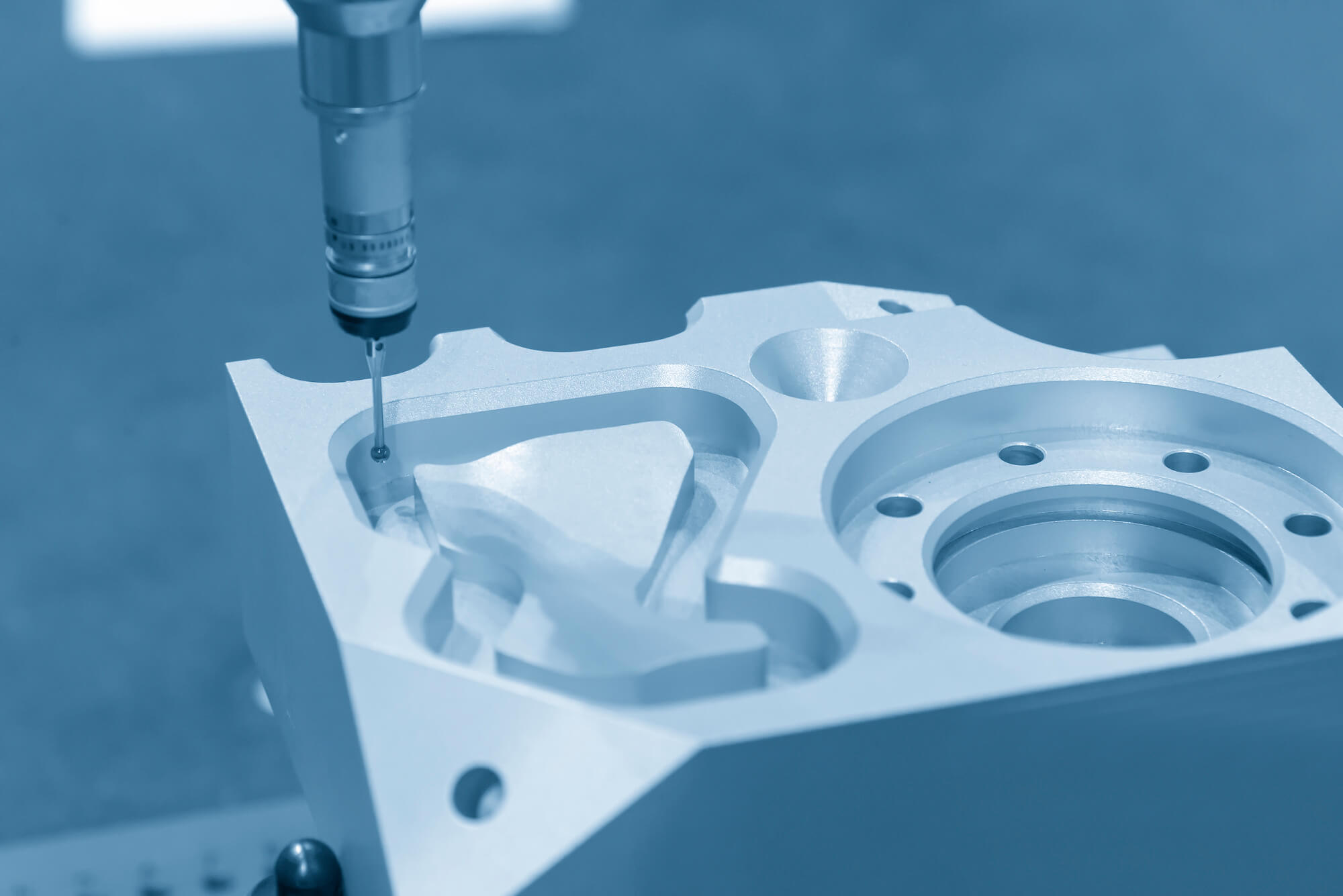
Check out the below listed common causes of mold flash that occur during the packing or holding phase, which is the second stage.
- Inadequate Clamping Pressure
Due to excessive or insufficient clamp force, mold flash could arise. It is to be noted that in order to keep the mold plates closed, the machine clamp force should be larger than the pressure within the cavity. The best solution for this is to alter the hold or pack pressure or utilize a press with the appropriate clamping pressure.
- Sprue Bushing Problems
The pack or hold pressure might cause the mold parting line to separate during the molding procedure. Insufficient sprue bushing support can also exert pressure on the parting line. Flash can occur due to thermal development in the sprue bushing. It is better to inspect the sprue bushing’s thermal expansion under manufacturing circumstances for non-sprue-gated items.
Fixing Process Variables That Can Cause Flash Molding Defects
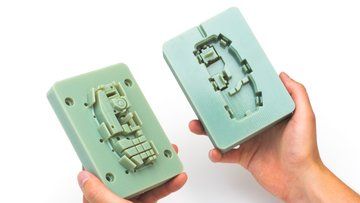
There are plenty of procedure variables that can lead to flash. Below are the main issues in procedure variables that result in mold flash.
- Injection And Packing Pressure
Decreasing pressure will automatically lessen the chances of the material to mold flash. In case of excessive pressure, the press would not have the capacity to keep the mold locked. Also, lessening the packing and injection pressure will slow down the clamping force.
- Temperatures Of Barrel And Nozzle
The temperature of the nozzle and barrel are also factors that will lead to flashes in the injection molding part. Due to elevated temperature, the liquid substance will become more vulnerable to leakage. This happens because of low viscosity and leads to a rise in the likelihood of molding flash.
- Overpacking
The design complexes and minute routes in the injection molding medical devices parts can also lead to flash. When there are slim areas, only some molten fluid can thicken and obstruct the entire flow, which leads to pressure inside the mold. Due to overpacking, there will be multiple issues like flashes, uneven density, warpage, etc.
- Insufficient Material Viscosity
Insufficient plastic viscosity implies that the molten fluid will stream out of the mold form and have warpings as flashes. In general, viscosity is a characteristic of material properties, temperature, speed, and pressure.
- Overfilling
When the mold is overfilled with the substance, it will automatically lead to leaks because of the high injection pressure, which is more than the clamping pressure. The excess substances will connect themselves to the manufactured item, which creates flashes.
Ways To Fix Flash In Injection Molding Process
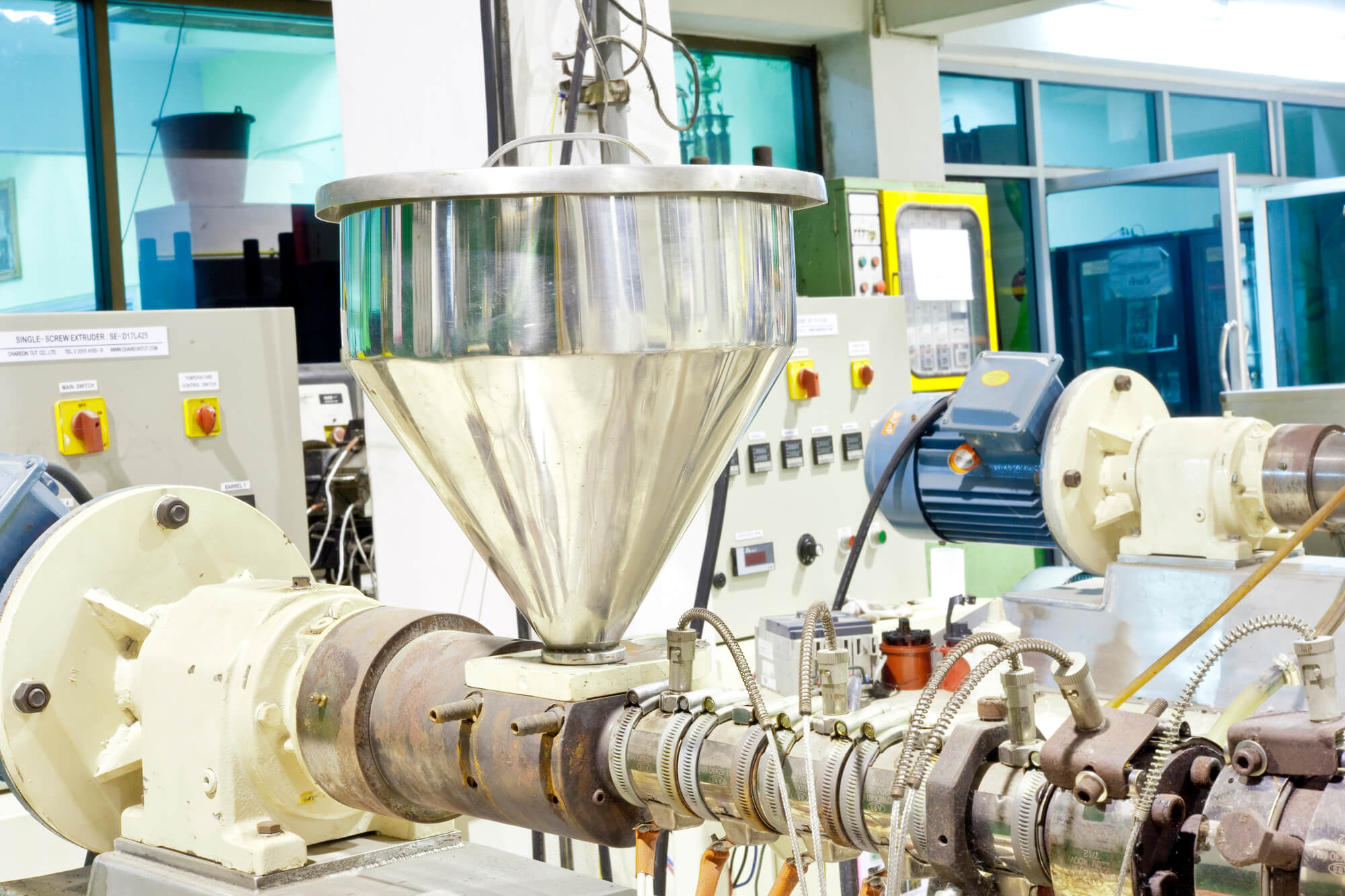
Flash can arise in many stages, including the filling phase, injection molding phase, or packing and hold stages. Go through the below pointers, which will help in fixing the mold flash defects in the injection molding process.
- Using Hot Air
When the mold flash is created, it is possible to liquefy the excess flash with the help of hot air. Nevertheless, one has to keep in mind that this method is useful only for clearing fine and slim flashes. It is best to use hot air as an alternative method for melting dense flashes once the major part of the flash is taken out mechanically.
- Using Open Flame
Similar to the hot air method, it is also a good option to utilize an open flame for melting the mold flash. But, it is to be noted that the open flame will change the surface of the substance. As a result, it will affect the aesthetics factor of the custom plastic molding parts.
- Cryogenic Deflashing
Another best way to remove flash is cryogenic deflashing. In this method, the excess flash is cooled down with the help of liquid nitrogen until it attains a certain temperature where one can take out the flash. One drawback of this method is that commercial cryogenic deflashing equipment is costly.
- Manual Deflashing
Due to its versatility, manual deflashing is another famous way to fix mold flash. In this method, the excess mold flash is chopped with the help of knives, scissors, grinders, etc. As a result, it will eliminate flash alongside the product’s parting line.
How To Prevent Flash In Injection Molding
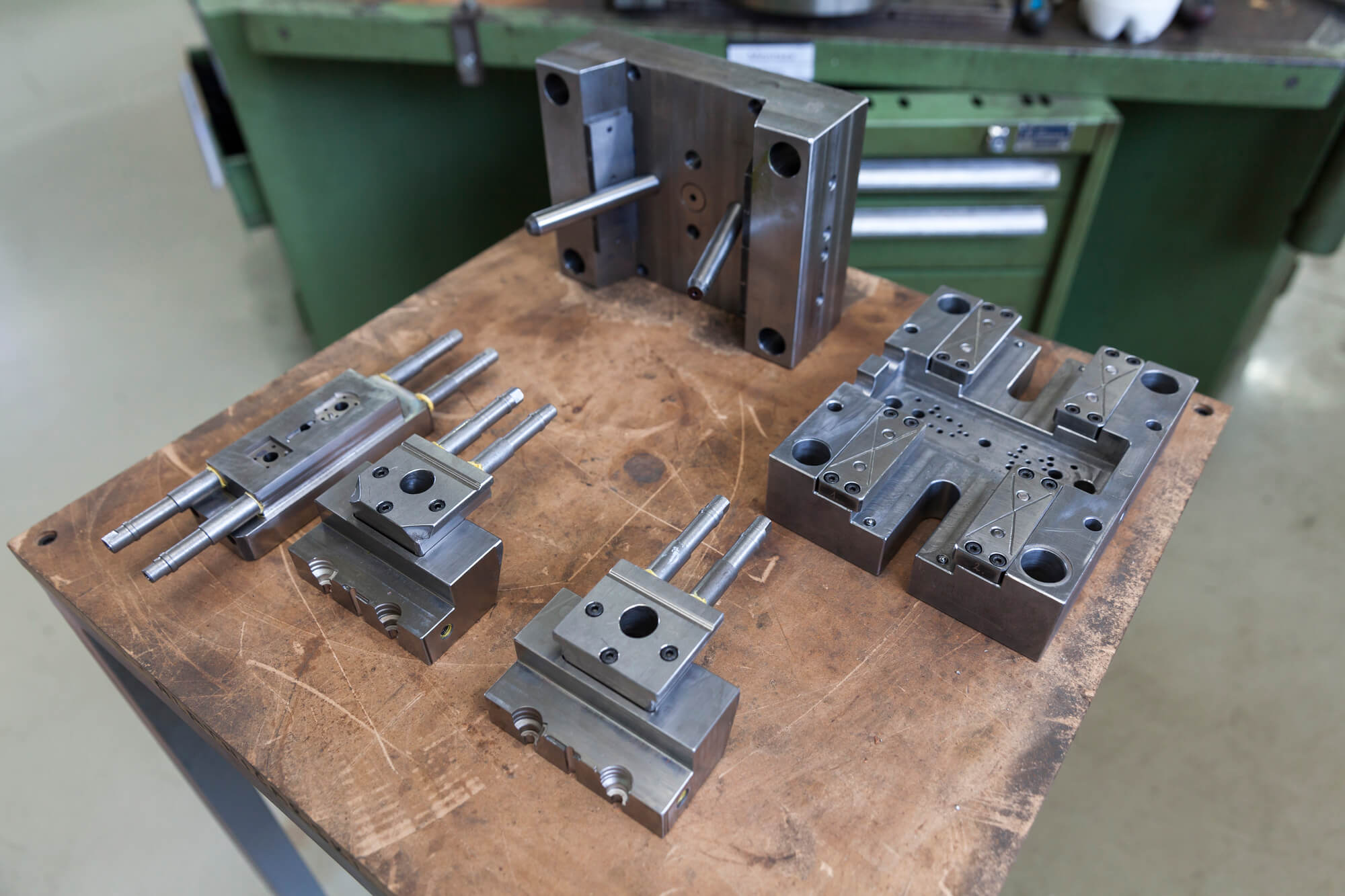
The above section focused on removing the mold flash from the products. However, this section is centralized on better ways that help in deterring the occurrence of mold flashes at all.
- Design For Manufacturability
One of the best ways to make sure that the injection molded parts do not have flashes is to design the mold for manufacturability. To put it simply, following some basic mold design rules that are associated with the mold manufacturing industry will help in creating simple mold designs. When these molds are designed correctly in injection molding in clean room with the proper wall thickness, precise mold gate design, and uniform mold parting line, the final product can be manufactured without flashes.
- Get Flash-free Mold
With the help of a flash-free mold, it is possible to deter flash defects in molded plastic parts. The mold should retain elevated injection molding tolerance and precision so that the final products will be the best in terms of functionality and aesthetics. One drawback is that they are slightly expensive.
- Use Sufficient Clamp Tonnage
The flash-free injection molding procedure is also based on the force exertion point, amount of tonnage, clamping mechanism, etc. It is to be noted that an excessive amount of force will destroy the mold, which will damage the final product. In order to deter the occurrence of mold flash, it is vital to use proper clamp tonnage.
- Decelerate The Injection Rate
When the injection rate is very high, it will raise the molten plastic substance’s pressure. Due to that, there are high chances for mold flash defects. Hindering the injection rate will decrease the injection pressure, so there will be no flashes.
- Ensure Adequate Mold Cleaning
In order to deter the formation of mold flash, it is vital to clean the mold regularly. It is better to utilize a cloth, compressed air, and mold cleaner to wipe the mold surfaces. Make sure to cleanly rinse the debris, leftover plastic, and various pollutants. If not, they will deter the mold from closing completely.
- Decent Mold Maintenance And Upgrades
Just like mold cleaning, mold maintenance is also crucial. To manufacture steady and quick products via injection molding, regular mold maintenance and procedure upgrades are vital.
Other Injection Molding Defects
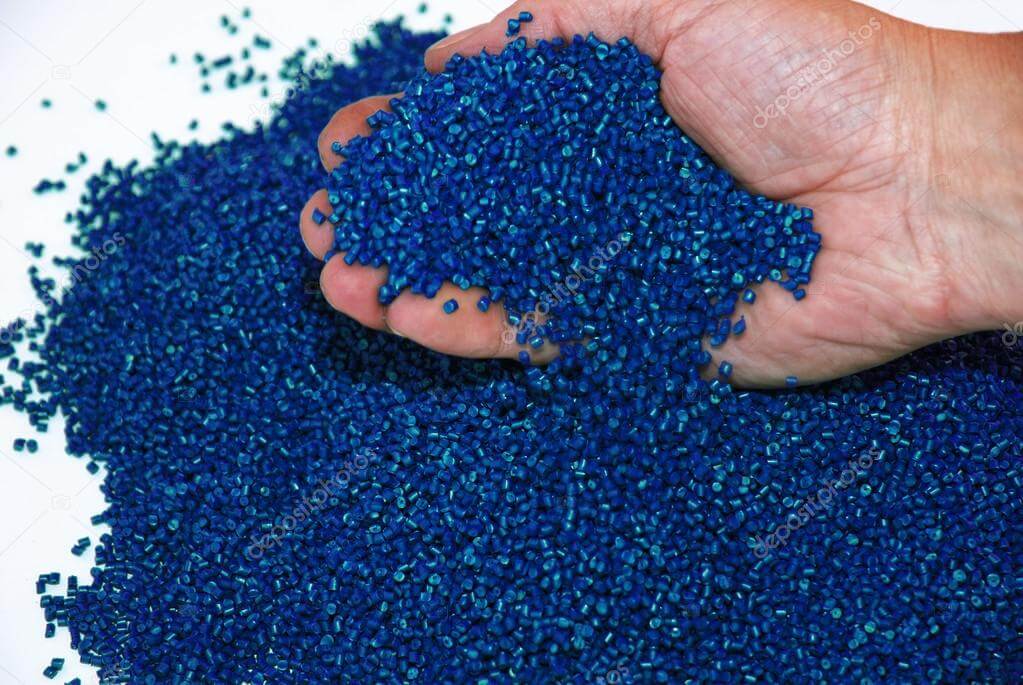
Apart from mold flashes, there are other types of injection molding defects that arise during the injection molding procedure.
- Sink Marks
Sink marks are tiny craters or depressions. When shrinkage happens in the innermost regions of the final product, sink marks form in thicker areas of the injection-molded prototype. Sink marks frequently result from insufficient cooling time or inadequate cooling mechanisms, which prevent the plastic from fully chilling and curing inside the mold. Improper cavity pressure or an elevated gate temperature are other potential causes.
- Discoloration
Discoloration, often known as color streaking, happens when a molded object is not in the preplanned color. On a molded item, the discoloration frequently only affects a small patch or a few lines. This flaw often reduces a part’s aesthetic appeal without weakening it. Remaining plastic pellets in the hopper, excess resin in the nozzle, or mold from an earlier production cycle are common causes of discoloration. Other probable causes include the coloring agent’s poor thermal stability, the masterbatch’s inappropriate mixing, etc.
- Weld Lines
Weld lines are actually planes that form in a region where molten plastic discharges from two different areas of the mold and meets another part. When clashing, two or more molten substance fronts must maintain a specific temperature. If not, they partially solidify and fail to join together at their points of contact leading to weld lines.
- Burn Marks
Burn marks sometimes appear on the surface or edge as discoloration that is black or looks like rust on molded parts. Burn markings normally do not impair the integrity of the part. These marks on injection-molded items are typically caused by trapped air or by the resin heating up in the mold cavity. Burns are frequently caused by overheating, which is oftentimes caused by excess injection speeds or material heating.
- Short Shots
Short shots are instances where a molding shot is insufficient. When molten material rushes through a mold but does not entirely fill the voids, it leads to short shots. As a result, after cooling, the molded component will be unfinished. Short shots are most frequently caused by flow restrictions due to narrow or obstructed gates. In other cases, the substance is very viscous or the mold is very cold for the molten substance to fill fully before cooling.
- Vacuum Voids
In a final molded part, vacuum voids, also known as air pockets, are air bubbles that have been caught up. Quality assurance experts generally view voids as small flaws. Nevertheless, in other circumstances, bigger or countless voids can degrade the molded item. Unstable solidification between the prototype’s outer and inner parts frequently results in vacuum spaces.
- Warping
When distinct portions of a component shrink unequally, the product can warp. The rapid cooling procedure is one of the primary factors that result in warping. The molten material’s poor heat conductivity or excess temperature can also cause this. In addition, a mold’s design might cause warping if the mold’s walls are not of the same thickness because shrinkage rises with wall thickness.
- Surface Delamination
Thin surface layers develop on the component as a result of a contaminating material, which is known as surface delamination. These coating-like layers can frequently be removed. The main reason for delamination is foreign material contamination of the plastic or other substances. When the two materials are not adequately bound to one another, flaky separation occurs. If the product is meant for a safety-crucial application, the loss of material strength would be quite harmful.
- Jetting
When molten plastic does not bind to the surface of a mold because of a fast injection, it is known as jetting. Jetting commonly originates from the initial gate of injection and is a squiggly streak on the final component’s surface. Due to that, it will lead to part weakening. Very high injection pressure is the primary reason that leads to jetting.
- Flow Lines
Flow lines are patterns, streaks, or strings that appear on the prototype part and typically have off-tone color. They could also take the form of ring-shaped bands close to the gates where the molten material enters the mold on the surface of the product. Most frequently, flow lines are the consequence of differences in the material’s cooling rate as it cools at distinct rates and flows in various directions inside the mold. The material may cool at various speeds due to variations in wall thickness, causing flow lines.
- Cracking
Cracking frequently appears around the weld line, but it can also appear throughout the whole surface. Less injection rates, cold mold surfaces, and outer environmental stress and deformation are the main contributors to cracking. It is better to raise the injection speed and boost the operational temperature in order to deter rupture or breakdown of the surface.
A Reliable Partner Help Your Injection Molding Project
For any injection molding project, regardless of the type of industrial application, it is better to get assistance from a top-notch injection molding company. It is best to contact SeaskyMedical to acquire huge quantities of high-quality injection molded parts for a low price.
SeaskyMedical is a Chinese-based company with great global demand. With over 20 years of injection molding experience, skilled professionals, a massive workshop area, and advanced injection molding machines, SeaskyMedical is one of the best injection molding companies and could prevent molding flash effectively.
At SeaskyMedical, there is an ISO 8 cleanroom, modern measuring equipment, sufficient stock of medical-grade materials, and quick production lines. All the injection molded parts go through various quality inspections before they are delivered to the client, including molding flash inspection.