Thermoplastic materials are one of several forms of plastics that are noted for their recyclability and diversity in use. They are made up of monomers, which are repeating units that connect together to create branches or chains.
When heated, the thermoplastic resin softens, and the more heat applied, the less viscous it becomes. The curing process is totally reversible, allowing the material to be remolded and recycled without affecting its physical qualities.
The bulk of the materials utilized are strong, flexible, and shrink-resistant, and may be used in both low and high-stress applications as thermoplastics are the main injection molding tool.
What Is Thermoplastics Material?
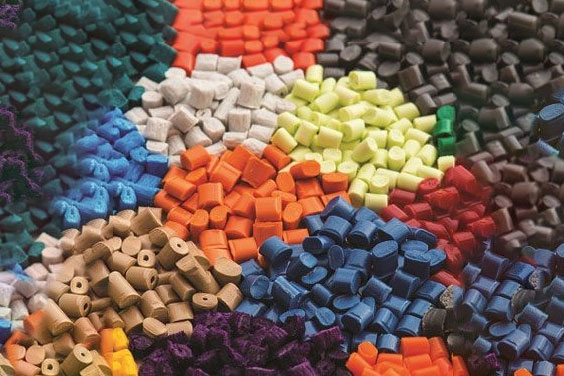
Thermoplastics are plastic polymers that soften when heated, allowing them to be molded, and then solidify when cooled.
Thermoplastic materials may be remolded and recycled without compromising their physical qualities due to their unique chemical features. Thermoplastics are an excellent material for injection molding because of this.
Depending on the kind of thermoplastic material, it may be utilized for a wide range of applications, from consumer items to micro molding medical devices. The easiest thermoplastics to process are commodity thermoplastics, which are utilized to make high-volume items.
Packaging, apparel, food, and drinks are all good candidates for these materials. Engineered and specialized thermoplastics, on the other hand, have been combined to improve their properties. They are employed in the military, aerospace, and medical molding company facilities for heavier-duty applications.
The only polymers that can be welded are thermoplastics. When heated, the plastic transforms into a paste or a liquid that can then be a specific mold design. Despite the fact that each type of thermoplastic has its own set of qualities and capabilities, they can all tolerate many reshapings without causing material damage.
What Are the Types of Thermoplastics?
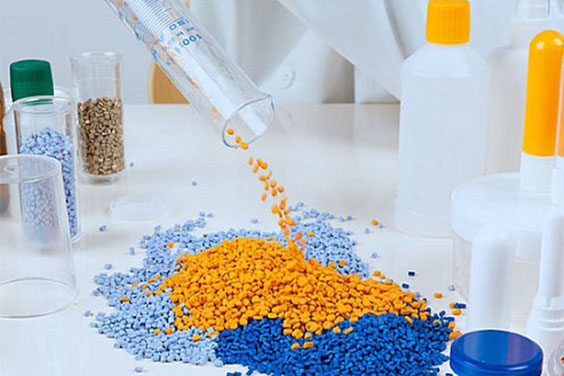
Plastics that can be melted and molded several times are known as thermoplastics. They have a molecular structure that is open-chain. A sign imprinted on the base of the bottle or on the package itself quickly identifies plastics in the packaging.
Molds are used to create a wide range of everyday items. Different types of thermoplastics are utilized to replicate these artifacts, and they are chosen for each function based on flexibility, stiffness, durability, and other important characteristics.
Here are the major types of thermoplastic materials with their properties and applications:
Type | Property | Application |
Acrylonitrile butadiene styrenes (ABS) | The most well-known substance among customers is ABS. Plastic products made by ABS plastic molding are strong and durable even at low temperatures. Dimensional stability, abrasion resistance, chemical resistance, heat resistance, and balanced tensile strength are all features of these materials. | LEGO bricks Safety hats Whitewater canoes Musical instruments Medical disposables |
Acetal Copolymer Polyoxymethylenes | Because of its lower melting temperature, this thermoplastic is easier and faster to produce than typical homopolymer resins. These thermoplastics are creep-resistant, have strong moisture resistance, and may be utilized in high-temperature applications for long periods of time. Excellent lubricity, high tensile strength, and fatigue resistance are further features. | Lucite Perspex Plexiglass |
Acetal Homopolymer Polyoxymethylenes | These thermoplastics have excellent weatherability and scratch resistance, as well as the ability to transmit and regulate light. Polyoxymethylenes are also resistant to discoloration, have minimal haze, and are scratch-resistant, making them suitable for optical applications. | Yarn Rope Conveyor belts Clothing Furniture Blankets Mousepads |
Polycarbonates | These polymers have outstanding durability throughout a wide temperature range. Polycarbonates are distinguished by their dimensional stability, heat resistance, hardness, and transparency. This category of thermoplastics contains a wide range of grades, from general-purpose and extrusion molding to particular grades for food processing and medical applications with flame retardant qualities or contamination resistance | Injection molding Kitchenware |
Polyethylenes | The key properties of this type of plastic are low water absorption, dimensional stability, hardness, and stiffness. Amorphous (transparent) and semi-crystalline (opaque) varieties are available. These polymers are useful for a wide range of manufacturing applications due to their gas barrier and chemical resistance. | Packaging film Trash and grocery bags Agricultural mulch Wire and cable insulation Squeeze bottle Toys Housewares |
Polypropylenes | These polymers have a reduced density and are suitable for thermal, chemical, and electrical applications. They require heat stabilization to work properly at high temperatures because of their weak heat resistance. Polypropylenes are less durable than high-density polyethylene and less brittle than low-density polyethylene, but PP injection molding are extremely fatigue resistant, making them an excellent choice for plastic hinges. | Lab equipment Carpets Textiles Packing Labeling |
Polystyrenes | These low-cost amorphous thermoplastics have a lesser heat resistance than other varieties and must be kept at temperatures below 200o F to retain their integrity. They do, however, have acceptable colorability, processing ease, hardness, and clarity, as well as good electrical qualities at ambient temperature and at typical humidity conditions. | Foam cups Smoke alarm housings Models Disposable cutlery CD/DVD cases |
Nylons | This categorization of thermoplastics includes a wide range of grades, each with its unique set of valuable features. Nylon has strong fuel, oil, and chemical resistance, as well as great fatigue resistance, hardness, and a low friction coefficient in general. | Carpet Rope Strings for musical instruments Fishing line Fabric |
Advantages and Disadvantages of Thermoplastic Materials
Source: Pinterest
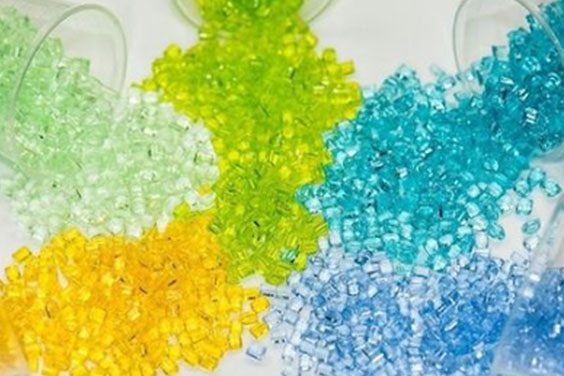
Advantages
Thermoplastic waste is reusable: Instead of dumping injection molding waste, thermoplastic materials may be recovered and re-melted for future use.
Higher-yielding material: Because of their recoverability, you’ll get a high piece yield from your entire material supply hence an advantage for medical plastic injection molding suppliers.
Easy to recycle: Thermoplastic materials are easy to recycle since they melt readily.
Good for prototyping: Because the goal of prototypes is to evaluate the functionality of things, using a reusable material is ideal. The plastic can be melted and re-molded for another prototype or production after the prototype has been tested.
Appropriate for high-impact applications: Thermoplastics’ molecular properties make them perfect for applications like plastic insert molding and overmold injection molding requiring high-stress resistance and strength.
Receptive to surface finishing: Thermoplastics are favored for items with decorations or logos because they adapt themselves to a wide range of surface finishing procedures and materials, making them ideal for consumer products.
Disadvantages
Not ideal for high-temperature applications: When exposed to enough heat, the material can liquefy, making them unsuitable for applications that need prolonged heat exposure. Highly polar solvents, organic solvents, and hydrocarbons are all resistant to thermoplastic materials.
Prone to creep: Creep happens when a material expands and eventually weakens as a result of extended stress exposure. Under high-stress situations, composites, a form of thermoplastic material, are prone to fracture.
Common Application of Thermoplastic Material
Thermoplastics plays a critical role in production, with applications in practically every sector. The pipe systems present in modern cities is one of the most common application of thermoplastic.
When it comes to preserving steel pipes from hostile conditions, the costs may be rather significant. Because they can endure corrosive situations, thermoplastic materials are ideal. They can also contain things that are both hot and cold, as well as any form of fluid.
Why Thermoplastics Is So Important for Injection Molding?
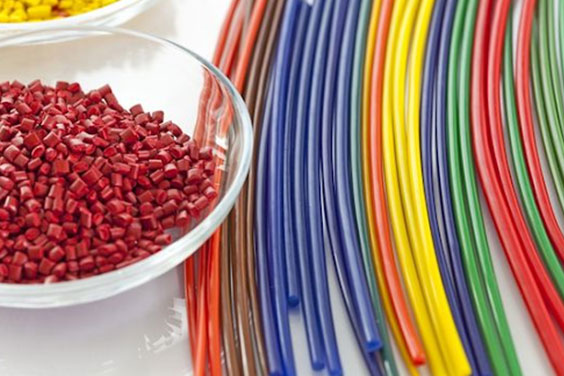
They’re common in manufacturing because they become viscous when heated, allowing for the production of precise geometries that the material keeps after cooling. As a result, making the best choice for a specific application can be difficult.
Thermoplastic materials may be remolded and recycled without compromising their physical qualities due to their unique chemical features. Thermoplastics are an excellent material for sterile injection molding because of this.
Because thermoplastic can be recovered and reincorporated into the raw material supply, you’ll nearly always get a better overall piece yield from your material stock than you would with a thermoset.
Although thermoplastics are normally more expensive than thermoset materials, the better production potential can more than makeup for the cost difference. When researching and purchasing materials for your product, be sure to keep that in mind.
Thermosetting vs Thermoforming
Thermosetting and therermoforming are different materials, below are the simple differences between thermosetting and Thermoforming.

Thermosetting
Once heated, thermosetting polymers cannot be remelted. Thermosetting polymers are interconnected like a web, resulting in increased rigidity. Thermosetting polymers are harder and heat resistant, making them ideal for electrical components and panhandles. They’re frequently generated from a liquid mixture that hardens and can’t be reformed:
- Camping plates and countertops are made of melamine.
- Araldite glue, casting resin, epoxy resin: a two-part resin and hardener that hardens when combined.
- Panhandles and bottle caps contain phenol-formaldehyde.
- Plug sockets, electrical switches, and door handle all contain urea-formaldehyde.
- Car bodywork and boats are made of polyester resin.
Thermoforming
Plastics that can be heated and molded repeatedly is known as thermoforming plastics. Thermoforming polymers are connected in long chains, making reheating and remolding simple. Thermoforming plastics are used to manufacture bendy plastics; they aren’t particularly heat resistant and can readily melt. It’s simple to recycle them by crushing them into pellets and reconstructing them:
- Milk cartons, buckets, and plates are made of polythene HDPE (high-density polyethylene).
- Food packaging, tote bags, dishwashing, and shampoo bottles are all made of polythene LDPE (low-density polyethylene).
- Syringes and reusable food containers are made of polypropylene PP.
- The casing on vacuum cleaners, radios, and other items is made of high-impact polystyrene (HIPS).
- Nylon injection molding is used for hinges, combs, and clothing.
- Pipes, shoe soles, and pill packaging are all made of polyvinyl chloride (PVC).
- Baths and machine guards are made of acrylic (Perspex).
Conclusion
We hope this blog has helped you understand the concept of thermoplastics and their applications. If you are unsure or need more information, you can go to SeaskyMedical for further information on production and manufacturing.