Injection molding is a common and inexpensive way of making both industrial and commercial parts. It offers many advantages over other manufacturing methods, including high precision, repeatability, and cost-effectiveness. It is also suitable for producing a wide range of parts, making it a versatile manufacturing method. With the advent of computer-controlled machines and automation, the process has become even more efficient and reliable.
However, there are many types of injection molding, with each having its distinctive preferred application. In this post, we will describe the different types of injection molding and state the products they are best used for.
What is Injection Molding
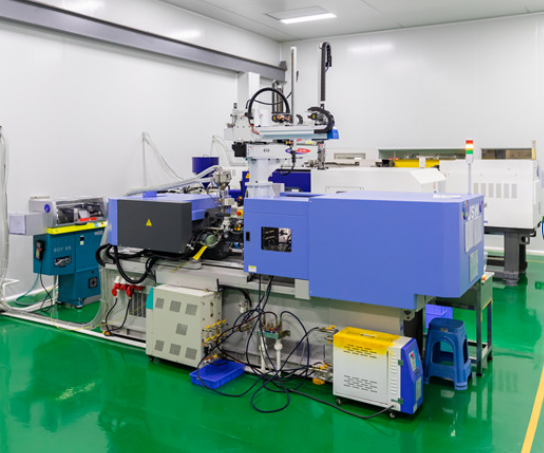
Injection molding is a manufacturing process used to produce parts by injecting molten material into a mold. The process is suitable for producing a wide range of parts, from small precision components to large, complex pieces. It is widely used by plastic molding companies to make different household, commercial, and industrial products.
How does Injection Molding Work
The process of injection molding begins with the creation of a mold, which is a hollowed-out cavity in the shape of the final product. The mold is typically made of steel or aluminum and is divided into two parts: the core and the cavity. The core is the inside of the mold and the cavity is the outside.
Once the mold is created, the next step is to heat the material to be injected, typically plastic pellets, until it is in a liquid state. The liquid material is then injected into the mold under high pressure, which forces it to fill the entire cavity. The material is then allowed to cool and solidify, which happens anytime from a few seconds to a few minutes.
What are the Types of Injection Molding
There are different types of injection molding. They include:
Plastic Injection Molding
This is a manufacturing process in which plastic material, in the form of pellets or granules, is heated and then injected into a mold under high pressure. This process can be used to create a wide variety of products, from simple household items to complex automotive parts, and medical components manufacturing.
Injection molding is a cost-effective way to produce high volumes of identical plastic parts. The process can be automated, and the molds can be designed and manufactured to produce intricate and precise parts with tight tolerances. Additionally, the process allows for the addition of color, texture, and other properties to the final product.
It is worth noting that the plastic injection molding can be done with various plastic resins, including thermoplastics, thermosets, and elastomers. Furthermore, new technologies and materials are being developed all the time, such as bioplastics, which are made from renewable resources and can be recycled more easily. As technology advances, the process will continue to evolve and adapt to new materials, making it even more versatile and efficient.
Micro-injection Molding
This is a manufacturing process in which very small parts, usually measuring less than 2mm in size, are produced using injection molding equipment. This process is similar to traditional injection molding, but it requires specialized equipment and techniques to handle the small size of the parts.
One of the benefits of micro injection molding is that it allows for the production of parts with very fine details and precise dimensions. Additionally, this process can be used to produce large quantities of parts at a relatively low cost. Micro injection molding is commonly used in the automotive, aerospace, and electronics industries, as well as microfluidic devices, optical components, miniature gears, and medical injection molding in a clean room.
However, the process is more demanding than traditional injection molding and requires precise control of the injection molding machine, mold, and process conditions. The small size of the parts also poses a challenge in terms of material handling, as well as in the inspection and testing of the finished parts. In addition, the cost of the tooling and equipment used in micro injection molding is generally higher than that used in traditional injection molding.
Overmolding
This is a manufacturing process in which a secondary material is injection molded over a primary substrate. This process is often used to create parts with multiple materials or to add a soft-touch grip or other functional features to a part.
It can be used with a wide range of materials, including plastics, rubber, and even metals. The process begins by placing the primary substrate into a mold, which is then closed. The secondary material is then injected into the mold, where it bonds to the primary substrate and takes on the shape of the mold.
Overmolding offers several benefits, including the ability to combine multiple materials into a single part, enhanced functionality through the use of different materials, improved ergonomics through the use of soft-touch grips, increased durability and resistance to wear and tear, and improved aesthetics through the use of different colors or textures.
This process is commonly used in the manufacturing of consumer electronics, automotive parts, medical devices, and other products. It can also be used to repair or modify existing parts.
However, overmolding is a complex process and requires precise alignment and timing of the two materials, which can be challenging to achieve. Also, it is not suitable for all types of products and materials, especially with plastic healthcare devices, which is why it’s important to work with experienced medical plastic manufacturers who have the necessary expertise and equipment to ensure success.
2K Injection Molding
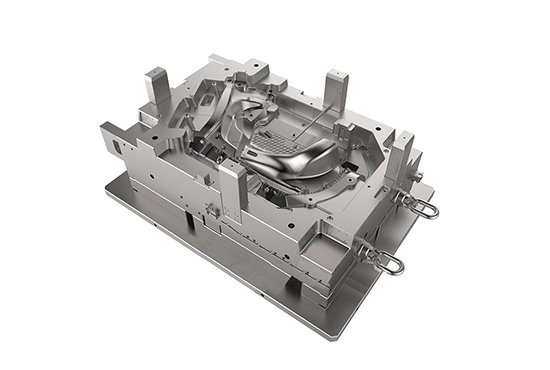
Also known as two-component injection molding or multi-component injection molding. This is a manufacturing process in which two different materials are injected into a single mold at the same time and then combined to form a single part. This process is often used to create parts with multiple colors or materials, or to achieve specific mechanical or physical properties in the final product.
The two materials used in 2K injection molding can be either thermoplastics or thermosetting plastics. The materials are typically injected into the mold through separate barrels and screws on the injection molding machine, and then combined in the mold to form the final part. The process is typically controlled by a computer, which ensures that the correct amounts of each material are injected and that they are properly mixed and blended together.
This injection molding is commonly used to produce products that require different properties for different parts. For example, a product may require a hard, durable exterior and a soft, flexible interior. It’s also used to reduce cost and weight of the final product.
2K injection molding process can be a bit more complex than traditional injection molding, as it requires special equipment and expertise to ensure that the two materials are properly mixed and blended together. However, it is a highly efficient and cost-effective way to produce complex, multi-material parts.
Insert Molding
This is a manufacturing process in which a pre-formed part, known as an insert, is placed into a mold and then injected with plastic or other materials to form a single, integrated piece. The insert can be made of metal, plastic, or other materials, and can be a simple component or a complex assembly. The process is used to produce a wide range of products, including electronic components, automotive parts, medical devices, and consumer products.
One of the main advantages of insert molding is that it allows for the integration of multiple materials and components into a single piece, reducing the need for additional assembly steps and increasing the strength and durability of the finished product. It also allows for the inclusion of specialized features such as threads, bearings, or electrical contacts, and can be used to produce parts with intricate geometries or tight tolerances.
Cube Molding
Also known as cubing or cuboid molding; it’s a method of creating three-dimensional objects by shaping a material, such as plastic or metal, into a cube or cuboid shape. The process typically involves heating the material to a malleable state and then shaping it into the desired shape using a mold. Once the material has cooled and hardened, it is removed from the mold, resulting in a precise and uniform cube or cuboid shape.
This injection molding process is a cost-effective method of manufacturing and is ideal for producing large quantities of identical items. Additionally, the process allows for a high degree of precision and control over the final shape and size of the product. It’s also a versatile method, with a wide range of materials and colors available to suit the needs of different applications. This method of molding is commonly used in the manufacturing of products such as small household items, toys, and industrial components.
Cubing is widely used in the mass production of items such as toys, electronics, automotive parts, and home appliances. This process is highly automated, which makes it efficient and cost-effective. It’s also a great way to produce a large number of identical items in a short amount of time. This process is used to make prototypes, as it is a quick and cost-effective way to produce a small number of parts.
Die Casting
This is a manufacturing process in which molten metal is injected into a mold (or “die”) at high pressure to produce parts with precise dimensions and a smooth surface finish. The process typically uses non-ferrous metals, such as aluminum, zinc, and copper, but can also use steel and other alloys.
There are two main types of die casting: hot chamber and cold chamber. In hot chamber die casting, the molten metal is already in a liquid state when it is injected into the mold, whereas in cold chamber die casting, the metal is first heated to a liquid state before being injected.
The die casting process begins by creating a steel mold, or die, in the shape of the desired part. The die is then mounted in a die casting machine, which consists of a furnace for heating the metal, a shot chamber for holding the molten metal, and a hydraulic or mechanical system for injecting the metal into the die. Once the metal is heated to the proper temperature, it is injected into the die under high pressure (typically between 1,000 and 30,000 psi). The metal solidifies quickly, taking the shape of the die. The die is then opened and the part is ejected.
Die casting is a relatively fast and efficient process that produces high-quality parts with tight tolerances and a smooth surface finish. It is commonly used to produce parts for a wide range of industries, including automotive, aerospace, electrical, and medical. The process is also highly customizable, as it can be used to produce parts in a wide range of sizes, shapes, and materials.
However, the cost of die casting can be high, particularly for small production runs, and the process may produce some scrap, depending on the part geometry and the skill of the operator.
Gas-assisted Injection Molding
Gas-assisted injection molding is a process used to manufacture plastic parts by injecting a gas, typically nitrogen, into a mold during the injection molding process. The gas is used to assist in filling the mold and to provide support for the plastic as it cools and solidifies. The gas also helps to reduce the amount of material needed to fill the mold, which can save on costs and weight.
The process is done by injecting a small amount of gas into the mold through a small nozzle, called a gas assist nozzle, which is typically located in the thickest section of the part. As the gas is injected, it pushes the plastic into the mold, filling it more quickly and evenly. The gas also cools the plastic more quickly, reducing the cycle time and improving the surface finish of the part.
Additionally, the gas helps to reduce the amount of material required to fill the mold, which can save on costs and weight. This process is particularly useful for creating large, complex parts with thick sections, such as automotive parts, household appliances, and toys.
Liquid Silicone Rubber Injection Molding
This injection molding process is used to manufacture parts from Liquid Silicone Rubber (LSR). The process involves injecting a measured amount of liquid silicone rubber into a heated mold, where it is then cured into the desired shape. The mold is typically made of steel or aluminum, and is precision-machined to the exact specifications of the desired part.
One of the main benefits of LSR injection molding is its ability to create highly detailed and complex parts with tight tolerances. The liquid nature of the silicone rubber allows it to flow easily into the smallest crevices of the mold, creating a detailed replica of the mold’s surface. This makes LSR injection molding well-suited for creating parts with intricate geometries, such as those found in medical devices and electronic components.
Another advantage of LSR injection molding is its ability to produce parts with consistent quality. Because the silicone rubber is injected into the mold under high pressure, the material fills the mold completely and evenly, resulting in parts with minimal shrinkage and warping. Additionally, LSR is a thermoset polymer, meaning it will not melt when heated, which makes it a great choice for high-temperature applications.
LSR is also biocompatible, which makes it suitable for use in medical devices that come into contact with human tissue. And it has good electrical insulation properties and chemical resistance, which makes it suitable for use in electronic components.
Metal Injection Molding
This is a manufacturing process that combines the design flexibility of plastic injection molding with the strength and integrity of metal parts. It involves the mixing of metal powder with a binder material to create a feedstock, which is then injection molded into a desired shape. The molded part is then debound, sintered, and heat treated to remove the binder and densify the metal.
Metal injection molding (MIM) is typically used to produce small, complex, and high-strength metal parts that would be difficult or expensive to manufacture using traditional methods such as machining or casting. The process is capable of producing parts with tight tolerances and excellent surface finish.
The feedstock used in MIM can be made from a variety of metal powders, including stainless steel, tungsten, cobalt-chrome, and titanium, which allows for a wide range of material options.
This process is a cost-effective solution for producing small quantities of parts, as the cost of tooling is significantly lower than that of traditional metal manufacturing methods. And it’s widely used in various industries such as medical devices, aerospace, automotive, and firearms. Its applications include gears, valves, bearings, and structural components.
Reaction Injection Molding
This is a manufacturing process used to produce complex, high-performance plastic parts. It is a variation of the injection molding process, but with the addition of a reactive chemical system that is mixed and injected into a mold. The chemical reaction that occurs between the two or more components creates a polymer that solidifies and forms the desired part.
RIM is commonly used to produce parts for the automotive, electronic, and medical industries, as well as for consumer products. It is particularly useful for creating large, complex parts with tight tolerances and high strength and durability. RIM parts are also lightweight and have a high resistance to chemicals and UV light.
This process begins with the preparation of the two or more reactive components, which are typically liquid polyisocyanates and polyol resins. These components are mixed together in a high-pressure injection unit and then injected into a heated mold. The chemical reaction between the components creates a polymer that solidifies and fills the mold. The mold is then cooled and opened, and the finished part is removed.
RIM is a highly efficient and cost-effective process that can produce high-quality, complex parts with minimal waste. However, it does require specialized equipment and skilled operators. It’s sensitive to variations in temperature and pressure though.
Thin-wall Injection Molding
This is a specialized process used to produce plastic parts that are thin-walled and have a high strength-to-weight ratio. This is achieved by using a highly engineered, custom-built mold and specialized injection molding equipment that can inject molten plastic at high speeds and pressures. The process is typically used to produce parts that are less than 1mm in thickness and have a complex shape, such as food packaging, medical equipment, and electronic components.
One of the key challenges of thin-wall injection molding is ensuring that the plastic cools and solidifies quickly enough to prevent warping or deformation. This is accomplished by using a combination of cooling channels in the mold, high-speed injection, and precise temperature control. Additionally, the mold itself must be designed with precise tolerances to ensure that the finished parts are accurate and consistent.
Another challenge is ensuring that the plastic is injected evenly and completely fills the mold, which can be achieved by using a high-speed, high-pressure injection system. Additionally, the use of a thin-wall molding process requires the use of high-performance plastic resins that have a higher flow rate and lower viscosity
RJG Injection Molding
Named after a company, Resourceful Joints Group (RJG) that specializes in providing solutions for the injection molding industry. They offer a variety of products and services, including training, software, and equipment that are designed to help injection molders, including medical molding companies improve the efficiency and quality of their operations.
One of the key areas of focus for RJG is the use of sensors and monitoring systems to track the performance of injection molding machines and identify areas for improvement. This can include monitoring things like temperature, pressure, and flow rate, as well as analyzing data to identify patterns and trends that can indicate potential issues.
Another important aspect of RJG’s approach is the use of training and education to help molding operators and technicians improve their skills and knowledge. This can include classes on topics such as mold setup and maintenance, process control, and troubleshooting, as well as customized training programs tailored to the specific needs of a particular company.
Overall, RJG’s goal is to help injection molding companies optimize their processes and improve their bottom line by increasing efficiency, reducing defects and scrap, and improving the overall quality of their products.
3D Prototyping
This is the process of creating a physical model of a three-dimensional object using computer-aided design (CAD) software. The prototype can be used to test the design and functionality of the final product before it goes into mass production. There are various methods of 3D prototyping, including additive manufacturing (also known as 3D printing), subtractive manufacturing (such as CNC machining), and rapid prototyping.
Additive manufacturing involves building up layers of material to create the prototype, while subtractive manufacturing involves cutting away material to create the prototype. Rapid prototyping is a term that refers to a variety of methods, including both additive and subtractive manufacturing that can be used to quickly create a prototype.
3D prototyping is used in a variety of industries, including automotive, aerospace, consumer electronics, medical devices, and many more. It allows designers and engineers to test the functionality and design of a product before committing to mass production, which can save time and money in the long run. Additionally, it allows for the creation of complex geometries and internal structures that would be difficult or impossible to create using traditional manufacturing methods
Types of Plastic Molding
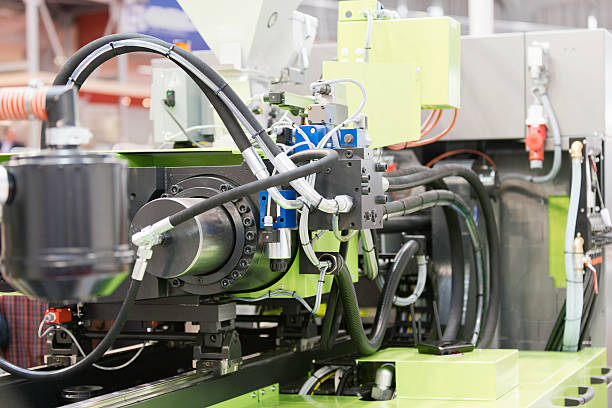
Plastic is one of the most popularly used materials in making products. And this is because of the several benefits they provide, which includes ease of production, lightweight, durability, and many more. There are different types of plastic molding process used for making plastic products. They include:
Plastic Injection Molding
Plastic injection molding is a manufacturing process for producing parts by injecting thermoplastic and thermosetting polymers into a mold. It is a versatile method for producing a wide range of parts, from small components to large, complex pieces.
The process begins by melting plastic pellets in a machine called an injection molding machine. The molten plastic is then injected into a mold, where it cools and solidifies into the shape of the mold. Once the plastic has cooled, the mold is opened, and the part is ejected. The mold is then closed, and the process is repeated to produce more parts. It’s used by the leading custom plastic injection molder because of its speed of production and efficiency.
Compression Molding
Compression molding is a manufacturing process in which a pre-heated plastic material is placed into a mold cavity, and then the mold is closed and clamped under pressure. The heat and pressure cause the plastic to melt and fill the mold, taking on the shape of the mold. The mold is then cooled, and the solidified part is removed.
It’s a versatile process that can be used to create a wide variety of parts, from small electronic components to large industrial parts. The process is particularly well-suited to creating parts with complex shapes, tight tolerances, and uniform wall thicknesses. The process is also well suited for producing large numbers of identical parts, as the molds can be used repeatedly.
One of the main advantages of compression molding is that it is a relatively low-cost process, especially when producing large numbers of parts. The materials that can be used in compression molding include thermoplastics, thermosetting plastics, and rubber.
Blow Molding
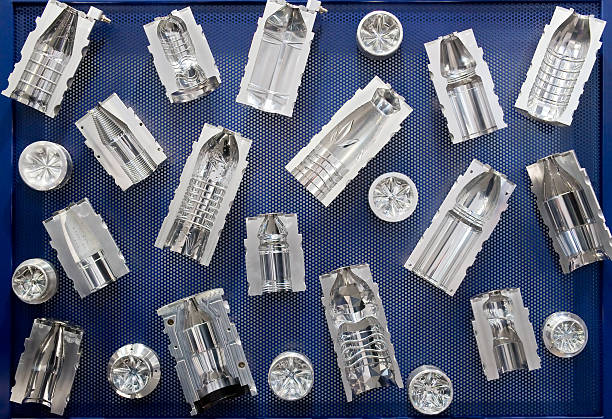
Blow molding is a manufacturing process used to create hollow plastic parts by inflating a heated plastic tube to conform to a mold. It’s a versatile and cost-effective way to create a wide range of hollow plastic parts and is commonly used for consumer goods, packaging, automotive, and medical device injection molding. It offers a high level of precision, with minimal waste and low production costs. There are three main types of blow molding: extrusion blow molding, injection blow molding, and stretch blow molding.
In extrusion blow molding, a cylinder of heated plastic is extruded through a die and into a mold. Air is then blown into the plastic to inflate it and conform to the shape of the mold. This process is used to create items such as bottles and containers.
Injection blow molding is similar to extrusion blow molding, but the plastic is first injection molded into a preform, which is then inflated and blow molded into the final shape. This process is commonly used to create small, precision parts such as medical bottles and containers.
Stretch blow molding is used to create hollow parts such as bottles and containers from thermoplastic materials, such as PET. In this process, a preform is heated and stretched using a blow molding machine, which inflates the preform and forms it into the shape of the mold.
Extrusion Molding
Extrusion molding is a manufacturing process in which a material, typically plastic, is melted and formed into a continuous profile. This process is similar to injection molding, but instead of injecting the melted material into a mold, it is forced through a die to shape the final product. The extruded material is then cooled and cut into the desired length.
This molding is used to create a wide range of products, including pipes, tubing, and cable insulation. It is also used to create products with a consistent cross-sectional shape, such as window frames and door frames. Additionally, it can be used to produce complex shapes, such as hollow tubes and solid rods, by adjusting the die shape.
The extrusion process can be done with either a single or a twin screw extruder machine. Single screw extrusion is typically used for simple shapes, while twin screw extrusion is used for more complex shapes and for mixing different materials together. The material is fed into the extruder and is heated and compressed as it moves through the machine. The die at the end of the extruder shapes the material as it is forced through.
Rotational Molding
Rotational molding, also known as roto-molding, is a manufacturing process used to produce hollow plastic parts. The process involves heating a hollow mold, which is filled with a plastic powder or pellet, to a high temperature. The mold is then rotated around two perpendicular axes, causing the melted plastic to evenly coat the interior surface of the mold. The mold is cooled, and the part is removed.
One of the main advantages of rotational molding is that it allows for the production of large, complex parts with uniform wall thickness. Additionally, the process is relatively low-cost and can be used to produce a wide range of shapes and sizes. Rotational molding is commonly used to produce tanks, playground equipment, kayaks, and other outdoor products.
The process has several steps, including loading the powdered plastic into the mold, heating the mold to melt the plastic, rotating the mold to evenly distribute the plastic, cooling the mold to set the plastic, and then removing the final product.
One limitation of rotational molding is that it is not well-suited for producing small, intricate parts or parts with thin walls. And the process is relatively slow, which can be an issue for high-volume production. However, for many applications, rotational molding is a cost-effective and efficient manufacturing method that offers a number of benefits over other processes.
Conclusion
Injection molding is arguably the most popular manufacturing method used across many industries, especially the medical industry. And this is because it provides safety for precise and healthcare operations. Above, we’ve mentioned other industries that apply injection molding, as well as the different types of injection molding. With this, you will be able to note the molding process that’s best suited for your need.
Having a specialty in one-stop injection molding manufacturing and clean room injection molding, we are here to help. We will assist you by shedding more light on any questions or worries you have about the different types of the molding process. Contact us to enjoy the best service available.