Though there is a variety of plastics available, it cuts down to two, thermoplastic and thermosets, when it comes to injection molding. Even though they are both polymers, and it is easy to assume there is no significant difference between them, thermoset and thermoplastic have vastly different thermal and chemical properties.
Most medical plastic injection molding suppliers give their customers the option of thermoplastic or thermoset materials for medical device injection molding. However, not everyone is aware of the distinction. So, without further ado, let’s dive into this in-depth article to view the key differences between thermosets and thermoplastics and the applications that may be made with them.
What Is Thermoplastic Material?
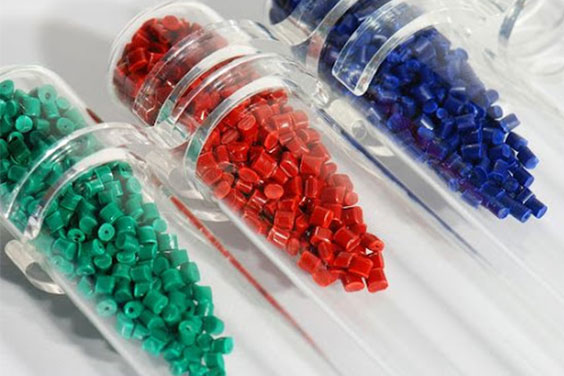
In order to bring a definite shape, plastics are usually seen melted with heat; these types of plastic materials are what we refer to as thermoplastic materials. In layman’s terms, plastic that melts when subjected to heat and returns to a solid set once cooled is called thermoplastic materials.
Thermoplastics may be reshaped in their melted liquefied state and are commonly used to manufacture parts using polymer processing techniques such as injection molding, compression molding, clean room molding, calendering, and extrusion.
Because of their chemical flexibility, thermoplastics are becoming a more desirable option for all medical overmolding companies.
When melted with heat, the plastic material will not undergo any significant changes in the chemical properties, making it possible to recycle the manufactured product again. Also, Thermoplastics are mainly resistant to chemical attacks, which makes them suitable for many process applications. Depending on their intended use, like disposable medical supplies manufacturering, these plastics are selected based on certain process specifics.
Thermoplastics are subjected to more than just heating and cooling. Plastics become brittle and more sensitive to break after cooling, so companies add plasticizers and use copolymerization to harden the plastic and make it stronger.
Due to their qualities, thermoplastics are a prominent choice in the injection molding sector. Various varieties are utilized for multiple purposes in various industries, most notably the healthcare, pipe, and textile industries.
Advantages of Thermoplastic Material

Here are some advantages of thermoplastic materials:
- Thermoplastics are often processed in an energy-efficient manner.
- Thermoplastic is used in a wide range of common products, and it has a wide range of positive qualities.
- High-volume, high-precision production at a cheaper cost.
- Various varieties can be used to replace metals, resulting in significant weight savings.
- Thermoplastics have a higher fatigue resistance than most metals. Therefore they are less likely to split or cripple when damaged.
- Without deforming, it can withstand more deflection than most metals.
- They’re also stained and chemical resistant so that they won’t discolor or yellow when exposed to cleaners, solvents, or chemicals.
- Because thermoplastics are recyclable, they are suitable plastic substitutes for a more environmentally friendly purpose.
Disadvantages of Thermoplastic Material
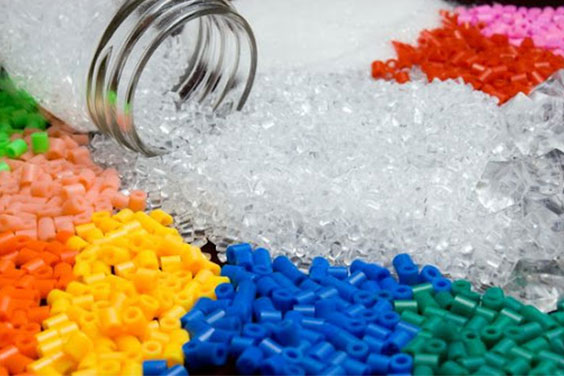
Here are some disadvantages of thermoplastics you should note down:
- Thermoplastics deteriorate more quickly in direct sunshine or when exposed to ultraviolet radiation.
- Not all thermoplastics are resistant to hydrocarbons, organic solvents, and polar solvents; some are rapidly damaged when exposed to these substances.
- Under long-term loading, some types incur creep.
- Under severe stress, many thermoplastic materials, particularly composites, tend to fracture rather than deform.
- Due to high toxicity levels, producing thermoplastic is dangerous to employees’ health.
- Thermoplastic materials are more expensive than thermosets.
- Some thermoplastics tend to yellow when exposed to direct sunlight over an extended period of time or kept under full-spectrum lights.
Types of Thermoplastic Materials

Depending on the type of chemical state, properties and application, there are different types of thermoplastics; here is a list of popular ones:
- Acrylic
- ABS
- PLA
- Nylon
- Polybenzimidazole
- Polycarbonate
- Polyethersulfone
- Polyoxymethylene
- Polyether ether ketone
- Polyetherimide
- Polyethene
- UHMWPE or ultra-high-molecular-weight polyethylene
- HDPE or High-density polyethylene
- MDPE or Medium-density polyethylene
- LDPE or Low-density polyethylene
- Polyphenylene oxide (PPO)
- Polyphenylene sulfide
- Polypropylene (PP)
- Polystyrene
- Polyvinyl chloride (PVC)
- Polyvinylidene fluoride
- Polytetrafluoroethylene (Teflon)
What Is a Thermosetting Plastic?
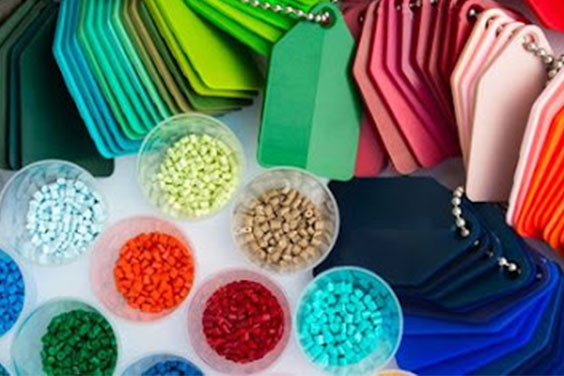
Thermosetting plastics are starkly opposite to thermoplastics. In contrast to thermoplastics, which are melted and cooled, thermosets are often soft solids or viscous liquids poured into a mold and subsequently cured. Another essential factor to note about thermosetting plastics is that they cannot be reversed once they have solidified.
Thermosetting plastics, such as resin, are typically available in liquid form. The liquefied plastic is poured into a mold and allowed to cure for some time. Curing is a procedure in which a particular point of radiation or heat is applied to the plastic, causing the polymer chains to react and transform the plastic into a solid-state.
Curing does not always require heat; in some instances, all that is required is the addition of a curing agent, a catalyst, or a hardener. In contrast to thermoplastic polymers, which are frequently produced and distributed in the form of pellets and molded into the final product form by melting, pressing, or injection molding, thermoset polymers cannot be melted for reshaping once solidified.
Due to the three-dimensional network of bonds (crosslinking), thermosetting plastics are generally stronger than thermoplastic materials. They are also better suited to high-temperature applications up to the decomposition temperature because solid covalent bonds between polymer chains cannot be easily broken.
Advantages of Thermosetting Plastic
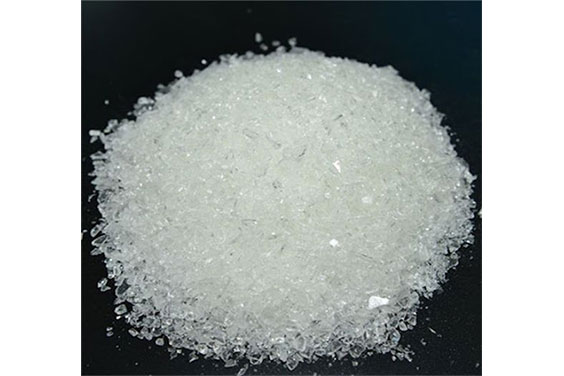
Here are some advantages of thermosetting plastics:
- Because thermosetting polymers are soft solid or liquid in their natural state, they can be designed in a variety of ways.
- It can be molded to a variety of tolerances.
- Wall thickness can be varied to improve structural integrity.
- The price of thermosetting plastics is usually lower.
- It has outstanding electrical insulating qualities.
- Thermosetting plastics are more resistant to high temperatures.
- Exceptionally corrosion-resistant.
- Thermal conductivity is low.
- Compared to thermoplastics, setup and tooling costs are lower.
- To optimize product performance, it has a high strength-to-weight ratio.
- Colors and surface finishes are available in a variety of options.
- The thermoset polymers have a higher temperature resistance than thermoplastics.
Disadvantages of Thermosetting Plastic
Here are some disadvantages of thermosetting plastics:
- The thermosetting resin is a disposable material that is difficult to recycle and reuse once thermosetting plastics have solidified.
- Their tensile strength and elasticity are both low.
- Once a thermosetting resin has been crosslinked and hardened, it cannot be reversed or molded.
- For housing replacements, the heat conductivity is poor.
- Surface finishing is much more complex.
- When utilized in high-vibration situations, the material’s stiffness might lead to product failure.
- It is difficult, if not impossible, to repair damage once it has occurred.
Types of Thermosetting Plastic

Depending on the type of chemical state, properties and application, there are different types of thermosetting plastics; here is a list of popular ones:
- Polyester resin
- Polyurethanes
- Vulcanized rubber
- Bakelite
- Duroplast
- Urea-formaldehyde
- Melamine resin
- Diallyl-phthalate (DAP)
- Epoxy resin
- Epoxy novolac resins
- Benzoxazines
- Polyimides
- Bismaleimides
- Cyanate esters
- Furan resins
- Silicone resins
- Thiolyte
- Vinyl ester
Difference Between Thermoplastic and Thermosetting Polymer
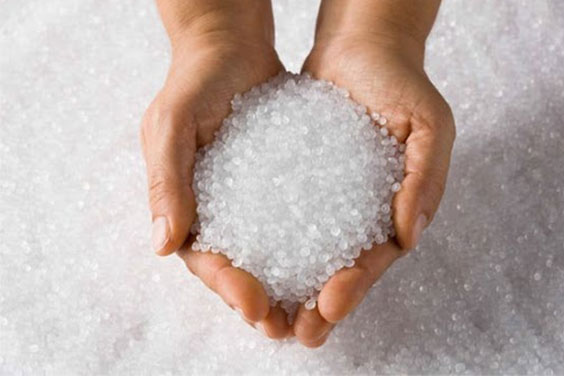
Thermoplastics and thermosetting plastics are two polymers with pretty distinct characteristics and applications. We’ve seen some abstract contrasts between the two polymer groups up to this point; now, let’s look at more comprehensive descriptions of thermoplastic and thermosetting plastic differences:
Process Methods
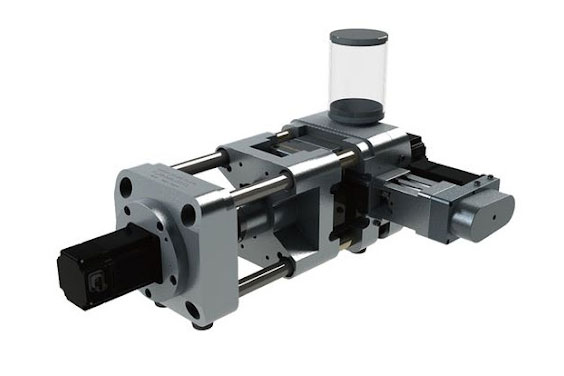
For Thermoplastics:
Thermoplastics are a type of flexible polymer that may be reused and recycled. As previously stated, there are several process methods for manufacturing and shaping thermoplastics, including:
- Extrusion – Extrusion is a high-volume manufacturing method that involves melting raw plastic and forming it into a continuous shape.
- Injection Molding – Injection molding is a manufacturing process that involves injecting plastic resin into a pre-made plastic injection mold design to generate completely functional parts.
- Compression Molding – Thermoplastics are transformed into high-volume, dimensionally exact, high-strength, temperature resistant products with good surface quality by compression molding.
- Blow Molding – Blow molding is a manufacturing process that involves inflating a heated plastic tube until it fills a mold to manufacture hollow plastic pieces.
- Rotomolding – Rotomolding is a manufacturing technology that involves using plastic molding tools that allow for creating hollow pieces of any size.
For Thermosetting Plastics:
Thermosetting plastics can be processed in a variety of ways to obtain shapes and qualities, in addition to their exceptional performance properties. There are several process methods for manufacturing and shaping thermosetting plastics, including:
- Compression Molding – Compression molding is a process in which heat and severe force are used to compress plastics into a specific shape with a mold.
- Filament Winding – Fibers are soaked in resin before being wound onto a mandrel until they reach the desired thickness.
- Pultrusion – A continuous pulling mechanism pulls glass fiber and rovings through a resin bath and subsequently through a heated die. As it travels through the die, the material is produced and cured.
- Wet Lay-Up Compression Molding – Resin is put over a glass mat and loaded into a press, and then the mold is closed. The substance cures when it is exposed to heat and pressure.
- Injection Molding – the thermosetting plastic is placed in a heated barrel and injected into a closed, heated mold in the Bulk Molding Compound (BMC) injection process. BMC is liquefied and poured into the mold, and components are evacuated and finished when cured. Smaller, high-volume items in aesthetic applications are better suited to micro injection molding.
Recyclability
Thermoplastics may be reheated and remolded for various purposes, making them recyclable. The thermoplastic polymers are strong, but their bonds are weak. These materials are highly recyclable because they may be reused endlessly.
Thermosetting plastics can’t be melted down to make new items, but they can be reused in various ways. Polyurethane foam is a great example. Flexible polyurethane foams are frequently shredded into small flakes and repurposed as carpet underlayment.
Synthesis Method
The process of addition polymerization can be used to make thermoplastics. Condensation polymerization is used to make thermosetting polymers.
Properties
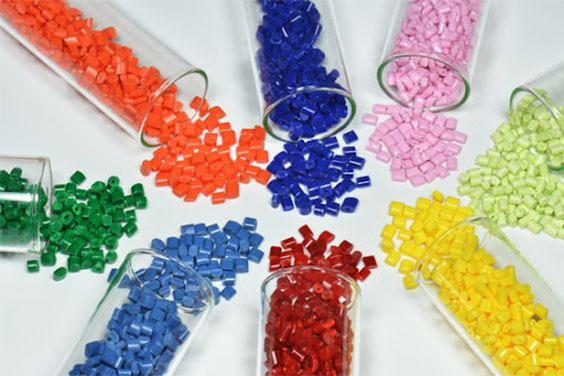
Properties of Thermoplastics:
The essential and unique properties of thermoplastics are:
- Thermoplastics are made up of straight-chained linear polymers with weak molecular bonds.
- The melting point of thermoplastics is low.
- Thermoplastics are elastic and flexible.
- Thermoplastics go through a process called addition polymerisation, in which the plastics are polymerised throughout the manufacturing process.
- Highly chemical resistant
- Organic solvents can be used to dissolve it.
Properties of Thermosetting Plastics:
The essential and unique properties of thermosetting plastics are:
- Network polymers with a high level of crosslinking and strong chemical molecular connections make thermosetting plastics.
- The melting point of thermosetting polymers is very high.
- Thermosetting polymers are rigid and inelastic.
- Thermosetting polymers go via polycondensation polymerization, in which the plastics are polymerized while being processed.
- Resistant to heat and chemicals.
- Organic solvents should not be used to dissolve the product.
Strength
Thermoset polymers are tougher and more durable than thermoplastics, which soften when heated. Because of their covalent solid crosslinks, thermosets do not soften and have superior dimensional stability to thermoplastics.
Melting Points and Tensile Strength
The melting point of thermoplastics ranges from 6500 to 7250 degrees Fahrenheit. Thermoplastics have high tensile strength, with PAI having the highest at about 60. The melting point and tensile strength of each kind differ.
Thermosetting plastics do not have a melting point because they burn rather than melt when subjected to high temperatures. The tensile strength ranges from 68 to 200, albeit depending on the type.
Molecular Weight
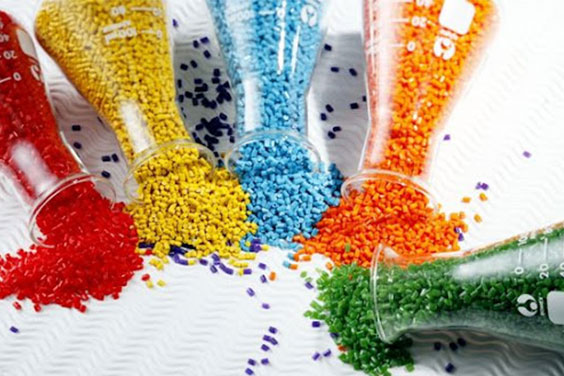
Thermosetting plastics have a higher molecular weight than thermoplastics, which could be attributed to the fact that when two thermosets crosslink, a polymer network with a molecular weight nearly double that of the two thermosets when they were separate is created. The molecular weight continues to climb as the number of connected molecules rises, eventually surpassing thermoplastics.
Aesthetic Difference
Thermosets can create low and high-gloss finishes at a lower cost right out of the mold. Thermosets that have been painted can appear to have beautifully detailed surfaces. Logos can also be added to thermosetting polymers.
What Are the Applications of Thermoplastic and Thermosetting Plastic?
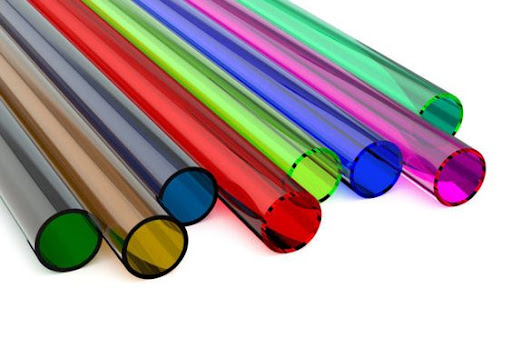
Thermoplastic and thermosetting plastics are two types of polymers used to make a wide range of everyday items for various industries, including healthcare, electricity, and many more. Let’s have a look at some of the uses for thermoplastic and thermosetting plastics:
Application of Thermoplastic
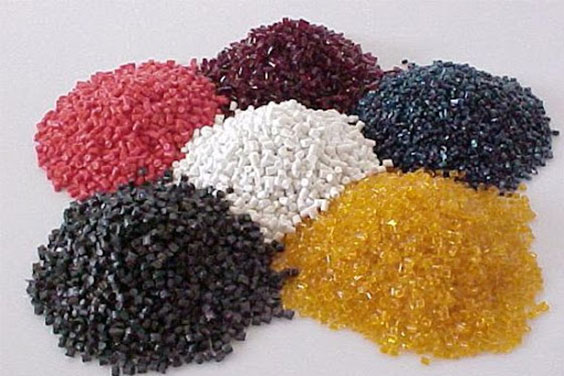
The applications of thermoplastics are:
- Parts for industrial machines.
- Electrical encapsulation and insulating materials
- Medical laboratory supply.
- Non-stick cookware
- Gas tanks
- Piping systems
Application of Thermosetting Plastic
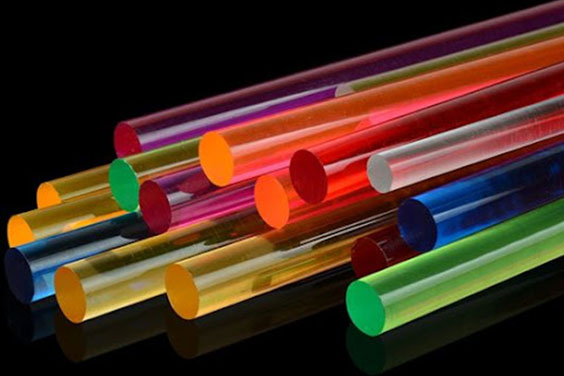
The applications of thermosetting plastics are:
- Electronic enclosures.
- Pipes, cell coverings, and fittings are examples of chemical processing equipment.
- Doors, panels, and housings.
- Medical instruments.
- Components and parts for vehicles
Which One Is Better for Injection Molding?
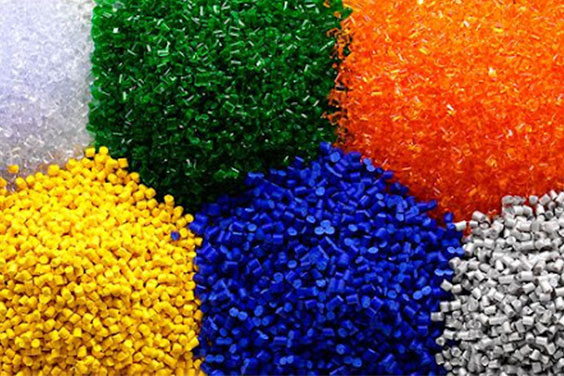
Injection molding can be used to make molded items out of both thermoplastics and thermosetting materials. When compared to thermoplastic injection molding, thermoset injection molding does not require significant heat or pressure, but thermoplastic injection molding requires.
So whether to choose depends on the types of products and durability you want.
Conclusion
With the pivotal details like properties, types, and applications mentioned, we are sure that you’ll have a better notion of which sort of polymer to use to make molded parts. If you are unsure or need more information, you can go to SeaSky Medical for further information on production and manufacturing.