With respect to that both vacuum forming and thermoforming need heat, they are quite similar. However when comparing, thermoforming vs vacuum forming, the two processes are utilized for distinct objectives. Vacuum forming is a procedure that occurs when plastic is heated to a specific temperature. Thermoforming is the process of producing plastic under extreme pressure and heat.
What Is Vacuum Forming?
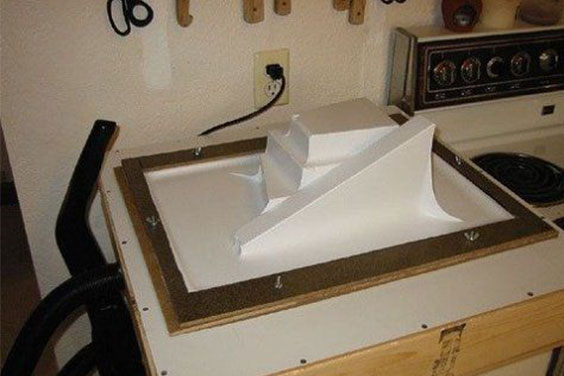
One of the earliest and most used methods of treating plastic materials is vacuum forming. Products made by vacuum forming can be found everywhere and play an important role in our daily lives. It is widely used to mold plastic into permanent things.
The procedure entails softening a plastic sheet before wrapping it over a mold. The sheet is sucked into the mold using a suction. After that, the sheet is removed from the mold. The vacuum forming process, in its enhanced version, employs complex pneumatic, hydraulic, and heat controllers, allowing for faster production speeds and more precise vacuum formed products.
The vacuum forming binds separate pieces together, resulting in a single mold that can be easily duplicated.
What Is Pressure Forming?
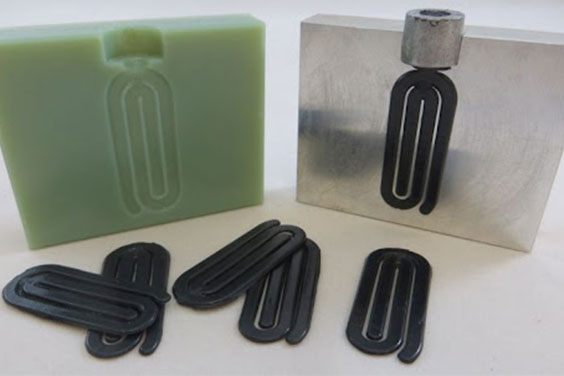
Pressure forming is an innovative procedure that involves applying vacuum and pressure to the opposite sides of a plastic sheet to generate the required structure or mold.
In most cases, this process works differently than vacuum forming. Instead of pulling out the air between the material and the mold with a vacuum, pressure forming uses high air pressure to drive the plastic down into the mold’s core. The mechanism that holds the plastic molds in position in pressure forming ensures that the material is melted with the optimum temperature for flexible mold making.
The potential of thermoforming machines to generate objects with better components, finer edges, and higher quality makeup are the advantages of pressure-forming plastic items.
What Is Thermoforming?
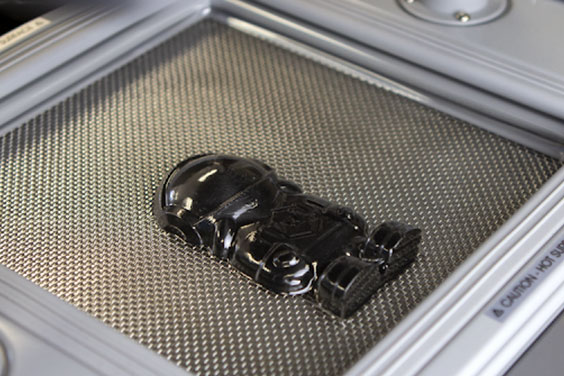
Thermoforming is the method of weakening a thermoplastic sheet by heating it to a certain temperature. The sheet is extended and controlled across a single-sided mold. Then it cools to its final shape. Vacuum-forming and pressure-forming are the most popular ways of getting the sheet to bend to its ultimate shape.
Thermoforming can be utilized in a variety of sectors and has a wide range of applications. The adaptability of thermoforming is one of its best features. This is seen in the wide range of materials that can be utilized in the procedure. Each material is ideally suited to certain applications and uses.
What Are the Differences Between Vacuum Forming, Pressure Forming, and Thermoforming?
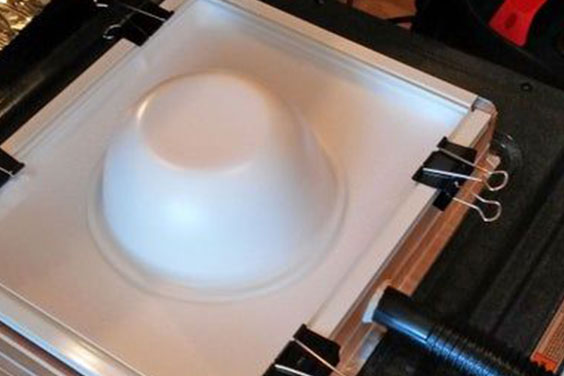
Under the scope of plastic thermoforming, the 2 most prevalent manufacturing procedures are pressure and vacuum forming. The only prominent difference between the three is the process of applying pressure/vacuum to turn the heated plastic sheet into a product. There are other differences as well, that we will discuss in detail below.
Process
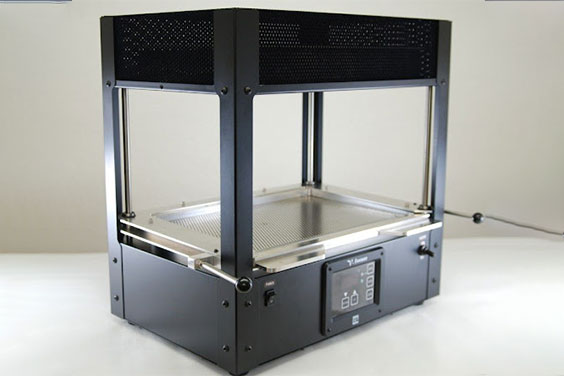
What Is the Vacuum Forming Process?
The following is a step-by-step vacuum forming procedure:
- A plastic sheet is clamped into position in an open frame.
- Heat is used to soften the plastic sheet till it reaches the proper molding temperature and becomes pliable.
- The framework holding the heated, malleable sheet of plastic is dropped over a mold and held into place by suction on the other side.
- The plastic must cool after it has been molded around/into shape.
- The plastic is taken out of the mold and removed from the framework once it has cooled.
- The surplus material is trimmed from the final product.
What Is the Pressure Forming Process?
Pressure forming is a modern plastic manufacturing method in which a plastic sheet is shaped to a complex and intricate shape with a single-sided mold using vacuum and pressure on different sides of the sheet to generate the formed shape. The vacuum forming technique is enhanced by pressure forming. The pieces are created in classic vacuum forming by establishing a vacuum on the sheet’s mold surface.
What Is the Thermoforming Process?
Thermoforming is the process of heating a plastic sheet to its melting point, loosening it over or into a single-sided container, and holding it in position while it cools down into the correct shape. The sheet is clamped into a gripping mechanism and softened in an oven with radiation. Using vacuum pressure, the sheet is then placed horizontally on a mold and forced into the mold. The softened sheet fits into the mold’s shape and is kept in place until it cools.
Mold Tooling
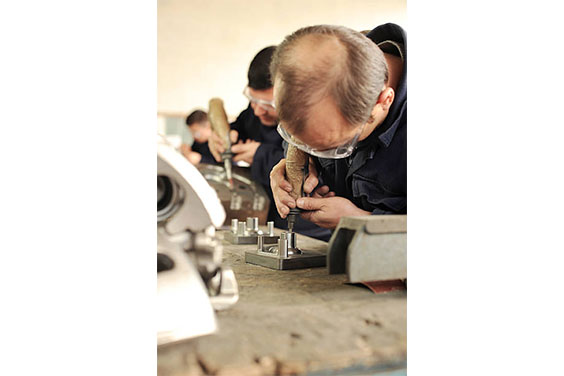
Mold Tooling Used in Vacuum Forming
A single mold along with a vacuum pump is used for vacuum forming. The heated sheet is inserted into the mold, and suction is used to ensure that it is correctly seated in the appropriate shape mold. It’s mostly employed in the curved packaging of foods, electronics, and other products. Instead of using a vacuum from the vacuum pump, the sheet is placed in a single mold and then pressed into the desired shape.
Mold Tooling Used in Pressure Forming
Pressure forming uses a combination of vacuum and pressure to compress the soft, hot plastic against the mold, resulting in a part with fine detail. Components produced by pressure forming have more precision and sharper features than parts produced by vacuum forming. In reality, pressure forming may generate highly detailed structures and aesthetics on par with injection overmolding.
Mold Tooling Used in Thermoforming
With the correct thermoforming mold, you can achieve consistent sharp lines, edges, roughness, and other features from piece to piece. Mold tooling for thermoformed products is easier to update or redesign. Replaceable mold inserts provide versatility, allowing you to modify styling characteristics or generate multiple models within a product series.
Application
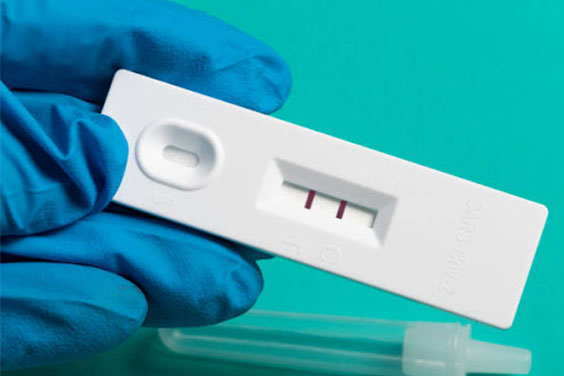
Applications of Vacuum Forming
Vacuum forming finds use in several sectors such as:
- Agriculture: Vacuum forming is commonly used in the agriculture business to make plastic components for heavy-duty machinery.
- Medical: lab consumables suppliers makes use of vacuum forming in producing trays, carts, pads, etc.
- Packaging: The plastics used in vacuum forming are also excellent for packaging.
- Retail: This specialized fabrication method has an infinite number of applications, and retailers are employing it to build promotional displays to attract the attention of customers.
Applications of Pressure Forming
Pressure forming is widely used for its options of custom mold and design. for Bezels, bases, housings, beautifully designed casings, coverings, and equipment panels are examples of pressure forming uses. It can provide precise and desirable designs for cleanroom molding medical devices, outdoor equipment, outdoor enclosures, retail products, transport, and construction equipment.
Applications of Thermoforming
In general, if you work in a manufacturing field, there’s a strong possibility you use or should utilize, thermoforming to create parts of your products. Thermoforming has a wide range of uses in production. Although this is not an extensive list, it does provide an overview of some of the most popular thermoforming applications.
- Automotive: For automotive parts such as dashboard, car handles, cup holders, etc.
- Aerospace and Aviation: For internal and external parts of aerospace equipment
- Business equipment: Small and large parts of business equipment
- Medical equipment: A medical device injection molding factory can assist you in all the stages of production
- Transportation: For seating and interior paneling
- Building and construction: For machinery covers, tool cases and skylights
- Recreational equipment: Fitness equipment and protective cases uses thermoforming for production
Advantages
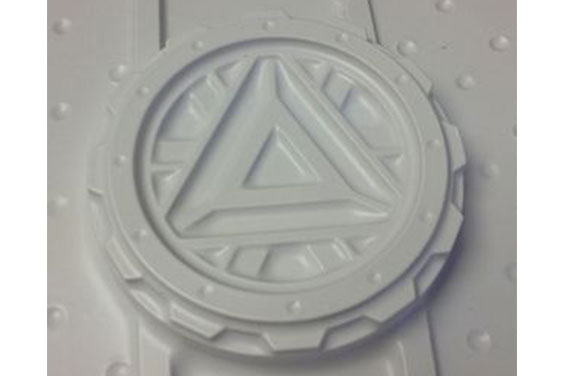
Advantages of Vacuum Forming
Some of the advantages of employing vacuum forming are:
- Each piece is made in a timely manner.
- Manufacturing costs are low.
- Molding costs are low
- Shapes and sizes are usually consistent from lot to lot, especially when the same mold is used numerous times.
- Mold forms and sizes are adaptable and adjustable.
- Scale production can go up or down as required, and create new components as needed.
Advantages of Pressure Forming
Some of the advantages of employing pressure forming are:
- Pressure-formed items can have sharp, precise surface details and characteristics that are comparable to those seen in insert injection molding.
- The procedure allows the plastic to pick up finely-grained surface features and provide finer surface finishes.
- Logos, lettering, and images may be produced with the same precision as injection molding.
- In comparison to other methods, tooling and product costs are low.
Advantages of Thermoforming
Some of the advantages of employing thermoforming are:
- Low tooling costs owing to the fact that just one-half of a mold is normally required.
- These products have the same quality as injection molded products, but they are faster.
- High speed is ideal for just-in-time manufacturing.
- Larger pieces are easier to produce, allowing for more design flexibility.
- Processes and materials have been optimized to save money.
- Prototype development is available at a low cost and in a short time.
Disadvantages
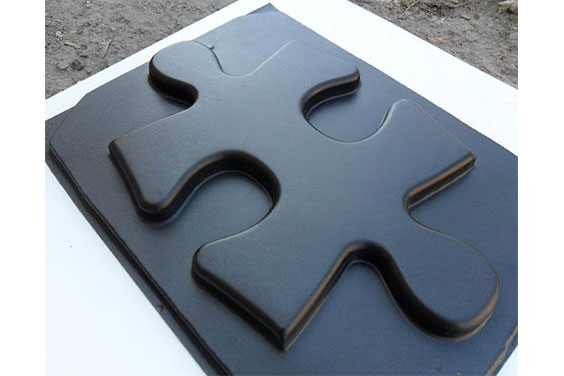
Disadvantages of Vacuum Forming
Some of the disadvantages of using vacuum forming are:
- At any given time, just one part or product can be manufactured.
- Additional expenses or resources may be required to complete parts.
- When vacuuming, thick plastic sheets might warp.
- Because the amount of detail you can achieve with a mold is limited, designs must be simple.
Disadvantages of Pressure Forming
Some of the disadvantages of using pressure forming are:
- The method can only be used on thin-walled designs.
- The product’s thickness may be uneven in some places, resulting in weak parts.
- When compared to other plastic molding technologies such as injection molding, it is a little more expensive.
Disadvantages of Thermoforming
Some of the disadvantages of using thermoforming are:
- In comparison to injection molded parts, the cost of the part is high.
- Due to film stretching, the gauge is not uniform.
- It may necessitate more plastic than conventional plastic molding techniques.
- Geometry restricts the process. Normally, pieces with undercuts aren’t possible.
Cost
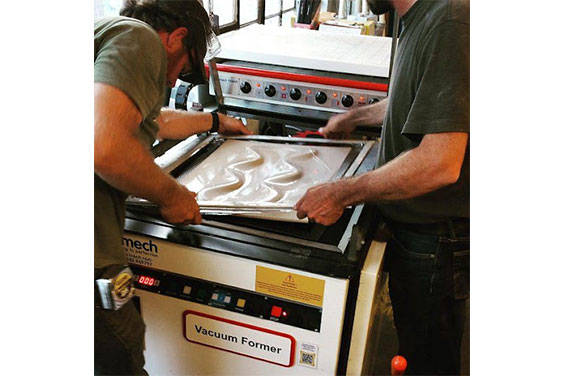
Cost of Vacuum Forming
While the vacuum forming method is a little more complicated, the tooling is less expensive, the manufacturing time is shorter, and the aesthetics are great, summing up the cost to be between $4,000 to $7,000.
Cost of Pressure Forming
With affordable tooling and low production costs, the cost of pressure forming ranges from $2,000 to $5,000, based on the injection molding material selection and other details.
Cost of Thermoforming
The cost of thermoforming is determined by a number of factors, including the product’s design, tools, material, and labor. A single thermoforming mold might cost anything from $2,000 to $10,000.
Prosperity

Prosperity of Vacuum Forming
The possibilities are unlimited when it comes to vacuum thermoforming, and that has to be one of the greatest vacuum forming prosperities. The procedure of heating a thermoplastic sheet and sucking it over a 3D object allows for the creation of innumerable products in a wide range of shapes and sizes.
Prosperity of Pressure Forming
Pressure forming has a benefit over other forms of thermoforming in that it can provide finer edges on forming without weakening the tray. This promotes uniform material distribution and preserves the tray in the appropriate shape, maintaining the level of detail while reproducing the mold design.
Prosperity of Thermoforming
Because the texture is added after the sheet is created, it is far more uniform and accurate than with vacuum forming. These textures can be utilized to conceal scuffing and flaws that may develop in the field, keeping the parts looking new for longer.
Material Used
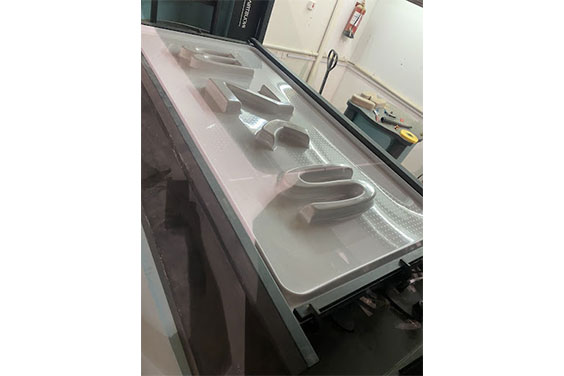
Plastic Used for Vacuum Forming
Thermoplastics, which are plastics that become elastic and pliable at particular temperatures before solidifying when cooled, are commonly used in vacuum forming. High impact polystyrene sheets are common vacuum forming materials. It is extremely flexible and can be molded into nearly any shape.
Another vacuum-forming material is polycarbonate (PC). PC is incredibly resistant to fires, chemicals, and water.
A premium vacuum forming material, acrylonitrile styrene acrylate (ASA) is easy to mold, trim, and manufacture. It has a high level of weather resistance, making it perfect for outdoor use.
Plastic Used for Pressure Forming
The following are some of the most regularly used materials in pressure forming:
- ABS is a high-impact plastic that comes in a range of colors and textures, as well as flame retardant grades.
- PC is a high-temperature and impact-resistant material.
- HDPE is a low-cost material that is impact, chemical, and cold temperature resistant.
Plastic Used for Thermoforming
The following are some of the most commonly used plastics for thermoforming:
- ABS: Has a tough resilience to outdoor elements
- HIPS: The translucent and brittle nature of this plastic makes it excellent for protective packaging.
- HDPE: HDPE is utilized in a wide range of applications, from plastic bags to bottles and even fireworks, because of its outstanding strength-to-density ratio.
- PVC: This rigid plastic has a robust, hard structure, making it the ideal rigid plastic that can tolerate harsh temperatures
Conclusion
Thermoforming and vacuum forming are both incredible methods of manufacturing plastic products and because of their versatility, they can be used in several industries. Look for a medical injection molding company that can help you get the best thermoplastic molds for your application. SeaskyMedical is a company that specializes in the development and manufacture of medical injection molded goods, the quality and durability of medical & surgical disposables and equipment wouldn’t let you down.