The quality of the molded plastic and the efficiency of the production process depending on the injection molding temperature is just right. One can melt plastic if one heats it up high enough. When plastic is heated, it loses its rigidity and softens. Nonetheless, this is dependent upon the plastic variety employed and the plastic melting temperature. When heated, some plastics become pliable, while others melt completely. The melting point is the temperature at which a polymer begins to show evidence of a phase transition from ordered to disordered as a result of heating.
Plastic Material Melt and Mold Temperatures Table
Materials | Melting Point Range (℃) | Mold Temprature Range (℃) | Key Characteristics |
ABS – acrylonitrile-butadiene-styrene | 190-270 | 40-80 | Strong impact resistance, even when at low temperatures. Excellent insulating capabilities. Strong ability to be welded. |
ABS/PC Alloy | 245-265 | 40-80 | ABS, an engineered thermoplastic polymer, is slightly amorphous, has no odour, and is completely safe to use. The relative density of this material is somewhere around 1.2. Features related to mechanics: Superb mechanical qualities, including a high degree of impact resistance |
Acetal | 180-210 | 50-120 | Powerful, resolute, and unyielding. Excellent stability in terms of mechanics. Excellent creep, moisture and fatigue resistance. |
Acrylic | 220-250 | 50-180 | Superior clarity and transparency at the optical level. Extremely resistant to the effects of temperature changes. Impact resistance that is up to 17 times greater than that of standard glass. |
CAB – Cellulose Acetate Butyrate | 170-240 | 40-50 | Functional groups of acetate and butyrate can be found within its structure. It has improved resistance to the effects of the weather. In comparison to cellulose acetate, it has a lower moisture absorption rate. |
HDPE – High-Density Polyethylene | 210-270 | 20-60 | Simple to weld using equipment designed specifically for welding thermoplastics. Low capacity for absorbing moisture. An excellent surface for preparing food. |
LDPE – Low-Density Polyethylene | 180-240 | 20-60 | It is composed of ethylene, making it a homopolymer. The density of a polymer can be altered through the manipulation of its branching structure. The branched chains in LDPE range in length from long to short. |
Nylon 6 or Polyamide | 230-290 | 40-90 | Lustrous and Elastic Oil and a wide variety of substances cannot cause damage to this material. Does not absorb water |
PEEK – Polyether ether ketone | 350-390 | 120-160 | Exceptional resistance to creep (the tendency of a material to permanently deform under the effects of perpetual mechanical stress). PEEK is heat and stress resistant Can be used in applications where it will be exposed to extreme conditions. |
Polycarbonate | 280-320 | 85-120 | As a result of its great strength, polycarbonate is not easily broken or damaged by impacts. PC is a transparent plastic that is nearly as transparent as glass and can transmit over 90% of the light. There is a wide variety of colours and finishes available for polycarbonate sheets, so they can be tailored to any need. |
Polyester PBT | 240-275 | 60-90 | Superior levels of stiffness and tenacity. Very little capacity for the absorption of moisture. Excellent resistance to creeping. |
Polypropylene (Homopolymer) | 200-280 | 30-80 | Semi-rigid and Translucent. Excellent resilience to chemical attacks. Excellent resilience to wear and tear. |
Polystyrene | 170-280 | 30-60 | Due to the presence of large phenyl groups, polystyrene is amorphous and its chains do not pack tightly. Polystyrene is a material that lacks polarity. At 240 degrees Celsius, polystyrene begins to melt. |
The mentioned plastic melting point and plastic melting temperature chart are correct but should be used as a reference. Talking to the raw materials provider or the concerned medical molding company is the best bet for maximizing production output.
Recommended Temperature Ranges for Different Plastic Materials
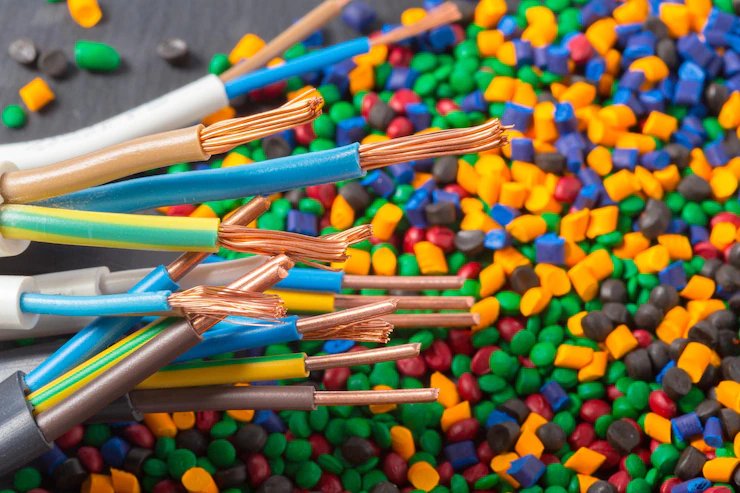
There are different types of plastic material available in the market, however, it is important to have a clear understanding of distinct materials for a better injection molding material selection
Polyethylene or LDPE & HDPE
An individual can get flexible polymer polyethylene (PE) in two major forms, low-density polyethylene (LDPE) and high-density polyethylene (HDPE). This plastic softens and melts at higher temperatures. The melting point of LDPE is 105 degrees Celsius, while that of HDPE is 125 degrees Celsius. Packaging films, bags, and sheets are just some of the many products that benefit from polyethylene’s versatility.
Polypropylene
The melting temperature of polypropylene (PP) is 165 degrees Celsius higher than that of high-density polyethylene (HDPE) plastic (which is 130 degrees Celsius). When exposed to colder temperatures, polypropylene plastic begins to degrade more quickly. Therefore, it is used for things like coffee mugs, plastic tableware, and sturdy home furnishings.
Polystyrene
The well-known polystyrene foam is made from polystyrene (PS), a strong polymer. Since a high melting point is not necessary, this plastic melts at temperatures of about 90 degrees Celsius.
Polyamide
Nylon is a common name for polyamide (PA), which is another name for the material. The melting point of polyamides is around 200 degrees Celsius, which is quite high. The only real drawback of polyamide is that it degrades in the presence of water. The fabric-like qualities of polyamide make it a popular choice for usage in the textile industry, where it is widely employed in the production of apparel.
Polyvinyl chloride (PVC)
PVC is a common plastic that has several uses, including piping, flooring, medical equipment, insulation, and more. PVC’s widespread industrial application necessitates not only that it be exceptionally tough, but that its melting point is similarly high. Therefore, the melting point of PVC is close to 210 degrees Celsius.
The Importance of Plastic Melting Temperature
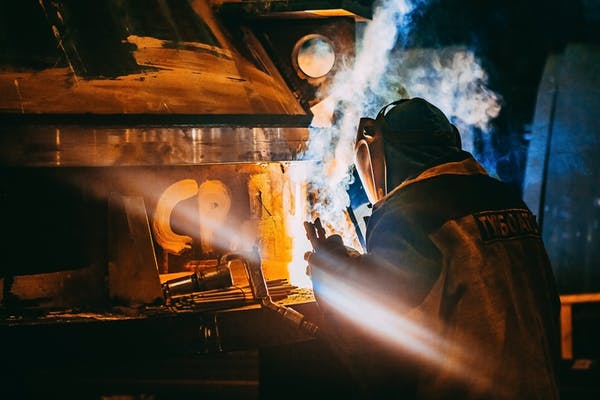
People tend to dismiss information about the boiling point of plastic and mold temperatures as meaningless digits on a screen, yet knowing the proper temperatures is crucial. Injection molding isn’t as simple as it seems because the molding circumstances have a huge impact on the end product’s strength, durability, and visual appeal. Differentiating between process conditions and the setpoints used to exert control over them is essential. The material’s true temperature as it leaves the nozzle and enters the mold is known as its melt temperature.
Melt temperature is not the same as the barrel setpoints, which display the methods employed to achieve it. The actual melting temp of plastic also depends on the mechanical work applied to the material, the residence period, and the condition of the screw and barrel. When discussing mold temperature, most people incorrectly assume that this has no bearing on the quality of the finished product. Although subtle, its impact on the finished product’s qualities is significant.
Higher model temperatures result in lower levels of molded in-stress and higher impact strength, fatigue performance, and stress-crack resistance in amorphous materials like polycarbonate and ABS.
Mold temperature becomes critical in determining the degree of crystallinity in a polymer when working with semi-crystalline materials. As a result, this has implications for a wide range of performance characteristics, including fatigue resistance, wear resistance, creep resistance, and dimensional stability at elevated temperatures.
Further Considerations for Plastic Melting & mold Temperatures
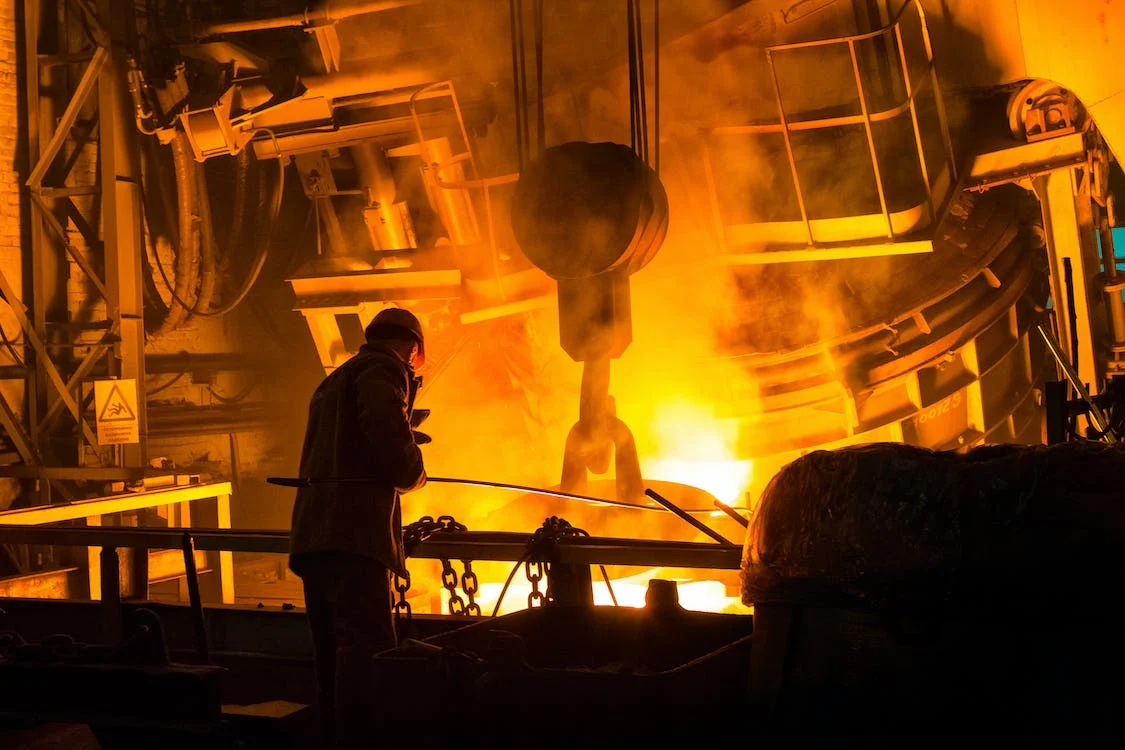
It is crucial to have a solid understanding of how the temperature of the mold and the temperature of the melting work together to produce the final part qualities. In the majority of situations, the most optimal performance can be achieved by combining a lower melt temperature with a higher mold temperature.
However, the majority of plastic injection molders are just people who push buttons, and they lack the technical skills necessary to execute and manage these two essential components of plastic molding. They believe that increasing the temperature of the melt is the only way to successfully lower the resin’s viscosity.
Inadvertently, greater melting temperatures can lead to the following:
- The Breakdown of Resin
- Extended periods of cooling
- Consumption of additional amounts of energy
Now, these plastic molders are compelled to lower the temperature of the mold in order to recoup the productivity that was lost as a result of lengthier cooling cycles necessary by higher melt temperatures. This is done in order to regain the productivity that was lost. Due to the high melt temperature compared to the low mold temperature, the characteristics of the component are frequently impaired, leading to an unstable part.
Instead, they should combine a lower melt temperature with a higher mold temperature. This will likely result in the creation of a component that has superior final qualities and a shorter cycle time, which will ultimately enhance part quality and decrease costs.
Conclusion
Temperature is a naturally very important factor in the process of plastic injection molding, and two specific temperature types hold an especially vital role. These temperature types are the melt temperature and the mold temperature. These are two distinct metrics that are connected in some way, and both of them speak volumes about how the finished injection-molded products will look, feel, and hold up over time. When it comes to the manufacturing of plastic parts using plastic molding, medical plastics manufacturer ensures that there is a correct melt temperature and mold temperature in order to guarantee that the final properties of the part will satisfy its performance requirements. Contact Seasky Medical for more information on the subject.