Plastic products have unique qualities that make them indispensable in modern life. They are the product of a careful balance between chemical composition, molecular mass, and polymerization processes, allowing them to provide a one-of-a-kind mix of mechanical, thermal, and physical qualities. This is a vital part for plastic part manufacturers. It allows plastic items to be molded into a wide range of shapes, colors, and textures that are easily sterilizable.
The advent of improved polymer processing techniques such as extrusion, injection molding, and blow molding has increased the adaptability of synthetic polymers in injection molding uses. These techniques enable exact control of final product qualities, such as suppleness, transparencies, and specific stiffness, which are crucial for maintaining optimal functionality for the manufacturing of plastic products.
Medical injection molding companies specialize in producing medical devices parts through the injection molding process. They not only specialize in medical molding but also in other manufacturing industries. Plastic materials can be developed to suit particular biological needs, such as biomedical applications, which refer to a material’s capacity to interact with live tissue without causing injury. One can Transform their plastic parts production with Sea Sky’s expert plastic parts molding services. Contact here to streamline your supply chain and provide high-quality, reliable plastic components.
Finally, because of their low manufacturing cost and versatility, plastic items are accessible to a broad spectrum of people, specifically in resource-limited contexts. This is especially relevant in developing nations.
Plastic Manufacturing Industry
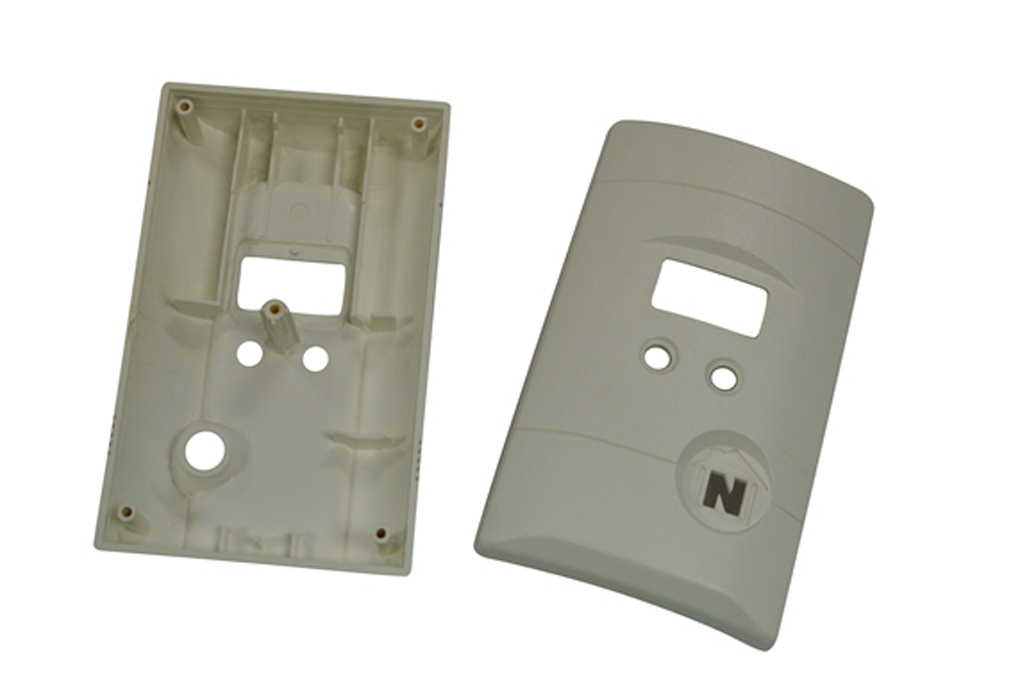
The plastic manufacturing industry is a dynamic and rapidly growing sector that has significantly impacted the global economy. A medical device component manufacturer produces various components for use in medical devices through injection molding or other manufacturing processes. Plastic products are used in various applications, from electronics housing and plastic chairs to construction and medical supplies. To know how to manufacture plastic products, read on.
Plastic products manufacturing begins with the selection of raw materials, typically petroleum-based feedstocks, which are then processed through a series of chemical reactions to produce polymer resins. These resins are then transformed into final products through various manufacturing processes, such as extrusion, injection molding, and blow molding.
- Injection Molding: A process where melted plastic is injected into a mold to produce a wide range of products, including household items, automotive parts, and toys.
- Blow Molding: A process where melted plastic is inflated like a balloon to form a hollow product, such as a bottle or container.
- Extrusion: A process where melted plastic is pushed through a die to create products with a continuous, uniform shape, such as pipes, sheets, and films.
- Rotational Molding: A process where a mold is rotated and heated to produce a hollow, seamless product, such as large tanks and playground equipment.
- Thermoforming: A process where a plastic sheet is heated and formed into a desired shape using a mold. It is commonly used to produce packaging and trays.
- Compression Molding: A process where a mold is filled with a pre-formed plastic material and subjected to high pressure to produce a final product.
- Vacuum Forming: A process where a plastic sheet is heated and formed into a mold using vacuum suction. It is commonly used to produce plastic packaging and trays.
These are the main types of plastic manufacturing processes used in the industry. Each process has its own advantages and limitations and is suited for specific products and applications for example: Like a medical plastic injection molding producer specializes in producing medical devices through the plastic injection molding process.
One of the key drivers of the plastic manufacturing industry is the low cost of production and versatility of plastic products. Plastic materials can be molded into a wide range of shapes, colors, and textures, making them ideal for various applications. Additionally, plastic products are lightweight, durable, and easy to transport, which has helped to drive their widespread adoption across the globe.
However, the plastic manufacturing industry has challenges. As a plastic molding company specializes in producing plastic products through various molding processes, including injection molding. Manufacturing process of plastic is widely recognized as a significant contributor to environmental pollution, particularly plastic waste in oceans and other waterways. This has led to increased regulatory pressure, particularly in Europe and North America, to reduce plastic waste and promote sustainable alternatives.
The Primary Manufacturing Process For Plastic Products
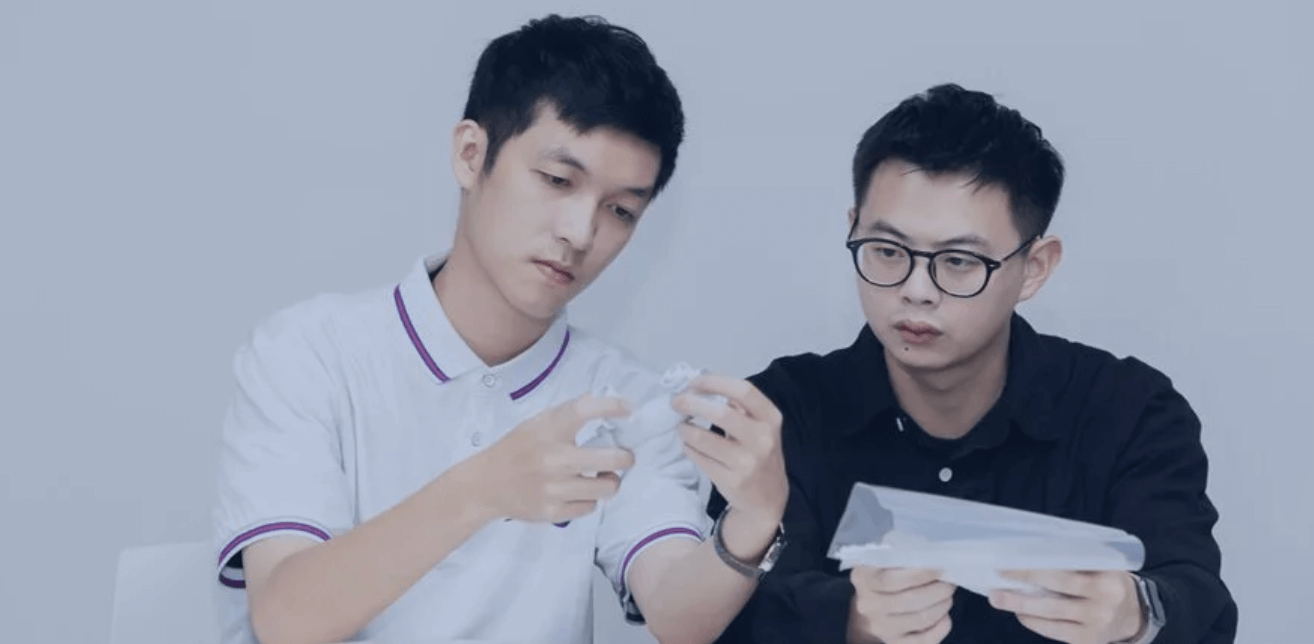
Plastic products have become integral to our daily lives due to their versatility, affordability, and durability and take in consideration injection molding medical devices which involve producing medical devices through the injection molding process. From packaging materials to home appliances, automobiles, and consumer goods, types of plastic manufacturing in various shapes and sizes are used in various applications.
The manufacturing of plastic products is a complex process that involves several stages, including the selection of raw materials, the design and creation of molds, the shaping of the plastic into its final form, and the finishing and assembly of the product. Several methods are used to manufacture plastic products, each with its advantages and limitations. Some of the most common methods include:
- Selection of raw materials: Raw materials for plastic production, such as resins, additives, and fillers, are chosen based on the desired properties of the final product. Acquiring high-quality raw materials from a reputable market is important to ensure the product meets quality standards.
- Mold design and creation: Molds are created for the shaping process and are designed based on the desired product shape and size. The mold design directly impacts the quality of the final product, so it is important to ensure that the mold is designed with precision.
- Shaping: The plastic is melted and molded into its final form using heat and pressure in the mold. The shaping process is crucial as it affects the final product’s quality and accuracy.
- Finishing: This stage includes adding necessary details, such as painting, printing or cutting, to complete the product. The finishing process significantly impacts the overall look and feel of the product.
- Assembly: The final step in the manufacturing process, involves putting together various components to create the final product. Proper assembly is essential for the product to function correctly and meet quality standards.
- Quality control: Quality control measures are implemented throughout the manufacturing process to ensure that the final product meets quality standards and customer requirements. Regular checks are conducted at each stage to identify and rectify any issues, leading to the production of high-quality plastic products.
Every plastic manufacturing company for injections should practice the clean room injection molding process which is – A clean room injection molding is a process where injection molding is performed in a clean and controlled environment. This method is ethically right and is suggested by the laws.
Introduction To The Main Manufacturing Processes For Plastic Products
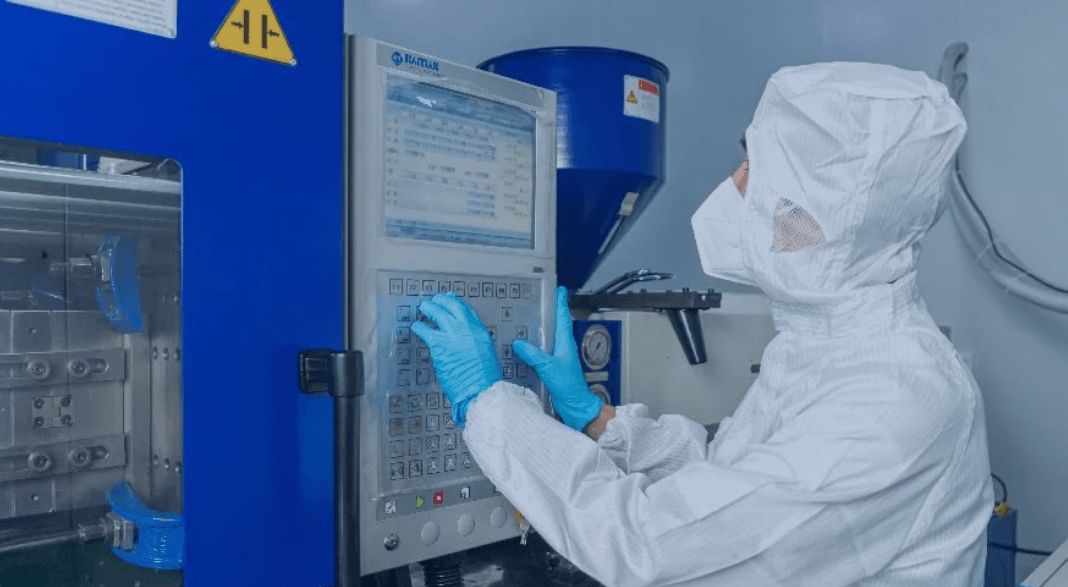
Plastic products have become essential to our daily lives due to their versatility, affordability, durability and injection molding in a clean room. From packaging materials to medical equipment part, automobiles, and consumer goods, plastic products are manufactured in various shapes and sizes and are used in various applications.
The manufacturing of plastic products is a complex process that involves several stages, including the selection of raw materials, the design and creation of molds, the shaping of the plastic into its final form, and the finishing and assembly of the product. Several manufacturing methods of plastic are used to produce plastic products, each with its advantages and limitations. Some of the most common methods include:
- Manufacture Plastic Products With Plastic Injection Molding:
This method produces high-volume, complex-shaped plastic products. It involves melting the plastic resin and injecting it into a mold, which is then cooled, and the finished product is removed to manufacture the plastic parts intricately.
- Manufacture Plastic Products With Extrusion Molding:
This process involves heating the plastic resin and forcing it through a die, where it takes on its final shape. Extrusion molding produces long, continuous products such as pipes and profiles.
- Manufacturing Plastics With Blow Molding:
This method produces hollow plastic products, such as bottles, containers, and automobile parts. It involves blowing air into a tube of melted plastic, which is then cooled, and the finished product is removed.
- Manufacturing Plastic With Rotational Molding:
This process produces large, hollow plastic products, such as tanks, playground equipment, and kayaks. The plastic is melted and rotated in a mold, where it takes on its final shape.
- Manufacturing Plastic Parts With Vacuum Forming:
This process of plastic manufacturing involves heating a plastic sheet and applying vacuum pressure to form it into a mold. It produces various products, from packaging materials to automotive parts.
- Manufacturing Plastic Parts With 3D Printing:
This method uses a computer-controlled process to build plastic products layer by layer. It is ideal for producing prototypes and low-volume, complex-shaped parts.
- Manufacturing of Plastic With CNC Machining:
This process uses computer-controlled cutting tools to remove material from a solid block of plastic and shape it into its final form. It is used to produce precise and intricate parts with tight tolerances.
- Manufacturing of Plastic With Thermoforming:
This process involves heating a sheet of plastic and forming it over a mold, where it takes on its final form. It produces various products, from packaging materials to automotive parts.
Each process of manufacturing plastic has its unique advantages and limitations. The selection of the process depends on several factors, including the production volume, the final product’s complexity, and the properties required for the finished product.
What Materials Are Used In Plastic Manufacturing?
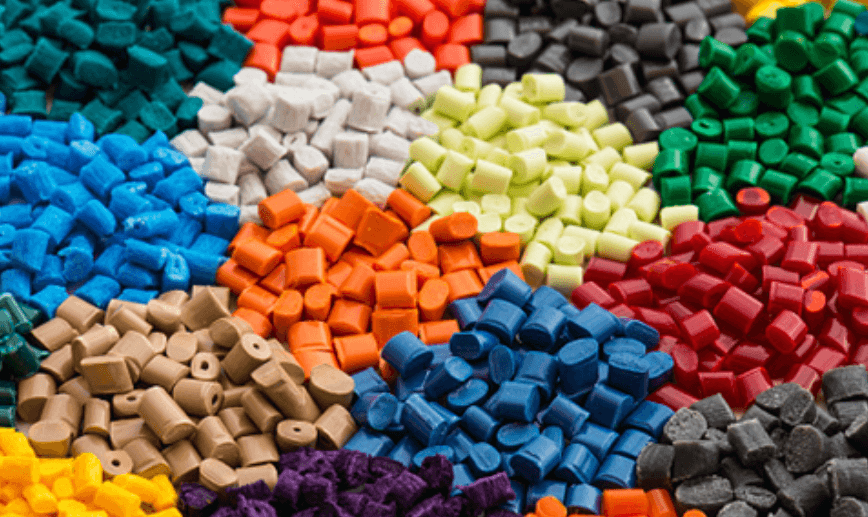
Plastic manufacturing relies on various raw materials to produce strong, durable, and versatile products. How to manufacture plastic can be made from common materials, including PVC, PET, bioplastics, and engineering plastics, each with its unique properties and applications. These materials can also be used for custom plastic molding which involves producing custom plastic products to meet specific customer requirements and specifications through various molding processes, including injection molding.
- Polyethene (PE):
A versatile, lightweight, and durable plastic commonly used in home appliance, consumer goods, and medical devices. It is widely used due to its low cost and ability to be produced in a variety of forms, including low-density polyethene (LDPE), high-density polyethene (HDPE), and linear low-density polyethene (LLDPE).
- Polypropylene (PP):
A robust and heat-resistant plastic commonly used in packaging, consumer goods, and automotive parts. PP is known for its ability to maintain its shape and stability under high temperatures, making it ideal for applications in the automotive and electronics industries.
- Polyvinyl Chloride (PVC):
A rugged and versatile plastic commonly used in piping, flooring, and electrical applications. PVC is known for its resistance to chemical corrosion and low cost, making it a popular choice for construction applications.
- Polyethylene Terephthalate (PET):
A lightweight and shatter-resistant plastic commonly used in beverage containers, food packaging, and textiles. The high level of transparency, low gas permeability, and lightweight make PET an ideal choice for food and beverage packaging.
- Acrylonitrile Butadiene Styrene (ABS):
A challenging and impact-resistant plastic commonly used in automotive parts, toys, and consumer goods. ABS is known for its high impact resistance, making it ideal for use in products that may experience frequent impact or rough handling.
- Polystyrene (PS):
A lightweight and low-cost plastic commonly used in packaging materials, consumer goods, and insulation materials. Its low cost, ease of processing, and insulation properties make it a popular choice in various industries.
How to Choose The Right Plastic Manufacturing Process
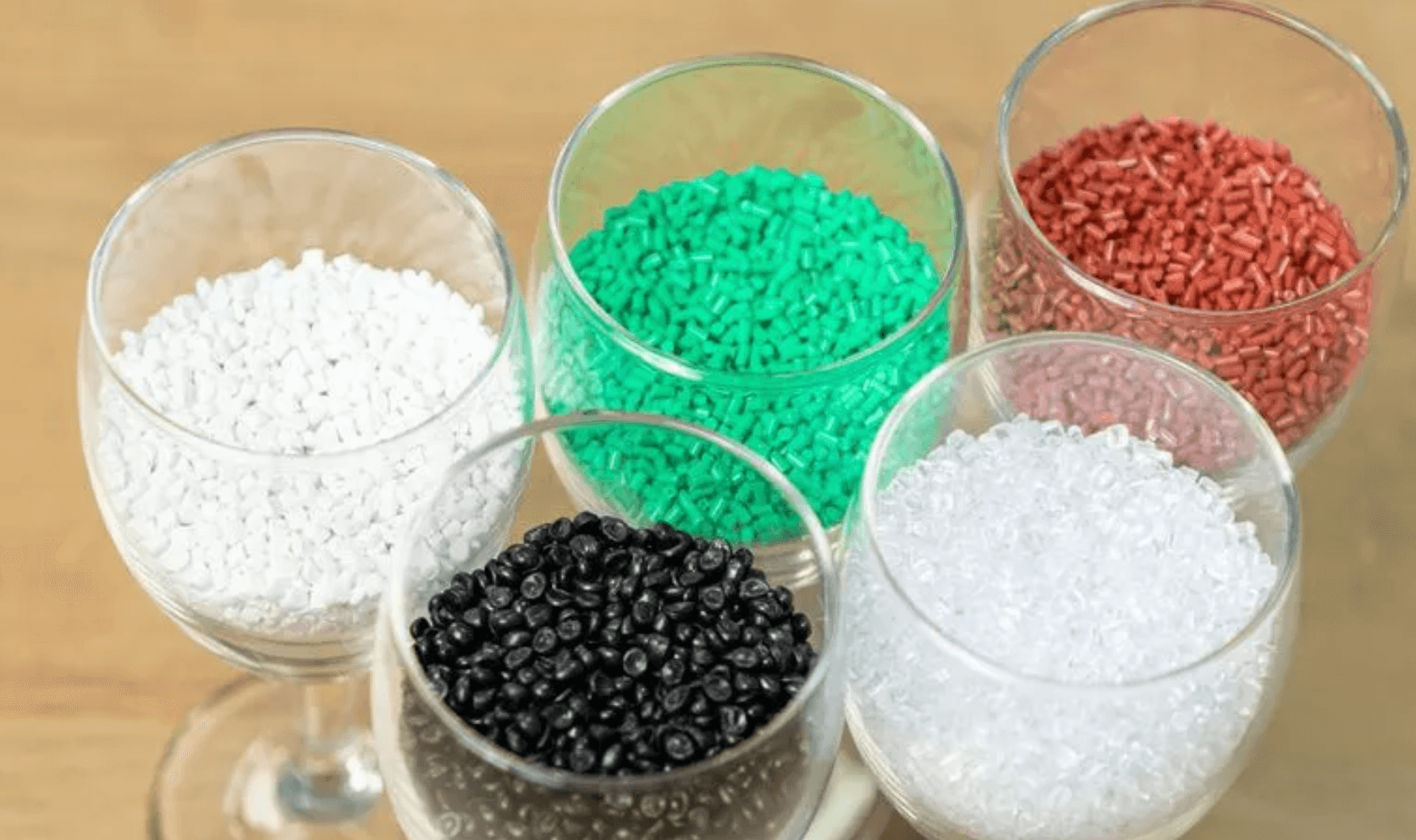
Choosing the proper manufacturing methods of plastic can significantly impact the final product quality, cost, lead time and molding of the product. Here are some factors to consider when choosing the proper process:
- Part Design: The design of the part will affect the choice of process. For example, injection molding is best suited for parts with complex shapes, while blow molding is best suited for large, hollow parts.
- Volume Requirements: The volume of parts required will impact the choice of process. High-volume production runs are best suited for processes such as injection molding or blow molding. In contrast, low volume production runs are best suited for processes such as vacuum forming or 3D printing.
- Material Requirements: The material used will impact the choice of process. Some materials are better suited to specific processes, such as PVC for extrusion molding or PET for blow molding.
- Lead Time: The lead time required for production will impact the choice of process. Faster production lead times are possible with processes such as injection molding or CNC machining, while slower lead times are more typical with processes such as rotational molding or thermoforming.
- Cost: The cost of production will impact the choice of process. Processes such as injection molding and blow molding typically have higher upfront tooling costs, but lower per-unit costs for high-volume production runs. Processes such as vacuum forming and 3D printing typically have lower upfront costs but higher per-unit costs for low volume production runs.
Ultimately, the choice of the process of plastic manufacturing will depend on the specific requirements of the part, and careful consideration of the factors listed above can help to ensure that the correct process is selected for each specific project for injection molding.
Conclusion
The plastic manufacturing industry offers a range of processes for producing plastic parts, each with its strengths and limitations. The proper process will depend on various factors, including part design, volume requirements, material requirements, lead time, and cost.
It is essential to carefully consider all of these factors when selecting a manufacturing process to ensure that the final product meets the required specifications and is produced cost-effectively and timely. Maximize the quality and efficiency of plastic products production with Sea Sky’s customized plastic molding solutions. Contact us here to schedule a consultation and see the results for yourself.