If a product doesn’t look and feel polished, no level of creative work will assist it. Because of this, a product’s plastic finish can determine its success or failure. An important component of the creative process is the plastic surface finish. A product can go from simple and average to spectacular and outstanding with the proper surface finish injection molding.
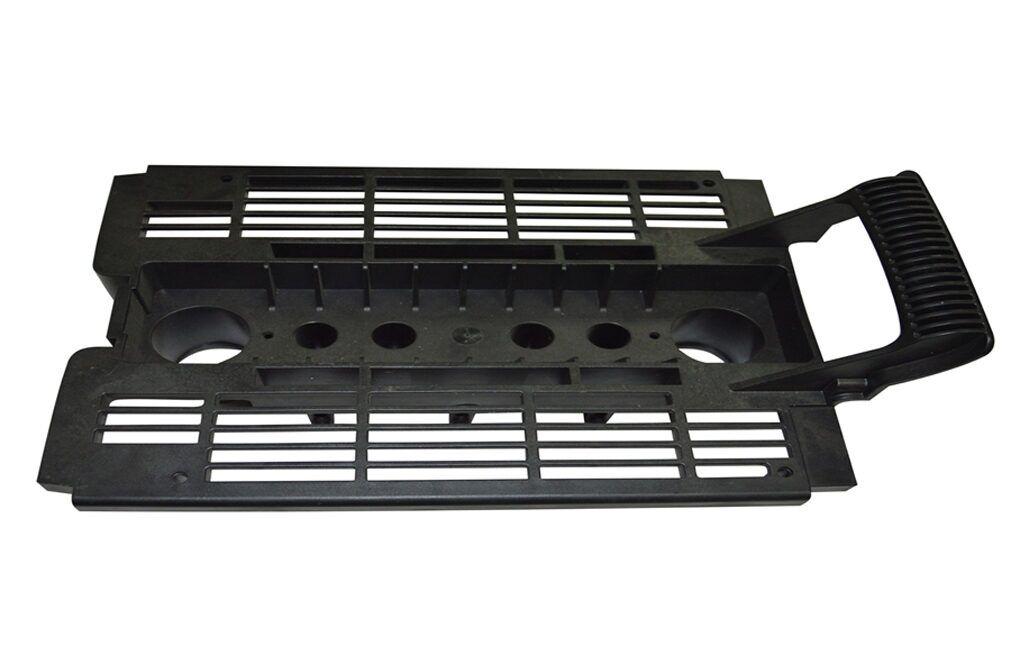
Since surface finishes are so important, this article discusses everything there is to know about injection molding surface finish types and how to pick the right one.
What is Injection Molding Surface Finishes?
Most plastic parts need additional processing after being molded to be finished. Several plastic finishing procedures, like surface finishing, are carried out for aesthetics or purposes of appearance. An injected molded object can have a certain appearance, feel, or texture by using injection mold texturing. Because it serves both an aesthetic and a functional purpose, the surface finish can play a significant role in how the product looks or performs.
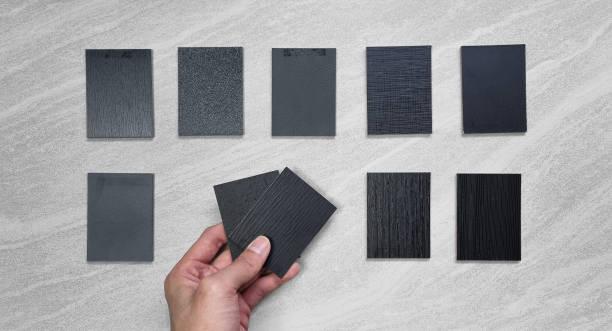
The plastic surface polish by a reputable plastic injection molding company will improve the part’s performance. For example, plastic with a textured finish will assist the consumer in getting a better grip and the right sensation when holding the product in their hands. An essential component of completing a product is choosing the right surface finish injection molding.
Importance of Surface Finishes in Injection Molding
The way a product is finished on the outside is just as crucial to its design as any other element. It can affect usefulness and performance in addition to raising the product’s perceived worth in the eyes of the consumer. Here is why injection molding surface finish is important:
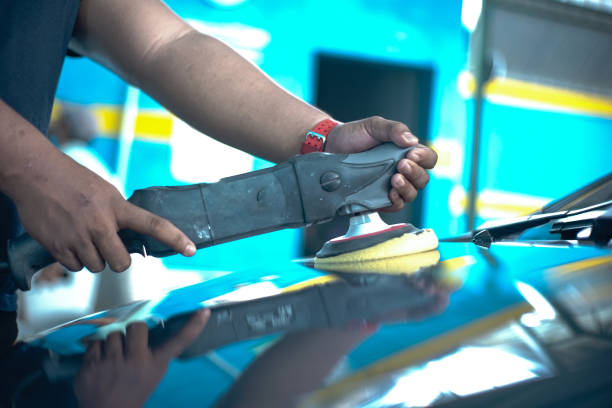
- Aesthetics
Texturing is a design choice that can be made for various aesthetic motives. In addition to enhancing aesthetics and giving a finished aspect, a glossy or matte injection mold texturing on a part’s surface generally helps to conceal injection molding-related flaws such as flow lines, stitch lines, sink marks, and shade marks. From a business standpoint, customers like parts with nice surface quality. For example, injection molding medical devicesare made with proper finishes to provide functional as well as aesthetic value.
In keeping with the aesthetics concept, concealing any wear and tear that might result from product transportation or other supply chain procedures is another justification for employing surface coatings.
- Functionality
The product’s functionality influences the final injection mold texturing decision during medical plastics manufacturing. The functioning of the created product is improved by surface polish. For instance, a product’s grip is enhanced with a textured coating. Also, the same finish performs admirably when there is a need of hold support. A textured finish increases the part’s strength and safety standards.
Plastic flow creases can frequently impair the quality of the manufactured component while molding plastic parts in an injection molding machine. Nevertheless, a textured surface can combat these plastic flow wrinkles. A textured coating can increase safety standards and provide beneficial strength.
- Durability
The quality of a surface’s finish can have a significant impact on a part’s functionality and longevity in a variety of applications. The product frequently becomes damaged over time from continuous use. This is frequently brought on by the high friction that develops between the product’s surface and the surface it is applied against. Surfaces with surface finishing are more resilient for usage with minimal to no friction.
The surface finish can impact many properties of the product part’s ability to resist wear and tear. Companies can either help or damage lubrication, change friction with contacting parts and resist corrosion, among other things, with the help of correct surface finish. Through decreased friction, the product’s durability is improved. For resistance to corrosion and chemicals, it is crucial. Coatings and paints adhere better because of it.
- Cost Savings
A product’s design has a key role in cost-cutting. When a surface finish is simple to recreate, it may be produced again in large quantities using the same mold, which is a productive way to produce goods cheaply. Instead of creating and installing numerous alternatives, the same mold can be used for the procedure, which results in lower costs and faster production times.
Common Injection Molding Surface Finishes
Plastic part production benefits greatly from the use of custom plastic injection mold. This method can produce large numbers of similar things quickly and inexpensively. The natural surface smoothness of molded objects is one of the essential benefits of injection molding.
For aesthetic reasons, certain businesses will demand particularly smooth plastic surface finishes. Others can choose a glossy plastic texture or a rough surface to increase a part’s lifespan. Injection molded items’ SPI surface treatment possibilities are discussed in this section.
- Glossy Injection Molding Surface Finishes

Plastic surface finish chart for glossy injection molding surface finishes:
Grade | Finish | Suitable Materials |
A-1 | Maximum gloss finish | Acrylic, PC, ABS, HDPE, Nylon, PP, Polystyrene |
A-2 | Standard gloss-finish | |
A-3 | Low gloss-finish | |
B-1 | Semi-gloss | |
B-2 | Medium-gloss | |
B-3 | Low medium-gloss |
- Definition
The glossy and semi-glossy finish is produced by diamond or sandpaper buffing. When combined with glass and plastic like acrylic, such treatments produce outstanding results. It works well in products like mirrors, clear casings, and injection-molded lenses. Without revealing a distinct texture, this tends to scatter or reflect light. The waviness of the surface has no orientation; therefore, it appears the same from any angle of light or sight.
Grade A and B are the two grades of gloss and semi-gloss finishes. The highest quality injection mold texturing is grade A. Very tiny grains make up diamond buffing paste. The outcomes are frequently glossy, and the product surfaces remain flat. Semi-gloss finish also referred to as grade B finish. It is used with sanding grit and works well to hide evident CNC machine molding markings. The grit number of the sandpaper regulates the surface finish.
This method allows plastics like acrylic and PC to achieve an extremely smooth finish. For a substance like TPU, however, it is practically difficult to achieve such a finish. This is due to the strong abrasion resistance of such plastic materials, making them resistant to polishing.
- Applications
Such finishes can produce a superb aesthetic appearance while being excellent at hiding machining, molding, and tooling marks. It is, therefore, excellent for many consumer goods. It also works well in products like mirrors, clear casings, and injection-molded lenses.
- Pros
- Reduces friction, abrasion, and fluid flow resistance to enhance a product’s performance.
- Increases a product’s aesthetic appeal and increases its marketability.
- Light is reflected from its surface in a significant proportion.
- Has better resistance against scratches.
- Cons
- Usually very pricey.
- Matte Injection Molding Surface Finishes
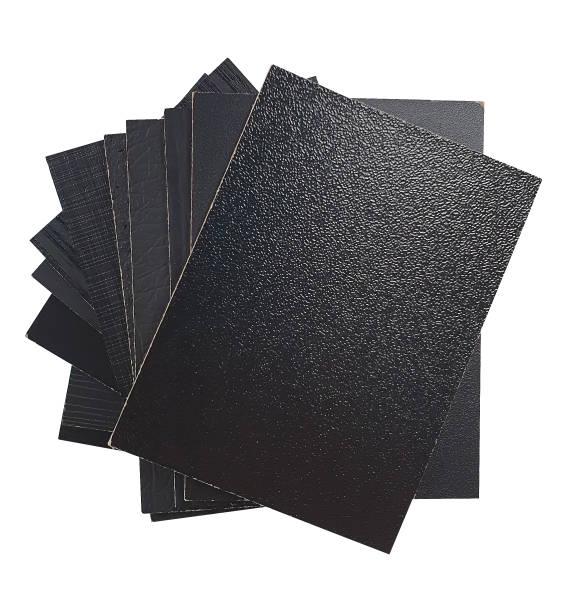
Plastic surface finish chart for matte injection molding surface finishes:
Grade | Finish | Suitable Materials |
C-1 | Matte finish | ABS, HDPE, Nylon, PP, Polystyrene |
C-2 | Matte finish | |
C-3 | Matte finish |
- Definition
Sanding stones with grit create matte finishes. By using this method, machining marks can be eliminated without producing a shiny appearance. It can assist designs for products that demand a more toned or understated appearance.
The stones’ grits, which vary from 600 to 320, are the same as those used for B-grade finishes, but because they cut more aggressively, they leave behind a coarser and less flat finish. This method leaves plastic items with a matte surface finish and is used to swiftly remove tooling and mold marks.
Grit sanding stones, also known as grade C, have a final injection mold texturing and grit number that are comparable to sandpaper. Contrarily, grit stones cut more forcefully than B grades, producing a coarser texture. Moreover, Grade C has three levels that, when combined, produce a matte-finished surface.
- Applications
Several industries, including the automotive, electrical, and consumer products sectors, use matte injection molding surface treatments. These coatings offer a non-glossy, textured surface that improves grip, lowers glare, and increases scratch resistance. They are perfect for goods that need a smooth surface or a subdued appearance. Matte coatings can also be utilized to enhance the aesthetic appeal of objects and generate visual contrast. Dashboard parts, electrical device casings, and beauty products packaging are a few typical applications.
- Pros
- Scratches are less prominent and noticeable to the human eye.
- Greater consistency of color.
- Makes a product more grippy.
- A reasonably priced surface finish.
- Easy to maintain.
- Cons
- Less aesthetic value.
- Printing on matte surfaces may make items more prone to twisting and wrinkling.
- Textured Injection Molding Surface Finishes
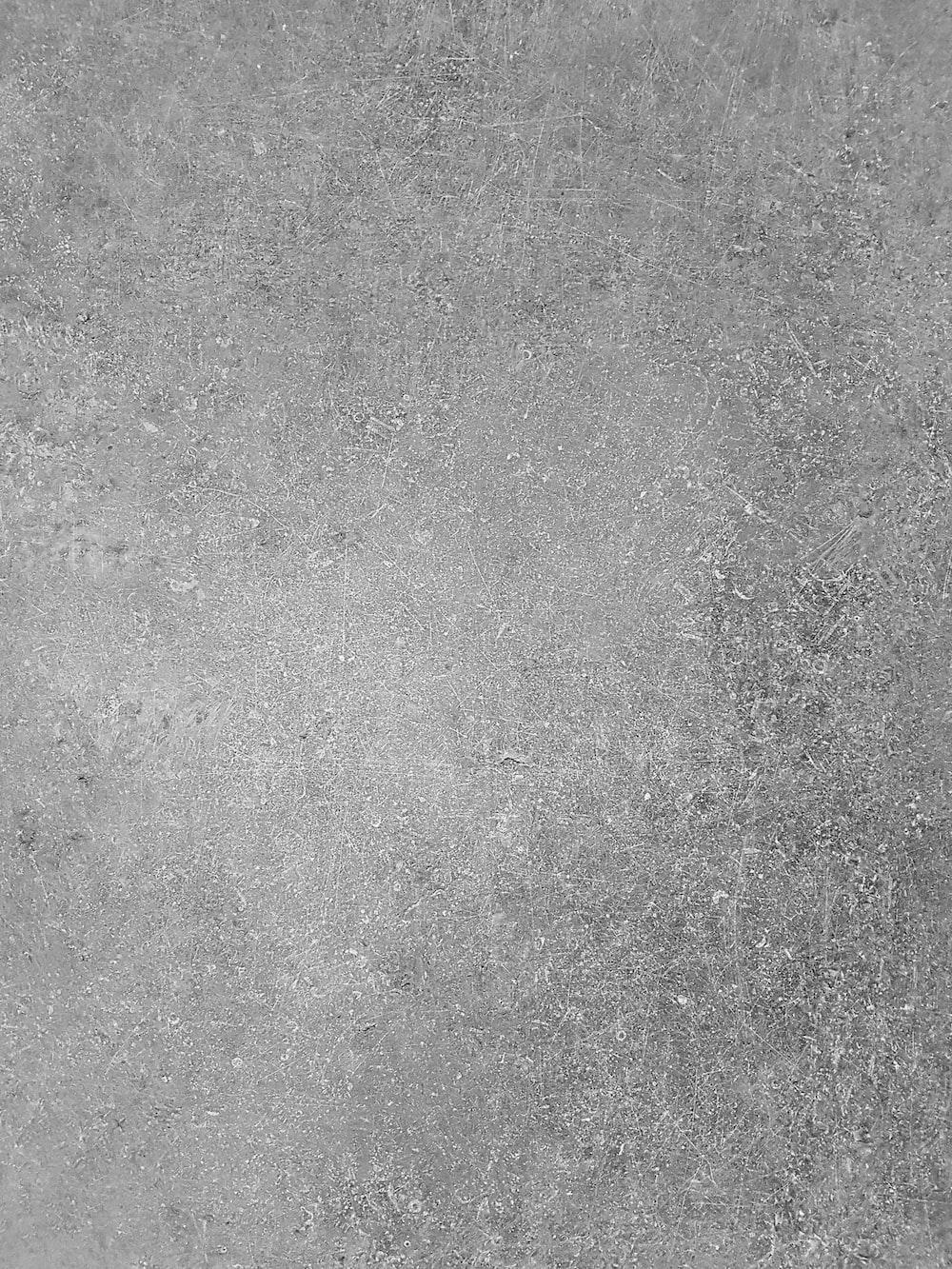
Plastic surface finish chart for textured injection molding surface finishes:
Grade | Finish | Suitable Materials |
D-1 | Satin | ABS, HDPE, Nylon, PP, Polystyrene, TPU |
D-2 | Dull | |
D-3 | Rough |
- Definition
Pressure blasting is used to create textured finishes, although this method may leave the surface looking flat, lifeless, and harsher. Such coatings can promote paint or label adhesion and help the end user grip the object more securely.
Sand or glass beads are used in abrasive blasting to provide rougher surfaces. They fall under SPI class D. The spraying process is random; thus, the finished surface is consistent yet non-directional. This category is utilized to give plastic objects a flat or dull surface.
Blasting is the process of applying high pressure while violently projecting an abrasive substance against a surface. A pressurized fluid, vapor streams, compressed air, centrifugal wheels, or pressurized fluid under pressure are used to propel the blasting material against the surface. The technique shapes a surface, roughens smooth surfaces, smoothens rough surfaces, and removes impurities from surfaces.
- Applications
Several industries, including the automobile, aerospace, and consumer goods, use textured injection molding surface treatments. They provide things a distinctive appearance and feel, enhance grip and wear resistance, and can be utilized to add visual flair. Consumer electronics, external automotive components, and textured instrument panels are some examples.
- Pros
- Enhances the look of the product.
- Conceals burn marks, flow lines, sinks, and other flaws.
- Increases the product’s strength.
- Makes the part easier to hold.
- Resists potential fingerprint smudges.
- Increases the application’s usability and security.
- Offers a superior surface for label attachment.
- Cons
- Might reduce fatigue resistance.
Three Injection Mold Surface Finish Standards
The standards related are the first item to take into account when choosing the surface finishes for plastic products. The market-available plastic items’ cosmetic quality is assessed using these standards.
- SPI Finish Standards
An independent us trade group formerly known as SPI is also called the Plastics Industry Association (pia). The entire industry accepts their specification for the surface finish of injection molding tools. Injection molders and product designers can define the surface quality of molded plastic items using SPI criteria. They gauge the common surface finishes that can be put on mold-making tools and the parts produced by such machines.
SPI rules specify twelve injection mold surface finish standards. Each of these standards is identified by an alphanumeric code that starts with the letter A, B, C, Or D and finishes with the digits 1, 2, 3, or 4. Between letters and numbers, there can be a dash.
There are four different SPI injection molding surface finish standards grades: glossy (A), semi-glossy (B), matte (C), and textured (D). Each of these four classes has three SPI categories, and every one of the twelve SPI categories has a unique set of characteristics.
- VDI Surface Finish Standards
The Verein Deutscher Ingenieure (VDI), the Society of German Engineers, established the mold texture standard known as VDI 3400 surface finish (often referred to as VDI surface finish). The VDI 3400 surface finish is mainly handled by Electrical Discharge Machining (EDM) while mold machining. Moreover, the conventional texturing technique could be used (like in SPI).
Even though the organization of German engineers established the standards, tool producers from North America, Europe, and Asia frequently employ them. Surface roughness is the foundation for VDI injection molding surface finish standards.
- RMS Surface Finish Standards
Since imperfections on the surface can create rust or fracture formation, surface roughness is a great indicator of how a product will perform. Rough surfaces have higher contact resistance and wear more quickly than smooth ones. In some circumstances, roughness is necessary to promote the adhesion of decorative finish coatings like electroplating, powder coating, or spraying.
Root Mean Square Roughness is referred to as RMS. Compared to the other mold texturing standards, it can be more accurate if used properly. It employs additional math and surface points, and one may use it to calculate the surface’s level of roughness. The average curve is discovered by RMS using a sine wave, and the average divergence from the mean line can be seen.
Considerations for Selecting the Right Surface Finish
The choice of surface finish must be made early in the product design process since the surface controls the choice of materials and the draft angle, which affects the manufacturing cost. There are some of main variables to consider.
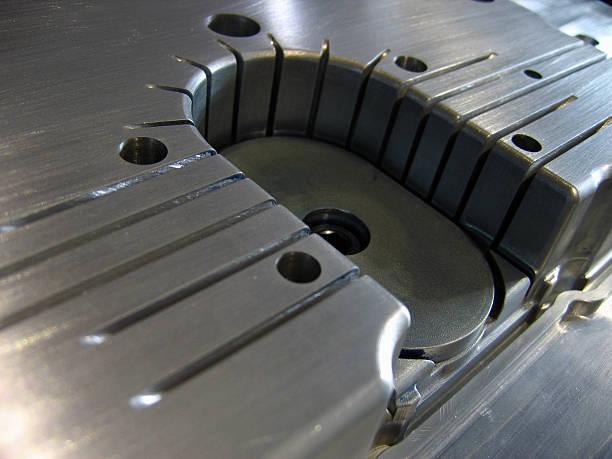
- Material Type
For injection molding, there are many different material choices. For example, some plastics are more suited to smooth finishes, others can be more easily textured by being roughened up.
In addition, some material additions, including fillers and colors, may have an impact on the way a molded object is finished on the outside. When thinking about incorporating additive compounds into the part material, a solid understanding of the material is necessary.
A qualified plastic injection mold-making company has access to a wealth of scientific information about materials science, material behavior, and processing parameters to make an accurate surface finish process option based on a set of criteria.
- Part Design
The design of the part of the product is also important when selecting a plastic injection molding surface finish. When choosing the right surface finish, elements including part shape, functionality, and appearance may all be important considerations.
A part with complex details, for instance, could need a smoother finish to preserve those details, whereas a bigger, flatter part might thrive from a textured finish to hide surface flaws. Also, the desired look of the part may impact the choice of surface finish; depending on the design’s aesthetic aspirations, glossy or matte surfaces may be appropriate.
- Manufacturing Requirements
When deciding on a surface finish, consider the stages of the manufacturing process and determine which injection molding surface finish can handle the intricacy of the manufacturing process.
The patterns on the steel material have an impact on a product’s surface finish. A surface’s flaws, such as sink marks, might be concealed by a coarser surface pattern. Moreover, a molded part’s surface finish may have an impact on the draft that is necessary; if the draft is improperly constructed, the surface finish may be damaged during the expulsion process.
- Function and Appearance
The choice of injection molding surface finish can be influenced by the product’s appearance and functioning. It may be necessary to have a particular texture or surface finish depending on how well a product performs, such as in terms of grip or wear resistance. Also, the desired product appearance might be quite important. Depending on the design’s aesthetic objectives, glossy or matte finishes may be appropriate. The ultimate product’s performance and aesthetic characteristics must be achieved by carefully choosing the surface finish.
Seaskymedical: Experienced One-Stop Injection Molding Supplier
For the most affordable pricing, Seaskymedical provides first-rate plastic injection molding services. We offer customized injection molding services thanks to their extensive supply of materials, knowledge, and experience. We ensure the parts receive the best mold surface finishes thanks to their thorough understanding of the various injection molding surface treatment possibilities.
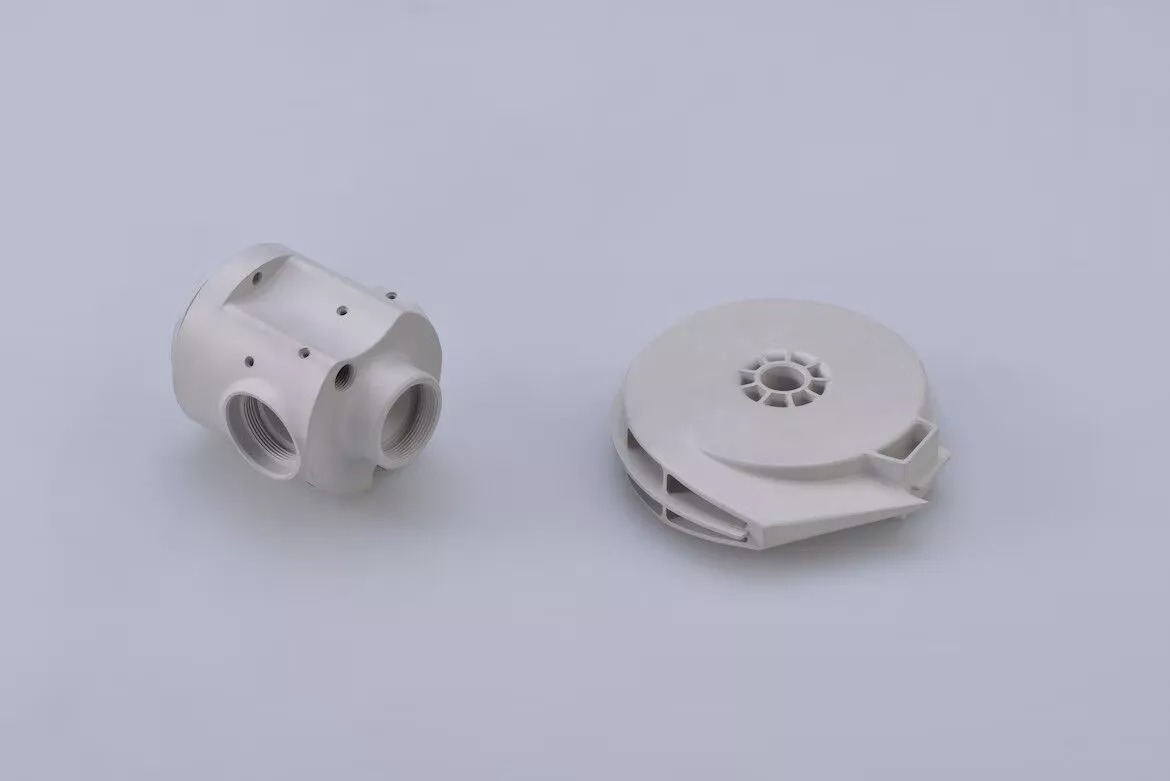
China-based Seaskymedical enjoys high levels of demand throughout the world. Seaskymedical ranks among the best injection molding firms that offer excellent injection mold surface finish standards thanks to its decades of injection molding experience, competent personnel, sizable workshop area, and cutting-edge injection molding machines.
We guarantee that all molding solutions exceed worldwide safety and industry standards by conducting the manufacture, assembly, and packing of goods in an iso 8 cleanroom utilizing dependable, cutting-edge machinery.
Conclusion
Selecting the proper surface finish for an injection-molded plastic product has a number of advantages. The reason is that a surface finish will affect how tools are made, what materials to utilize, and other choices. In addition, the injection molding surface finish raises the product’s aesthetic value. By avoiding scuffs and scratches, also increases product durability. An optimal surface finish aims to achieve all of these things and more.
Quality comes first at the seasoned plastic injection molding company Seaskymedical, which offers consumers a simple, affordable option to buy injection molding products. Don’t forget to contact Seaskymedical if there is a need for injection molding services.