It’s very important that before the injection molding process is started, the plastic injection manufacturer must have estimated the shrink rate, or else the part’s geometry, appearance, and performance will be affected. This can also result in timely and costly production line disruptions.
However, calculating the shrink rate isn’t a 100% guarantee that there won’t be injection molding shrinkage. This process involves a lot of complexities that need to be properly evaluated and in the case where there is shrinkage, what do you do? This and more will be discussed in this article.
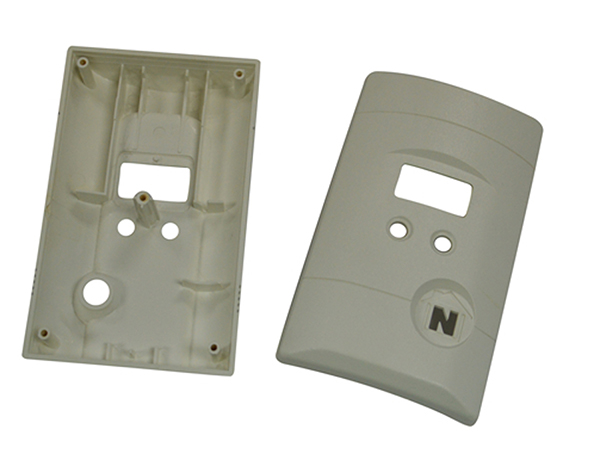
What is Injection Molding Shrinkage?
Injection molding shrinkage simply refers to how much the polymers will contract during the cooling phase. During the injection molding process, molten plastic material is injected into a mold cavity under high pressure, and when the plastic material cools, it shrinks as it solidifies. This shrinkage can cause the molded part to be smaller than the intended size, and have an uneven shape known as warpage.
Injection molding shrinkage can vary depending on the type of plastic material used, the design of the part, and the processing conditions. It is important to take into account the expected shrinkage during the design and tooling stages to ensure that the final part meets the required specifications.
To be safe, manufacturers often compensate for shrinkage by oversizing the mold cavity or adding additional material to the part, which is then trimmed or machined after molding to achieve the desired dimensions.
Mold Shrinkage Rate
Before beginning production, the mold shrinkage rate should have been predicted to eliminate the additional cost and adjustments. All plastic materials have a minimum and maximum shrinkage percentage, which helps you evaluate the changes in the plastic from when it’s molded to when it will be completely cool. This and other factors that influence the shrinkage rate should be considered.
How do You Calculate Mold Shrinkage?
The most convincing method to calculate the plastic injection shrinkage rate is to develop a prototype tool to mimic the cooling and gating requirements that’s used during production. Not only will this technique provide an accurate shrinkage measurement, it will also allow for the opportunity to change the tooling before the production begins in case a potential defect was predicted.
What Causes Mold Shrinkage?
Shrinkage in plastic injection molding can be attributed to several factors, which are highlighted below:
- Plastic Composition: The type of plastic used for injection molding can greatly affect the shrinkage of the final product. For example, high-density polyethylene mold shrinkage is due to its crystalline structure, which causes the polymer chains to contract during cooling.
- Molecular Weight: Higher molecular weight polymers tend to shrink less than lower molecular weight polymers because they have more intermolecular forces holding them together.
- Additives: Additives such as fillers, colorants, and lubricants can also affect the mold shrinkage of plastic parts. For example, adding a filler material can increase the stiffness of the plastic, which results in higher shrinkage during cooling.
- Stress Level: During the injection molding process, the time and pressure at which the part is placed under stress cause an excessive amount of fluid, which leads to shrinkage and brittleness. And if the plastic is subjected to high levels of stress during cooling, it can cause the polymer chains to rearrange and contract, resulting in higher shrinkage.
How Does Shrinkage Occur
Most of the shrinkage happens in the mold while the molten plastic is cooling. However, a small amount of shrinkage occurs after ejection as the molded part continues to cool. In fact, the plastic part may continue to shrink slightly after that till the temperature and moisture content becomes stabilized.
How to Avoid the Shrinkage in Plastic Moulding?
While shrinkage tends to happen often, it must be avoided when dealing with some delicate and sterile products, such as medical device injection molding. There must not be any form of distortion in the medical parts to ensure safety in healthcare procedures.
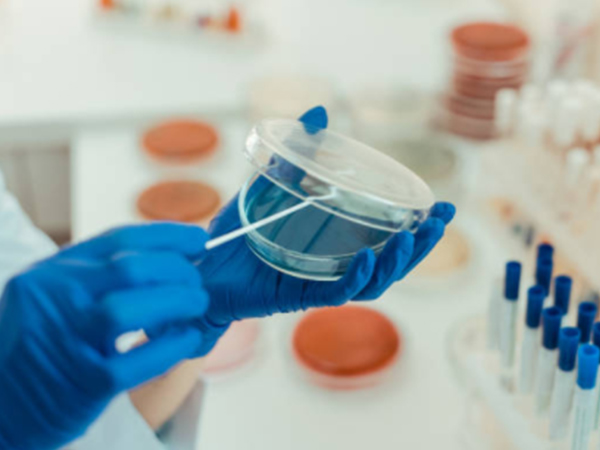
Optimize the Cooling Effects
One of the most effective ways to avoid shrinkage problems in injection molding is to optimize the cooling effects. Cooling channels or plates in the mold design should be used to ensure that the cooling process is uniform throughout the mold cavity. This will help regulate the temperature of the mold and prevent the formation of hot spots, which can cause uneven cooling and shrinkage.
Mold temperature controllers can also help with the cooling effects and maintain a consistent temperature throughout the mold. It is essential to maintain a balance as excessive cooling can cause warpage, which can lead to a defective molded part.
Reduce Wall Thickness Reasonably
Careful design and engineering of the part should be done to ensure that the wall thickness is consistent and optimized for the specific material being used. Thinner walls will result in a shorter cooling time, which will help minimize shrinkage.
However, it is important to note that reducing wall thickness can also cause the part to become more fragile and prone to breakage. Thus, it is essential to strike a balance between wall thickness and overall part strength. Furthermore, other factors such as the mold design and processing parameters can also affect the wall thickness of the molded part.
Reduce the Plasticizing Temperature
Lowering the plasticizing temperature can be done by adjusting the temperature of the plasticizing unit or by using a material with a lower melting point. A reduced plasticizing temperature will decrease the viscosity of the molten plastic, which will reduce the shrinkage caused by uneven cooling.
However, the plasticizing temperature should not be too low as this can cause other defects such as flash or incomplete filling of the mold cavity. It is essential to optimize the plasticizing temperature for the specific material being used to achieve the desired results.
Enhance Injection Pressure Speed
Increasing the injection pressure speed will force the material into the mold cavity more quickly and with greater force, resulting in a more uniform and consistent molded part. However, increasing the injection pressure speed can also cause other defects such as flow lines or burn marks on the molded part.
Therefore, it is important to optimize the injection pressure speed according to the customized plastic injection molding specifications to achieve the desired results.
Improve Back Pressure
Back pressure is the resistance of the molten plastic as it flows through the mold cavity. By increasing the back pressure, the material is forced to fill the mold cavity more completely and with greater force, resulting in a more uniform and consistent molded part.
However, excessive back pressure can cause other defects such as sink marks or voids on the molded part. It is essential to optimize the back pressure for the specific material and mold design to achieve the desired results.
Factors Influencing Shrinkage in Plastic Injection Molding
Polymer composition & material properties, applied processing conditions, and part design & geometry are three crucial factors that affect shrinkage in plastic parts.
Polymer Composition and Material Properties
The degree of shrinkage depends on the polymer’s molecular weight, viscosity, and crystallization behavior. A higher molecular weight and viscosity result in a higher degree of shrinkage, while crystallization behavior affects the shrinkage rate. Crystallizable polymers have a higher tendency to shrink than non-crystallizable polymers.
Additionally, additives such as fillers, fibers, and stabilizers can affect the shrinkage behavior of the polymer. Thus, it is crucial to select the appropriate material based on the desired shrinkage characteristics.
Processing Conditions Applied
The processing conditions applied in plastic injection molding can also affect shrinkage. The temperature, pressure, and cooling time all impact the shrinkage behavior of the molded part. Higher temperatures and pressures result in a higher degree of shrinkage, while longer cooling times lead to a slower rate of shrinkage. Thus, it is important to carefully select and optimize the processing conditions to avoid a shrinkage problem in injection molding.
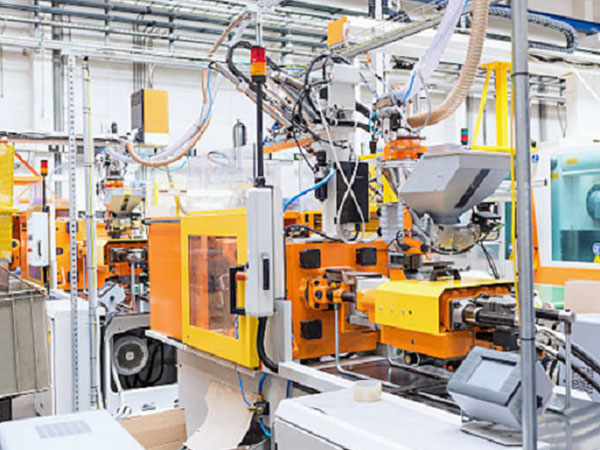
Part Design and Geometry
Part design and geometry, such as the thickness of the walls, the size and location of ribs, and the presence of sharp corners or edges can all impact the shrinkage behavior of the part. Thin walls, which are popular in medical plastic injection molding may experience a higher degree of shrinkage, resulting in warpage or distortion.
Additionally, the placement and design of gates and vents can impact the shrinkage behavior of the molded part. It is important to optimize the part design and geometry to minimize the degree of shrinkage and achieve the desired dimensions and tolerances.
Which Polymers Have High or Low Shrinkage
Some examples of polymers with high shrinkage rates include high-density polyethylene (HDPE), polypropylene (PP), and polycarbonate (PC). These materials have a high degree of crystallinity and can experience significant shrinkage during cooling.
On the other hand, some examples of polymers with low shrinkage rates include acrylonitrile butadiene styrene (ABS), nylon, and thermoplastic elastomers (TPEs). These materials have a lower degree of crystallinity and may experience less shrinkage during cooling.
Set up Your Plastic Moulding Project for Success With Seaskymedical
Seaskymedical is a leading plastic molding company that specializes in the manufacturing of medical plastic parts. We have more than 10 years experience of in handling various medical injection molding projects, starting from product development to mold design and manufacturing, material selection, and injection molding production. With an extensive capability to work with a wide variety of materials, we produce parts that are high-quality and functional.
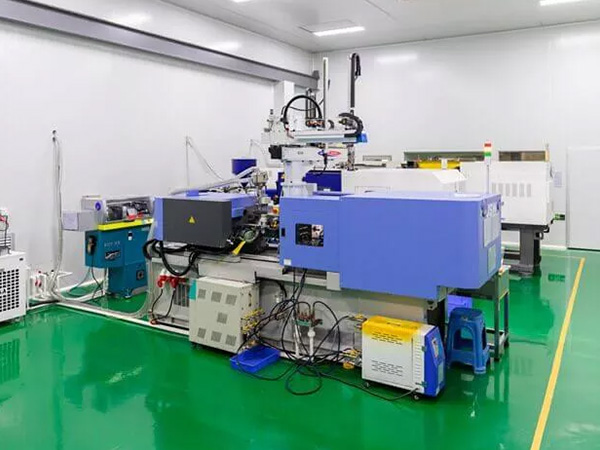
Our R&D team is composed of highly-skilled experts with rich knowledge and understanding of undertaking complex plastic injection molding projects with no shrinkage. All our activities are carried out in our ISO-certified factory using premium raw materials and state-of-the-art machinery that fastens the production process and ensures optimal quality. Afterward, they are inspected to ensure compliance with industry standards.
As a reliable plastic injection manufacturer with solid experience and specialty, we assist in all stages of production, including offering professional advice as to the best materials for your application, as well as other factors to consider. Our goal is to help set up your plastic mold project for success.
Conclusion
Injection molding shrinkage is a common issue in plastic part manufacturing. But it can be avoided by following some steps, which include the assessment of the resin shrinkage rate to ascertain the reliability of the polymer, the composition of the polymer, the injection molding process, and the plastic part shape. All these elements play a critical role in preventing the occurrence of shrinkage.
Overall, understanding the causes and how to solve shrinkage in plastic injection molding is a great determinant to the success of every injection molding process. Do you need professional assistance with your plastic injection molding projects, you can reach out to us here.