For plastic objects, injection molding is the preferred manufacturing method. Injection molding is a manufacturing technique that allows producers to rapidly produce large quantities of comparable objects. The process involves filling various molds with molten material using a highly pressurized nozzle.
The approach makes it possible to produce thousands to millions of similar things. It accomplishes this in cycles with cycle times measured in seconds. Molding machines is used in a variety of sectors for both large and small products. As the need for plastic goods has grown, so has the design complexity.
To improve the efficiency of the injection molding process, the mold must be built so that it can be readily opened and closed. To accomplish this, use a mold with an incorporated lifter. Numerous elements must be managed while constructing an injection molding machine lifter.
This includes the size and weight of the mold. Also, the material to be employed must all be taken into account. In addition, the shape of the lifter must be considered. The toggle clamp is the most commonly utilized type of lifter in injection molding.
The upper part of this type of lifter is attached to the mold. While the lower part is attached to the machine. The hinged connection between the two components causes them to move in opposite directions when the toggle clamp is engaged, opening or closing the mold.
A pneumatic lifter is another form of lifter that can be used. Compressed air powers this sort of lifter. Pneumatic lifters are typically used for larger molds or molds that are difficult to open with a toggle clamp.
In addition, the quantity of rejected parts produced per million can be reduced using a high-quality mold. In addition to cutting down on tooling and cycle times, a well-designed mold can cut costs associated with post-processing and those associated with tooling.
There is a correlation between the intricacy of the product’s design and the complexity of the mold. When undercuts are incorporated into the product’s design, this becomes a significantly more challenging task.
There are holes, slits, indentations, or protrusions in this product. This makes product ejection rather tricky. A mold that opens in two halves is the most basic design. This design makes it easier to remove the product and shouldn’t require any post-processing after it has been released. The ejection of components with undercuts necessitates a more complex mold design.
This article will discuss injection molding lifter design, standard requirements, and design considerations to assure effectiveness.
What Is a Lifter in Injection Molding?
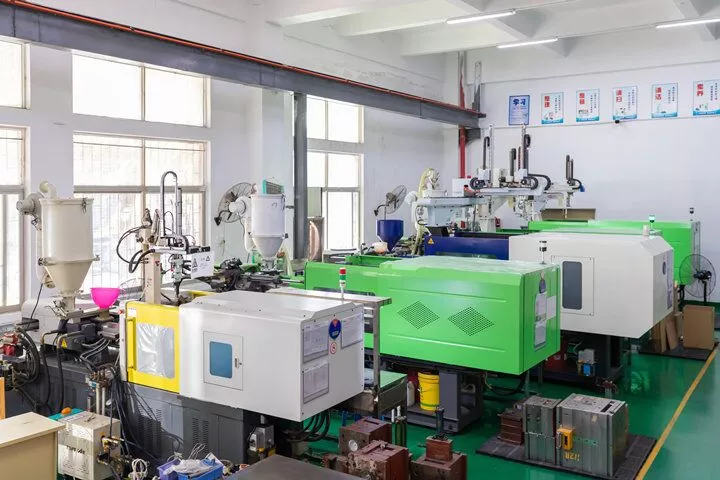
An injection molding lifter is an essential component of the injection molding process that slides and pulls the cavity steel away from the undercuts in the die as the ejection stroke progresses. This allows the cavity steel to be moved farther away from the undercuts in the die.
Undercuts are required for particular items, and the usual mold ejection process makes removal difficult or impossible. The ejector pins are pressed in a single direction in conventional ejection. When there are undercuts, the product’s release is jeopardized.
The usual lifter is used to manufacture the internal undercuts of a plastic molding object while simultaneously providing a mechanism of ejection once the finished product has been formed, such as plastic molded chairs or car plastic parts. This mechanism is made up of a very simple structure with some rigidity that allows it to travel a very short distance.
The injection molding lifter comprises two essential parts: the body and the shaping portions. Lifters for injection molding can be classified as integral or non-integral. These two distinctions are determined by the construction’s body and forming components. Necessary lifters are much more compact and damage-resistant. As a result, it is used in injection molding operations involving more extensive parts.
An integral lifter mold design also allows for the employment of a combined form, which allows for the installation of replacement parts and the maintenance and repair of the injection molding machine without affecting other components.
How Do Mold Lifters Work?
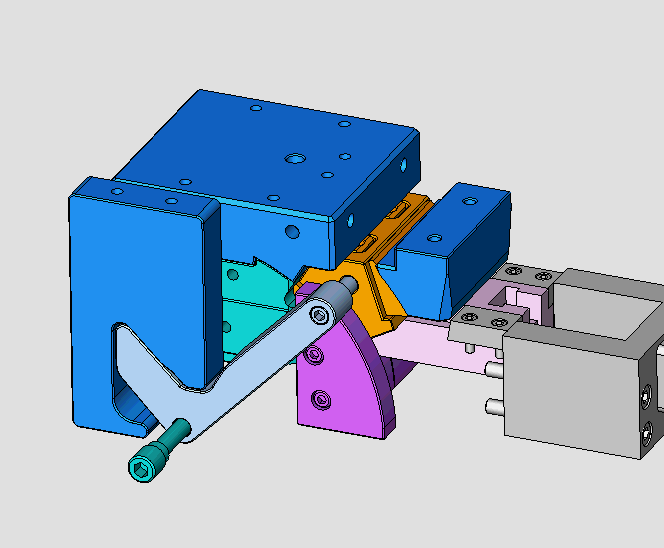
There are several types of lifters. Different mold manufacturers develop and manufacture lifters in several methods. The lifter is incorporated into the molding region during injection molding.
The precise fabrication and installation process varies based on the equipment’s various specifications. It also depends on the design of the product. However, the lifter’s general operation remains consistent across all systems. The goal of any lifter or mold system is to make product release easier. This is done by extending the range of motion.
The mold lifter is attached to the mold’s end, and the object to be molded is placed on it. The machine then starts injecting hot plastic into the mold, and the lifter physically moves up and down as the injection happens. As a result, the molded object is always raised out of the machine, simplifying removal.
Furthermore, lifters comprise the lifter body and the lifter forming sections. They are classified as integral or non-integral. Integral lifters have a single body and forming portion. Nonintegral lifters are composed of two separate pieces that function as the body and forming components.
Integral lifters are better suited to molding smaller parts. They are simpler and more popular because they are easier to manufacture and maneuver. Non-integral lifters are used in broader portions of the body.
This allows them to be built more extensively, making them easier to operate and maintain. Integral lifters are more common. They are more durable and smaller in size. The lifter’s shape can also vary. Some lifters are cylindrical and T-shaped. Because it is easier to manufacture, the cylindrical lifter is more common. The T-shaped filter is commonly used for larger products that require precise shaping.
Lifters, as the name implies, provide a “lift” to aid with product ejection. They allow the product to move laterally during the ejection process. They are incorporated into the mold closure and opening mechanism in an angled manner.
The lifter is inserted into a locating block with a corresponding angled hole. The block is located between the ejector plates and the lifter. The mold is ready to be removed once it has totally cooled. In traditional systems, mould opening causes the ejector plate to evacuate the pins.
This forces the stuff out of the mold. Ejectors come in a variety of styles, including blade and pin models. However, the releasing processes are equivalent.
Standard Requirements for Injection Molding Lifter Design
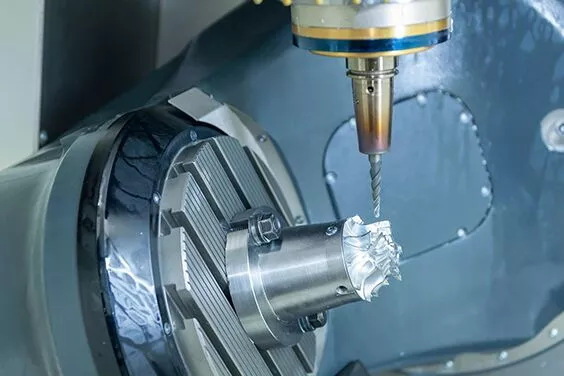
For an injection molding lifter design to function correctly, it is necessary to satisfy several different criteria and specifications. The following are the standard requirements:
- A minimum of 3 degrees of the draft must be on all shut-off surfaces pointing in the direction of slide travel. If a consumer requests explicitly, a shut-off angle can be smaller than the standard 3 degrees.
- Any slide design must include two-angle pins that are longer than 7 inches.
- Three degrees is the most minor angle difference between the angle pin and the rear wedge.
- The rear wedge must be built to withstand injection pressure by raising the entire moulding surface. The lifter must be considered for any large molding surface if the design is double-edged.
- When the slide is in the back section, a minimum space of 1.2 inches must exist between the slide detail and the molded piece.
- Unless the user specifies differently in writing, there should be no ejection beneath the slide detail. If the client requires that the ejection be positioned beneath the sliding element, the switches must be limited to the maximum movement range of the ejector.
- For optimal ventilation, every deep rib detail must be sub-inserted.
- Slides with flat faces that can engage the cavity in the direction of the slide’s motion must be manufactured with face-loaded or external springs to prevent gaulding.
- There must be a hardness difference of at least 6 points between the slide material and the Gib material. RcC is the symbol for this.
- The whole length of the slide foot must equal 50% of the total height of the slide.
Considerations in Lifter Mold Design
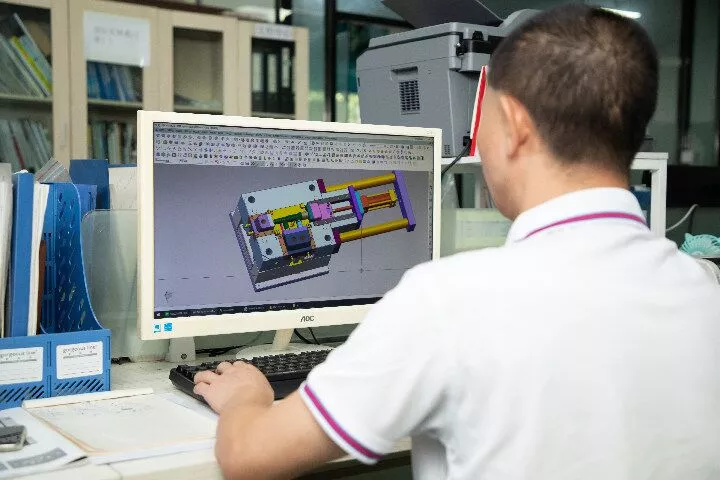
Specific material specifications must be addressed during the design phase for an injection molding lifter to perform appropriately. The movement of the lifter and the weight of the load that the lifter will be lifting are the most critical aspects of the entire procedure.
The lifter performs precise motions, such as entering and exiting the locking block and thus puts a significant force on the material being molded. The lifter must be made of an abrasion-resistant material that can withstand high pressure during the process to ensure that nothing is injured during the operation.
The materials used in the lifter must be stronger and more resilient as the load increases in weight. Another critical factor is the height at which the load will be hoisted. A more robust frame and more extensive supports are required for greater lifting height.
To ensure a lifter’s safety and durability, the materials utilized in its construction must be carefully chosen. The frame of the angular lifter injection molding must be composed of solid and long-lasting materials, such as steel or aluminum.
The supports that hold up the frame must also be made of a durable material and properly fastened. The load-bearing platform should be made of a strong material, such as wood or plywood.
Significantly, the platform must be reinforced to avoid collapse under the weight of the load. Despite its effectiveness, using this lifter incurs additional costs due to its complex design.
Material Considerations for Lifter Design
Some injection molding procedures need no lifters at all. Depending on the mould engineers ‘ preferences, injection molding producers can use various molding options to achieve the same goals. Two sliders and inserts are the most common.
Sliders work similarly to lifters but have a distinct mechanism. On the other hand, inserts use a simpler mold ejection mechanism that ejects the product together with the inserts.
How to Do Injection Molding Lifter Design
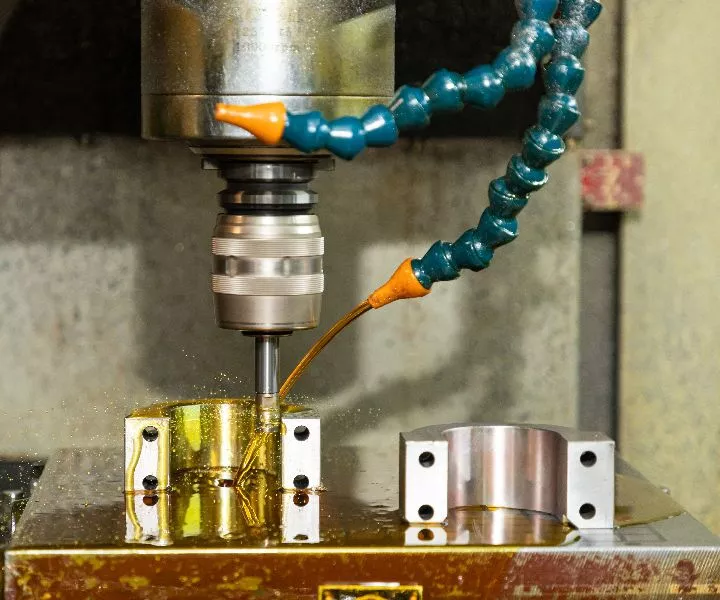
The molten material is pumped into a mold to create a final product in injection molding. To ensure the injection process’s success, the mold must be designed so that the molten material flows consistently and smoothly into all places. The lifter mould design is one of the most essential aspects of an injection mold.
The lift design is in charge of distributing the material evenly throughout the mold. It also keeps the material from gathering in one spot, which could lead to an uneven or misshapen final product. The angular lift design also aids in preventing material from leaking out of the mold during the injection process.
The main advantage of linear lifts is that they are much easier to design and build than non-linear lifts. This simplicity lowers the cost of manufacturing linear lifts. Furthermore, linear lifts are more trustworthy than non-linear lifts.
Alternatives to Mold Lifters
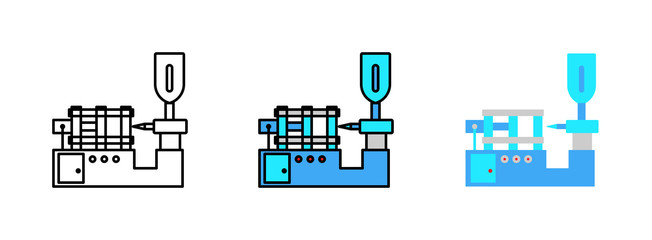
The method and mold lifter design part will be evaluated by the mould design engineer. This will help determine which features are the most useful. Numerous factors determine the feature selection for undercut release.
These include tooling, capabilities, cost, and the component’s design. Sliders and inserts are alternatives to lifters when they are not used. Sliders function similarly to lifters, but their mechanism is distinct.
Inserts allow for the use of a simpler mold ejection mechanism. This is done while keeping the undercut. Inserts expel both the product and the inserts. The implant is then removed in a separate procedure. When the part design allows it, this is a good option.
Conclusions
The design of an injection molding lifter can be made more efficient by following a few simple guidelines. By making the most of the available space, minimizing friction, and using the right materials, an injection molding lifter can be designed to run more efficiently and smoothly.
Those who want to start a medical-related business may discover that working with Seaskymedical is an excellent option. Seaskymedical is an ISO-certified medical molding company that produces injection molded plastic products for the medical market. In the firm’s ISO 8 cleanroom, which is used for production, assembly, and packaging, the company utilizes injection molding equipment that is reliable and raw ingredients that have been verified.
The medical plastic injection molding producer goes through a stringent inspection. This is to ensure that they are up to par with the norms of their industry. Customers benefit from Seaskymedical’s assistance because the company also offers custom mold and design and superior medical injection molding solutions for various medical products. Apart from medical injection molding, Seaskymedical also custom platsic injection molding for other industries, like electronic enclosure and automotive parts molding. Contact us to know more.