Injection molding is a quintessential manufacturing technique employed for the fabrication of premium-grade plastic parts. Esteemed for its adaptability, operational efficiency, and fiscal prudence, it is indispensable in a myriad of industries. Nonetheless, as with any manufacturing practice, injection molding might present certain anomalies that could compromise the integrity and performance of the end product. Comprehensive comprehension and timely remediation of these challenges are crucial to guarantee a seamless production continuum. In the ensuing segments of this analysis, we will elucidate ten prevalent injection molding defects, delineate their underlying causes, and suggest robust strategies for their amelioration.
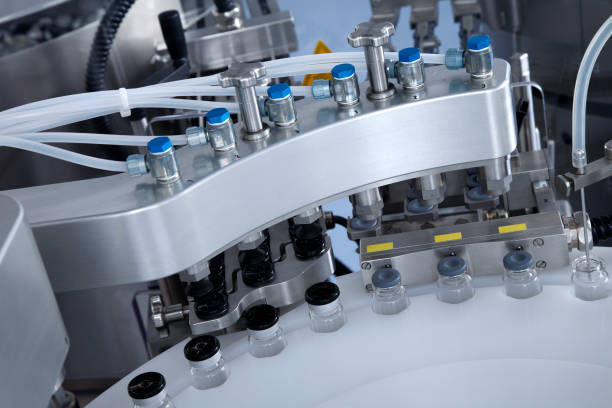
Some of the most common injection molding defects are listed here:
- Flow lines
- Sink marks
- Vacuum voids
- Surface delamination
- Weld lines
- Short shots
- Warping
- Burn marks
- Jetting
- Flash
Flow Lines
Flow lines are linear demarcations or streaks observed on the surface of plastic components. These demarcations emerge due to differential cooling rates during the molding process, resulting in an uneven distribution of the molten plastic.
Causes: The formation of flow lines can be attributed to several factors, including inadequate material throughput, sub-optimal melt temperatures, accelerated injection velocities, and restricted gate openings. Additionally, complex component geometries, variable wall thicknesses, or the integration of reinforcing fibers can exacerbate the propensity for flow line development.
Solutions: To counteract flow line occurrences, it is imperative to optimize the injection velocity, molding temperature, and wall specifications. Introducing a strategically designed gate, enhancing mold thermal consistency, and utilizing mold flow analyses are proficient approaches to minimize the potential for flow line anomalies.
Sink Marks
Sink marks are depressions manifested on the surface of a molded component, primarily attributable to non-uniform cooling and contraction during the solidification process.
Causes: Sink marks can be attributed to several factors, such as suboptimal packing pressure, insufficient cooling time, elevated melt temperatures, excessive wall thickness, or unsuitable gate locations. The incorporation of structural features like ribs, bosses, or significant design elements can exacerbate their occurrence.
Solutions: To mitigate the occurrence of sink marks, it is recommended to optimize packing pressure, prolong the cooling phase, and reduce the thickness of the component. The strategic inclusion of supporting elements such as ribs or gussets, coupled with precise gate positioning, can effectively minimize sink mark defects.
Vacuum Voids
Vacuum voids refer to the presence of air pockets or cavities that emerge within a molded component during its formation process. Such voids materialize when air gets confined, and subsequently, drawn inward as the material undergoes cooling and solidification.
Causes: A multitude of factors can instigate the development of vacuum voids in the molding process. These include insufficient venting, overly rapid injection speeds, and unsuitable mold temperatures, along with a pronounced viscosity of the resin used. Furthermore, deficits in mold design, gate design irregularities, and lack of adequate venting facilities significantly contribute to vacuum voids’ occurrence.
Solutions: Implementing several corrective strategies is crucial to mitigating vacuum voids. Enhancements in venting mechanisms, modulation of injection speeds, and meticulous optimization of mold temperatures are imperative. Concurrently, ensuring the robustness of gate and runner designs, paired with the employment of resins with reduced viscosity, proves instrumental in minimizing the prevalence of vacuum void defects in molded parts.
Delamination
Delamination pertains to the distinct separation or division of layers within a manufactured component. This phenomenon arises from the insufficient melding of molten layers during the intricacies of the injection molding procedure.
Causes: Delamination may be instigated by suboptimal material compatibility, insufficient drying of the material, inadequate melt temperature, or prolonged cooling durations. Moreover, unsuitable injection velocities, insufficient holding pressures, or the infiltration of contaminants may exacerbate delamination anomalies.
Solutions: To circumvent delamination, it is imperative to select harmonious materials, execute comprehensive resin drying, and maintain an appropriate melt temperature. Refinement of injection velocity, sustaining optimal holding pressure, regulating cooling duration, and upholding a contaminant-free molding environment can further mitigate the onset of delamination.
Weld Lines
Weld lines are defined as noticeable seams that emerge when multiple flows of molten plastic intersect and solidify, adversely affecting the structural integrity of the molded component.
Causes: Weld lines can be attributed to factors such as inadequate material flow, insufficient melt temperatures, high injection velocities, complex component designs, suboptimal mold pressures, or interferences like inserts or ribs within the mold cavity.
Solutions: Addressing weld lines necessitates the optimization of material flow, regulation of injection velocities, and the implementation of appropriate gate designs. Enhancing melt temperatures, fine-tuning processing parameters, and reducing mold interferences are also pivotal in diminishing weld line occurrences.
Short Shots
Short shots are a manufacturing defect wherein the mold cavity is not adequately filled with molten plastic, leading to an incomplete or undersized component.
Causes: The occurrence of short shots can be ascribed to inadequate injection pressure, non-optimal melt temperatures, incorrect gate dimensions or placement, and prolonged cooling durations. The issue can be exacerbated by the existence of entrapped air.
Solutions: To mitigate the prevalence of short shots, it is imperative to fine-tune the injection pressure, calibrate the melt temperature, and ensure accurate gate design and placement. Minimizing the cooling duration, enhancing mold ventilation, and the eradication of air entrapment are vital measures to circumvent such anomalies.
Warping
Warping pertains to the inadvertent alteration or deformation of a fabricated component, causing it to deviate from its specified geometry or dimensions. This aberration arises primarily due to non-uniform cooling and contraction dynamics within the component.
Causes: The principal factors inducing warping include inadequate cooling durations, flawed mold configurations, non-uniform wall thicknesses, and abrupt temperature fluctuations during the component’s demolding. Furthermore, the component’s architectural design, material specifications, and inherent stress factors can intensify its susceptibility to warp.
Solutions: To mitigate warping, it’s essential to refine the cooling methodologies, adhere to rigorous mold design criteria, and ensure wall uniformity. It is also crucial to circumvent abrupt temperature transitions during demolding, employ suitable mold release agents, and exercise prudent material selection to diminish the potential risks of warping.
Burn Marks
Burn marks pertain to the visible discolorations that manifest on the surfaces of molded components, a consequence of undue heating or the charring of plastic resin amidst the injection molding procedure.
Causes: The genesis of burn marks can be traced to a multitude of elements including, but not limited to, escalated melt temperatures, excessive dwell durations, high-velocity injection rates, or insufficient venting mechanisms. In parallel, the incidence of moisture or impurities within the resin could significantly amplify the susceptibility to the materialization of burn marks.
Solutions: The circumvention of burn marks necessitates meticulous management of the melt temperature, calibration of residence time to its optimum, and the judicious modulation of injection velocities. Enhancing the venting systems, guaranteeing comprehensive resin desiccation, and maintaining an immaculate molding milieu constitute essential steps to rectify inconsistencies related to burn marks.
Jetting
Jetting arises when the molten plastic is introduced into the mold cavity with an excessive velocity, leading to discernible linear patterns or deformities on the finished product’s surface.
Causes: The primary contributors to jetting encompass suboptimal gate design, overly rapid injection speeds, non-optimal melt temperatures, and deficient mold venting. The scenario can be exacerbated by the existence of contaminants or a non-standard wall thickness.
Solutions: To mitigate jetting phenomena, it is advisable to refine the gate design, calibrate injection speeds to appropriate values, and ascertain the melt temperature is within the recommended range. Furthermore, improving mold venting, reducing contaminants, and adjusting the wall thickness are essential steps to counteract jetting-associated complications.
Flash
Flash is the unintended protrusion of plastic beyond the designated part geometry, observed at the mold’s parting interface.
Causes: Flash may arise from undue injection pressure, insufficient clamping force, deteriorated or impaired molds, or misalignment of parting surfaces. Moreover, inadequate mold upkeep or a mispositioned ejection system can lead to flash anomalies.
Solutions: Addressing flash requires fine-tuning the injection pressure, augmenting clamping force, and upholding mold maintenance standards. Precise alignment of parting interfaces, diligent inspection and rectification of mold impairments, and ensuring an aligned ejection system are also pivotal in averting flash irregularities.
Why Injection Molding Defects Exist?
Aspect | Description |
Process Overview | Injection molding is a core process in the manufacturing of products, especially when using plastic injection molding. The process involves the flow rate of molten material into an injection mold, where the molding material solidifies as it cools. |
Common Defects | A variety of defects can manifest in the finished product, with causes ranging from material use to production equipment intricacies. |
Thin Layers/Knit Lines | One of the most common quality defects resulting from resin flow meeting from different directions. It can be caused when molten material flows at varying rates or speeds through the mold. These can cause color inconsistencies in the molded component, especially if contaminated by foreign material or residual resin from previous production. |
Uneven Cooling | Major cause of defects. Different areas of the molded part might cool at varied rates leading to uneven shrinkage. Thicker parts might cool differently than thinner areas, causing internal stresses. This might also result in flow marks or minor surface defects. Consistent wall thickness is vital for prevention. |
Air Bubbles | Introduced potentially from gas vents, they are common defects in plastic injection molding. They can compromise the strength of the part and be visible in the finished product. Some severe cases, like missing prongs, can be due to inadequate pressure or issues like excessive temperature and heating during molding. |
Foreign Materials | Different colored plastics or foreign materials can mix with the base material if there’s leftover resin from previous production. This might cause color inconsistencies in the molded part. Mold tool defects or inconsistent cooling can lead to excess material in the component, causing issues affecting the product’s function. |
Mold Walls & Injection Gate | They ensure the material progresses in a unidirectional manner. Any deviations may lead to flow anomalies or surface irregularities. Challenges such as elevated temperatures, undue heating, or cooling complications can result in defects like thermal degradation. The internal section might exhibit problems stemming from insufficient gas venting or inconsistent material cooling, leading to internal strain. |
Preventive Measures for Avoiding Injection Molding Defects
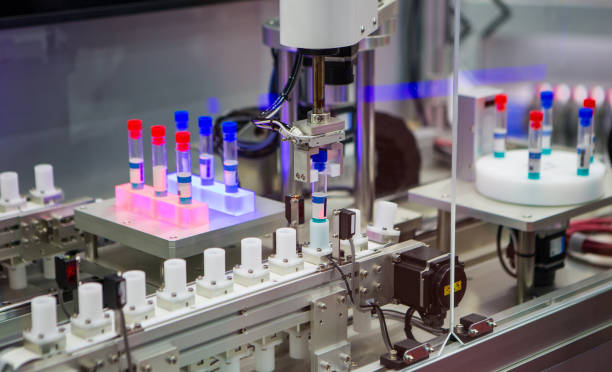
To enhance the efficiency and quality of injection molding processes, please adhere to the following professional guidelines:
- Choose materials with discernment and conduct compatibility analyses.
- Execute mold flow assessments coupled with advanced computational simulations.
- Ensure complete resin desiccation before molding.
- Maintain optimal processing parameters, taking into account melt temperature, injection speed, and cooling time.
- Engineer molds with a balanced design, prioritizing ideal gate placement and efficient venting.
- Conduct periodic inspections and upkeep of molds.
- Allocate resources to the ongoing education and development of operators and technicians.
- Implement stringent quality control protocols throughout the production process.
- Undertake detailed root cause analyses to address and mitigate recurring defects.
- Remain dedicated to the continuous improvement and supervision of the injection molding procedures.
Conclusion
Injection molding anomalies can negatively influence the lifespan, operational efficiency, and general excellence of fabricated plastic parts. An in-depth understanding of these imperfections, identifying their root causes, and the implementation of corrective measures outlined in this manual, enables manufacturers to maintain elevated quality benchmarks. The refinement of the injection molding process and the realization of uniform, reliable results are contingent upon the collaborative and open interactions amongst designers, engineers, and production personnel. It is pivotal that these professional groups engage in synergistic efforts to enhance procedural integrity and product consistency, affirming the adherence to exemplary manufacturing standards.
At Seaskymedical, we maintain a rigorous commitment to defect-free components. We proactively address challenges and provide prompt solutions. For further information on our approach, we welcome engagement with our expert team.