Injection molding retains innumerable applications in a broad range of industries, including the medical industry, automotive industry, telecommunication field, consumer electronics, transportation industry, etc. In 2022, the size of the international injection molding market was USD 273.2 billion. In addition, it is estimated to reach USD 397.6 billion by 2030.
Injection molding allows broad material selection, produces complex shapes easily, ensures quick production, assures high repeatability, and produces little to no waste.
Due to the various benefits of injection molding, this manufacturing process is highly used by reliable injection molding manufacturers.
What Is Injection Molding
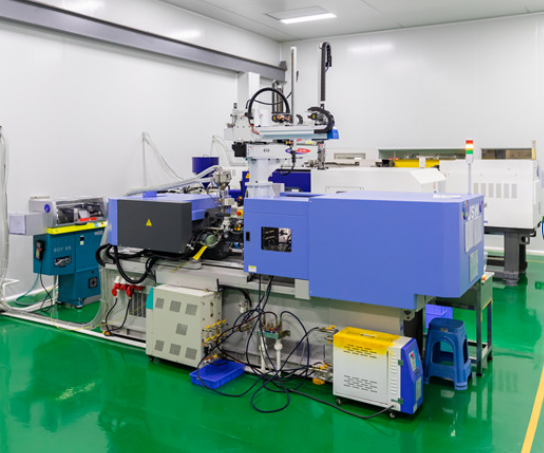
Injection molding is an old manufacturing procedure for creating parts by infiltrating molten substances into a mold. Materials like polymers and synthetic resins are heated until they are melted, then they are transferred to a mold, where they are chilled to take on the desired shape. This method is known as injection molding because it resembles the procedure of injecting fluids with a syringe. With injection molding, a wide variety of parts, even those with intricate shapes, can be produced swiftly and continuously in significant quantities.
To start the medical device injection molding process, resin pellets are loaded into the hopper, which is the material entry point. In order to prepare the pellets for injection, they are subsequently heated and melted in the cylinder. The substance is then driven through the injection unit’s nozzle before it is pushed into the mold cavity via branching runners and a passage in the mold known as sprue. The mold opens, and the molded object is expelled from it when the material has cooled and hardened. The sprue and runner are removed from the molded item to complete it.
Advantages Of Injection Molding
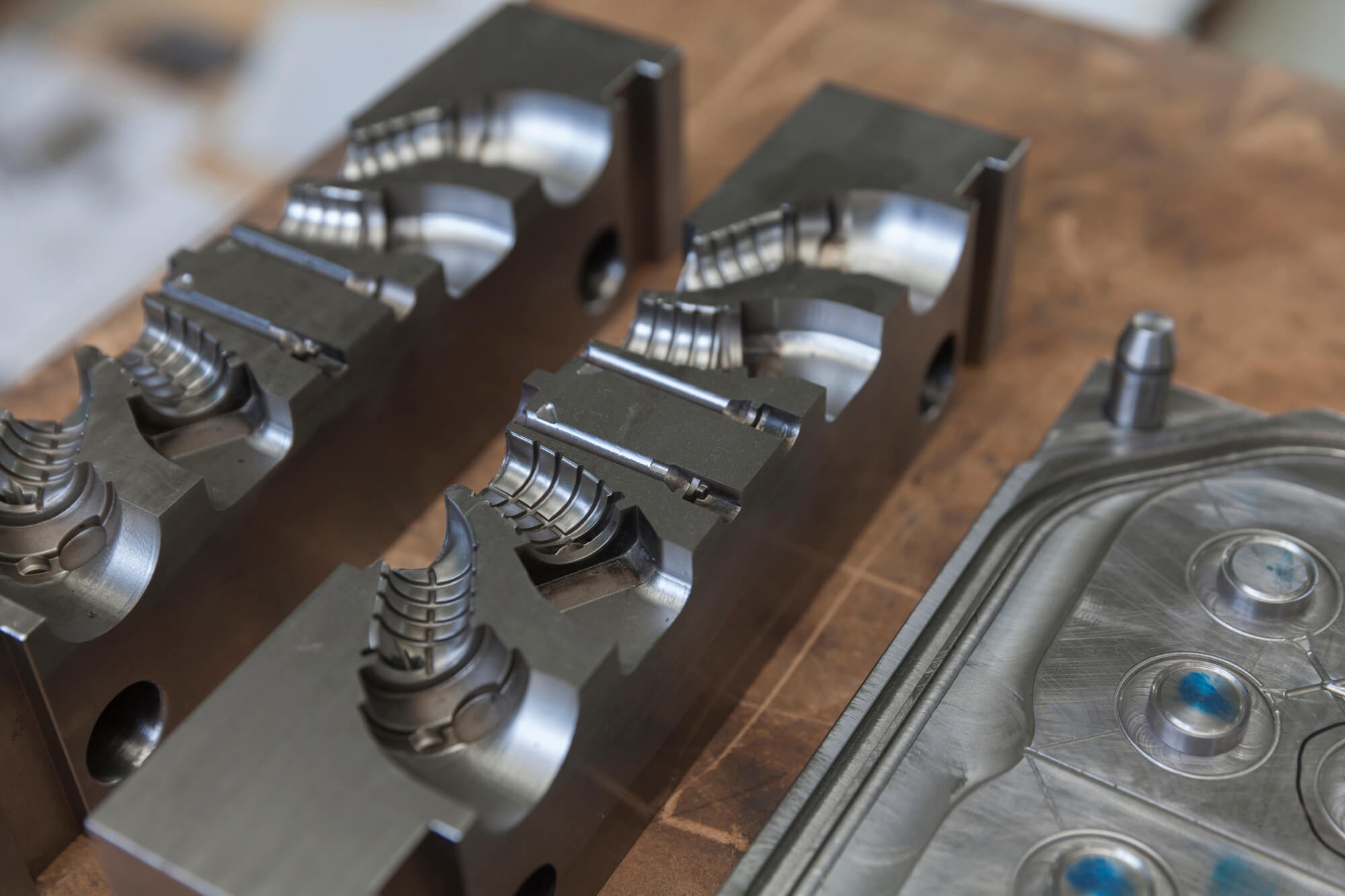
Below are the primary advantages of the injection molding procedure, which explains why many medical plastic manufacturers are choosing this procedure for manufacturing plastic parts for different applications.
- Wide Material Selection
Based on the qualities the final product should have, one can choose from a wide variety of plastic materials. Even including fillers in the molding substance will increase the finished part’s strength. Currently, thermoplastics, thermosets, resins, and silicones are only a few of the approximately 25,000 engineered substances that can be used in injection molding.
One can choose the material that has the ideal combination of mechanical, chemical, and physical attributes. Acrylonitrile butadiene styrene, polystyrene, polyethylene, and polypropylene are examples of materials that are frequently utilized. To create a part with high strength, impact resistance, or stiffness, it is also possible to combine different materials.
- Highly Efficient And Short Lead Time
Though 3D printing or CNC machining one part needs many minutes or hours, most injection molding processes last about 10 to 60 seconds. Even the parts with intricate geometry need 120 seconds or less to form. It is possible to combine numerous smaller components in a single larger mold.
One can produce hundreds of similar components each hour at a reasonable cost. In addition, it assists in maximizing productivity and making the most of every mold. Utilizing a multi-cavity or family mold, which produces many pieces from a single press, might occasionally help in enhancing output.
- Produces Complicated Geometries With High Tolerances
Massive quantities of complex, even pieces can be produced via injection molding. To facilitate ejection and produce exact parts, one must check the weld lines, vent and gate placements, corner transitions, rib and boss design, wall thickness, and other things.
The plastic molding companies can attain repeatable part tolerances of ± 0.500 mm (0.020″) with injection molding. Some applications even allow for the production of parts with tolerances as low as ± 0.125 mm (0.005″), making them as exact as 3D-printed or CNC-machined parts and suitable for the majority of applications.
- Reliable Repeatability
After the mold is made, it is simple to produce hundreds of components before tooling needs to be maintained. A full-scale plastic production mold can survive for over 100,000 cycles. In addition to that, as each item is made using the same mold during injection molding, the products will be similar.
- Affordable Price Per Part
The plastic injection molding tool requires a large initial investment, but after that, the expense per item is relatively inexpensive. The cost per part for massive volume production is quite cheap. One can reduce expenses by employing a custom plastic injection molder, even for modest volumes, such as those between 10,000 and 25,000 components.
- Less Labor Costs
The majority of the phases in the highly automated process of injection molding are carried out by a machine. It is run by an operator with little assistance from physical labor, which is why it lowers the expense of production.
- Little To No Waste And Can Be Reused
In comparison to numerous other production processes, injection molding in clean room generates very little amount of waste. Even if there is any leftover or trash plastic, it can be recycled and used again. The material can be reground and utilized again, even with the runners, sprues, and remaining pieces of plastic.
Disadvantages Of Injection Molding
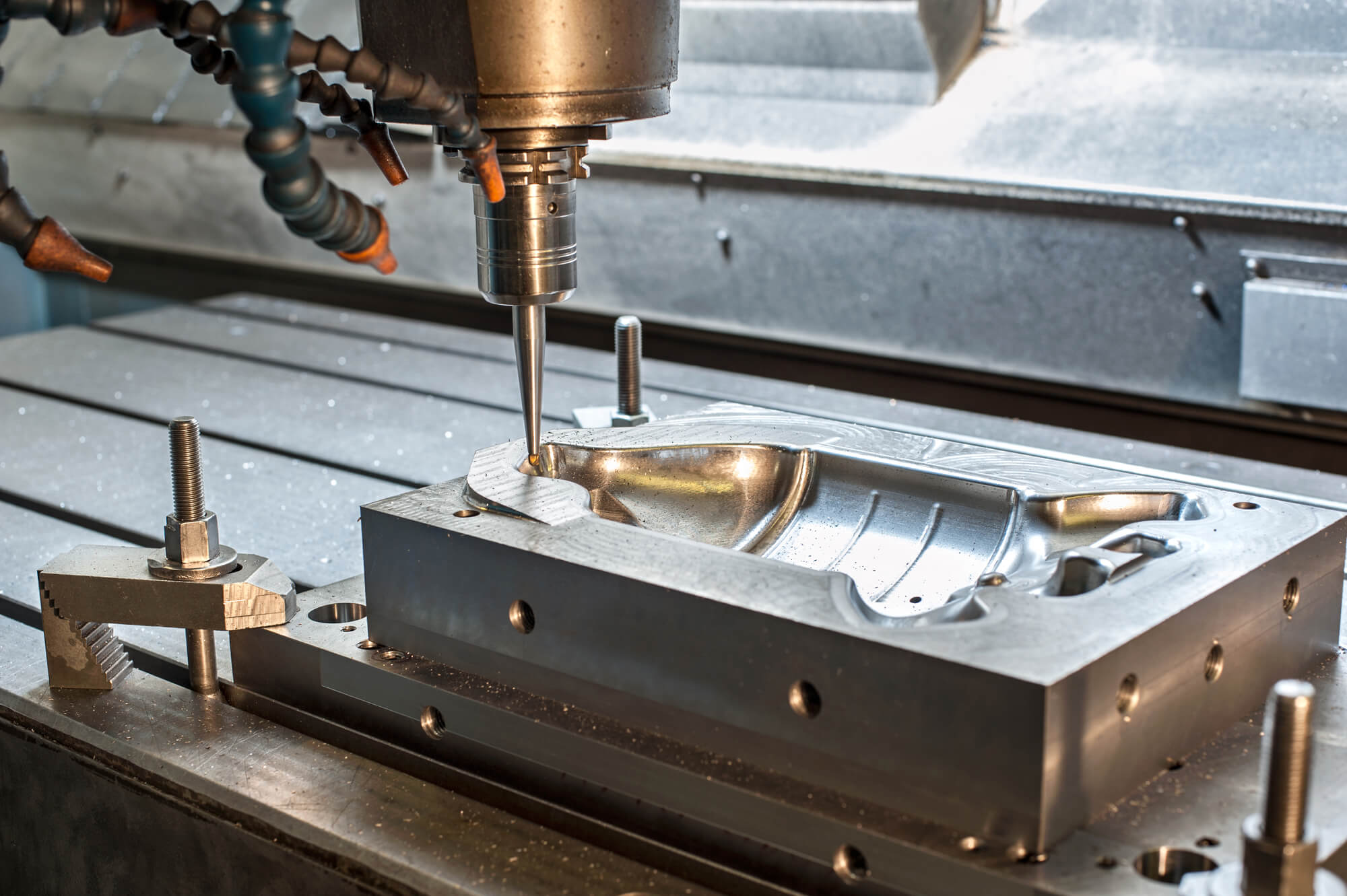
The following are the top disadvantages of injection molding because of which a few manufacturers are in dilemma of whether to use this procedure or not.
- Initial Costs Are Very High
As each injection molded part requires customized tooling, there are substantial initial start-up expenses, making low-volume production very expensive. Tooling for a simple design and a tiny production can range in price from $2,000 to $5,000. In contrast, the price for creating large, complex molds for large-scale production will be more costly than that amount.
- Costly And Hard To Make Design Changes
Any modification to the part’s shape and size necessitates altering the mold cavity’s dimensions. If the part’s size is to be enlarged, a section of the cavity needs to be removed to make room for more molten plastic. Tooling must be created utilizing metal fabrication techniques because it is created with strong metal. In addition, to decrease the part size, another tool with tiny cavities is needed for medical molding companies to produce the parts.
- Starting Lead Time Is High
From product development to manufacturing the part, it may take months of design, testing, and tool manufacture. An industrial 3D printed product typically includes a lead time of 3 to 5 days, and a CNC machined part can be delivered in between 5 to 10 days. Nonetheless, the lead time for injection molding is very long. Making tools often need about 5 to 7 weeks, while making and shipping parts usually needs another 2 to 4 weeks.
- Design Restrictions
A few design components will need to be taken into account. For instance, one such design element is to use draught and radii to aid in the ejection of the pieces. Other ones include limiting wall thicknesses and deterring undercuts and sharp edges. If aesthetics are important, one should also think about where to place the ejectors, gates, cooling lines, etc.
Find A Reliable Injection Molding Company
Make sure to contact SeaskyMedical for molding injection molded parts for various industrial applications.Make sure to contact SeaskyMedical to injection mold plastic parts for various industrial applications. SeaskyMedical also offers custom injection molding services for manufacturing many types of products.
SeaskyMedical is a 10+year experienced injection molding manufacturer based in China with enough domestic and international product demand. Being an ISO-certified company, SeaskyMedical is equipped with the latest cutting-edge injection molding machines, ISO 8 cleanroom, and advanced molding technology techniques.