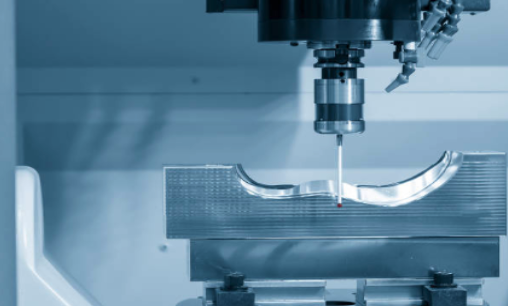
Injection molding is a special method used to make medical devices. It’s like making ice cubes. You pour water into a tray and freeze it to get solid ice. Similarly, in injection molding, you inject liquid material into a mold, cool it, and get a solid product.
This way, you can make simple things like bottle caps to more complex items like life-saving medical tools. It is like using a detailed, accurate, and large stencil to create a lot of pieces quickly and cheaply.
The best part is, it can use different materials. From plastic to metal, it’s all possible. So it can make many different types of medical devices. This process helps a lot in healthcare as it can make good quality and reliable tools that doctors and nurses can use to help people.
Why Medical Device Injection Molding Plays Critical Role in the Dental Industry?
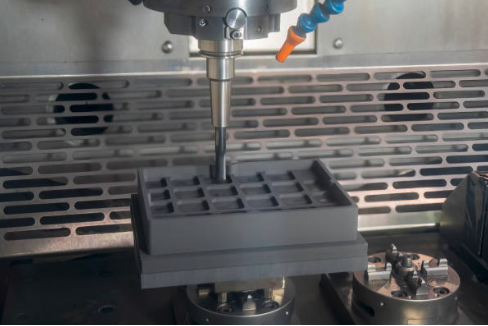
In the dental industry, the medical device injection molding process has revolutionized the way dental tools and applications are manufactured. Precision is vitally important, and this technique enables the production of complex geometries while ensuring uniformity and high-quality.
Dental devices such as caps, bridges, and orthodontic appliances all benefit from injection molding. The ability to produce devices from various biocompatible materials has significantly improved patient comfort, while the detailed precision enhances the functionality and longevity of the devices created.
Moreover, the cost-effectiveness of injection molding permits more affordably priced products, thus potentially enhancing oral health globally. It also facilitates the production of single-use tools to maintain high standards of hygiene and sterility, an essential aspect of dental care. By enabling mass production at low costs, the technology enhances both patient care and the bottom line for dental tool manufacturers.
On top of these practical benefits, injection molding can fulfill aesthetic needs. The use of colorants with mastery of the injection process allows manufacturers to create devices that are esthetically pleasing and more personalized to patient preferences.
In summary, medical device injection molding is playing a critical role in advancing the dental industry. As technology improves, the technique is anticipated to continue enhancing dental care delivery, bringing a more effective, safer, and pleasant experience to patients, and cost-effectiveness to the industry.
Novel Techniques of Medical Device Injection Molding in Orthopedics
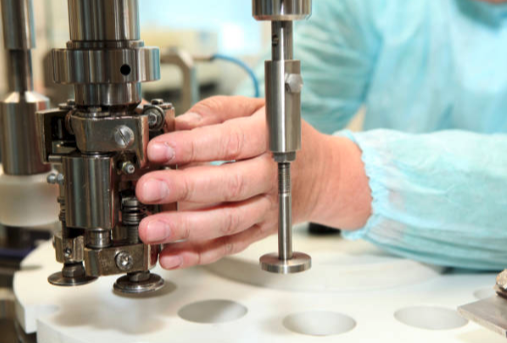
Orthopedic device manufacturing has seen considerable advancements thanks to innovative techniques in medical device injection molding. The process now allows for the creation of intricate components with unprecedented precision, such as hip and knee replacement parts, surgical screws, plates, and other implants.
The rapid prototyping convenience offered by injection molding accelerates production, offering substantial lead-time reductions. It also supports design flexibility, a critical aspect when it comes to customized orthopedic solutions to fit individual patients’ requirements.
This manufacturing method’s robustness also contributes to significant reductions in production-related risks, ensuring the high sterility necessary for orthopedic devices. New techniques such as over-molding and insert molding have further revolutionized the sector, allowing manufactures to design and deliver biomechanically superior devices that improve patient outcomes.
Impacts of Medical Device Injection Molding in Cardiovascular Care
Cardiovascular care depends on high-quality medical devices, from life-saving pacemakers to heart valves and stents. Medical device injection molding has enabled groundbreaking transformations in the cardiovascular devices industry. The ability to produce complex geometrical designs and tiny parts with precision has been crucial in producing state-of-the-art cardiovascular devices.
Due to the capability of injection molding to utilize a wide variety of materials, including biocompatible plastics and metals, device manufacturers can efficiently produce robust, flexible, and durable cardiovascular products. These properties are especially important for devices that need to withstand constant motion and resist body fluids and tissues, such as heart valves or catheters.
Moreover, the potential for high-volume production offered by injection molding techniques reduces the manufacturing cost per unit, making these crucial devices more affordable and accessible for patients globally.
Drive toward minimally invasive procedures has gained impetus from injection molding, leading to the production of smaller, more precise devices aiding quicker recovery and less surgical risk.
Medical Device Injection Molding: A Breakthrough in Ophthalmology
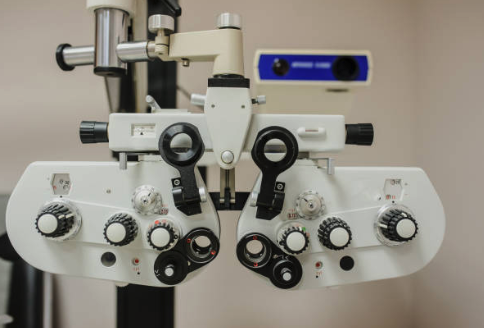
From intraocular lenses to contact lenses to various surgical tools for eye surgery, medical device injection molding has brought several breakthroughs in ophthalmology. This technique’s precise, efficient, and cost-effective nature has made it a preferred manufacturing method among ophthalmic device creators.
The ability to produce tiny, highly intricate devices with unmatched precision is crucial in ophthalmology, where intricate details can influence product performance substantially. The variety of biocompatible materials available for use in injection molding has also broadened the possibilities for device customization, enhancing patient comfort and device efficacy.
Materials Selection for Medical Device Injection Molding in Neurology Applications
Medical device injection molding is also extensively used in neurology applications, including deep brain stimulation devices, cerebral shunts, cochlear implants, and more. The injection molding process’s flexibility accommodates a variety of materials to create products that are not just biocompatible and durable but also tailored to match the specific needs of each medical application.
The choice of material is vital in neurology applications as these devices often need to interact seamlessly with sensitive neural tissues. Materials ranging from special plastics, silicone, and other special alloys are used to ensure that the devices offer the highest biocompatibility, optimal performance, and longevity.
How Medical Device Injection Molding is Revitalizing the Radiology Field
Radiology, with its diverse array of imaging devices, heavily relies on medical device injection molding. Due to its versatile nature, it is hugely advantageous in designing and manufacturing parts that are lightweight, durable, and resistant to a variety of substances. This is particularly crucial for devices like MRI machine components or parts of diagnostic imaging equipment that require strict safety and efficiency parameters.
Injection molding provides the benefit of producing large quantities of components with high precision and consistency. On top of this, the flexibility in material choice, including radiation-resistant materials, extends the life of equipment, hence bringing major cost benefits.
Exploring the Capabilities of Medical Device Injection Molding in Oncology
Medical device injection molding plays a pivotal role in oncology – a field that requires cutting-edge technology and precision. With its ability to manufacture complex parts with great precision and durability, injection molding is critical for creating oncological devices, from surgical tools to implants and port devices to radiation therapy system components.
Swift prototyping and mass production become feasible with injection molding, resulting in faster device availability and lower cost. Considering the increasing incidence of cancer globally and the great need for affordable medical solutions, this is a remarkable advantage brought by medical device injection molding in the field of oncology.
Quality and Precision: Why Medical Device Injection Molding Matters in Surgical Tools
Making medical devices, especially those that are as vital as surgical tools, requires precision and reliability. Surgical tools, expectably, leave no room for error, and their effectiveness is largely determined by their quality. Medical device injection molding has been transformative in this regard, delivering high precision along with efficient mass production.
The ability to produce complex geometrical shapes with exact repeatability, even in high volumes, is one of the critical benefits of injection molding. This technology allows reliable production of instruments with micro to macro-size scale, such as forceps, scalpels, retractors, and clamps. Plus, the sheer assortment of sterilizable and biocompatible materials available for use ensures surgical tools’ compatibility and longevity.
Transforming Diagnostics with Medical Device Injection Molding
Diagnostic devices have been experiencing diverse benefits from the usage of medical device injection molding. From simple devices like plastic disposable syringes and vials to intricate componentry in scanning devices and testing machines, this technology is instrumental. Its ability to maintain high precision levels and finish quality in parts production, regardless of the volume, enables affordable and reliable diagnostics.
Injection molding also benefits the production of Point-of-Care (POC) diagnostic devices, rendering them more accessible and affordable. POC devices made using injection-molded parts can help bring rapid, accurate diagnostics closer to patients, strengthening healthcare outcomes.
Key Benefits of Medical Device Injection Molding in the Pharmaceutical Industry
Within the complex pharmaceutical industry, medical device injection molding plays a massive role, especially in the production of drug delivery systems. Devices like inhalers, insulin pens, autoinjectors, prefilled syringes, and drug-eluting implants are often a product of this process.
The key reason injection molding is favored in this field is its capability to form highly intricate parts with accuracy, using a tide range of biocompatible and FDA-approved materials. The ability to produce these components in high volumes cost-effectively, ensuring repeatability and consistency, is crucial for the pharmaceutical industry to meet the global demand for such devices.
Pioneering Respiratory Care through Medical Device Injection Molding
Numerous respiratory care devices, from simple tools like spacers and inhalers to complex parts in ventilators or oxygenators, owe their manufacturing to medical device injection molding. Its ability to produce high precision, intricate designs has made it the go-to method for respiratory device manufacturing.
By using this technique, manufacturers can create devices that are lightweight, portable, and robust, making them user-friendly and reliable for the end-users. The use of various approved materials also ensures the devices’ durability and effective functionality across different usage and environmental conditions.
Advancements in Medical Device Injection Molding for Assistive Devices
The medical device injection molding process has significantly advanced the field of assistive devices, from hearing aids to mobility aids. This manufacturing process has bolstered the development of compact, lightweight, and complex designs that have previously been challenging to produce.
Hearing aids, for instance, demand a sizeable degree of miniaturization and precision, which is successfully achieved using micro-injection molding techniques. For mobility aids like prosthesis and orthotics, the molding process allows the creation of customized, patient-specific designs promoting a better fit and comfort.
Regulatory Challenges and Considerations in Medical Device Injection Molding
While medical device injection molding brings a plethora of benefits, it also comes with its unique array of regulatory challenges. Medical devices, such as pharmaceutical parts, medical injection casings, and test tubes, are subject to rigorous ISO standards and FDA regulations for safety, efficacy, and quality. As such, manufacturers must adhere to strict specifications throughout the design and production process to guarantee patient safety and device effectiveness.
The injection molding process, particularly plastic injection molding, must meet regulatory considerations for material selection and biocompatibility. Products made from diverse materials, like polypropylene, polyethylene, and polycarbonate, must undergo strict quality control to meet industry standards. This mechanized fabrication also has to ensure sterilization capability, production traceability, and resistance to contamination, especially when dealing with medical-grade plastics.
However, with technological advancements and quality control measures, complying with these regulations becomes significantly manageable. Enhancements in thermoplastics, improvements in mold tooling, and refinement of plastic resins all contribute to addressing these challenges, thereby streamlining the production process.
Leveraging Automation in Medical Device Injection Molding for Healthcare Solutions
Automation plays an essential role in enhancing medical injection molding efficiency. From automated CNC machines for creating the molds to robotic arms for handling plastic parts, the integration of automation technology has enabled high-speed and high-volume production without compromising accuracy or quality.
Leveraging automation in injection molding increases cost-effectiveness, repeatability, and process control, enhancing part consistency and reducing defect rates. Furthermore, automation helps meet the high demand for the medical devices like mechanical equipment enclosures, ensuring compliance with stringent quality standards and regulations.
Medical Device Injection Molding: Prosthetics and Orthotic Applications
Medical device injection molding has revolutionized prosthetics and orthotics, offering great promise for the future. This process empowers the molding of a variety of materials, including biocompatible plastics and lightweight metals like medical-grade aluminum, allowing the production of customized prosthetic and orthotic devices down to precise millimeters and microns.
The fabrication speed, along with the potential for complex design capabilities, makes injection molding a practical and economical manufacturing solution for these vital medical devices. Case studies have shown that advancements in this field are likely to bring even more exciting developments to the world of prosthetics and orthotics.
Conclusion – The Future of Medical Device Injection Molding
It’s prevalent that medical device injection molding, including plastic molding and medical injection molding, has significantly shaped the medical industry. The functional sophistication, wide material selection, and affordability make it a notably beneficial process for manufacturing various medical parts.
Medical device injection molding has redefined the possibilities, and its essential role will continue to influence the continued progress of the medical field. By facilitating the timely creation of accurate, durable, and patient-centric medical applications, this manufacturing process truly stands at the heart of many healthcare advancements we see today.
In conclusion, we can expect even further improvements as technology continues to evolve. The future likely holds greater achievements, better outcomes, and easier access to medical care through this pivotal manufacturing technology. With advancements in technology, automation, and regulations, the medical molding process is set to continue mitigating current challenges, and pushing boundaries. If you are looking for a reliable supplier for medical device injection molding, wait no further to contact Seasky Medical from clicking here.