The initial usage of plastics in medical equipment started in the early 2000s and grew throughout the following 20 years. The international market for medical plastics has grown, and by 2027, it is expected to reach a value of $37.2 billion. Due to their improved cost-effectiveness, durability, lightness, and compatibility with diverse manufacturing processes, the usage of these medical plastics is continuing to revolutionize the healthcare industry.
Many different types of medical equipment and devices, including monitoring machines, medical tubes, surgical tools, etc., are made of medical-grade plastic. Sterilization trays, imaging technology, surgical instruments, dental instruments, etc., are other medical products that are frequently made of medical-grade plastics by reliable medical part manufacturers.
What Is Medical Grade Plastics
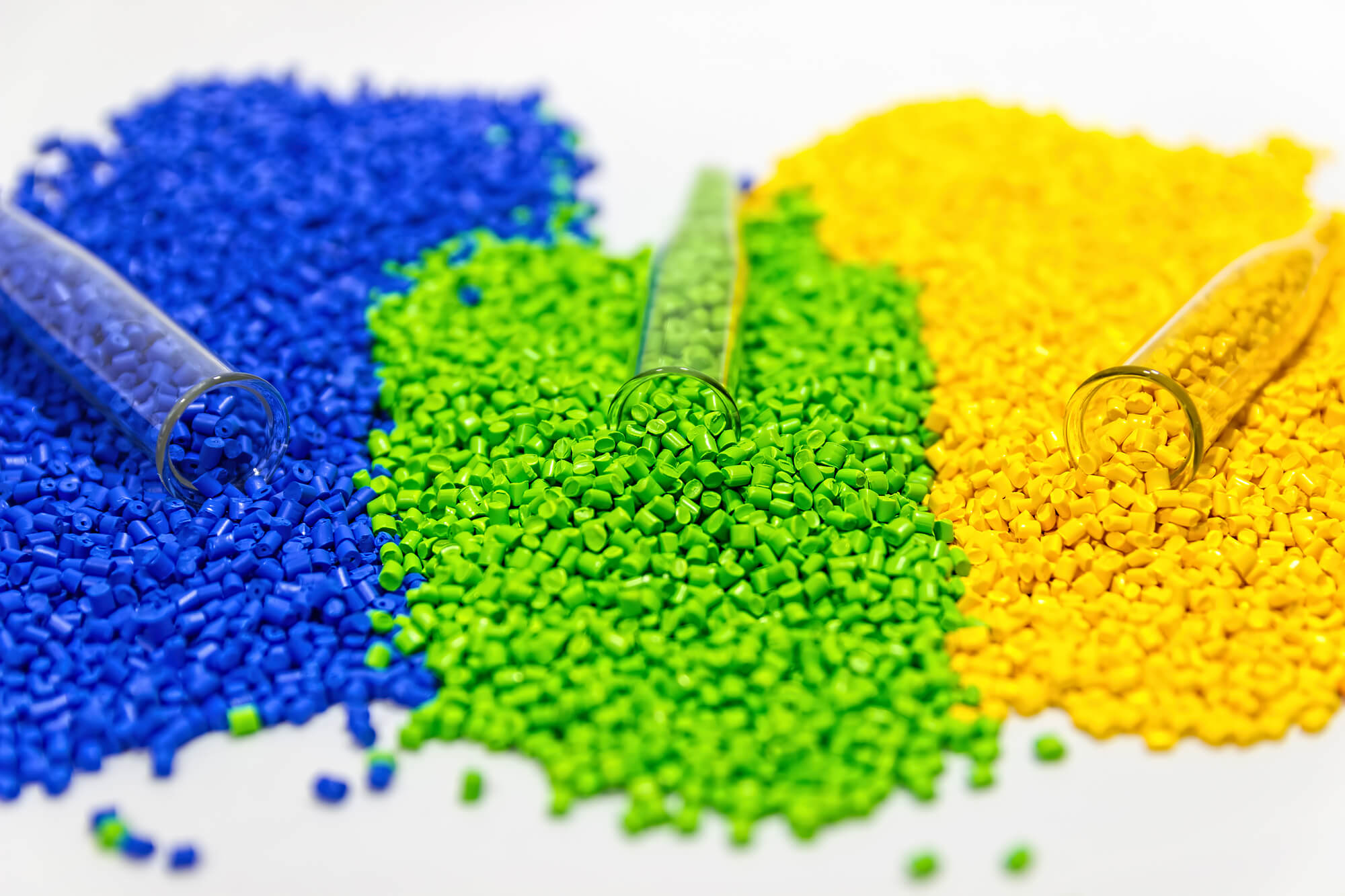
To create various sorts of medical plastic items for the healthcare sector, medical plastics are used. These polymeric polymers have developed into crucial elements of the latest healthcare system. Medical prototypes and components made of medical plastic are intended to provide enough resistance to wear, impact, temperature, and corrosion.
Temperature, chemical, and corrosion resistance are all features of medical-grade plastic. It will be able to manage repeated sterilization processes as well as any other bodily fluids or medical supplies it comes into touch with. The medical injection molding parts are typically created from thermoplastic materials to guarantee the plastic’s safety and efficacy.
Is Medical Grade Plastic Safe?
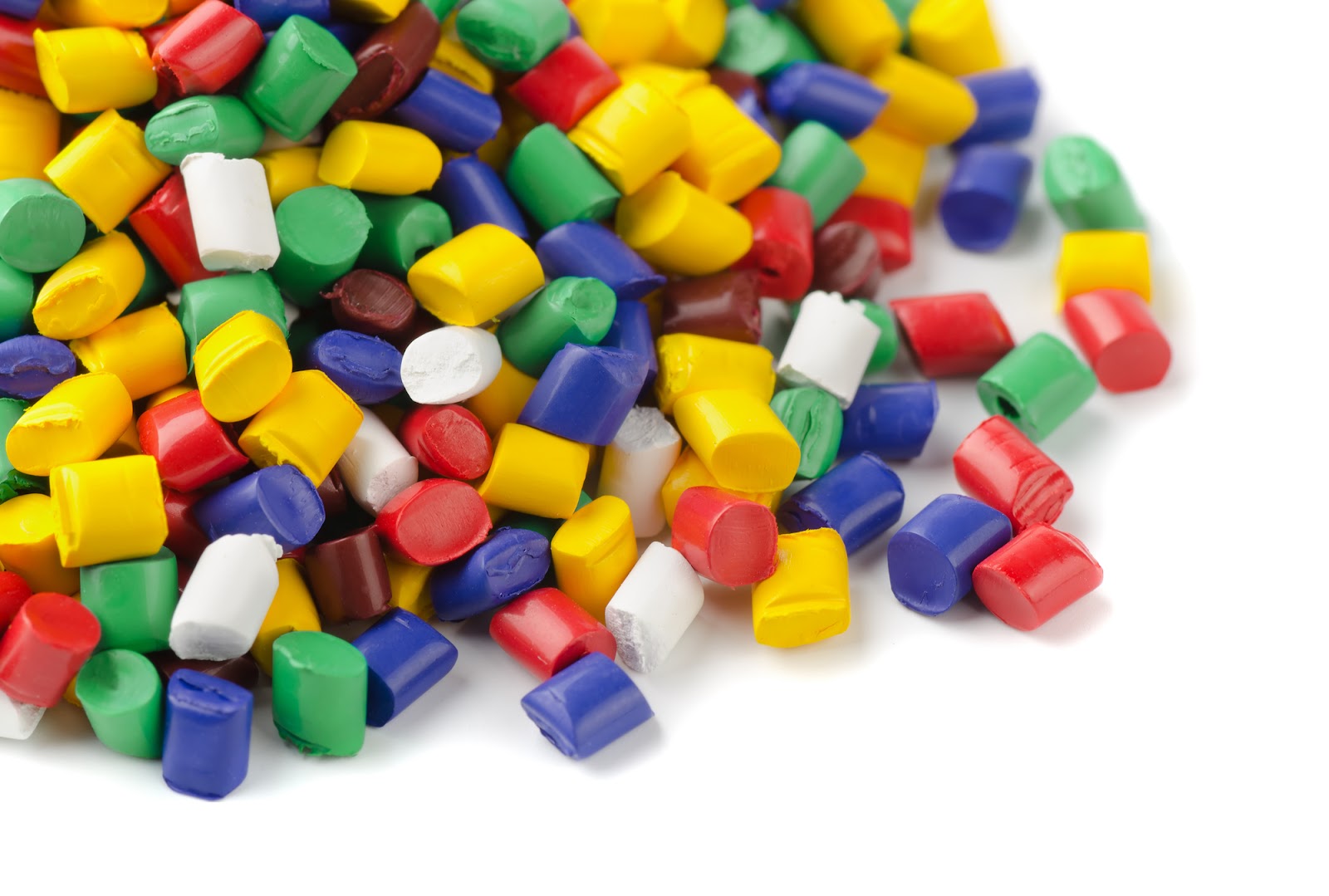
Medical-grade plastic materials are made to create sterile, secure medical items. In addition, it is utilized in the production of in vitro diagnostic devices and medicine packaging, which safeguards and contains medications to deter tampering. Chemical and heat resistance, hardness, non-permeability, and biocompatibility are safety characteristics of medical plastic.
The antibacterial traits of plastics safeguard them from microorganisms’ harmful impacts. Besides, they prevent the expansion of fungi, algae, mold, and other bacteria that can contaminate polymers and produce odors and color modifications. The structural integrity of medical-grade plastic substances allows for exceptional strength, stiffness, and resistance to impact.
These polymeric polymers deter the growth of disease-causing organisms because they are impermeable. Because of their resilience to chemicals and heat, they can be sterilized. So, devices used in transferring biohazardous chemicals are ideal to be made from medical grade polymers using medical injection molders machines.
Why Choose Plastics For Medical Devices
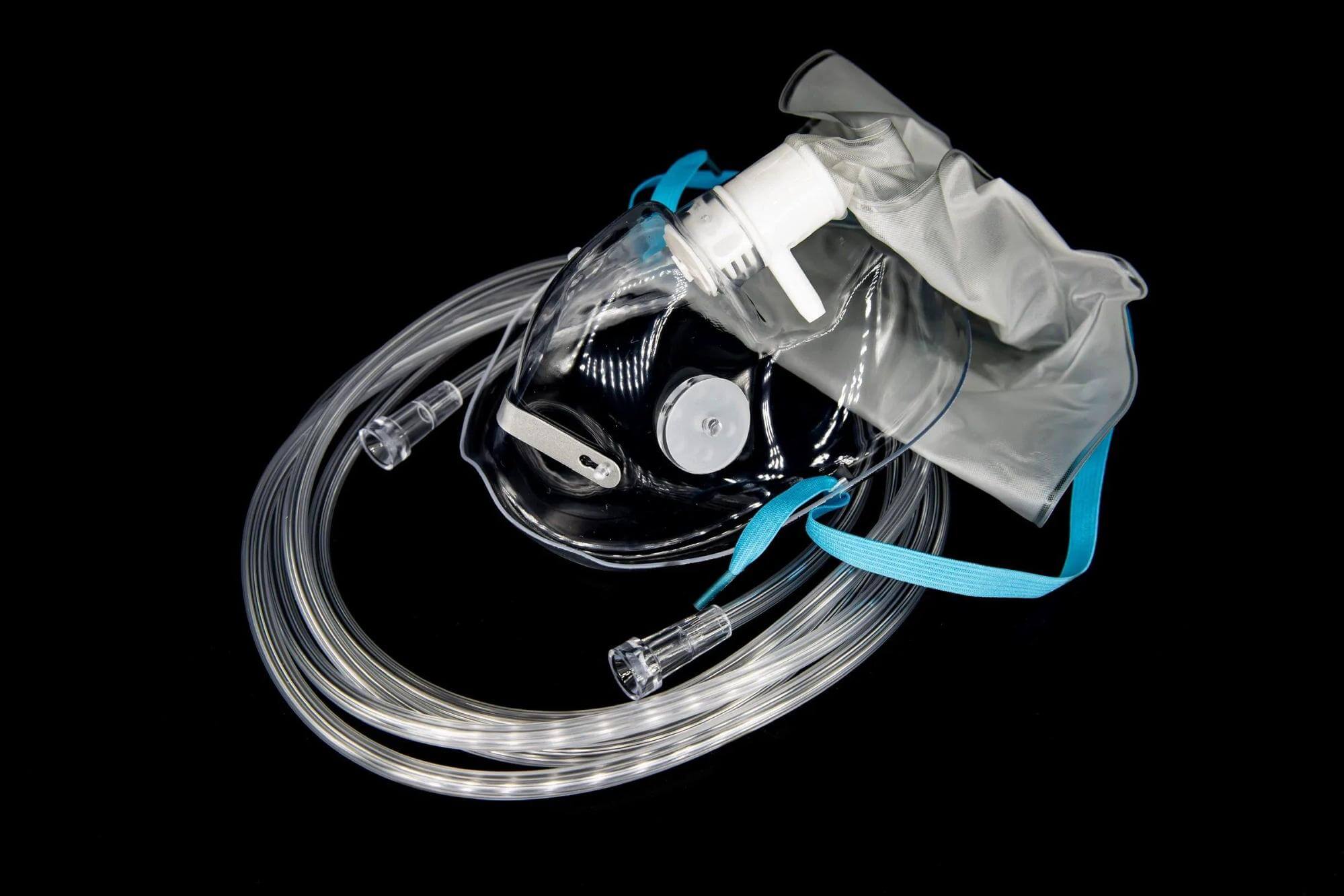
Medical-grade plastics are the perfect material for medical tools and equipment due to their distinctive properties. These materials can tolerate steady usage and multiple sterilizations because of their great temperature, wear, and corrosion resistance without malfunctioning or jeopardizing patients.
As biocompatible medical-grade plastics are chemically inert, and they do not interact with the environment of the human body. Due to that, biocompatible medical plastics can be utilized without worrying about toxicity or allergies. Implanted devices are mostly made from biocompatibility because the body would not refuse them, and the polymers would not leak dangerous chemicals into the patient’s body.
A few medical plastic polymers are far better than metals in terms of tensile strength and hardness, which is why they are preferred by medical component manufacturers. For instance, the highest tensile strength of nylon is 12400 psi. Presently, plastics are substituting metals in the production of medical device components due to their affordable cost.
Plastic polymers are resistant to chemicals, heat, and light and are highly robust. They are helpful for making medical products as they can endure repeated sterilization. Plastic has especially enhanced safety in the medical sector, where good sanitation is greatly needed. Plastic’s intrinsic sterility and inertness assist in deterring the growth of the disease.
Medical plastics can be recycled repeatedly, so they are one of the most environmentally friendly solutions for producing medical equipment. Medical-grade plastics make it more simpler for healthcare experts to make demanding medical applications and uphold environmental responsibility. So, leftover components during production can be used again, and it lowers material waste and increases cost savings.
High machinability and compatibility with a variety of production processes characterize plastic polymers. Common plastic production techniques include clean room injection moulding, blow molding, and CNC machining since they can be utilized in huge quantities without surrendering precision.
Types Of Thermoplastics In Medical Device Molding
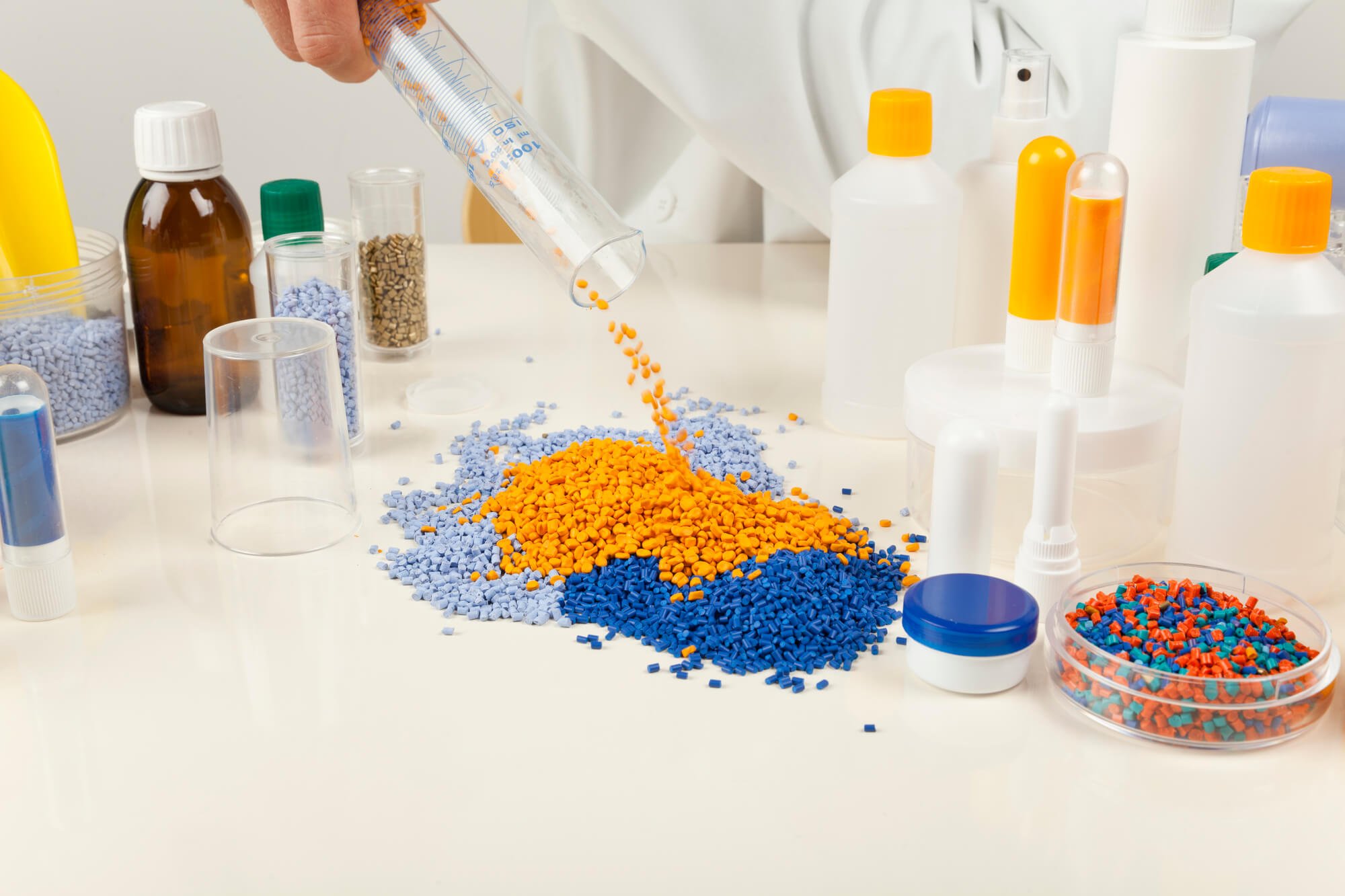
All plastics are created from distinct kinds of synthetic polymers, and there are three primary kinds of polymers, which are thermoplastics, elastomers, and thermosets. However, thermoplastics stand out from regular synthetic polymers due to their capacity of getting reheated and reshaped continuously without significant degradation.
Thermoplastics are linear or branched polymers that can be liquefied and molded utilizing several molding methods. When reheated, the plastic resin can be developed into a distinct shape. The most common types of thermoplastics used in the medical field by injection molding companies to manufacture medical devices via plastic injection molding are listed below.
- Acrylonitrile Butadiene Styrene (ABS)
ABS is often used in the production of medical devices through 3D printing. This material has heat-resistant qualities and can tolerate numerous medical sterilizing techniques, including ethylene oxide and gamma radiation. It is utilized in the production of non-absorbable sutures, tracheal tubes, tendon prosthesis, drug delivery devices, etc.
- Polyethylene
Polyethylene is an affordable kind of plastic employed in the production of surgical implants for use in medical devices. It is often known as polythene and can resist impact and corrosion, uses little water, and keeps its structural integrity through numerous sterilization procedures.
- Polypropylene
Polypropylene is a biocompatible thermoplastic with strong stress resistance, chemical, cracking, impact, and fatigue resistance. This material is utilized to make connections, disposable syringes, and finger-joint prostheses with elevated melting points.
- Polycarbonate
Polycarbonate is a thermoplastic polymer with high UV protection qualities. Medical-grade polycarbonate is fairly resistant to breaking and can endure several sterilization techniques, such as gamma radiation. This material is utilized to create medical components, including IV connectors for heart surgery and renal dialysis, etc.
- Polyvinyl Chloride
Polyvinyl chloride (PVC), which is made as a rigid or unplasticized polymer, is frequently employed in settings where sterilization is of utmost importance. Rubber is often replaced by Polyvinyl chloride because it is more affordable. This material is frequently used to create disposable medical equipment such as blood bags, heart catheters, etc.
- Polymethyl methacrylate
Methyl methacrylate is utilized to make the polymer known as polymethyl methacrylate. It is often known as acrylic glass. In addition to retaining good light transmission and a variety of color possibilities, this material is sturdy, waterproof, strong, resistant to UV light, and long-lasting. It is utilized to make endoscopic medical components due to its elevated melting point and elevated level of chemical resistance.
- Polyamide
Polyamide is a synthetic polymer that is often known as nylon. It is renowned for its durability, chemical resistance, high-temperature resilience, and stability. This material can be used to create plastic components via CNC machining, injection molding, or 3D printing.
- Polyethylene Terephthalate Glycol (PETG)
Polyethylene Terephthalate Glycol is perfect for medical applications since it would not fade when put through sterilization processes like radiation and liquid chemicals. This material is used in the production of food containers, sterilization trays, etc.
- Polystyrene (PS)
Due to the simplicity of Polystyrene in sterilizing, this plastic substance is utilized for numerous medicinal applications. Due to its optical characteristics, it can be utilized to create components for medical devices like tissue culture trays, diagnostic tools, Petri dishes, test kit cases, test tubes, etc.
10 Benefits Of High-performance Plastics For Medical Devices
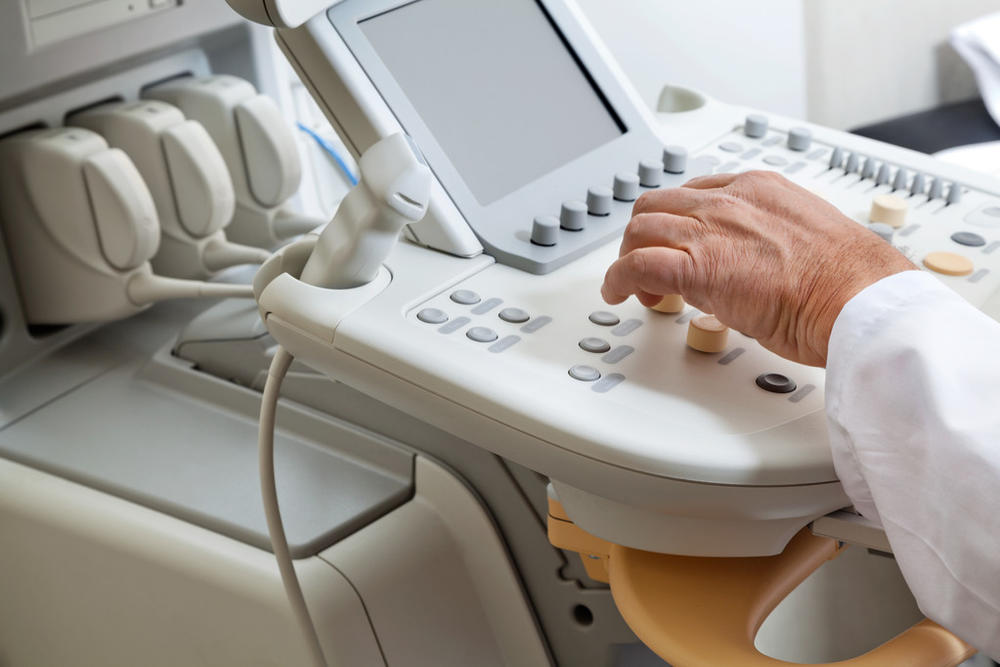
Medical-grade plastics are highly preferable in the medical field for making medical devices due to their lightweight, high-end performance, incredible properties, and low cost. Below are the top 10 advantages of high-performance plastic materials for medical devices.
- Highly Safe
Plastics can be used to make medical safety devices because of their durability. Some examples include blister packs, tamper-proof caps on medical packaging, medical waste bags, etc. For instance, non-permeable biohazard bags made of polypropylene are frequently utilized to transfer things like medical waste.
Since medical plastics are shatterproof and impermeable, it is safe to transport biohazardous chemicals in them. This promotes the safe clearance of medical waste, which stops the transmission of harmful illnesses. Tamper-proof caps are utilized for medications to guarantee that the medicines are clean and pathogen-free.
- Enhanced Sterility
Medical equipment and tools such as medical syringes, insulin pens, surgical gloves, IV tubes, inflatable splits, catheters, etc., have all been made largely of plastic. By removing the requirement to sterilize and reuse an instrument, the disposable items are designed for single use and aid in preventing the growth of harmful infections.
In addition, plastic is being utilized to make specialized contact surfaces that are resistant to germs and other microbes. Due to that, it deters the transmission of harmful infections. Besides, antimicrobial plastic can destroy bacteria and eradicate infections as well.
- Injection Resistance
Plastic has been produced by manufacturers utilizing antibacterial components that can eliminate microorganisms by up to 99%. The plastic’s surface composition can repel or kill microorganisms. It can considerably lower the likelihood of infection even if it is not washed every time. Medical plastic’s anti-infection traits aid in quickening the development of new medications by deterring cross-contamination.
- Versatile Solutions
Almost all shapes can be made out of medical plastic without any cracks using injection molding in clean room. Currently, plastic is employed to create disposable items, including breathing masks, IV tubing, bedpans, catheters, etc. In addition, plastic is also used to make internal implants such as joint replacements, pill containers, and many more. The majority of the items in the present hospital rooms are made of plastic.
- Saves Money
Plastic retains a long lifespan and can be utilized for a wide range of applications. It costs less to develop things out of plastic, which lowers the cost of production. Plastic shows resistance to corrosion and breaking, different from metal and glass. The plastics used in medical applications are made to withstand repeated sterilizations. Due to all these cost-effective benefits, hospitals are able to drastically minimize their overhead expenses, which is advantageous for both their operations and their patients.
- More Patient-friendly Solutions
Currently, producers create lightweight, strong prosthetic limbs using medical plastic and injection molding. They enhance users’ independence, movement, and capacity for everyday tasks. In addition to that, numerous medical plastic polymers are hypoallergenic. As a result, a patient who is sensitive to substances like latex is less likely to experience an adverse reaction while undergoing therapy.
- Highly Sustainable
One-use plastic tools are the best sustainable alternative to metal medical parts. Manufacturers found that the carbon footprint of one time-use equipment is negligible. Due to that, it can assist in attaining net-zero emissions. When compared to the production of metal, the medical plastic injection molding method creates the least amount of waste. In addition, this technique utilizes less energy because it requires a lower heating temperature compared to metal.
- Allows Customization
Manufacturers can easily develop affordable and pleasant medical applications due to the introduction of 3D printing machines. Prosthetics are one such medical application since they can be greatly customized because of injection molding.
- High Compatibility
Metals show less compatibility with imaging and X-ray machines than plastic injection-molded devices. Due to the X-rays’ improved penetration, they provide better bone observation. As plastics would not interfere with MRI equipment’s magnetism, they produce more precise imaging findings.
- Highly Innovative Solutions
Plastic is also utilized to create innovative medical equipment as it can be molded to meet the needs of a particular medical application. Engineers and medical innovators are developing new medical products out of the tiniest micro-molded components. As a result, plastics are increasingly being utilized in medical tools and techniques.
Applications Of Medical Device Plastic
Medical plastic polymers are put through several fabrication and screening processes before being used in the medical manufacturing field to create a variety of medical equipment and devices that adhere to quality and hygiene standards.
Plastics offer better resilience and a longer lifespan since they show high resistance to chemical, weather, physical, and environmental threats. Below are some of the common applications of medical-grade plastics in the medical industry.
- Plastic Medical Disposables
Source: Seaskymedical
There are medical disposables made of plastic that are generally used for anesthesia, general surgery, pediatric treatment, urology, gynecology, gastroenterology, etc. Some of the most common medical disposables are caps, vials, dishes, pipette tips, disposable tubes, medical syringes, etc. Healthcare experts utilize staples, sutures, and bandages to stitch injuries.
The custom IV infusion set is also made of sterile plastic with all its parts, including the IV cannula, tubing, and connectors. Plastic is also used to make disposable products for transfusion/blood management, like blood bags with a flexible drip chamber and a micron blood filter, needles, etc.
- Prosthetics
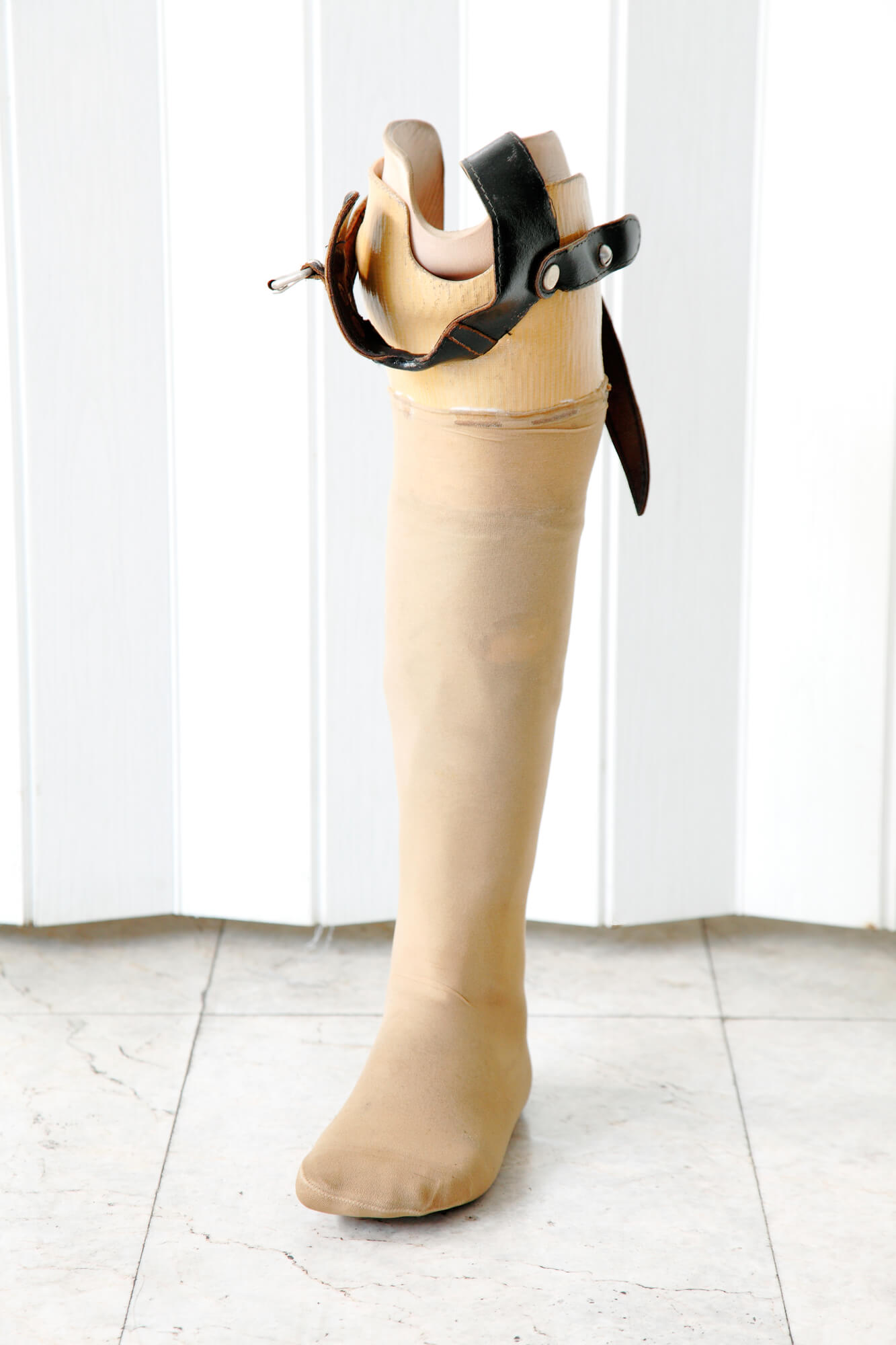
Plastics are also used to manufacture prosthetic implants, which are artificial devices that substitute a missing body part. There are prosthetic limbs, prosthetic legs, prosthetic knee implants, artificial fingers, eyes, noses, and many more. In addition, plastics are used to make knee and hip replacements, heart valves, facial augmentation implants, etc. Only flexible and lightweight plastic materials are used for custom plastic injection molding prosthetic implants to allow more movements for patients.
- Medical Devices Enclosure
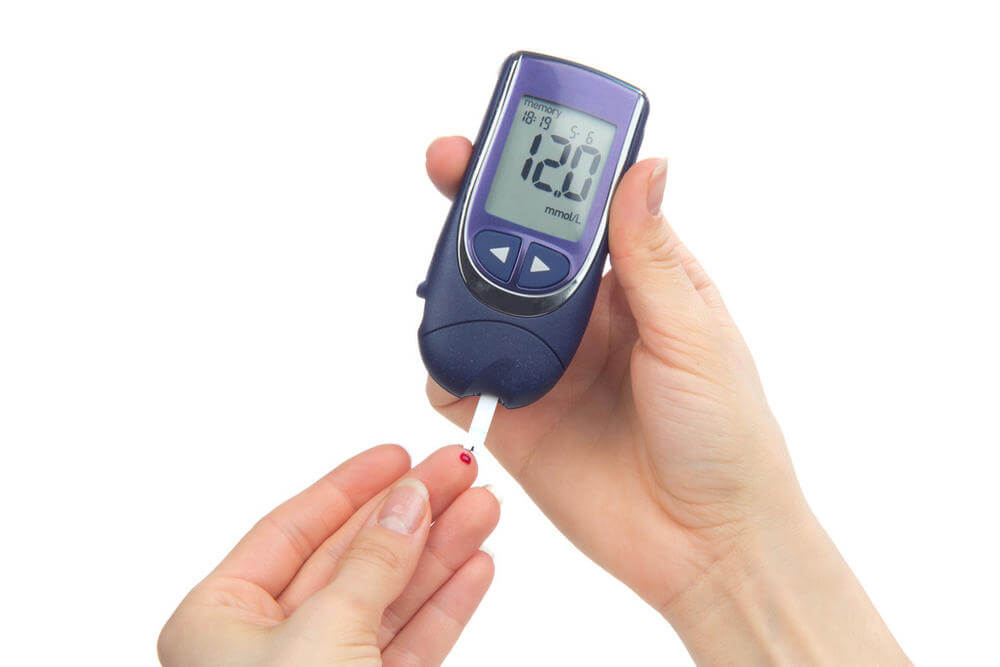
Medical-grade plastics are also known for their usage in producing various medical devices and monitoring equipment, including MRI machines, rehabilitation equipment, handheld diagnostic wands, oxygen masks, etc.
- Orthodontics
Plastic materials are also utilized for orthodontic purposes. It is because retainers, braces, and aligners are prepared using medical-grade plastic as per the patient’s specific requirements.
- Surgical Disposable Products AndSurgical Wear
Medical grade plastic is also used to make surgical disposable products such as supplemental lines, syringes, drug test disposables, 3-way stop cock, suction catheters, plastic mouthpieces, TMP Y connectors, and many more. Using sterile plastic, a wide range of plastic medical surgical wear items are manufactured to supply to the healthcare industry. Those include medical gloves, sterile masks, body gowns, scrubs, rubber theater shoes, etc.
- Packing
It is vital to safeguard products such as medicines or needles from cross-contamination, which is why medical plastic is utilized for packaging purposes. Disposables are also packed with plastic materials to eliminate contamination.
Factors To Consider When Choosing Plastics For Medical Devices
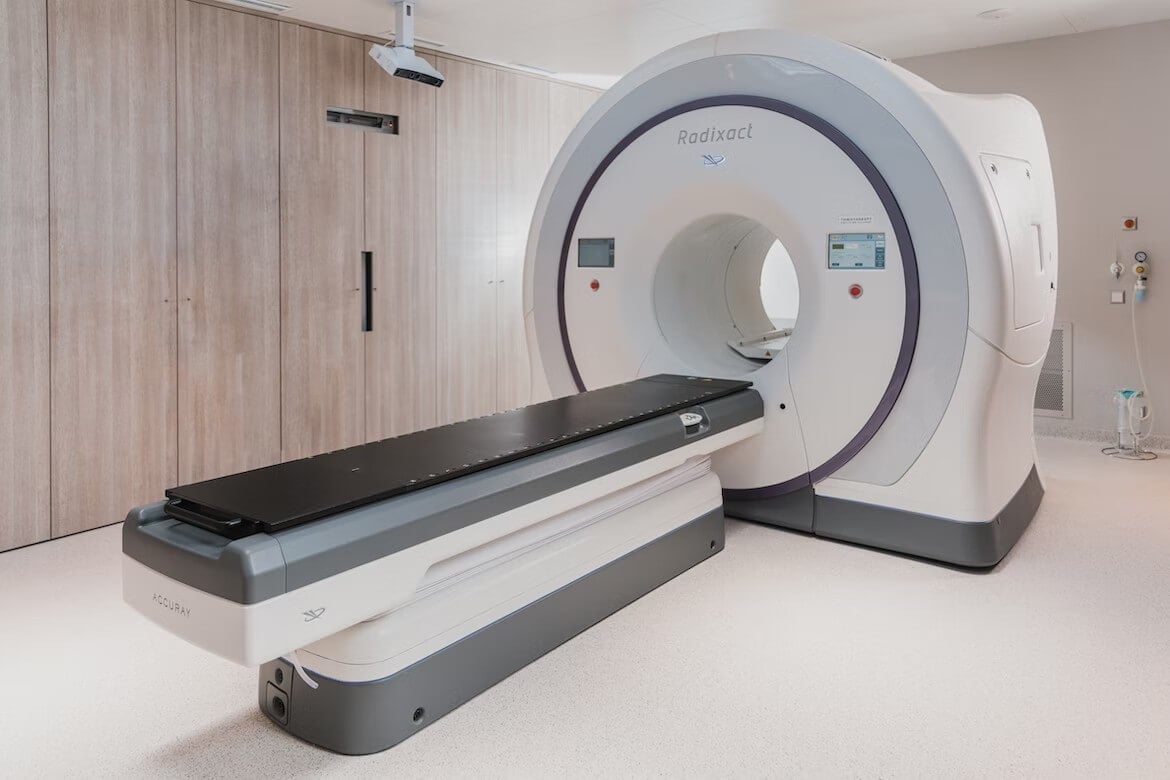
Selecting the right plastic materials for medical applications is vital to ensure the performance of the final device. Material selection for plastics utilized in medical devices is affected by the following parameters.
- Medical Device Environment
A medical device’s exposure environment must be taken into consideration when choosing the plastic material. A medical device may be exposed to a variety of circumstances, including temperature, humidity, chemicals, body fluids, body tissue, wetness, radiation, etc.
- Dimensional Stability
The medical device’s functionality can be extremely impacted by the dimensional stability of the plastics employed to make the device. Various chemicals, elevated temperatures, and surroundings can have an impact on an instrument’s material-specific physical conduct. Materials with incredible dimensional stability and tolerances are needed for most medical applications.
- Implantation Or Direct Contact
When choosing medical plastics, it is important to take into account whether the medical device will be implanted or come into touch with people directly. The medical plastic injection molding companies must make sure that an FDA-compliant, biocompatible plastic is utilized if the device will be injected or come into direct contact with people.
- Thermal And Electrical Characteristics
It is necessary to determine the properties of plastic materials under extreme environmental circumstances, such as high temperatures, humidity, sterilization temperatures, melting temperatures, etc. Electrical considerations such as insulation, conductivity, and the requirement to release stored static charge are also necessary.
Choose Biocompatible Plastics For Medical Devices
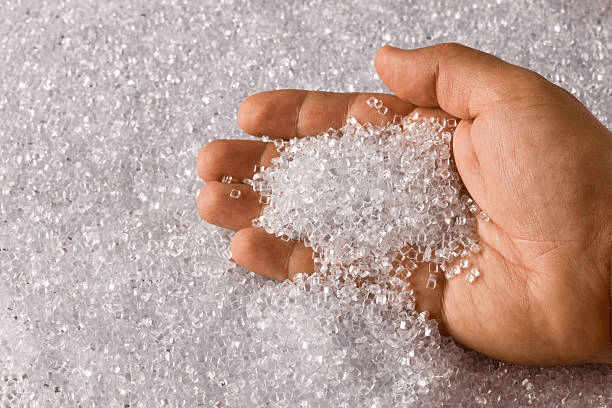
From medical tubes to complex implants, biocompatible polymers are used in a broad range of medical equipment, tools, and parts by biocompatible medical part manufacturers. Biocompatible polymers have many benefits over metal and other materials for medical device applications. Resilience, malleability, durability, optimum performance, and chemical inertness are some of the characteristics of plastics.
Materials that are biocompatible can stay for a long time in a person’s body without the risk of creating an unfavorable response. Biocompatible plastics promote healing without posing a risk of toxicity or allergic responses. Their chemical inertness prevents them from interacting with the human environment and enables the body to accept the devices without suffering negative consequences. The medical device’s biocompatibility is confirmed by ISO 10993 certification.
Medical devices are divided into surface devices, implant devices, and externally communicating devices considering the biocompatibility assessment. A wide variety of monitoring tools, catheters, endotracheal tubes, contact lenses, sigmoidoscopes, etc., are examples of surface devices. Stents, grafts, pins, plates, etc., are examples of implant devices. External communicating devices are laparoscopes, oxygenators, pacemakers, blood delivery equipment, etc.
Some of the typical biocompatible plastics used in the medical industry are Polyvinyl Chloride (PVC), Polytetrafluoroethylene (PTFE), Polyurethane (PU), Polyethersulfone (PES), Polycarbonate (PC), Polyethylene (PE-UHMW or PE-LD & HD), Polysulfone (PS), Polyetherimide, Polypropylene (PP), and Polyetheretherketone (PEEK). Biocompatible plastic devices can be classified by the total duration they stay in direct touch with the person’s body: non-contact, short-term contact, and long-term contact.
The non-contact devices are made of PA, PS, PVC, PE, and Epoxy resins, which are glucose bag drips, blood storage bags, and syringes. The short-term contact devices like surgical instruments, feeding tubes, and drainage tubes are made of Nylon, Polyester, PEEK, Teflon, PE, PeBax, and Polyphenylsulfone. The long-term contact devices include implants and drug delivery devices that are made from Polyphosphaszenes, PE, Polysulphones, PMMA, UHMWPE, Hydrogels, Polydimethylsiloxane, etc.
SeaskyMedical – A Proper Medical Injection Molding Company
SeaskyMedical is a 20+ year experienced medical injection molding company. From plastic medical disposables to medical equipment and laboratory consumables, we manufacture a variety of low-risk and sterile plastic medical solutions. We are an ISO-certified manufacturer with a massive ISO 8 cleanroom and a huge production area with the 10 latest medical injection molding machines.
At SeaskyMedical, ISO 13485:2016 quality management is rigorously followed, and we source premium raw materials and offer ISO10993 biocompatibility reports. There are a broad variety of high-quality plastic materials ideal for various plastic medical applications. Our experts also deliver plastic medical device customization options to provide better solutions.
We offer plastic medical product development, mold designing, mold tooling, and medical part sample services. Contact SeaskyMedical to order medical product solutions in bulk quantities for a reasonable price. We supply medical injection plastic molding solutions to worldwide healthcare facilities.