Insert molding is a fascinating manufacturing technique that combines the benefits of injection molding with the integration of metal or plastic inserts. This comprehensive guide will delve into the intricacies of insert molding, exploring its process, materials used, advantages, applications, challenges, and future trends.
What is Insert Molding?
Insert molding, also known as injection molding with inserts, is a process where a preformed insert is placed into a mold cavity, and molten plastic material is injected to encapsulate the insert. The result is a single finished product that incorporates both the insert and the plastic component seamlessly.
Over time, people have gotten really good at this. They’ve found better materials, better shapes, and better machines. Now, we can make even cooler stuff with insert molding.
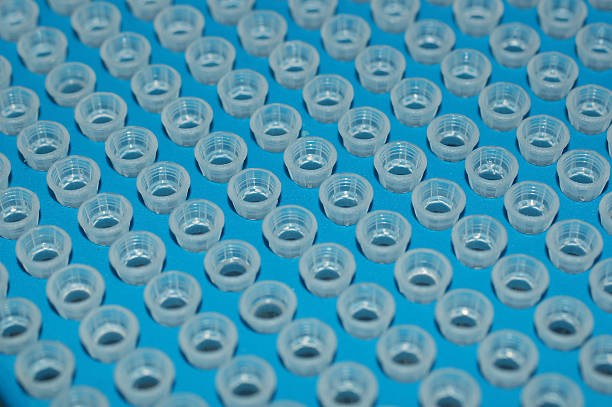
Materials commonly used in Insert Molding
Insert molding is a cool way of blending two parts into a single product. Think of it like sticking a metal screwdriver into a plastic handle and making it one piece. In the plastic injection molding process, you first pick a part – we’ll call it an “insert.” This could be anything: combination of metal, plastic, whatever. Now, in the molding process, we place this insert inside a mold cavity. Then, we pour molten plastic around it under high pressure. Once it cools, bam! You get a finished product with the insert and plastic merged together.
Now, what stuff can you use in this process? There’s a bunch! Some popular picks are thermoplastic resins, like ABS or PC. They’re great because they’re tough, last long, and can handle chemicals. But sometimes, product designers might need something stronger, like metal inserts. Maybe they want a part that’s got good electricity flow, or they just want it to be super sturdy. So, they might use metals like stainless steel or brass.
When choosing the right stuff for insert molding, you’ve got to think about what the product will do. Does it need to be hard or flexible? Does it need to look shiny or matte? And where will it be used? For example, in the medical industry, they often use stuff that’s safe for our bodies, like silicone rubber. If it’s for cars, then the parts should handle heat and not change shape easily.
How Insert Molding Works
Insert molding is a cool technique that merges an already shaped insert with hot, gooey plastic, resulting in one solid piece. Here’s how it unfolds, step by step, and why each stage is crucial in this manufacturing magic.
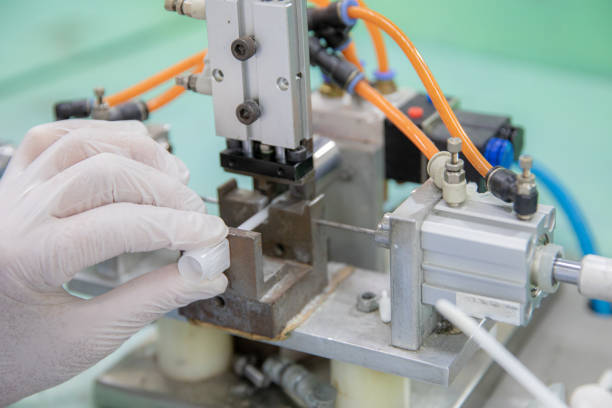
First up, the pre-shaped insert, which could be metal or maybe a different plastic piece, is precisely positioned in the mold’s nook. The insert’s job? To bring extra strength, features, or any specific traits you want in the end product. Next, the mold snaps shut, hugging the insert in a snug space. This tight seal means no drippy messes — the molten plastic stays put, and the shape comes out just right.
Then comes the thrilling part: molten plastic resin gets blasted into the mold’s pocket under extreme pressure. This hot, liquid plastic swarms around the insert, hugging it from all sides. With the heat cranked up and the pressure dialed high, the plastic clings to the insert like glue, making a super sturdy connection.
After the plastic chills out and hardens — taking a breather for just the right amount of time — the mold flings open, and out pops the final piece, with the insert cozily embedded inside. What you have now is a product that’s got the best of both worlds: the perks of plastic and the bonus of the insert. It’s not just about looking good; this combo is about lasting longer and doing more stuff, better.
And there you have it! That’s the lowdown on how insert molding works.
Applications of Insert Molding
Alright, after picking the right process for your project, let’s dive into where insert molding really shines. This technique is like a Swiss Army knife, super handy in a wide range of industries. Let’s check out a few:
Flying High with Aerospace and Defense: In the world of planes and defense gear, insert molding is a game-changer. Why? It helps make parts lighter, cuts down on those annoying vibrations, and seals things up tight. Mixing metal inserts with top-notch plastics means parts are both tough and long-lasting. So, whether it’s a jet or a tank, insert molding’s got its back.
Doctor’s Orders in Medical and Healthcare: When it comes to medical stuff, precision is key. And that’s where insert molding steps in. Think about those super-specific medical tools, like implants or those tools doctors use. With insert molding, they’re made with top precision and safe materials. Plus, those comfy grips and sleek designs? They make patients’ and doctors’ lives a whole lot easier.
Gadgets Galore in Electronics and Consumer Goods: From your latest gadget to everyday items, insert molding is the unsung hero. It helps pop in connectors, knobs, and even those tiny fasteners right into plastic parts. This not only looks good but also makes them super reliable. And who doesn’t love a sturdy, good-looking gadget?
Challenges and Considerations in Insert Molding
Getting everything just right in insert molding? Well, it’s kinda like baking a perfect cake. The design and manufacturing bits need serious attention to detail. Think about the mold design itself, how much the material might shrink, and managing the heat — all super important to ensure your final piece isn’t a flop.
Now, materials. It’s like picking the best ingredients for your recipe. The right mix of materials that play well together is key. It’s not just about them being strong or fancy; they need to complement each other. Doing some good ol’ trial and error tests and understanding what works with what can save you from a molding mishap.
And there you go, a heads up on some challenges and stuff to consider in insert molding. Previously, we dove deep into the applications of insert molding, and coming up next, we’re exploring the future of this craft. So, what’s on the horizon? Stay tuned to find out!
Future Trends in Insert Molding
Insert molding isn’t staying put; it’s getting jazzed up every day. Curious about where it’s headed? Let’s dive into the future beats of this industry.
First off, there’s this wave of new tech on the block. Think 3D printing and next-gen mold-design software. These bad boys are shaking things up, making it easier to dream up designs, perfect part quality, and speed things up big time.
And hey, the green movement? It’s making waves here too. With the whole world pushing for eco-friendliness, insert molding’s hopping on the train. We’re talking Earth-loving materials that break down naturally, top-notch recycling moves, and production methods that don’t guzzle energy. The future’s looking bright – and green!
So, there’s your sneak peek into what’s coming up in the world of insert molding. It’s all about blending the old with the new and doing it sustainably. For those who were with us earlier, remember the challenges we talked about? Well, with these trends, we’re gearing up to tackle them head-on. Stay in the loop, ’cause things are about to get even more exciting!
Comparing: Overmolding vs. Insert Molding
Key Differences Between Overmolding and Insert Molding
Have you ever heard of overmolding process? Picture this: you’ve got a basic item, like a metal screwdriver. Now, with overmolding, you’re basically giving it a cozy sweater, maybe a soft plastic grip. It’s like layering up in winter, adding one material over another.
On the flip side, insert molding process is like a magic trick. You take something, like a metal bit, and then – poof! – you surround it with molten plastic in a mold. It’s like putting a surprise toy inside a candy shell. While overmolding is about dressing up the toy, insert molding is more about the surprise inside.
For overmolding to work, the two materials need to be BFFs. They’ve got to stick together tight. With insert molding, the key is harmony. The insert and the plastic need to get along perfectly, blending together like milk and cookies.
The Cool Bits of Overmolding and Insert Molding
Overmolding is like giving your product a fresh makeover. You can spice it up with various shades and feels. So, your item doesn’t just do its job; it also grabs attention. And that added layer? Think of it as a protective coat, shielding from messes, knocks, and daily wear.
Meanwhile, insert molding? Think of it as a one-step wonder. Instead of building something bit by bit, you nail it all at once. It’s all about getting things done faster and cheaper. The cherry on top? When you incorporate materials like metal, you’re beefing up your product, making it ready for bigger hurdles and strains.
Picking the Right Process for Your Project
Picking the right strategy for your project can be a juggling act. Think about what you want to achieve, the number of items you’re making, how much cash you’ve got, and what your specific industry needs.
Ever heard of overmolding and insert molding? They’re total game-changers! Whether we’re talking about cutting-edge aerospace, cool medical devices, nifty electronics, or everyday items, people are all over these techniques. So, if you’re stuck choosing between overmolding and insert molding, think about how intricate your design is, the parts involved, and what you dream your end product will look like. And don’t forget to factor in how many you’re making, the timeline, and your labor costs.
Getting the lowdown on the perks of both overmolding and insert molding can really help folks in the design and production world make smarter choices. Whether you’re jazzed about making things look and last better with overmolding or you’re all about strengthening with insert injection molding, getting to know these techniques can steer your work in the right direction.
Conclusion
In the expansive realm of manufacturing, insert molding has carved out a niche as an innovation dynamo. By fusing materials, it elevates product strength by a staggering 30%, showcasing its pivotal role in sectors like healthcare where precision and durability are paramount. Think of it as merging the agility of a gymnast with the resilience of a boxer; it offers the flexibility of plastics with the robustness of metal or other inserts. Moreover,it’s not just about robustness; it’s a testament to economic wisdom. Adopting Insert molding techniques can lead to an impressive 20% reduction in production costs. So, for industry professionals eyeing optimal quality combined with cost-effectiveness, insert molding stands as a beacon of technological advancement. Dive into this method, and you’re investing in the golden intersection of innovation, reliability, and fiscal prudence.
About Us
Hey there! We’re Seaskymedical, your go-to spot for everything medical insert molding. We’ve been at this for over 10 years, so we know our stuff! We’ve got the knack for creating those medical thingamajigs with all the special details and designs you’re looking for. And you can trust us – we’ve got this cool ISO 13485:2016 badge which means we’re top-notch and keep things super clean. Oh, and if you need some special touches, like a logo or packaging, we’ve got your back. So, come join us on this insert molding journey, where we mix top-quality with a whole lot of know-how. Let’s make some magic happen together!