Casting and molding, in terms of definition, are sophisticated techniques for creating models that are employed by manufacturing companies to develop their products. Though the processes are similar, casting is more widely used to create metallic molds, whereas molding is the preferred method for making plastic molds.
On the other hand, manufacturers should be aware of the subtle variations between casting and molding so that they may make the best decision possible based on the sort of material they will be producing.
Here’s a breakdown of the distinctions between casting and molding to help you understand what they are and how to pick between the two:
What Is Die Casting?
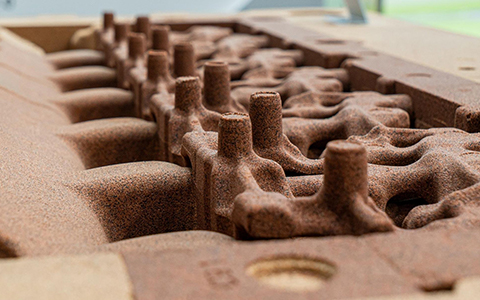
Die casting is a metal casting process that includes pouring hot liquid metal into a mold and subjecting it to high pressure and filling speed. Die casting molds, unlike other molding procedures, are designed to be used for a much more extended period of time. In contrast to sand casting molds, die casting molds are neither destroyed nor thrown away after use.
The mold cavity comprises two hardened tool steel dies that have been machined into form and function in the same way as an injection mold.
Non-ferrous metals, such as zinc, copper, aluminum, magnesium, lead, pewter, and tin-based alloys, are used in most die castings.
There are two forms of die casting: hot and cold casting.
Hot chamber die casting melts metals in the casting machine, whereas cold chamber die casting heats metal in a furnace and transfers the molten metal to the casting machine. With minimum additional tooling and shaping, the method generates complicated structures with tight tolerances, heat resistance, and high tensile strength.
Hot chamber die casting employs low-melting-temperature metal alloys, whereas cold chamber die casting uses high-melting-temperature metal alloys.
What Is Vacuum Casting?
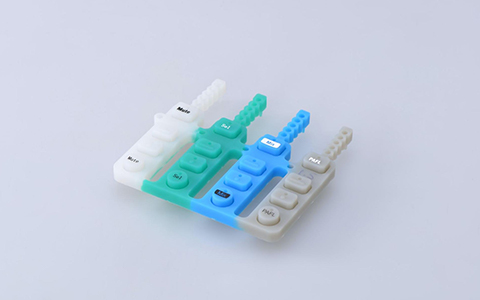
Vacuum Casting is a casting procedure that uses a vacuum to suck a liquid material into a silicone mold to produce complex components. Elastomers like plastic and rubber are employed as liquid materials in vacuum casting.
Because polyurethane resin, a form of elastomer, is utilized as the casting material, vacuum casting is also known as polyurethane casting or urethane casting. Vacuum casting is a cost-effective alternative to injection molding for producing plastic components since the production costs are reduced.
Vacuum casting is an efficacious manufacturing method for batch production and low-volume projects. Vacuum casting is widely utilized in the manufacturing of FMCG and consumer goods, as well as industrial electronics.
What Is Injection Molding?
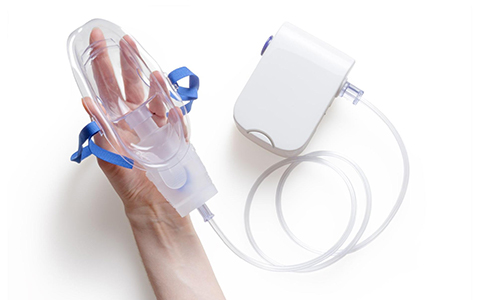
Injection molding is a molding process for producing identical plastic parts in large quantities with tight tolerances. Thermoplastic polymers that can be dyed or filled with various additives are utilized in injection molding.
Injection molding is used to make everyday plastics like vehicle parts, electronics, and household appliances, among other things.
Because of the substantially reduced cost per unit when producing large numbers, injection molding is one of the most popular and favored options. Injection molding has a high degree of repeatability and allows for a lot of design flexibility.
Injection molding is done with a piece of unique equipment that consists of three parts: an injection unit, a mold, and a clamp.
Injection molding is typically utilized when thousands or millions of identical parts must be produced from a single mold.
Difference Between Casting and Moulding
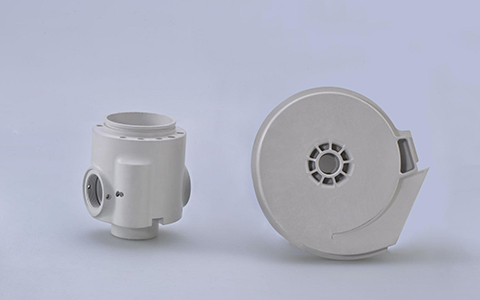
The critical distinction between casting and molding, as previously stated, is the type of materials used. Metals are used in casting, while plastics are used in molding. But the variances don’t end there; there are several other significant distinctions between the two molding techniques:
Molding
In molding, a liquid material is injected into a metal, transforming the injected material into a mold. The many types of molding are as follows:
Thin Wall Molding
The goal of this technique is to make the part’s wall as thin as possible in order to make it lighter and more flexible. The width of the wall is usually less than.025 of an inch.
Gas-assisted Injection Molding
Materials can shift during injection molding, resulting in deformed end products. The developer can use gas-assisted injection to blast a hole or hollow point into the mold and ensure that it does not distort as it cools.
3D Printing
While it is a distinct category, 3D printing is a sort of injection molding that is commonly utilized in prototyping due to its low cost and widespread availability.
Another distinguishing feature of molding is that it is actually faster than casting and may be employed in the mass manufacturing of molds for nearly any material.
Casting
Casting is equivalent to molding in terms of process. The liquid metal that will be used to make a mold is poured into a silicone rubber or similar material shape. There are two sorts of casting processes that everyone should be aware of:
- Hot chamber die casting
- Cold chamber die casting
Hot Chamber Die Casting.
The material is heated within the casting chamber, which is why it’s called a “hot chamber.” Instead of heating the metal someplace else, it is melted and formed in the exact location, which is why hot chamber casting is so popular.
Cold Chamber Die Casting.
Cold chamber die casting entails first liquefying the metal and then funneling it into the die through a cold chamber. For metals with high melting points, cold chamber casting is frequently recommended.
For manufacturers seeking long-lasting, high-quality molds, casting is the favored option. Casting allows for more design complexity and is perfect for creating multiple elaborate, dissimilar designs simultaneously.
Die Casting vs Injection Molding: Process
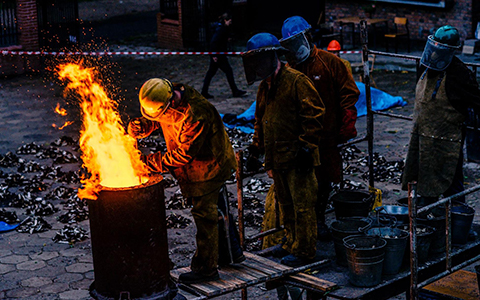
If you want to learn more about casting and molding, you’ll need to know how the procedure is carried out in detail, and the difference between die and mould.
Here is a step by step procedure that details the intricate process of both casting and molding:
Process: Steps Involved in Die Casting
Die casting is also referred to as high-pressure die casting because of the tremendous pressure involved in the process. This procedure is broken down into four distinct parts.
Step 1: Die Preparation
Using a lubricant, spray the mold cavity. Lubrication helps to regulate the temperature inside the die and makes the die-casting process easier. The die is ready to use after lubrication. Remove the mold from the oven.
Step 2: Filling
Molten metal is pumped into the die under high pressure once the mold is closed. As the liquid metal rapidly cools and becomes the shape of the die, the high-pressure situation is maintained.
Step 3: Cooling
To speed up the cooling process, submerge in (or spray with) water.
Step 4: Ejection
Open the dies to eject and retrieve each shot once the mold has cooled. Castings are not the same as shots. A die can have many mold cavities. Individual castings emerge from each cavity. Shots are all the castings that come from a mold cavity.
Process: Steps Involved in Injection molding
The steps for manufacturing plastic parts using the injection molding technique are outlined below.
Step 1: Mold Preparation
Lubricate the mold before starting the injection molding process. Apply a suitable lubricant to the mold. Mold lubrication helps regulate the temperature inside the mold and enables simple product ejection after molding.
Step 2: Filling
High-pressure injection of liquefied plastic compounds into aluminum molds. As the molten plastic cools and takes the shape of the mold, maintain the high-pressure conditions of the mold.
Step 3: Cooling
Spray or soak the mold in water to speed up the cooling process.
Step 4: Ejection
Before opening, make sure the mold has cooled down a bit. After you’ve finished injecting, eject and collect your product. If necessary, the manufacturer can perform additional processing processes, such as finishing.
Die Casting vs. Injection Molding: Precision and Tolerances
Below are some key points of difference between molding and casting.
Precision
Product tolerance is critical in injection molding when dealing with micro products or parts. Injection molding especially micro injection mold is sufficient for producing high-precision components. Die casting or other production methods could also achieve it, such as machining, instead.
Tolerance
The tolerance of the part produced is determined by the metal alloy used in die casting. There is a standard tolerance grade for each metal. Size and usefulness are essential considerations that influence tolerance levels. On the other hand, Die-cast materials have a high tolerance and are extremely precise.
Taking medical moulded products for example, injection molding technology like medical insert molding offer a higher level of precision and tolerance. Tighter tolerances usually result in higher precision products, which provides great convenience for the medical injection molding industry. While Die Casting plays a greater role in metal products.
Differences in Used Materials
Source: Unsplash
Materials used in casting and molding are the ones that explicitly differentiate both processes. Now for more clarity, let’s look into the different types of materials used in die casting and injection molding:
Die Casting Materials
Die casting is a manufacturing method that involves pouring or squeezing molten metal into steel molds. The dies or molds used for this are made to last with the various utilized materials.
Aluminum, zinc, and magnesium are some alloys that are mostly used in die casting.
Along with that, copper alloys like Yellow brass, manganese bronzes, silicon brass, alloys like C85800, C86200, C86500, C87800, and special die casting alloys like C99750 and C99700 are also some of the die casting materials used.
Injection molding materials
Injection molding is a fundamental approach to thermoplastic production. While there are several common plastics that can be used for injection molding, material selection is tricky. But professional modling company could provide you with the most professional injection molding materials selection guide.
Nylon, High-Density Polyethylene (HDPE), Low-Density Polyethylene (LDPE), Polycarbonate (PC), Polyoxymethylene (POM), Acrylic Poly (Methyl Methacrylate), Thermoplastic Polyurethane (TPU), Thermoplastic Rubber (TPR), Polypropylene (PP) are some of the materials used in injection molding.
Difference in Prototyping
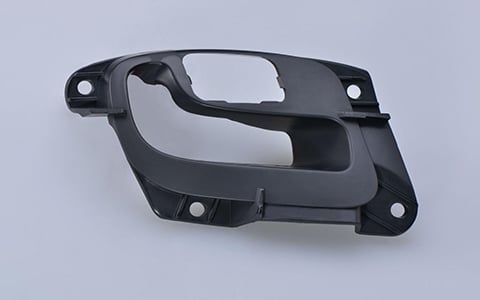
Prototyping is a method of creating a rough or sample model of a mold so that the mold manufacturer may discuss accuracies, designs, defects, and other details with users and designers.
Die Casting Prototypes
Most manufacturers provide the following types of prototypes for customers to analyze and confirm the model in die casting. They are:
Investment Casting
Investment casting entails creating an identical reproduction of the model you’ve requested. The appearance, correctness, and design are all comparable to the final product.
Spin Casting
Spin casting is the procedure to use if you need a prototype for a product with complex, accurate geometries quickly. For small items with elaborate wall designs, spin casting provides the best return on investment.
Machined from Solid
Solid prototypes are prototypes with die casting designs that are similar to earlier models. This prototype is designed for customers that need a quick model to help them make a decision.
Injection Molding Prototypes
When it comes to prototype injection molding, a common practice in the manufacturing business is to employ 3D printed parts for prototypes, test them, and then move on to production molds. This process may generate less than ideal outcomes because of the constraints of 3D printing, such as the limited plastic materials accessible compared to injection molding. In many circumstances, however, injection molded plastic prototypes are required to test plastic material features properly.
Differences Between Injection Molding and Die Casting: Applications
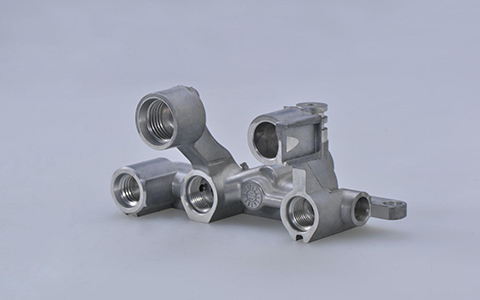
Whether you want casting or molding, it entirely depends on the products you want to get manufactured. Here are some typical injection molding and die casting applications.
Injection Molding Applications
Because of its high output rate and consistency of quality, injection molding is the ideal production process for most mass-produced plastic products. The following plastic items are items that you will frequently encounter in your daily lives:
- Automotive parts: dashboards, bumpers, grilles.
- Electronic components: electrical connectors, enclosures, protective sleeving.
- Medical device molding: syringes, valves, dishes.
- Consumer plastics: mobile phone cases, bottle caps, toys.
- Furniture parts: seat cushions, chairs, seat covers.
Die casting Applications
Die casting is the preferred process for making more durable items such as metals and other metal alloys. Die casting is used to create a variety of daily items, including the following:
- Health Care: ultrasound systems, pacemakers, dialysis equipment, medical robots, monitoring devices.
- Culinary: stainless steel and cast-iron pans, skillets, and ovens.
- Mining: excavators, drills, draglines, crushers.
- Energy: drilling machinery, valves, flow controls, filtration devices, impellers.
- Construction: window frames, roof superstructures, and building frames.
Casting vs. Molding:Surface Finishing Options
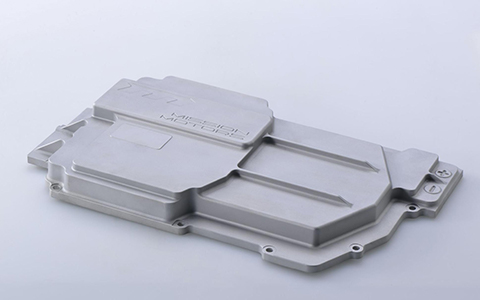
When production is completed, the manufactured parts will be subjected to various finishing processes. This is the final step in the process of both casting and molding.
High-quality surface finishes are necessary for:
- Decorative finish
- Protection against environmental exposure
- Abrasion resistance
- Galvanic corrosion protection
Casting and molding have distinct surface finishing possibilities, so let’s take a look at the varied surface finishing alternatives supplied by casting and molding.
Casting Surface Finishing Options
The aesthetic and performance of die castings are affected by surface finishing. Specific characteristics like as parting lines, ejector pins, and gates are taken into account early in the design phase when our team collaborates with you to assess your needs and select the most effective finishing applications from a variety of possibilities.
Some of Casting Surface finishing processes are:
- Glass bead blasting
- Burnishing
- Vibratory Deburring
- Sanding
- Polishing
- Graining
- Buffing
- Silk Screening
- Painting
- Powder coating
- Laser engraving
- Plating
- Anodizing
- Ceramic Coating
Molding Surface Finishing Options
Injection molding is a valuable method for producing plastic components. This method is quick and inexpensive, and it allows for the production of large quantities of similar things. The natural surface smoothness of molded objects is one of the most fundamental advantages of injection molding. Molded products have smooth surface finishes suitable for numerous end uses even without any injection molding surface finish or post-processing treatment.
Despite the fact that molded parts from injection molding have a tidy surface finish by default, you still have a variety of surface finishing options to pick from.
Certain companies will need exceptionally smooth plastic surface finish types for aesthetic purposes. Others may want a high level of roughness or a glossy malleable texture to prolong the longevity of a component.
The following are some of the surface finishing options for moldings:
- Glossy
- Semi-glossy
- Matte
- Textured
Casting vs. Molding: The Advantage
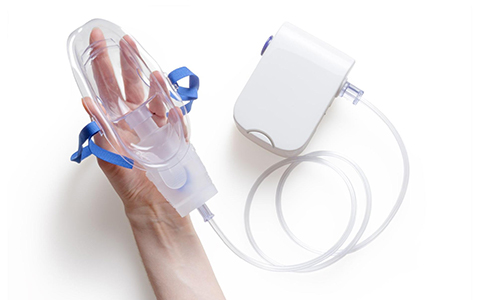
As peculiar and important casting and molding are in producing molds for a various purposes for different industries, they sure come with their own set of advantages, which is worth knowing as a consumer before you invest in one:
Advantages of Molding
- In injection molding, mass production can be done in a limited time.
- Labor costs are lower compared to other processes.
- Multiple designs and variety of colors can be used.
- Usually, all of the parts are identical, so all the parts will usually be consistent.
- Because of the versatility of plastic injection molding, types of equipment can manufacture even the tiniest of parts with as little post-production as possible.
Advantages of Casting
- Die casting allows for more intricate shapes to be produced with tighter tolerances than many other mass-production methods.
- Die castings are mass-produced at a high rate. There is little to no machining required.
- Die casting produces parts that are long-lasting, dimensionally stable, and have a high-end feel and look.
- Before additional equipment is necessary, die casting dies can manufacture thousands of identical castings within specified tolerances.
- Die cast surfaces are smoother than most other casting methods, including sand, permanent mold, and investment casting.
- Die castings include integrated fastening components like bosses and studs, which can save time and money during assembly.
Casting vs. Molding: The Disadvantage
As advantageous and distinctive as they are, casting and molding have a number of drawbacks. The downsides, however, are not related to product quality but rather to minor details such as turnaround time and expenses.
Molding
- May necessitate a significant upfront investment in tooling and machinery.
- When it comes to plastic injection molding, there are few restrictions.
- Not economical for low production volumes.
Casting
- Casting is not recommended for metals and alloys with high melting points.
- Large pieces are harder to cast.
- Die costs are pretty high.
- There is an excessively long lead period.
- Some gasses could be trapped in porosity.
Casting vs. Molding: Tooling and Manufacturing Costs
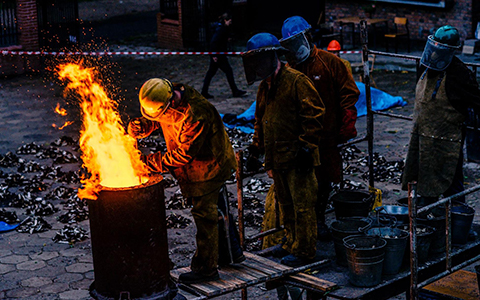
Another key point that to consider before deciding between casting and molding is the cost. The two similar processes use entirely different equipment, labor, and processes to accomplish the task, which necessitates on why one should look out for the costs of both.
Tooling and Manufacturing Costs for Casting
The entire cost of casting is usually measured by the amount of labor and the equipment required. Although dies casting does not necessitate a significant quantity of labor, it does necessitate a large number of tools and equipment.
The expense of tooling for high-precision die casting is significant. They are, in fact, among the best of any top-tier production process.
Furthermore, there is a small probability that the steel components of the die will erode throughout the manufacturing process, losing their sharp edges. The perception of tiny details tends to deteriorate as well. All of this will result in higher tooling costs.
Tooling and Manufacturing Costs for Molding
In contrast to die casting, which has higher expenses, injection molding is considerably less expensive. The cost of molding is solely determined by the raw materials used and the design of the pieces.
When compared to die casting, the cost of creating a unit product utilizing plastic injection is significantly lower. It is noteworthy because it is one of the most cost-effective manufacturing methods. Another interesting feature is that the more pieces you want, the lower the price becomes. Injection molding is one of the most popular solutions due to its low cost.
Die Casting vs. Injection Molding: Comparing Their Mold

After all the differences we have seen between the two popular methods, let’s look at the subtle differences between the molds produced from die casting and injection molding.
- Because high injection pressure is required for die casting, the mold should be reasonably thick to avoid deformation and breaking during heat treatment.
- Because the gate of a die casting mold differs from that of an injection mold, it requires the employment of a diversion cone to break down the high pressure of the material flow.
- The die casting die’s core does not require quenching; however, the general injection mold should be quenched to HRC52 or above.
- Die casting mold injects faster; plastic injection is broken down up into multiple phases.
- Since die casting tooling is particularly corrosive, it is frequently treated on its surface.
- There are two halves to the die casting mold. Distinct plastic molds have different product structures.
- You must open the exhaust slot and slag collection bag to exhaust gas from a die casting mold. Ejector pins and a separating surface are all that are required for an injection mold.
Vacuum Casting vs Injection Molding

Injection molding and vacuum casting are the two most important processes are preferred by many to produce quality products.
Vacuum Casting is the method of producing plastic or rubber components from silicone molds under vacuum. The vacuum casting technique produces dimensionally accurate parts, exact duplicates of the master pattern, with profiles and texture perfectly replicated.
Injection molding is a process where liquefied plastic components are injected into a mold, and hardening them. Injection molding in clean room is done to produce sterile medical products. Injection molding is best suited to the mass-production of products with complex geometries and is the best solution for plastic parts production.
As you can see, there are few discrepancies between the procedures and many parallels, which is why most people struggle to tell the difference between vacuum casting and injection molding.
Here’s a complete reference to the distinctions between vacuum casting and injection molding to help you comprehend the nuances:
Vacuum Casting vs. Injection Molding: The Pros
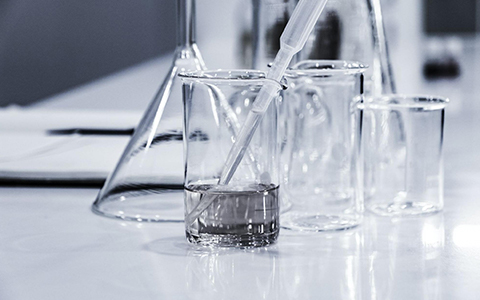
We said earlier that vacuum casting and injection molding are two preferred options by most. So now let’s look at their set of pros which contribute to this fact:
Advantages of Vacuum Casting
- Vacuum forming has a faster turn-around time.
- Much cheaper initial tooling costs.
- This technology is capable of producing more significant plastic parts.
- For smaller batch sizes, the costs are relatively modest.
Advantages of Injection Molding
- A wide range of materials with varying mechanical qualities can be used.
- Parts can be manufactured in any color that is desired.
- Inserts are used in the molding process.
- Closer tolerances and more significant design complexities are feasible.
- Large orders are far more cost-effective.
- Parts created from injection molding are best suited for medical disposable companies.
- There is very little garbage or scrap that can be recycled.
Vacuum Casting vs. Injection Molding: The Cons
As many of benefits there are, Vacuum Casting and Injection Molding brings their own set of cons too; they are:
Disadvantages of Vacuum Casting
- It is not always possible to achieve consistency in wall thickness/consistency in plastic items.
- Parts are limited in terms of depth and complexity.
- On larger batch runs, this procedure is not cost-effective.
- The finishing step requires more time and money.
Disadvantages of Injection Molding
- Because of the necessary tooling, the early start-up expenses are higher.
- More knowledge, talent, and experience are necessary.
- The time it takes to make the initial tooling is longer.
Vacuum Casting vs. Injection Molding: Process Capabilities
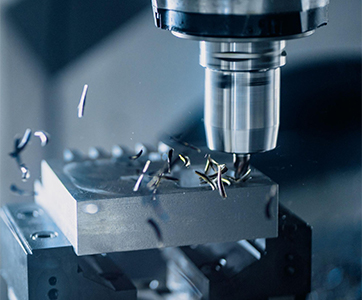
Injection molding can create even the most delicate design elements. Even micro-sized parts can contain ribs, bosses, metal inserts, multiple molding materials, side cores, screwthread, and so on, and the plastic can be any shape.
Because the plastic sheet is stretched over or into a mold, the shaping is done in only one direction, limiting the object’s shape; vacuum casting may not be as adaptable as injection molding. On the other hand, Vacuum casting can achieve significantly thinner product walls. Parts are always hollow, as the vacuum forming above demonstrates. After that, the holes were cut.
Vacuum Casting vs. Injection Molding: Finishing & Waste
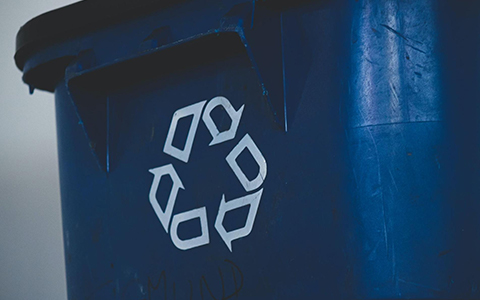
Injection molding produces very little waste, and even if it does, the waste can be reused for the next mold. Each mold tool has ‘runners,’ which are passageways in the tool that allow molten plastic to reach the product’s core and cavity.
- During each molding cycle, cold runners in the mold tool will harden. They must be taken from each molding and reground before being re-used.
- The plastic in the runners of hot runner mold tools stays hot and is reused in the next molding, resulting in no waste throughout manufacturing.
Vacuum casting, too, yields little waste. This can be a rather wasteful technique because the actual product always requires cutting out of the plastic sheet, depending on the sheet and part size. On the other hand, leftover sheet portions can be reground and reused in other operations.
Vacuum Casting vs. Injection Molding: Materials
Antistatic plastic, thermoplastic rubber, chemical resistant polymers, infrared, biodegradable, and other materials are utilized in injection molding.
ABS, Fire Retardant ABS, HDPE, HIPS, Conductive HDPE, Conductive HIPS, PP, PVC, Clear HIPS, Ultra Violet Stable HIPS, and PETG are some of the materials utilized in vacuum casting.
How to Choose Between Injection Molding or Vacuum Casting?

Injection molding and vacuum casting are both reasonable procedures for making plastic analogs, and they can make even the tiniest detailed designs, so picking the appropriate one for your production needs isn’t easy. So, here are a few more ideas to help you decide which technique is best for your needs.
Products Quantity
Without a doubt, injection molding is the finest option when it comes to large volume orders.
Why?
The unit cost is minimal, and you can produce hundreds of models with pinpoint accuracy in a short amount of time.
On the other hand, Vacuum casting is a better alternative if you do not require mass manufacturing of your desired products because the mold and production costs are lower, and time is saved.
Precision & Tolerances
Injection molding allows for extremely small tolerances, resulting in identical goods every time.
Vacuum forming can reach adequate tolerances, but it is less controlled than injection molding since the material is stretched over or into a tool.
Product Complexity
Injection molding enables for the manufacture of more detailed parts than vacuum casting since its tooling is often constructed of high-quality metals. For more intricate products, injection molding may be the superior alternative.
Vacuum casting may be better for more straightforward items, especially those that only need to be produced in small quantities. Vacuum casting can produce a very smooth surface finish while also being reasonably inexpensive.
Material Used
Even if all signals point to vacuum casting, keep in mind that some prototypes, particularly those that will be subjected to physical testing, must be as near to the end-use part as feasible.
As a result, if a functioning item will eventually be made using injection molding, it may be advantageous to create the prototype using the same method, even though the initial investment is higher.
Speed & Iteration
Changing vacuum casting molds is significantly more accessible and less expensive than modifying or replacing injection molding tooling if a design needs to be changed at any point during production.
As a result, vacuum casting is frequently the preferable option throughout the early stages of development. In reality, enterprises often employ vacuum casting to create early prototypes before adopting injection molding to produce end-use parts or later-stage prototypes.
In general, making molds for vacuum casting is faster than injection molding. However, this does not imply that injection molding takes longer. The time it takes is entirely dependent on the quantity ordered. For more enormous volumes, injection molding will be faster.
Testing
For the manufacturing of plastic prototypes, vacuum casting is a frequently utilized technique. Vacuum casting is not only more cost-effective, but it’s also the best method for producing plastic prototypes on a small to medium size.
Vacuum casting, in essence, allows users to duplicate a wide range of functioning plastic parts. Compared to other production methods, the vacuum casting process is relatively quick, and the items produced have a higher quality and better surface finish.
When compared to rapid injection molding, which is one of several technologies used for similar types of manufacturing but has longer lead times and is considered more expensive, vacuum casting technology, on the other hand, may frequently produce the same results with shorter lead times and no particular material requirements.
When an individual firm or primary industry must fulfill deadlines in a short period of time and only for functional and working prototype testing, vacuum casting is frequently a preferable alternative based on the needs.
Lead Time
Casting in a vacuum Depending on the part specification and volume, we can produce up to 20 parts in 15 days or less.
Molding via injection Lead times is always determined by our shop’s workload and the complexity of the mold fabrication. In 2-4 weeks, a simple mold can be completed. In 6-8 weeks, you’ll have a complex mold. Depending on the complexity, a prototype aluminum mold could be ready in 2 to 3 weeks.
Cost
Injection molding requires a higher front-end cost but a much lower unit price, whereas vacuum casting requires a lower front-end cost but a significantly lower unit price. Vacuum casting allows for a drip feed of pieces, whereas injection molding typically requires a longer wait with a quick finish.
Is It Die Casting Better Than Injection Molding?

The technique is essentially the same whether you use die casting or injection molding to make a part. You make a mold or die in the shape of the part you wish to make. The material is then liquefied and injected under great pressure into the die/mold. The die/mold is then cooled with internal cooling lines and die spray applied to the die cavities. Finally, you remove the shot by opening the die.
Although there are some variances in method, the most significant distinction between die casting and injection molding is that die casting employs a metal as the raw material, such as aluminum alloys or other metallic alloys, whereas injection molding uses plastic or polymers.
So, which should you choose?
It depends entirely on you.
If you want to produce metal parts, the right choice will be die casting.
If you want to produce plastic parts, the right choice would be injection molding.
However, if you’re unsure about the type of material to employ, consider about your objectives.
Does the part necessitate a high level of dimension and design precision?
Then unquestionably, die casting is the best option.
If you are perhaps designing simpler parts that do not need many intricacies, then injection molding is the best choice.
How to Choose Casting or Injection Molding for Your Need
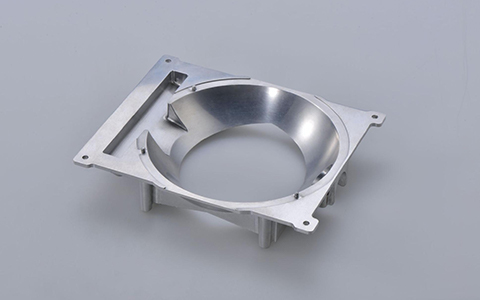
Seasky Medical has long been a leader in providing high-quality OEM services to its clients. With over a decade of successful projects under our belts, we are proud to call ourselves industry leaders that manufacture precision molds in accordance with ISO standards.
Customers can expect precise dimensions and prompt delivery from our well-trained, professional workforce.
With our extensive experience, we at seasky are well aware that consumers often wonder whether to go with molding or casting.
The choice is simple.
Casting allows you to create intricate designs, shapes, and quality pieces. It’s worth noting. However, die casting is not the best process for bulk production. Casting is the superior alternative if you want to create a lot of intricate parts with high accuracy.
On the other hand, Molding is an excellent choice if you need to mass create thousands of parts. It’s also a perfect choice for prototyping because it’s quick and accurate.
Conclusion
There are also other considerations like material type, costs, quantity., prototypes, and many more to consider before deciding on a process, which is why it is necessary to work with a manufacturer who understands the ins and outs of each. Why not visit SeaSky Medical and choose the most affordable and quality molding partner.