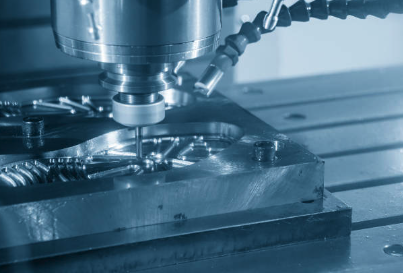
Precision injection moulding is a specialized process that offers unique benefits to various industries requiring high-precision parts. This comprehensive guide will explore the differences between conventional and precision injection molding, the challenges faced in this process, troubleshooting common problems, the importance of areas of precision, choosing the best manufacturer, maintaining quality control, industries that commonly use precision injection molding, factors to consider when selecting a precision machine, cost comparison.
What is the difference between conventional and precision injection molding?
Conventional injection molding is a common method for making different shaped, sized, and complex plastic pieces. In this method, melted plastic is put into a mold, and it becomes solid in the shape of the mold’s space as it cools down. In contrast, precision injection moulding focuses on producing parts with extremely tight tolerances and high levels of accuracy, and the mold material is of high quality and sturdy, with great accuracy in the cavity dimensions, a smooth finish, and precise alignment between the different mold parts. This process demands high precision molds, advanced machinery, and skilled operators to achieve the desired results.
The main difference between the two lies in the tolerance levels. Conventional injection molded parts typically have a tolerance of +/- .005″, whereas precision molded parts require tolerances between +/- .002″ and +/- .001″ or even less in some cases.
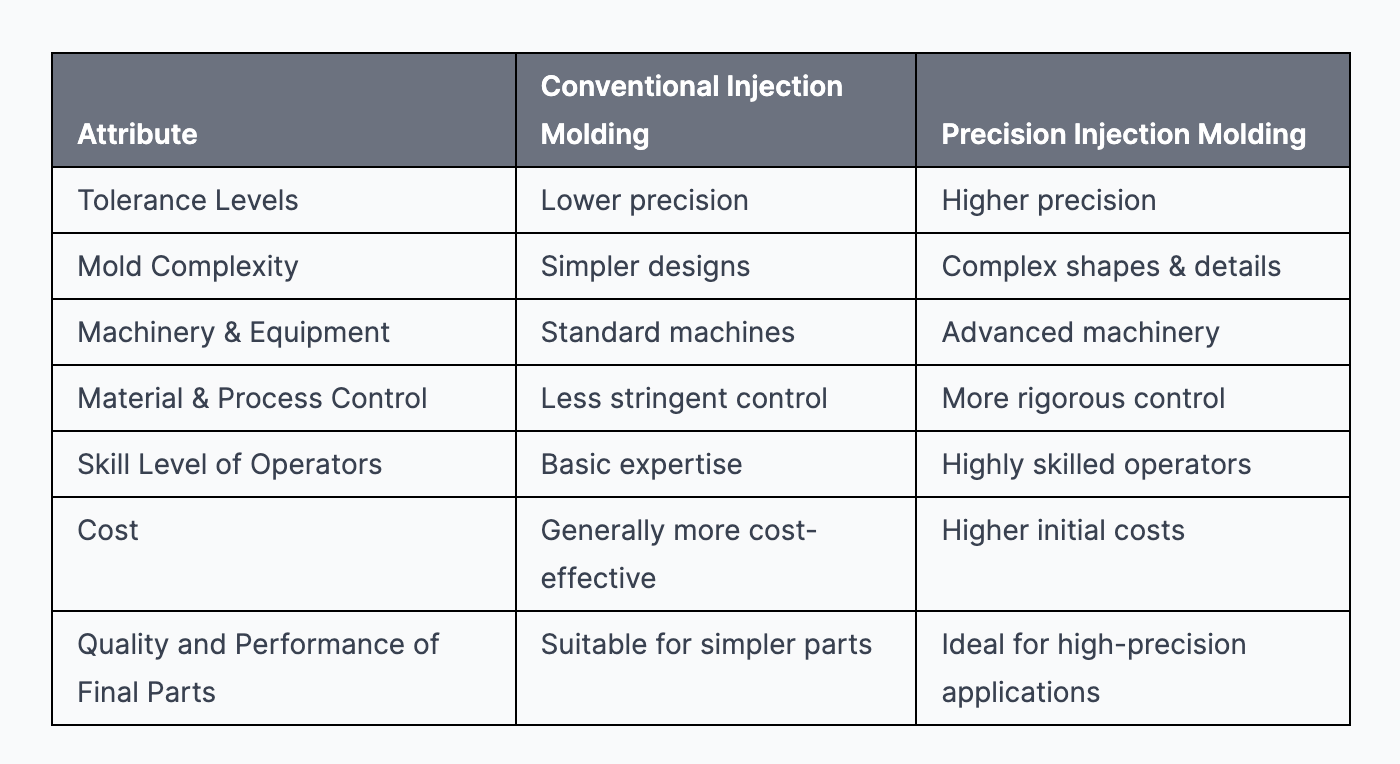
What are some of the challenges in precision injection molding?
Precision injection molding is a complex process that involves producing high-precision plastic products with close tolerances, intricate geometries, and intricate design features. While this technique has many advantages, it also faces several challenges, including:
- Material selection and preparation: Choosing the correct material for a specific application is essential when working with precision injection molding. The features of materials, like thickness, ability to handle the heat, and how much they shrink, can really affect how well the process works and the final product’s quality. Material preparation, including drying and blending, must be done carefully to maintain consistency and avoid defects.
- Tooling design and fabrication: Designing and making precision injection mold require advanced engineering skills and sophisticated machinery. The mold must be capable of producing parts with tight tolerances and intricate details consistently. Factors such as venting, cooling channels, and gate placements must be meticulously considered during mold design.
- Machine calibration and process control: Precision injection molding machines need to be correctly calibrated and maintained to ensure consistent, reproducible results. Factors such as injection pressure, melt temperature, cooling rates, and part ejection must be tightly controlled throughout the process.
- Shrinkage and warping: During the cooling process, the plastic material shrinks, which might result in dimensional inaccuracies or warping. It is crucial to account for these issues during mold design, material selection, and process control.
- Process repeatability: It is vital to control and monitor the molding parameters to ensure repeated success in delivering high-quality parts with close tolerances. Variations in the process can lead to defects and inconsistencies.
- Part inspection and quality control: With tight tolerances and intricate details, quality control and inspection for precision injection molding parts can be challenging. Advanced measuring and inspection techniques, such as coordinate measuring machines (CMM) or optical inspection systems, may be required to assess part quality accurately.
- Cost and lead time: Precision injection molding can be more expensive and time-consuming due to the complexity of tooling design and fabrication, material preparation, and process optimization. Finding the right balance between cost efficiency and part quality is essential.
- Skilled operators: The precision injection molding processes require a deep understanding of material behavior, machine capabilities, and process control. Skilled operators and engineers with the right expertise are crucial for achieving optimal results consistently.
Troubleshooting common problems in precision injection molding
Troubleshooting common problems in precision injection molding involves identifying the root causes and implementing appropriate corrective actions. Here are some common issues and potential solutions:
Common Problems | Causes | Solutions |
Short shots | When a plastic part is not completely filled, it results in a short shot. Causes include insufficient material, low injection pressure, or incorrect shot size. | ✔️Increase injection pressure, and ensure the shot size is adequate. ✔️Check for any obstructions in the mold or material flow. ✔️Increase material temperature to improve flow properties. ✔️Optimize the gate and runner design. |
Flash | An excess plastic material that flows beyond the parting line, resulting in undesired thin layers, is called a flash. Causes may include high injection pressure, worn or damaged mold, or insufficient clamping force. | ✔️Reduce injection pressure. ✔️Inspect and repair the mold if necessary. ✔️Increase clamping force on the injection molding machine. |
Sink marks | Depressions on the part surface are caused by uneven cooling or material shrinkage. | ✔️Adjust the cooling rate and injection speed. ✔️Modify gate location or part-wall thickness to improve material flow. ✔️Optimize material selection or processing conditions. |
Warping | Distortion of the part, typically caused by uneven cooling, material shrinkage, or residual stress. | ✔️Improve mold design to ensure uniform cooling. ✔️Adjust packing pressure to reduce residual stress. ✔️Check material moisture content and drying process. |
Weld lines | Visible lines on the part where different material flows meet, usually caused by insufficient fusion or air entrapment. | ✔️Increase injection pressure and speed. ✔️Optimize gate placement and venting. ✔️Ensure material temperature is within the proper range. |
Burn marks | Discolored or charred areas on the part, are typically caused by trapped air, overheating, or excessive residence time. | ✔️Optimize venting and gate placement. ✔️Adjust injection speed and pressure. ✔️Ensure the material temperature is within a suitable range |
Jetting | Wavy patterns in the part caused by a turbulent flow of material during filling. | ✔️Increase injection pressure and speed. ✔️Improve runner and gate design to ensure proper material flow. ✔️Adjust material temperature. |
Delamination | Separation of layers within the molded part, is usually caused by contamination or material incompatibility. | ✔️Ensure material and additives are compatible. ✔️Improve material preparation and drying process. ✔️Thoroughly clean the mold and the injection molding machine. |
Troubleshooting precision injection molding problems is a continuous process of monitoring, optimizing, and fine-tuning. Each problem may have multiple causes, and solutions may involve making adjustments to multiple variables. An experienced team of operators and engineers plays a crucial role in addressing these issues and maintaining a high-quality molding process.
Areas of Precision
Tolerance Issues
Precision injection moulding is necessary when a product requires tight tolerances, which means the dimensions of the part must be followed precisely and accurately. Identifying the areas that require precision molding ensures a cost-effective solution without compromising quality. In some cases, tolerances can be achieved through conventional injection molding, but precision molding provides a more reliable solution for critical components.
Materials
Choosing the right plastic material plays a significant role in achieving the desired level of precision in injection molded parts. Materials with low shrinkage properties are preferred for precision molding applications. In some cases, the addition of fillers or reinforcements, such as glass fibers or carbon fibers, can help improve the material’s dimensional stability and reduce shrinkage.
Technique
The technique used in precision injection moulding is crucial for ensuring the production of identical parts with tight tolerances. A high-precision mold, advanced machinery, and skilled operators are required for a successful precision molding process. The process should be slow, steady, and focused to produce consistent and accurate results.
What to Look for When Selecting The Injection Molding Manufacturer
Choosing the right precision injection molding company is essential for achieving high-quality, precise parts. When selecting a manufacturer, consider the following factors:
- Expertise in precision molding: Look for a company with extensive experience and a proven track record in precision injection moulding.
- High-precision mold and machine capabilities: Ensure the manufacturer uses advanced machinery and high-precision molds to produce accurate parts consistently.
- Quality control measures: The manufacturer should have stringent quality control measures in place to ensure the production of consistent, high-quality parts.
- Technical support and customer service: A reliable manufacturer like Seaskymedical, should provide excellent customer service, technical support, and assistance throughout the production process.
How can Quality Control be Maintained in Precision Injection Molding?
Maintaining quality control in precision injection moulding is critical for producing consistent, high-quality parts. The following steps can help ensure quality control:
- Use high precision of the mold and machines with advanced capabilities to produce precise plastic parts consistently.
- Implement strict injection molding process control measures, such as monitoring temperature, pressure, and cycle time, to maintain consistent part quality.
- Conduct regular inspections and testing of parts to ensure they meet the required tolerances and specifications.
- Train and educate operators on the importance of precision and accuracy in the molding process.
What Industries Commonly Use Precision Injection Molding?
Precision injection moulding is widely used across various industries requiring high-precision parts, including:
- Medical devices: Precision molded components are used in surgical instruments, diagnostic equipment, and implantable devices.
- Automotive: High-precision parts are critical for the performance and safety of vehicles, such as fuel injectors, sensors, and electronic components.
- Aerospace and defense: Precision injection molded parts are used in aircraft components, satellite systems, and military equipment.
- Electronics: Precision injection moulding is used to produce connectors, switches, and other components for electronic devices.
- Optics: The process is employed for the manufacturing of lenses and other optical components that demand high levels of precision.
What factors should be considered when selecting a precision injection molding machine?
When selecting a precision injection molding machine, consider the following factors:
- Clamping system stiffness: The machine should have a stiff clamping system with a controlled movement between 0.05 to 0.08mm.
- Dimensional tolerance capabilities: The machine should be able to maintain tight tolerances consistently throughout the production process.
- Injection pressure: High pressure machines are preferred for precision molding, as they can improve part quality and reduce shrinkage.
- Machine speed: The speed of the machine, including die opening and closing, should be optimized for precision molding applications.
- Plasticizing components: The machine should have high-quality plasticizing components, such as the screw, screw head, and material barrel, to ensure consistent part quality.
What is the cost of precision injection molding compared to other manufacturing processes?
Precision injection molding usually costs more than regular injection molding because it needs special molds, better machines, and trained workers. But the good parts of precision molding, like making things exact, high-quality products, and having less waste, often make up for the extra costs. Sometimes, precision injection molding costs less than other methods, like using machines or adding materials, especially when making a lot of items at once.
Conclusion
Precision injection moulding is a specialized process that offers significant advantages for industries requiring high-precision parts.
By understanding the differences between conventional and precision molding, addressing common challenges, and implementing best practices, manufacturers can produce consistent, high-quality parts that meet the demanding requirements of various applications.
Selecting the right precision injection molding company, like Seaskymedical, materials, and machinery is crucial for ensuring a successful precision molding project. With proper planning and execution, precision injection moulding can be a cost-effective solution for producing high-quality, accurate parts across various industries.