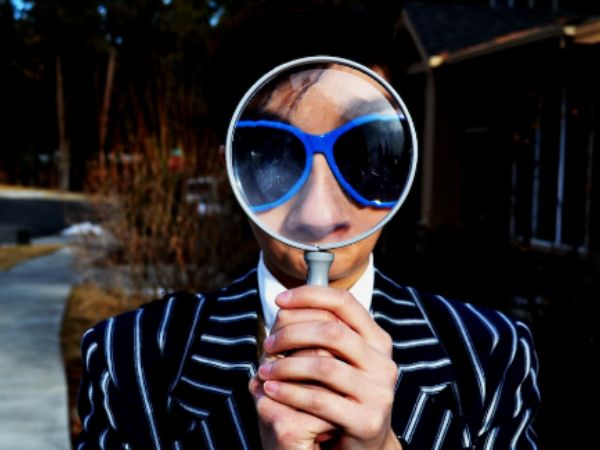
The medical industry has witnessed significant advancements in recent years, driven in part by the increasing use of medical plastics. Medical grade plastic has become a vital component in the manufacturing of various medical products and devices, providing cost-effective, versatile, and safe solutions for manufacturers and end-users alike. This comprehensive guide aims to explore the incredible advantages of medical grade plastics, their properties, and their role in the rapidly evolving healthcare landscape.
The Incredible Advantages of Medical Grade Plastic
Medical grade plastic offers several benefits that make them an ideal choice for use in the healthcare industry. Some of the key advantages include:
Safer
Medical places have lots of germs and viruses that can make people even more sick. But plastics can be cleaned well to make things more hygienic for all. They can even be coated to fight germs better. Plastics don’t break like glass, and they’ve been great for those with metal allergies. Medical grade plastics stop germs from spreading and cut the chance of infection.
Biocompatibility
One of the main reasons why plastics are commonly used in medicine and healthcare is that they are biocompatible. This means that these medical-grade plastics are specially designed to interact well with the human body. Medical grade plastic doesn’t cause any harmful or allergic reactions when they come in contact with living tissues and organs.
These plastics are safe to use on and in the human body. Because they are so compatible with human tissues, medical grade plastics are preferred for many healthcare applications like medical devices, tools, and implants.
Versatility
Medical grade plastics are highly versatile and can be molded into various shapes and sizes, making them suitable for a wide range of medical applications. This versatility allows manufacturers to create intricate medical devices and components with ease.
Durability and Strength
Medical grade plastics are known for their durability and strength, making them perfect for long-lasting medical products that must withstand constant use and sterilization. Certain medical plastics, such as nylon, even possess a high tensile strength that rivals some metals.
Cost-effectiveness
Put simply, plastics used for medical purposes are usually cheaper than other options like metals or glass. Because plastics can be made quickly and in large amounts, it keeps the costs down. This means that medical grade plastics are often the most budget-friendly choice when making medical equipment, tools, or other healthcare products.
Sterilization
Medical grade plastics can be easily sterilized using various methods, such as steam autoclaving, ethylene oxide (ETO) gas, and gamma radiation. This ensures that medical devices and components made from these materials remain safe and free from contamination.
Popular Thermoplastics Used in Medical Devices
Medical injection molding involves the use of various plastic materials. To name a few, thermoplastics are among the most commonly utilized. Let’s delve into the exciting world of medical plastics used in the medical device industry!
Polyethylene
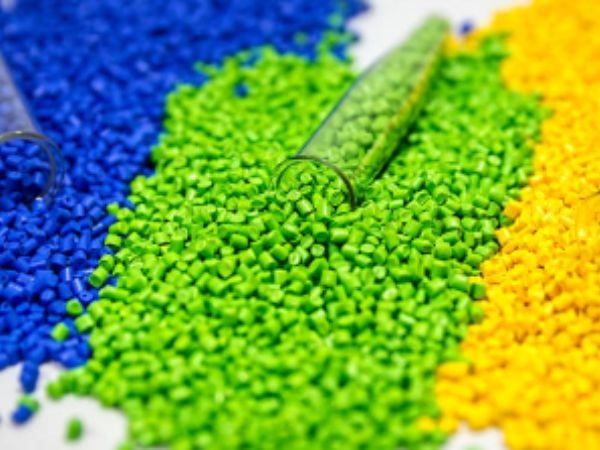
Polyethylene is a top medical plastic because it’s affordable, impact-resistant, rust-resistant, and stays solid when sterilized often. It’s biologically inactive and doesn’t break down in the body, so it’s good for prosthetics.
Polypropylene
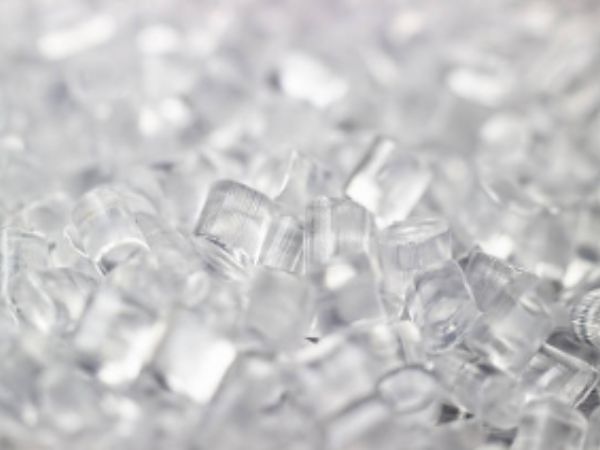
Polypropylene is stress-resistant, crack-resistant, impact-resistant, and fatigue-resistant. It has a high melting point, about 1710C, so it can handle the heat of an autoclave. It’s used for disposable syringes, oxygenator membranes, prescription bottles, connectors, and finger joint prosthetics.
Polymethyl methacrylate
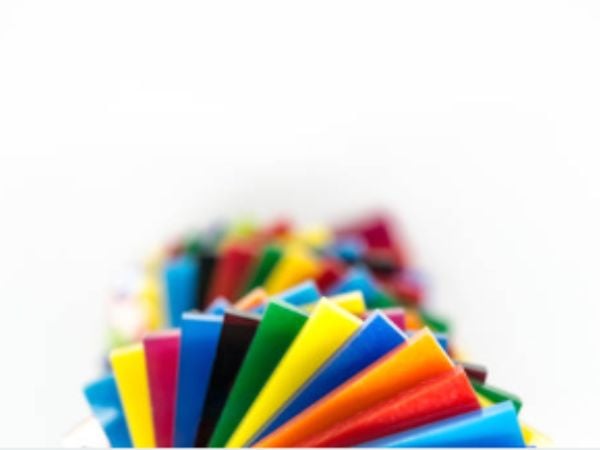
Polymethyl methacrylate has a high melting point, 200-250°C, and works with blow molding or extrusion. The medical kind is used for endoscopic medical parts.
Polyvinyl chloride
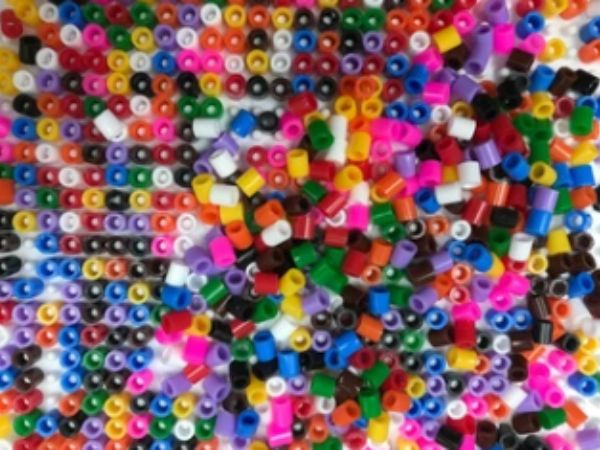
Flexible PVC is dense, cost-effective, and easy to find. It’s good where sterility matters. Hard PVC is durable, strong, and stiff. Both are used for hemodialysis equipment, tubing, heart catheters, and artificial limbs.
Polyamide
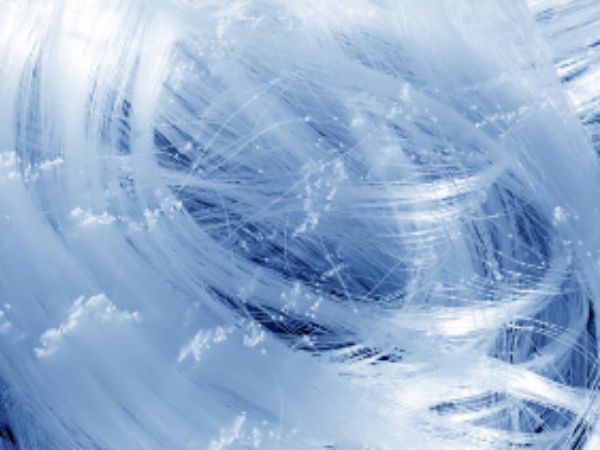
Polyamide or nylon is a fascinating plastic material that links amino and carboxylic acid groups together. Its remarkable properties include strength, durability, chemical resistance, anti-rust capabilities, and flexibility. It’s truly a remarkable plastic material that has found its way into many industrial and consumer applications.
Acrylonitrile butadiene styrene (ABS)
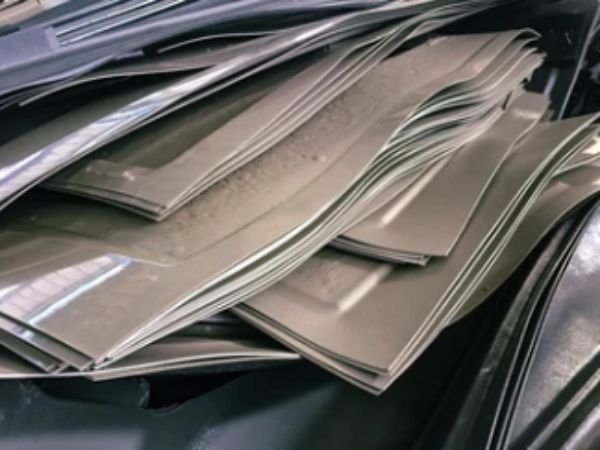
Medical grade abs plastic is a super cool material made by combining styrene, acrylonitrile, and polybutadiene. The resulting product is a durable, strong, and resistant plastic that can withstand all sorts of wear and tear. It’s pretty amazing how it can be molded in so many different ways – by injection, blow molding, or extrusion. Whether you’re a science geek or just love cool materials, ABS plastic is definitely something worth geeking out about!
Polycarbonate
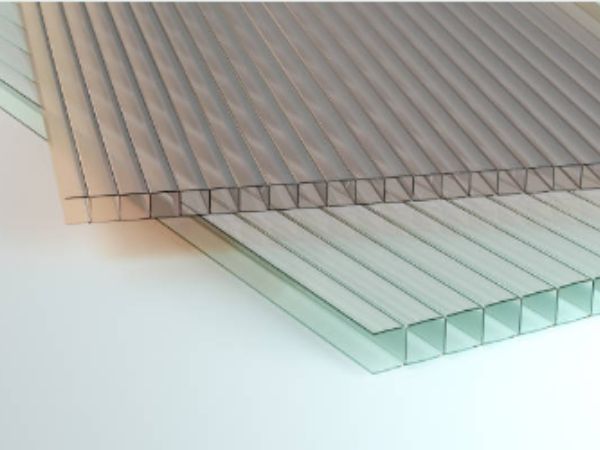
Polycarbonate is favored for strength, heat resistance, and biocompatibility. It’s used for IV connectors in kidney dialysis and heart surgery.
Medical plastics make products like plastic gloves, syringes, and surgical tools. They differ from regular plastics by being biocompatible. To choose the right medical plastic components, know the types and their advantages.
How Medical Grade Plastics Ensure Product Safety and Performance in the Healthcare Industry
Medical grade plastic is crucial for ensuring that medical plastic products and devices are both safe and effective. Their unique properties contribute to their widespread use in the healthcare industry:
An overview of medical grade plastic unique properties
Biocompatibility
As mentioned earlier, medical grade plastics are biocompatible, meaning they do not cause toxic or immunological reactions when in contact with living tissue. This property is essential for medical components that come into contact with the human body, such as implants and surgical tools.
Non-permeability
Medical plastics are non-permeable, which means they do not support the growth of bacteria and other disease-causing organisms. This property helps to maintain the sterility of medical products and devices, reducing the risk of infection.
Resistance to Sterilization
Medical grade plastic can withstand various sterilization methods, ensuring that medical devices and components remain safe and free from contamination. This resistance to sterilization is essential for maintaining the safety and effectiveness of medical plastic products throughout their lifecycle.
Lightweight and Durable
Medical plastic can be easily cleaned and sterilized in many ways. This is important because it means that any medical equipment or parts made from these plastics can be properly sanitized. Common ways to sterilize medical plastics include:
- Using pressurized steam, known as autoclaving. This kills any germs or viruses on the plastics.
- Exposing the plastics to ethylene oxide gas. This is a very effective way to sterilize plastics while ensuring they remain safe to use.
- Bombarding the plastics with gamma radiation. This high-energy radiation eliminates any contamination of the plastics.
Because medical plastics can be sterilized in so many effective ways, healthcare workers can be confident that any medical device, tool, or component made from these plastics is clean and germ-free. This is critical for safety and preventing infection.
What tests are performed on medical grade plastics?
- Biocompatibility testing
This includes cytotoxicity testing, sensitization testing, irritation testing, etc. to ensure the material does not have adverse effects on biological tissues and systems.
- Chemical testing
This includes tests for extractable and leachable to identify any potentially toxic chemicals that could leach from the material into the body. Tests are also done to ensure the material is chemically stable and inert.
- Physical and mechanical testing
This includes tests like tensile strength, impact resistance, fatigue resistance, etc. to ensure the material has sufficient strength and durability for the intended medical use.
- Sterilization testing
The material is exposed to different sterilization methods like autoclaving, irradiation, ethylene oxide, etc. to ensure it can withstand sterilization without significant degradation.
- Shelf-life and aging testing
The material is stored under controlled conditions for extended periods to evaluate changes in its properties over time and ensure it meets specifications throughout its intended shelf-life.
- Bioburden and endotoxin testing
These tests are done to ensure the material does not contain unacceptable levels of microbes, bacteria, or endotoxins which could contaminate the medical device.
- ISO 10993 compliance
Most medical grade plastics go through a series of tests to ensure compliance with the ISO 10993 standard for biological evaluation of medical devices. This helps to standardize biocompatibility and safety evaluation of the materials.
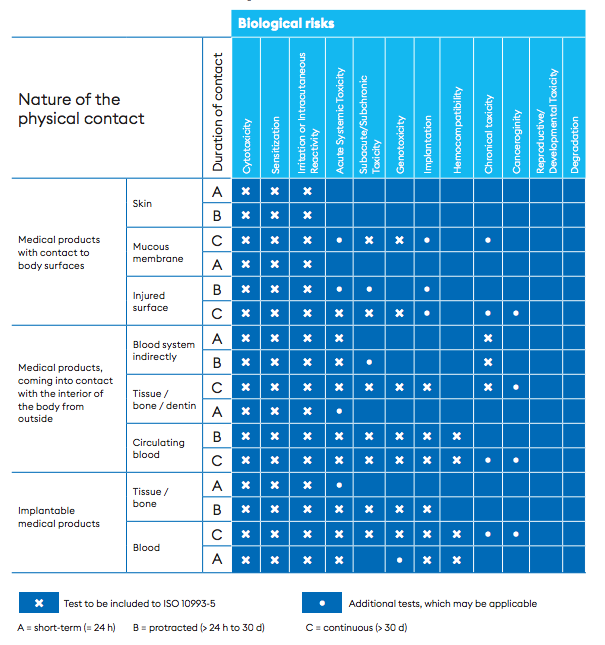
Medical-Grade Materials Apply for Medical Technology
Plastics machined into final products are utilized in various medical devices and equipment currently. For applications necessitating established biocompatibility, we provide an array of medical-grade materials and a wide selection of standard plastics for applications without direct patient contact.
No. | Application | Medical Device |
1 | Surgical instruments and supplies | ● Handles and grips for instrumentation ● Sizing trials for knee and hip replacement ● Endoscopic housings and eyepieces ● Sterilization trays and caddies |
2 | Diagnostic | ● Parts for X-ray and MRI devices ● Components for supports and biopsy units |
3 | Therapeutic systems | ● Blocks and housings for dialysis machines ● Pistons and valves for anesthetic equipment ● Supports and adaptors for respiratory units |
4 | Dental | ● Grips and handles for dental instruments ● Components for treatment and therapy units |
5 | Pharmaceutical and biotechnology | ● Components for sample changers ● Valve housings and nozzles for fluid distribution ● Spectrometer parts for chromatography systems ● Wear parts for pill and tablet production |
Challenges and Opportunities for Medical Plastics in a Rapidly Evolving Healthcare Landscape
The healthcare industry is constantly evolving, and medical grade plastic must adapt to meet the changing needs and expectations of patients, healthcare providers, and regulators. Some of the challenges and opportunities faced by medical grade polymer in this rapidly changing landscape include:
Material Innovations
As new medical applications and technologies emerge, there is a growing need for innovative medical grade plastics with improved properties and performance capabilities. Material innovations can help address this need, enabling medical plastics manufacturers to develop novel products and solutions that cater to the specific requirements of the healthcare industry.
Regulatory Compliance
Medical grade plastic must adhere to stringent regulatory standards and guidelines to ensure the safety and effectiveness of medical products and devices. As regulations evolve, medical plastics manufacturers must stay up-to-date with the latest requirements and ensure that their products meet these standards.
Sustainability
Environmental concerns and the growing emphasis on sustainability are driving the need for more eco-friendly medical grade plastics. This presents an opportunity for medical plastics manufacturers to develop new materials and processes that minimize their environmental impact while still meeting the performance and safety requirements of the healthcare industry.
Customization and Personalization
The growing trend towards customization and personalization in healthcare is driving the demand for medical grade plastics that can be tailored to meet the unique needs of individual patients. This presents an opportunity for medical plastics manufacturers to develop innovative materials and processes that enable the production of customized medical products and devices.
Get Medical Grade Plastic Parts At Seaskymedical
Medical plastics are being used more and more in healthcare because of how useful and important they are. But before making any medical plastic parts, manufacturers have to carefully choose the right kind of plastic components for the job. And it’s essential that high-quality methods are used to make medical supplies from plastics.
As a medical plastics manufacturer, Seaskymedical provides high-quality plastic machining and manufacturing services to produce medical graded plastic parts. We have a skilled team devoted to making all kinds of industrial plastic components. We take pride in being able to make medical graded plastic products to suit your needs.
We are the company to get medical plastic parts from. We use state-of-the-art techniques to machine and fabricate high-quality plastics for the healthcare industry. Our experienced staff knows that medical plastics have to be made precisely and carefully to exacting standards. We are committed to providing plastic medical supplies and parts that meet your requirements.
In short, if you’re looking for a reliable source for medical plastic parts that are expertly crafted, come to Seaskymedical. We have the know-how, experience, and dedication to quality to make plastics suited for any medical purpose.