In the medical device industry, contract medical manufacturers play an important role in the development and production of new products. These companies specialize in the design and manufacture of medical devices, and they often work with original equipment manufacturers (OEMs) to develop new products. There are many benefits to working with a contract manufacturer, including access to cutting-edge manufacturing technology, expertise in quality assurance, and cost savings. However, it is important to choose a reputable and experienced contract manufacturer who can meet your specific needs. This blog post will overview the top 10 medical device contract manufacturers based on experience, quality, and capability criteria.
List Of List 10 Medical Device Component Manufacturers
1. Seaskymedical
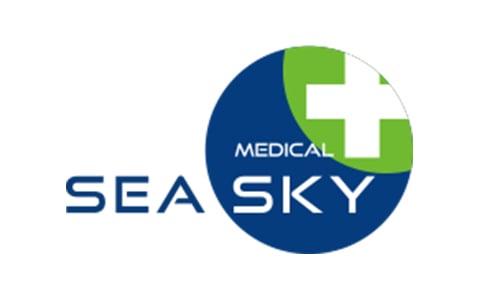
SeaskyMedical is a specialist medical molding company that offers high-grade molding solutions. All assignment phases are supported by professional, all-inclusive support, including product design, mold manufacturing, material preference, and plastic injection molding. SeaskyMedical uses cutting-edge medical molding technology for product production. Under the experienced and sincere service, they draw together the production practices experiences and analyze data to reduce risk.
They are popular with many medical partners due to their ISO 13485 certification, Class 7 medical device clean room, and multiple medical molding technologies. The quality and sterilization medical device parts could be guaranteed in Seaskymedical.
2. Scapa Healthcare
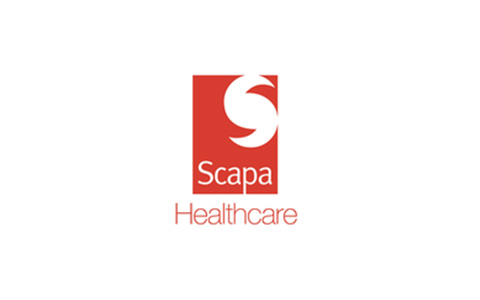
Scapa is the preferred strategic partner of medical device component manufacturers. They work with the most renowned organizations in cutting-edge wound care and consumer wellness. They have an in-depth knowledge of medical needs, which allows them to use their high-end technology, manufacturing, and development expertise to develop innovative solutions to help customers thrive in the market.
3. Spectrum Solution
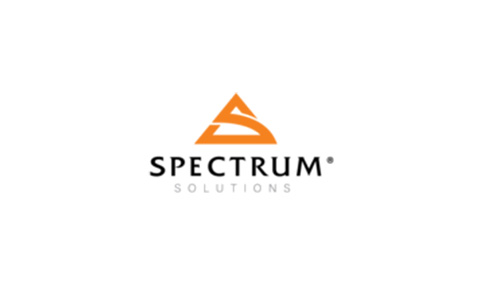
Spectrum Solutions is a leading provider of medical device molding. They provide clients with a full range of services, from product development and prototyping to manufacturing and packaging. They are ISO 13485 certified and are registered with the FDA as a medical device establishment.
4. HDA Technology
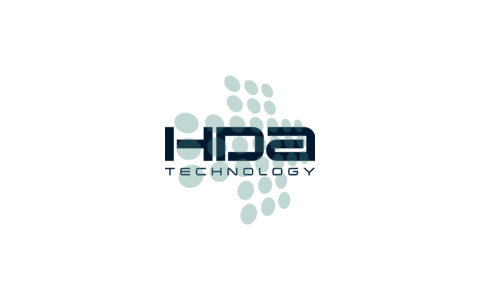
HDA Technology is one of the best medical device contract manufacturing companies. They specialize in designing and manufacturing medical devices and components for the healthcare industry. They have a team of experts who provide a full range of services to help clients quickly and efficiently bring their products to market quickly and efficiently. They handle all medical device contract manufacturing aspects, from engineering and prototyping to assembly and packaging.
5. Advantech Plastics, LLC
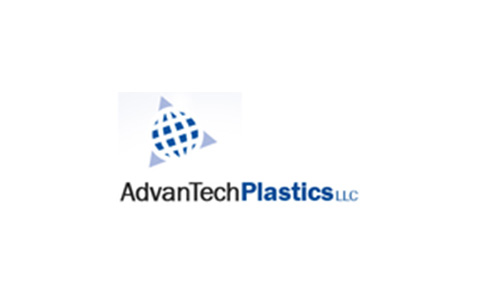
Advantech Plastics, LLC is a medical device contract manufacturer specializing in custom medical device components and assemblies. The company was founded in 1996 and is headquartered in Geneva, Illinois. Advantech Plastics has over 20 years of experience in the medical device industry and works with various Fortune 500 companies. The company’s services include everything from design and engineering to manufacturing and assembly. Advantech Plastics is dedicated to providing its customers with the highest quality products and services.
6. Medtronic
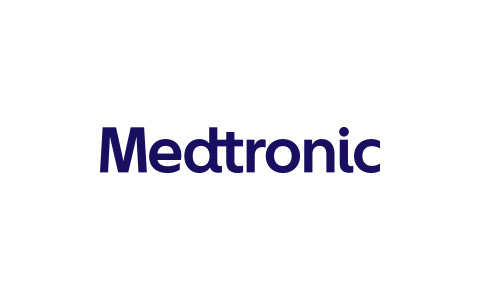
Medtronic is a medical device contract manufacturing company with over 30 years of experience. They work with some of the world’s top medical device companies to bring their products to market. The engineers, quality assurance experts, and project managers are dedicated to ensuring that our customers’ products meet all regulatory requirements and are manufactured to the highest quality standards.
7. Abbott Laboratories
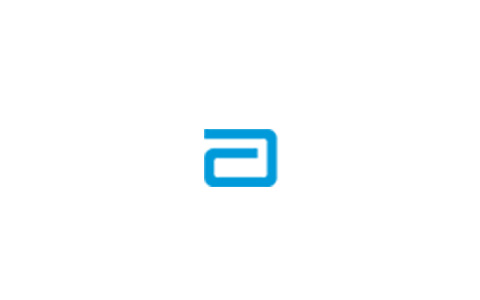
Abbott Laboratories is a leading healthcare company that develops and manufactures a broad range of branded and generic pharmaceuticals and medical plastic injection molding producer and diagnostics. The company has a long history of innovation. It has developed many groundbreaking products, such as the first commercially available test for HIV and the first FDA-approved mechanical heart valve.
8. GE Healthcare
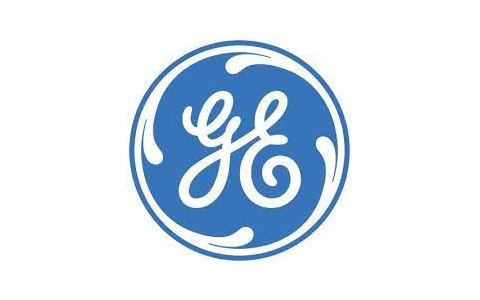
GE Healthcare is a world leader in medical device contract manufacturing. They help customers design and develop new medical devices and manufacture and assemble devices to the highest quality standards. Their state-of-the-art facilities, experienced engineers, and technicians are dedicated to helping our customers bring new life-saving devices to market quickly and efficiently.
9. Becton Dickinson
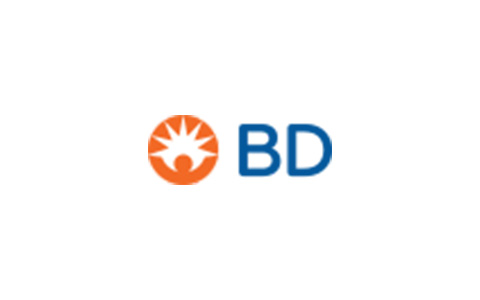
Becton Dickinson is a leading medical device contract manufacturer with over 50 years of experience in the industry. They partner with clients to deliver high-quality, innovative medical devices that improve patients’ lives worldwide. They offer a complete range of services, from product development and design to manufacturing and assembly. They are ISO 13485 certified and compliant with FDA regulations and pride themselves on our quality, customer service, and commitment to excellence.
10. Alcon Laboratories
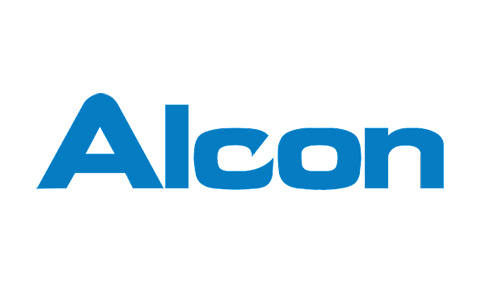
Alcon Laboratories is a medical device contract manufacturer specializing in designing and producing surgical devices and equipment. Founded in 1948, Alcon has a long history of providing quality products and services to the medical community.
Alcon is ISO 13485 certified and has a team of experienced engineers and production staff dedicated to meeting their customers’ needs. Alcon works with various medical device companies, from small startups to large multinational corporations.
How do Medical Device Contract Manufacturing Companies Molding Products?
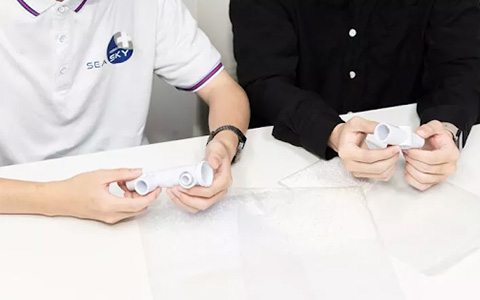
Molding is a process in which a material, such as plastic, metal, or glass, is shaped by pressing it into a mold. This process is often used to create products with a complex shape or that are too large or small to make using traditional manufacturing methods.
Medical device contract manufacturing companies often use molding to create products such as prosthetics, implants, and tubing. The process begins with creating a mold, typically made from a material such as silicone or aluminum. Once the mold is created, it is filled with the desired material, cooled, and hardened to create the finished product.
Medical device contract manufacturing companies take on the challenge of molding products that meet the highest standards of quality and safety. These products must be able to withstand the rigors of use in the medical industry and meet the expectations of patients and doctors.
There are a few steps that medical device contract manufacturing companies follow to mold products. These are:
Product Development
Molding products for medical device contract manufacturing companies must adhere to extremely tight dimensional tolerances to be used in life-saving medical devices. The product development process for these products must consider the wide range of potential uses for the finished product and the need to meet stringent regulatory requirements.
Material Selection
The material selection of molding products in medical device contract manufacturing companies must adhere to the specific requirements of the medical device industry. Compliance with industry standards is essential to ensuring the safety and efficacy of medical devices.
Four primary materials are commonly used in the medical device industry: plastics, metals, ceramics, and composite materials. Each material has unique properties that make it suitable for specific applications.
Common plastics used in medical devices include polyethylene, polypropylene, and polycarbonate. Metals are often used in medical devices for their strength and durability. Typical metals used in medical devices include stainless steel, titanium, and nickel alloys.
3D Prototype and Printing
In medical device contract manufacturing, 3D prototypes and printing technologies have become increasingly important. These technologies can be used to create prototypes of new products or to print molds for existing products. 3D printing can be used to create the mold directly from a digital model, eliminating the need for traditional tooling methods.
Additionally, 3D prototypes and prints can be created in various materials, including plastics, metals, and ceramics.
Mold Making
Molding is a manufacturing process used to create products from materials such as plastics and metals. Molding can be done using various methods, but injection molding is the most common method in the medical device industry. In this process, molten materials are injected into a mold that is the desired shape of the final product. The mold is then cooled, and the product is ejected.
CNC Plastic Machining
CNC plastic machining is a process that is commonly used in the medical device contract manufacturing industry. This process involves using computer-controlled machines to cut and shape plastic parts. CNC machining is an exact manufacturing method, and it can be used to create parts with very tight tolerances. This process is often used to create complex shapes that would be difficult to produce using traditional methods.
Medical Device Contract Manufacturing
Medical device contract manufacturing of molding products is a process whereby a manufacturer produces molded parts or products for another company. The parts or products may be used in medical devices, implants, or other medical products. The medical device contract manufacturing process of molding products generally includes the mold’s design and development, the molding tool’s creation, the molding of the parts or products, and the final assembly of the parts or products.
Medical Plastic Injection Molding
Molding is a manufacturing process used to create products from materials such as plastics and metals. Molding can be done using various methods, but injection molding is the most common method in the medical device industry. In this process, molten materials are injected into a mold that is the desired shape of the final product. The mold is then cooled, and the product is ejected.
Validation And Verification Of Medical Devices
The validation and verification process is essential to ensure that medical devices are safe and effective. Validation is the process of testing a product to ensure that it meets all the requirements of the intended use. This includes ensuring the product is safe and effective for the intended patient population. Once a product has undergone validation, verification is conducted to confirm that the validation results can be reproduced.
Secondary Operation
In medical device contract manufacturing, the term “secondary operations” refers to all the processes performed on a product after the initial molding process. These operations can include but are not limited to trimming, inspection, assembly, and packaging.
While secondary operations are not always required, they can sometimes be essential. For example, a secondary operation would be necessary if a product is too large or too complicated to be trimmed by hand. Or, if a product needs to be inspected for defects before it can be shipped to the customer, assembly and packaging would also be necessary.
In some cases, secondary operations can even be used to improve the overall quality of a product. For example, if a product is prone to defects, adding an extra inspection step can help ensure that only flawless products are shipped to the customer.
Find Medical Device Contract Manufacturer – Seaskymedical
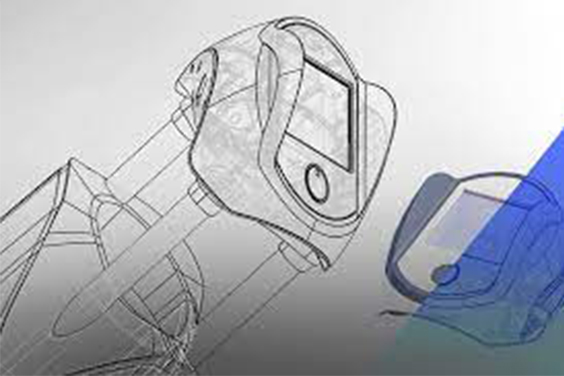
Looking for a reliable medical device contract manufacturing company? Seaskymedical is a leading contract manufacturer of medical devices with years of experience in the industry. We provide a full range of services, from design and development to clean room injection moulding
and assembly. We also offer a complete package of quality assurance and regulatory compliance services.
Our state-of-the-art facility is equipped with the latest manufacturing and testing equipment. We have a dedicated team of engineers and technicians who are experts in medical device manufacturing. Seaskymedical is ISO 8 Cleanroom certified, and our products are CE marked.
We will be the reliable partner for the next medical device project. Don’t hesitate to contact us today. We will be happy to discuss the requirements and provide a proposal.