Molding is one of the significant steps of manufacturing, especially the process of injection molding. The process requires a metallic mold with a cavity of a specific shape. The thermostat plastic is inserted in the molten form which further solidifies. The process can not only create small detailed objects but also large voluminous parts.
Such molding can be completed within a short span and is highly cost-effective. Two of the most essential molding procedures: Insert Molding and Overmolding have been discussed in detail below.
What Is Insert Molding?
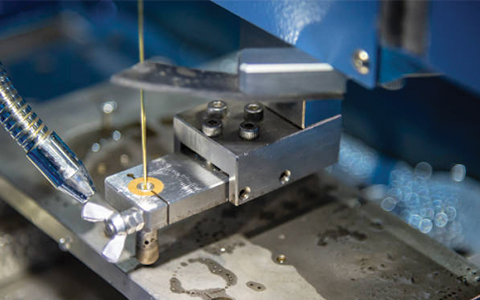
Plastic parts are cost-efficient and thus form an important component in several industries from automotive to medical. This has increased the significance of the process of Insert Molding, especially for the medical injection molding company and other sectors.
Insert Molding can be defined as the procedure of molding a thermoplastic material around a specific object or an insert as it may be called to create a finished product or part that can be used in different materials.
These are mainly simple objects or inserts such as a rod, thread, or battery. The different materials utilized in the process can be either metal or plastic or sometimes a combination of both.
It does not use regular plastic, but rather engineering plastic that is not only wear-resistant but also provides better tensile strength.
Moreover, metallic substances used for molding provide better conductivity and strength to the overall object.
Adopting this method can be quite beneficial for several other processes that occur in your organization as it reinforces the mechanical characteristics of plastic products.
Advantages Of Insert Molding
Getting different products molded into one can really have advantages like none.
A large variety of products such as medical consumables and disposables, screws, magnets, tubing, and many more can be inserted inside the molds.
Some of the beneficial characteristics of insert molding that can prove to be profitable for your company have been mentioned below.
- It enhances the design and durability of the product.
- The accuracy with which the objects can be placed within the molds cannot be achieved in other processes. Thus the product created is stronger and has better reliability.
- It’s a one-step manufacturing process, thus there is a scope of minimal to no error in molding the objects.
- Plastic products are 50% lesser in weight as compared to metallic ones. Getting a product that is both strong and light makes it a preferable process. Being fuel-efficient and easy to use, a medical plastic injection molding producer and several other producers from different sectors adopt this process.
- The process can mold products that are tinier and thinner without compromising on its durability.
- Cost-efficient as they not only allow the use of cheaper materials for production.
- There is no need for a second assembly step in insert molding. The entire process is integrated into a single step.
Disadvantages Of Insert Molding
Although your organization can leverage the process of insert molding, there might be certain shortcomings too. Some of the cons of the process have been mentioned below.
- Several sessions of the designing and modeling take place before molding the final products, this might lead to a higher initial cost.
- Although it’s a one-step process, the entire procedure of designing, molding, and testing the parts might take up to several weeks.
- In the case of larger parts, the process will require huge machines that might be expensive to purchase for an organization.
Insert Molding Process
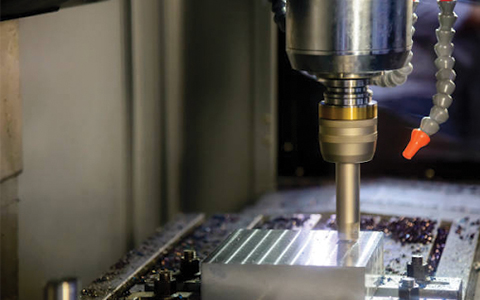
For a successful procedure, it is always appropriate to use advanced machines in molding that are specifically designed for the insert molding process..
Utilizing any other machine for molding might compromise not only the entire process but also the finished product.
The process begins with placing the inserts into the mold, after which thermoplastic is inserted to coat it and form a part. Further, it is kept aside for a while until the entire part solidifies.
Once the solid form is obtained, it is removed from the mold. Even the slightest error in the process can lead to the failure of the entire process.
It is essential for the objects inserted or the inserts to survive the process of molding. Often there might be a failure due to increased pressure and temperature.
The design solutions not only protect the inserts but also ensure an accurate design formation.
Insert Molding Applications
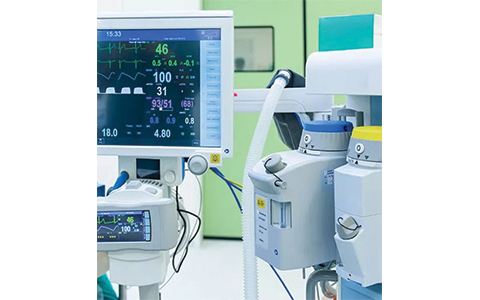
With an increase in demand for plastic parts, insert molding is used in a variety of industries such as safety, defense, electronics, aerospace, medical, pharmaceutical, and many more. Its application in such industries includes:
- Medical equipment parts and instruments such as tube valves and needle
- Knobs used in the controls or appliances
- Electrical parts and devices
- Military equipment
- Threaded fasteners
The metallic inserts that have to be molded into plastic parts include:
- Clips
- Screw
- Surface Mount Pads
- Studs
Materials Used In Insert Molding
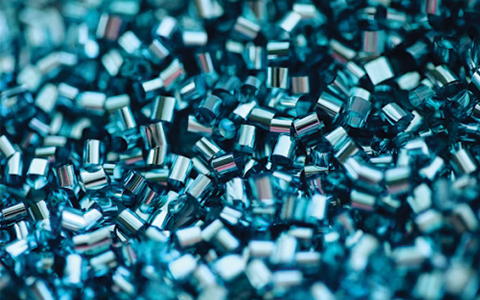
The Insert Molding mainly utilizes the most thermoplastic resin that is moldable and at the same time compatible with the process.
The inserts are mainly made from typical metals such as brass, stainless steel, or aluminum. In the case of threaded inserts, one can consider a variety of sizes.
What Is Overmolding?
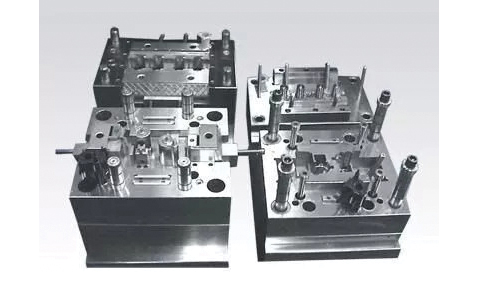
Overmolding can be defined as the multi-step process of injection molding plastic, commonly rubber-like plastic TPE over the other object or substrate as it may be called.
In this process, two or more objects are molded over one another. This substrate is mainly an already injection-molded plastic part, however other materials can also be molded.
This process is often termed the two-shot molding processing since it has two steps involved.
Advantages of Overmolding
In comparison to the other molding processes, overmolding can be a lot more beneficial for your business as it utilizes a wide range of products.
Some of the advantageous features of the process that can enhance the functioning of the different parts created from it have been mentioned below:
- Strong adhesive nature allows for better fixing between the components.
- The finished products of this process are compact and also involve a lesser labor cost while production
- It has a strong resistance against UV and other harmful chemicals.
- There is a lesser emission of noise and vibrations while the process
- The great electrical insulation offers reduced risks during overmolding.
Disadvantages Of Overmolding
Overmolding can be a great choice if your business involves large production and multi-layered designs. However, there are certain limitations and drawbacks to this process.
Some of them have been enlisted below.
- There can be huge initial costs spent mainly on designing and modeling.
- It can be often time-consuming as well as an expensive manufacturing process.
- The two-step process can be complex for some.
- There has to be a production of a large number of parts to distribute and balance the costs.
Overmolding Process
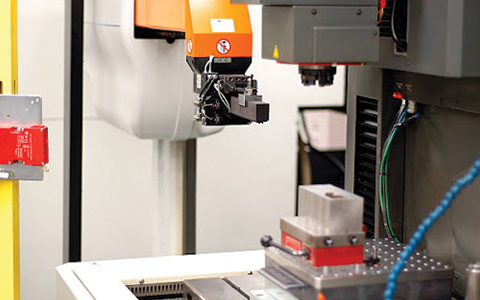
The process of overmolding leads to the formation of a single component by combining two or more materials. These raw materials can either be similar or different.
The process is divided into two parts. The first step is to substrate while the second one is molding.
The substrate forms the base material of the process which is molded over with another material. In some instances, there might be more than one overmolding as well for better strength and grip.
The number of overmolds mainly depends on the type of the product and the design that needs to be created.
Overmolding Application/Industries
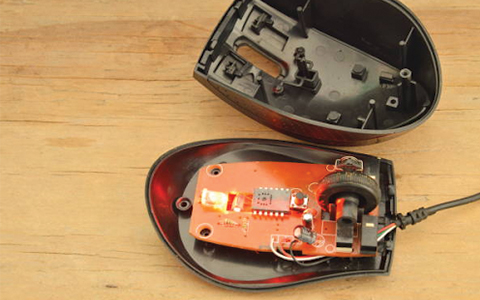
Considering the distinct advantages of overmolding in different industries, nowadays a large number of overmolding factories are being set up.
The different industries that utilize the process are electronic, medical, mechanical, and many more.
Some of its applications include:
- Medical device clean room molding for injections and other medical instruments.
- Window reveals
- Electronic parts and devices
- Parts with soft grips.
- Hardware Tools
- Car trims
Materials Used In Overmolding
Different materials are used in creating a compact design from overmolding. Some of the most common materials utilized in the process are- High-Density Polyethylene, Acrylonitrile butadiene styrene (ABS), PEI Resin, PBTR Resin, and other compatible materials.
Compression Molding Vs Injection Molding: Which One Is Better For Your Need?
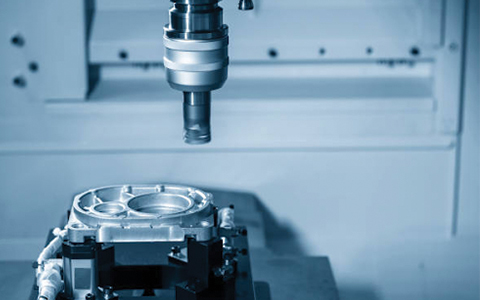
Molding can be considered the most common process of manufacturing that utilizes liquid materials and transforms them into a solid essential component.
There are different types of molding. The process of molding differs for each. The two common types of molding include compression molding and injection molding. Both are molding processes yet different in several aspects.
Compression molding is a process that involves heat and pressure. In this process the raw material is placed inside the mold and heat is applied to it.
Further plugs are inserted towards the top of the mold not only to seal it but also to apply adequate pressure for compression.
Thus with appropriate heating temperature and pressure, a new component is created inside the mold.
Injection molding mainly includes injection technology for molding. In this process, the raw materials are injected inside the mold, wherein a screw further moves the material in the hopper.
Although there is heat and pressure applied to the material it is not as much as the compression molding.
- Production Speed
The process of compression molding has the capability of high volume production. It takes place at a temperature of 350 degrees Fahrenheit and a pressure of 100 PSI with a curing time of 3 minutes. Once the raw material has been cured the mold is opened and the finished product is removed from the mold.
On the other hand injection molding is a quick method and the entire process can end within the range of two seconds to two minutes.
- Material Selection
Compression molding mainly involves thermoset components such as polyester, polyurethane, melamine, epoxy, and alkyd resins.
The materials selected for the injection molding have insulant properties, are resistant to harmful chemicals, are cost-efficient, easy to use, and have a higher strength. Some of the raw materials used in the process include Polypropylene, Low-Density Polyethylene, High Impact Polystyrene,, and more.
- Different Molding tools
Some of the common tools used for Compression molding include high potential., 2-part metallic tools and plugs are required for applying heat and pressure to the material. The component is created in the shape of the tool and can be modified accordingly.
The different molding tools required in injection molding include bolts, moving half-back plate, moving half support plate, ejector plate feet, risers, bolster sleeves, and guide brushes.
- Cost
A typical compression molding would cost between $750 to $1500, other factors influencing the cost include production volume, design, and material.
A simple injection molding, low-volume production might cost between $1000 to $5000 based on the product to be formed. Some of the factors that largely influence the cost of molding are material, complexity, and size.
Injection molding can be considered the best process of molding as per the needs, especially in terms of production. It can not only create smaller and thinner parts with accuracy but also work well with larger ones.
If you wish to achieve versatility, durability, consistency, and reliability, then injection molding is a beneficial process for you.
Contact Us for More Details About Plastic Insert Molding & Overmolding
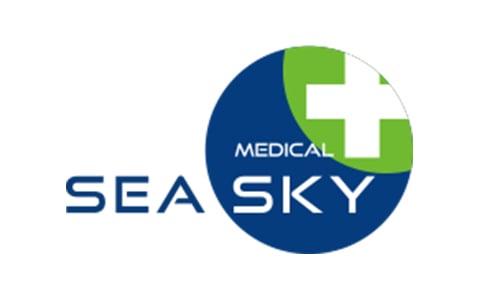
Both the processes though appearing similar have a lot of differences between them. There are several important considerations that are needed, and you may need a reliable manufacturer for the same.
Seasky Medical is a reputable injection molding organization that provides efficient molding for medicinal or surgical equipment. Some of the factors that make us a preference of several businesses in the medical field are:
- We interpret your need and try to create a detailed model and design for efficient product development.
- Our professionals work closely with the resin suppliers to get the best and most suitable raw materials for the products.
- With advanced technology and great expertise, our skilled experts mold the material with utmost precision to meet your business requirements.
- We have ISO 8 cleanrooms to meet the cleanliness requirements for medical products.
Contact us if you need this kind of service.