
Although plastic has been used to make a huge variety of consumer goods, its potential applications go far beyond making toys for kids or storage containers. Today, industry specialists use plastic to produce everything from synthetic human body parts to vehicle parts.
Such products require the utmost attention and accuracy to create. When manufacturers start creating these crucial components, plastic molding ensures peak performance.
Different medical injection molding companies have different specifications, demands, and limitations. Due to this, a variety of plastic molding alternatives are available, each with unique advantages and features. What sort of molding method is suitable for a certain product is frequently determined by the specific requirements of an application. Compression molding and injection molding will be the main topics of this article.
What Is Compression Molding
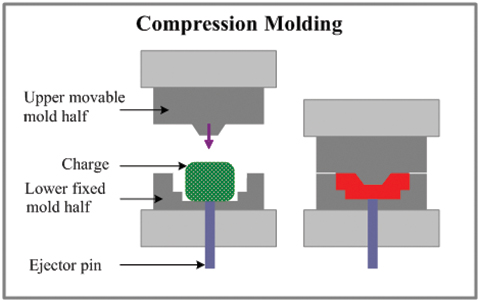
The cavity of a heated mold is filled with preheated material, such as thermoset resins, which are subsequently pressed down or closed by pressure. After that, the resins are dispensed throughout the mold and held at a high, predetermined temperature to be cured under pressure.
As a result, a premium-grade, stiff, and long-lasting rubber that is employed in many industries, including the automotive industry, is produced. In order to make massive volumes of gaskets, seals, and grommets, compression molding is frequently utilized. Natural rubber, silicone, and synthetic rubber such as EPDM are often used materials.
Compression Moulding Advantages and Disadvantages
- Advantages of Compression Moulding
Compression molding is regarded as being both economical and extremely effective, much like cleanroom injection molding. In comparison to other production methods, the procedure is straightforward, and it frequently results in less expensive component production. Additionally extremely adaptable, compression molding is utilized to make items of different complexity, lengths, and thicknesses.
Many goods produced by compression molding are more durable and resilient than those produced using other molding procedures because the process frequently uses high-strength materials. It generates less waste, benefiting both the environment and customers’ wallets.
- Disadvantages of Compression Moulding
- Better suited to creating simple parts only.
- Flash, which must be manually cut, causes the operation to go more slowly.
- High labor charges
- Slower than the injection molding procedure
Compression Moulding Process
In the compression molding procedure, plastic is put within a heated mold. The mold is then sealed, which causes the plastic to heat up and compress into the correct shape. The final product’s integrity and shape are guaranteed by the heating procedure, commonly known as curing. Products are taken out of their molds after cooling.
Compression Molding Applications
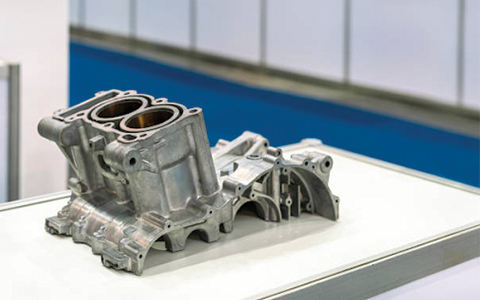
The best method for creating stronger, more resilient parts is compression molding. These days, the technique is frequently crucial to the production of the appliance and automotive parts. Additional uses include:
- Garment fasteners
- A body suit
- breaker switches
- Stove handles
- Disposable dinnerware
- Switchgear for electricity including electronic parts in a container
Materials Used in Compression Molding
Compression molding often works best with the following thermoset materials:
- Bulk molding compound (BMC)
- Sheet molding compound (SMC)
- Diallyl phthalate (DAP)
- Epoxy
- Phenolics
- Silicone
- Thermoset polyester
- Shoddy pad
- RUS underbodies
- Vinyl ester
What Is Injection Molding

Melted plastic is injected into a stainless steel mold during fabrication to take on the desired shape. To create the product, the mold is loaded with a variety of personalized cavities.
The material starts filling the cavities and the rest of the mold after the melted plastic has been injected. The items are allowed to cool before being expelled by pins.
Injection Molding Advantages and Disadvantages
- Advantages of Injection Molding
Plastic injection molding is frequently used by businesses that need complex products or big production volumes because technology makes it simple to accomplish high levels of production while maintaining relatively reasonable prices. Once production gets going, the cost per part dramatically decreases.
Of the molding techniques now on the market, this method is also regarded as the most adaptable. It makes it simple to produce goods of diverse sizes, shapes, and styles. Numerous production-related factors can be changed with relative ease if a project requires a high level of customization. To make customization simple, manufacturers employ a range of plastic resins, additives, and finishes.
Among injection molding’s further advantages are:
- High levels of personalization and adaptability
- Low manufacturing costs
- Effective and trustworthy procedures
- Strong and long-lasting finished goods
- Disadvantages of Injection Molding
- Higher tool prices
- Costly materials
Injection Molding Process
Feed hoppers, heaters, an injection unit, a clamping unit, hydraulic cylinders, and more are necessary for tpu injection molding. The raw materials are first processed into pellets or resins that can be machined before being fed into the hopper. Consistent heating precedes the materials’ careful transfer into the mold or workpiece, where they are formed. The remaining side of the mold is fixed into place by the clamping unit. The finished product is chilled after release before being expelled from the die.
Injection Molding Applications

Injection molding is frequently utilized for a range of applications due to its adaptability. The procedure can be used to improve everything from medical plastic components to tiny, delicate auto parts. Other instances of applications include:
- Drinks and food packaging
- Aeronautical parts
- Automobile-related goods
- Door and window parts
- Components for avionics
- Assembly of cables
- Components of point-of-purchase displays
- Encapsulations
- Technical prototypes
- Instrumentation
- Dental and medical supplies
- Components of medical laboratory tests
Materials Used in Injection Molding
On the other hand, the following materials suit injection molding the best:
- Acrylonitrile butadiene styrene (ABS)
- Polystyrene
- Polypropylene
- Polycarbonate
- Polyethylene
- Nylon
Compression Molding vs Injection Molding: Which One Is Better for Your Need?
- Production Capacity
Compression molding is best for high-volume manufacturing while injection molding is best for various volume production in terms of production capacity. Injection molding would be recommended for applications that don’t necessarily require numerous prototypes of the same sort.
This allows you a low-cost way to figure out what modifications or revisions the product needs before full manufacturing begins.
However, depending on the type of raw material used, both injection and compression molding can be appropriate for a range of production levels.
- Precision
The best part about injection molding is that the precise dimensions mean that the molds that are expelled from the machine don’t need any additional post-processing. Steel, which has a high strength and hardenability grade, is a dependable material that may be utilized to create the injection molding die. This indicates that they are less likely to deform, especially after repeated use, which could influence the shape of the finished mold.
In contrast to compression molding, the machine operator has simple control over the amount of heat and pressure used throughout the molding process. They can more easily produce prototypes as a result, which have more uniform shapes and need less fine-tuning.
- Complexity of Models
In comparison to compression molding, the injection molding process can create models and designs that are far more complicated. In light of this, using the injection molding method to test out design concepts is more practical. Additionally, injection molding gives you the chance to test the finished product to evaluate how well it performs in the real world.
Bottle caps, rounded inserts, kitchenware, electrical casing, and similar items are some of the most typical products made as a result of the compression molding technique. The minimally complicated components and processes are the primary reason for the simplicity of designs across all compression-molded goods.
In the meantime, injection molding enables the production of goods including sporting goods, safety equipment, plastic containers, headphones, and other plastic replacement parts.
- Lead Time Length
Despite what was previously stated, compression molding has substantially longer lead times than injection molding and is better suited for usage in high-volume production. Lead time is simply the amount of time that passes between the start and finish of a process.
Injection molding is far more dependable for clients who need to try out a provided prototype in a single day because the production procedure is shorter. Before they can even determine whether the product is fit for use, they don’t have to wait long.
Manufacturers can accommodate other essential elements of their business because of the short lead time. They can handle a variety of machines at once and raise the facility’s overall productivity levels.
- Cost
Both compression molding and injection molding are effective, affordable, and flexible processes for producing high-quality components. Despite their similarities, the two varieties of shaping each offer different advantages. The following guide provides a general overview of both approaches and some recommendations regarding which approach to employ for large components.
Compression molding is better suited for simpler components and can be slightly less consistent than injection molding. Although both molding techniques may produce products in large quantities, compression molding is more cost-effective for producing straightforward yet sturdy components. Compression molding also has the benefit of making extra-large items more inexpensively.
Contact Us for More Details About Plastic Injection Molding
Compression molding vs. injection molding has been the subject of a protracted debate about which technique is actually more effective.
Compression molding uses simpler machines, making it possible to produce a variety of basic plastic products. On the other hand, due to the intricacy of the injection molding process, it is possible to carry out a wide range of tasks to produce goods that are needed by numerous industries. Knowing which of the two approaches can best satisfy your needs is the key to choosing between them.
Want to know more about the procedure for injection molding? You can get assistance from Seasky Medical, the medical plastic injection molding company. To get in touch with them, click here.