In plastic mold manufacturing, injection molding and extrusion are two common methods used in producing plastic products. There is a slight similarity between these two methods, which is why most people think they are the same. But they are not; they are way different.
In this post, we will be sharing with you the differences between injection molding and extrusion.
History of Injection Molding and Extrusion

Injection molding is a manufacturing technique that involves injecting molten plastic material into a mold to form a shaped item. In 1795, Joseph Brahman invented the process. But later in the year 1820, Thomas Burr gave the process more life by building the first hydraulic press. Even then, the process was only patented on paper, not until 1894 when it evolved.
The evolution involved the use of copper and brass alloys and this led to the final establishment of an injection molding process in the 1930s. However, thermoplastic and thermosetting plastics are considered to be more effective than metal alloys. Since then, it has been the most widely used manufacturing method in the plastic industry.
Extrusion molding, on the other hand, was invented in the early 19th century. It first started in 1820 when Thomas Hancock produced a rubber masticator that was designed to recycle processed rubber waste. And in 1836, Edwin Chaffe created a two-roller machine for mixing additives into rubber.
However, the first thermoplastic extrusion did not happen not until 1935 when Paul Troester and his wife Ashley Gershoff who were based in Germany carried it out.
What is Injection Molding

Injection molding is a method of producing a wide range of parts from plastic. Despite the fact that the method was invented in the 19th century, it is still one of the greatest ways to produce complex parts while minimizing costs. This is why it’s not a surprise that the global market for this method was valued at about 260 million dollars, with forecasts for continuous increase in the near future.
Injection molding involves producing identical replicas from custom-made molds. Just like CNC molding, injection molding is a versatile process that allows for a wide range of materials and finishes, making it a popular choice in a variety of industries. Because of its versatility, it is used for some of the world’s most demanding manufacturing projects, such as parts for aerospace, automobiles and medical device molding. It can also be used to make medical items that match the exact specification given to a medical injection molding company.
What is Extrusion Molding
The word “extrude” signifies “to push out,” and that is exactly what happens during extrusion molding. The process of extrusion molding involves the pushing of molten material through a die cavity to form an extruded shape. It’s essentially the same as squeezing toothpaste from a tube. This molding method is used to make anything that is long with a fixed cross-sectional profile.
Just like injection molding, extrusion is a commonly used manufacturing method in many industries, and it can be done with almost any thermoplastic. Examples of items made with this method are straws, pipes, fence sections, and window frames.
Differences between Injection Molding and Extrusion
Now, let’s take a deep dive into injection molding vs. extrusion to know more about both methods – how they work, their advantages & disadvantages, their applications, the types of plastics they use, and so many more.
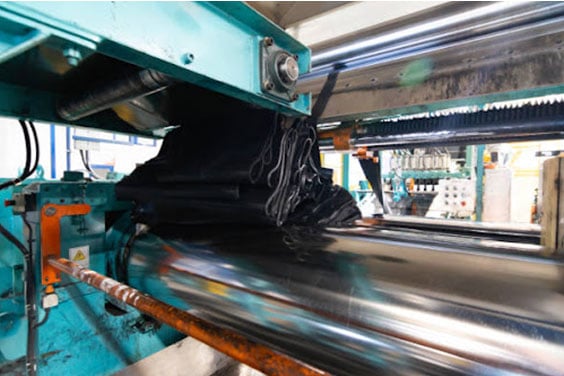
Process
In injection molding, the plastic resin is poured into the hopper, which then moves the plastic pellets from the feed section to the compression zone, where frictional heat is generated to make the melt. After this, a reciprocated screw is used to force the plastic through a protracted chamber. Then the melt is pumped into a closed, cooled/hot mold through the nozzle. When the mold is filled and pressurized, cooling takes place. Finally, the ejection cylinder releases the clamps on the mold and pushes the molded part out onto a conveyor.
In extrusion molding, the plastic resin is poured into the feeder. Usually, on the outer casing, the feeder is headed by heat jackets, and this causes the resin to be melted into a thick, uniform liquid. Also, a die with a small cavity is fixed to the feeder’s end; the molten resin is forced into the die cavity and pushed out from the other end. The molten resin travels in a screw-thread pattern from the feeder to the die, ensuring equal distribution. As the pushed-out part cools down, the desired shape of the product is formed. You can now cut it into the size you want.
Mold Tooling
Injection molding tool design is primarily made up of two units – the injection unit and the clamping unit.
On the other hand, extrusion mold tooling is composed of the feeder and the heated jacket.
Advantages
The most significant advantage of injection molding is that it can be used to manufacture 3-dimensional plastic items. Apart from that, this method is fast, capable of capturing the intricate details and complex geometry of the mold, and enables manufacturers to use several plastic resins in the production of products. In this method, when a product has been completely molded, you can still improve the strength and minimize waste materials by recycling them.
Extrusion molding is the fastest and most efficient method for manufacturing long continuous plastic parts. It’s most suitable when several lengths of the same profile shape are needed. The plastic remains hot when it is removed from the extruder, which enables post-extrusion fabrication. Extruded products have very smooth surfaces that do not need extra finishing or clean-up after production.
Disadvantages
The lead time might be lengthy as mold design, reviews, testing, and tool manufacturing take time. Although once these are completed, it takes very little time to manufacture the needed products. And unless a proficient team that knows your industry handles this method, there will definitely be some constraints in the designing and raw materials procurement aspects. So, it’s best for a medical plastic injection factory to handle medical parts and other industries to handle their respective parts.
In extrusion molding, the plastic can inflate after it has been removed from the die, and it has the likelihood of getting distorted. Also, the nature of this method places limits on the kinds of products it can manufacture; it can be used only for linear polymers. This is because rather than using custom-made mold cavities to shape the final form, it uses a die.
Application
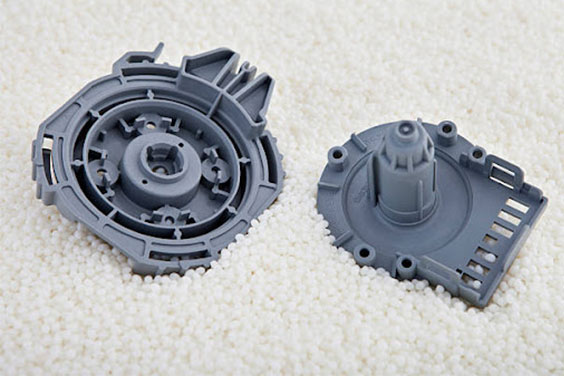
Injection molding applies to virtually all kinds of plastic product manufacturing. In fact, if you look at any plastic in your house, there is a high probability that it was made through injection molding. This method is applicable for both part manufacturing and continuous manufacturing. Some of the several products made through this method are toys, bottle caps, knife handles, baskets, casings, chairs, vehicle dashboards, buckles, etc.
On the other hand, extrusion molding is only applicable for continuous manufacturing. Some of their applications include hoses, straws, door frames, tubes, pipes, and cable housing.
Plastic Used
Injection molding uses both thermoplastic and thermosetting plastics. This is why you can make both fixed and recyclable parts through this method. Some of the numerous plastics used are ABS, nylon, polypropylene, polycarbonate, acrylic, polyethylene, etc.
Extrusion molding, on the other hand, only supports the use of thermoplastics. This is because the method is focused on producing recyclable products. A few of the plastics used are ABS, PVC, polypropylene, polyurethane, clear acrylic, thermoplastic rubber, and thermoplastic elastomer.
Characteristic Comparison
As earlier mentioned, injection molding takes the form of 3D products. Once the molten resin is poured into the mold, it will solidify, and produce a 3D shape product. This is one of the major advantages that it has over extrusion molding.
Rather than producing 3D shapes like injection molding, extrusion molding is only capable of producing 2D shapes. Also, extrusion gives room for additional fabrication and adjustments to the product, from cutting cross-sections to shaping the parts into specified product shapes, just like toothpaste tubes. Whereas, products always come out of the mold completely formed.
Cost
The price of an injection molding machine is expensive, resulting in this method’s high cost of production. This is why it is not suitable for low volume production as the cost only reduces when a higher volume of parts are produced.
Extrusion molding cost of production is low due to the benefit of gathering and reusing extra plastic. Because of the features of the plastic used, the molded items can be recycled, making the process more sustainable, which cuts down excess plastic and lowers costs.
Conclusion
The question of which is the best between injection molding vs. extrusion doesn’t always have to be an unending argument. Both of them have their distinct purposes and benefits, and they are both applicable to plastic part manufacturing.
However, some noticeable differences between injection molding and extrusion that cannot be avoided are the fact that injection molding can create complex 3D shapes, while extrusion is best at 2D shapes. Also, injection molding cannot be used to manufacture the typical cross-sections that extrusion molding will produce accurately.