Hospitals, laboratories, and every sector related to the pharmaceutical manufacturing industry are being put under strict regulations as the devices they produce have a great part to play in the determination of life and death. The assurance that a person will live is dependent on the efficiency of these sectors as their products are used to administer treatment and surgical operations. This made regulatory agencies increase the standard that their products must meet.
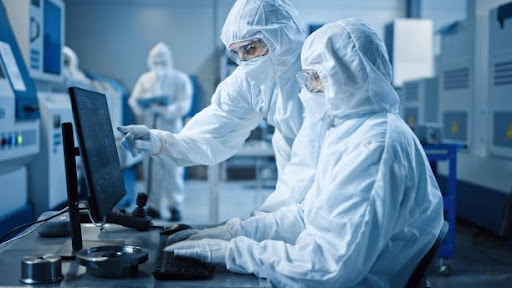
Medical device injection molding companies are now under compliance to manufacture products in a clean room. Medical injection molding clean rooms help to ensure the quality of devices as all external factors like air particles, dirt, and moisture are prevented from interfering with the production.
In the remaining part of this post, we will discuss what a clean room is, why you need a clean room, and the things to consider when building a clean room.
What is a Clean Room
A clean room is an enclosed area within a production or research facility that is constructed to control air pollution, pressurization, temperature, humidity, staff access, and other factors that could contaminate the production process.
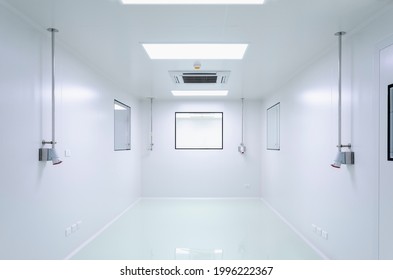
It is a sterile work environment where particles and other pollutants are prevented from interfering with the production process. Clean room production makes devices manufactured safe to be used inside and outside the body. Medical device production, scientific research, biotechnology, food packaging, and chemical processing industries are examples of many of the industries that use clean rooms.
A clean room is an investment that can be a valuable asset to an industry’s strategy, so the construction and design should be carefully considered. It could be a positive-pressure clean room or a negative clean room.
Approximately 90% of the clean rooms built are positive-pressured; they are built to keep pollutants out. A fan-powered High-Efficiency Particulate Air (HEPA) filter that eliminates particles as little as 0.3 microns is placed at the ceiling level. This results in a pressurized room in which the air pressure inside the room is higher than the air pressure outside the room, resulting in positive pressure.
The air and the pollution in the room are then pushed out through the vents of the lower part of the room’s wall or through the door when it’s opened. What this means is that the air and the pollutants from the production processes are continually expelled. Furthermore, the air leaving the room is at such high pressure that it prevents air and pollutants from entering.
On the other hand, negative-pressure clean rooms are built when the plan is to prevent pollutants from going out of the room. It’s used in cases of infectious diseases, hazardous procedures involving chemicals, and flammables. While building the room, the High-Efficiency Particulate Air (HEPA) filter will be inverted, causing air to be pulled out through the enclosure. Vents and other openings are used to draw in air and because of the force of the air coming in, pollutants won’t be able to leave.
However, in this post, we will be focusing on the positive-pressure room because it’s commonly used in manufacturing processes like medical device molding and micro injection molding.
Why do You Need a Clean Room
A clean room is not only needed by manufacturing industries, it is greatly beneficial for individuals too. You can have a clean room in your home, you don’t necessarily have to be a medical practitioner, science researcher, or the likes.
There are several pollutants flying in the air and they become more noticeable when you have a nostril issue like continuous sneezing, catarrh, or an over-sensitive smell sense organ. This makes a clean room important for you as you can shield yourself from inhaling polluted external air.
Also, it can be used when there’s an active fire in your environment. It could be from a burning bush or a burning apartment. A clean room will shield you from inhaling smoke.
You need it as well when the Air Quality Index notifies you that the smoke level is harmful and is expected to stay that way for a while. In fact, in a case like this, local authorities may recommend that you remain inside your house or set up a clean room. While staying inside the house, and staying in a clean room, your exposure to smoke is immensely reduced.
Who Needs a Clean Room
Having stated that a clean room is beneficial to everybody, it’s more than a necessity for some people. These set of individuals are:
- People suffering from heart or lung disease. Individuals suffering from diseases like heart failure, asthma, and ischemic heart disease are at greater risk when they are exposed to smoke.
- Older adults. People who are very old are prone to having heart and lungs related diseases faster than young people. This means that they shouldn’t be exposed to smoke as it’s a deadly risk.
- Children and teenagers. Young people’s respiratory systems are yet to be fully developed and they breathe in more air than adults. Breathing more air entails breathing in more pollutants. This makes them prone to suffering asthma.
- Diabetes patients. People suffering from diabetes are more than likely to have heart issues, this means that they need to breathe in less polluted air.
- Pregnant women. People with babies could be endangering their life and that of their offspring if they inhale bad air.
Things to Consider when Building a Clean Room
Building a clean room is quite different from traditional construction projects as the standards and criteria that are to be met are high. Professional standard organizations like the Food and Drug Administration (FDA) stipulate guidelines that must be followed to ascertain laboratory consumables and medical consumables suppliers’ products are safe for human use. These guidelines serve as a template for building a clean room that meets the required standard of a safe production site.
The intended application, acceptable particle concentration, production method, and cost must all be carefully considered when designing a clean room. Also, the design team and the whole personnel that will be using the clean room must collaborate to build the production space together.
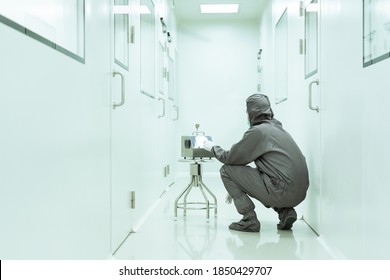
Below are the clean room injection molding requirements that should be put into consideration.
Type of Clean Room
As stated above, there are two types of clean rooms – positive-pressure clean room and negative-pressure clean room. Before building your clean room, you must have been clear on the type you want. You should ask yourself if you want the pollutants to be contained in the room and not leave, or if you want the pollutants to be expelled from the room through the vents and the door.
However, this depends on the type of activity you will be doing in the clean room. For instance, if it’s about medical plastic products, then a positive-pressure clean room is most suited, but if it’s about hazardous productions like infections and chemical reactions that are harmful to life and the environment, your whole operation better be contained in the production room i.e., a negative-pressure clean room is most suited.
High-Efficiency Particulate Air (HEPA) Filters
These filters are essential for keeping pollution under control. They can filter particles as little as 0.3 microns with a minimum particle-collective effectiveness of 99.97 percent. To remove airborne pollutants and provide fresh air into the room, the HEPA filters are usually used to circulate the air.
Recirculation Air System
The recirculation air system that you will need is dependent on the size of your clean room. After air is blown into the room, the whole of the room needs to be circulated with the air. This system must be designed to provide sufficient and conditioned clean air into the room to meet the production professional standards.
Air Exfiltration Flow
Since most of the clean rooms are positive-pressured, air has to go out. So, you need to consider the outlets through which the contaminated air will go out. During the building of your clean room, the design team in conjunction with you should have a plan of the places through which air can be expelled, the size of the openings, and the amount of air that can be expelled through those spaces.
Majorly, vents and doors are being used as outlets. The vents are usually located at the lower part of the clean room’s wall. After air is blown into the room, the air transports the pollutants towards the floor, and then they go out through the built-in vents.
Also, air can be expelled through the door when it’s opened. Note that the door is not to be opened always, but once in a while if the vents are not very effective.
Application
The fundamental purpose of building a clean room is to improve product quality or yield. Several production methods now necessitate a regulated environment in which the amount of dust and filth in the manufacturing area is kept to a minimum. Medical instrument production and packaging, food preparation, and some military applications are just a few of the industries with stringent environmental standards.
You must be aware of the specifications for your unique product or process. If the product you are making is controlled by the government, or you’re working with a private company that demands a certain level of cleanliness, the clean room requirements should already be written, so look through it for the things you need to put into consideration.
Structure of the Clean Room
The clean room should be structured in a way that production activities will be carried out without contamination. The pathway and movement of people and materials should be considered as clean room staff are the room’s largest pollution source. All critical manufacturing processes should be kept away from the door or in close proximity to pathways.
The most important zones in the clean room should have a single access. It shouldn’t be connected to less-important zones that more staff frequent. In fact, SeaskyMedical, a medical device clean room molding company reduces staff contact with the production process and maintains cleanliness by separating the feed from the injection and equipping the production line with automated equipment like robotic arms.
Cross-contamination should be prevented from occurring. Contamination could happen and be spread within the raw material inflow, material processing, and finished product outflow.
Clean Room Classification
It is important to understand the fundamental clean room classification standard as well as the particulate performance requirements in order to choose a befitting clean room classification. These classifications as well as the maximum number of particles allowed at various particle sizes are specified in the Institute of Engineering Science and Technology (IEST) Standards 14644-1.
The classification of a clean room has a significant impact on the cost of the construction, maintenance, and energy in a clean room.
High-Efficiency Flexibility
A flexible clean room allows for faster equipment changeover, resulting in higher output, lower costs, and a lower risk of pollutants in the long run. There are various design considerations that can be used to make a clean room more adaptable to changes.
Wall chases can be employed to conceal unused ductwork, electrical utilities, and process operations. Bulkheads allow equipment or medications to be transferred across clean room walls without the risk of spillage or damage. Struts can be employed to free up valuable floor space.
Clean Room Pressurization
Your clean room should be kept at a static pressure higher than ambient pressure in order to prevent wind from entering. Also, the air pressure should be adjusted such that air flows from clean zones to contaminated zones.
One exception to the positive differential pressure rule is that when dealing with dangerous compounds, such as hazardous chemicals, government agencies specify that the room should be kept at a negative pressure.
Room Space
The size of the room determines if the space will be convenient for you to carry out your tasks. You might need a large space because of the big machines you will need to place at strategic places. On the other hand, all you might need is a small room where you can produce products and easily meet the cleanliness standard.
So, this decision boils down to you comparing your activities and the cost of meeting cleanliness standards with the space of the room.
Space Air Balance
This has to do with adding all the airflow of the clean room i.e., the amount of air supplied or infiltrated into the room and the amount of air that’s expelled or exfiltrated out of the room. This is to determine the average amount of air that will be available in the room.
Temperature and Humidity Control
Temperature control is necessary to ensure that materials, instruments, and staff are comfortable. To limit particulate formation and potential contamination, clean room personnel wear smocks or full bunny suits over their normal clothes. Because of the additional clothes, they might feel uncomfortable if the temperature is not conducive.
Humidity control is required to avoid corrosion, stop condensation on work surfaces, as well as to minimize static electricity, and provide a comfortable working environment
Both of these controls are required for personnel comfort, thus striking a balance is important to maintain the best working condition for workers as well as the equipment.
Blower
To build a clean room, ensure you get a blower that can provide sufficient air pressure at the required airflow. Also, keep in mind that over time, particles will be stuck in your filters, thereby requiring additional pressure to maintain the needed airflow. To regulate your blower, you’ll need a large (6 Amp) knob.
Measurement and Instrumentation
Essential contamination parameters, such as particle count, airflow and air velocity, humidity, temperature, and surface cleanliness need to be measured. To do this, specialized devices and standards, such as the IEST standards are used.
Products Storage
You should have a ‘gray room’. It’s a room close to the clean room where you can store your work clothing, tools, equipment, products, etc. This room should also be clean as the items taken out of it will be used in the clean room.
Electrostatic Discharge (ESD)
Anything as simple as a human walking across the room can generate turbo-electric charges, which might mistakenly harm or destroy some things in the clean room. Static damage can be avoided and proper grounding can be implemented with the right packaging.
Cleaning specialists should collaborate with their staff to find out where these occurrences may exist and to avoid them. Insulating materials should be replaced where possible, and if necessary, install ionization technology. Also, there should be clean room specialists that will carry out a static audit to detect potential problems and their causes.
Consider Operations and Maintenance
When laying out the layout and the size of the clean room, keep the equipment’s serviceability in mind. Inquire with the maintenance crew and operators about how they plan to service and operate equipment. Nothing is more frustrating than having equipment installed and operational but unable to be serviced.
In cases of new equipment, confirm that they are compatible with the former equipment. Prior to design and equipment procurement, it is a good idea to hire an engineering expert to do a detailed utility study of the facility. Nothing is more disappointing than discovering after a project is completed that an existing air compressor is incapable of delivering at the quoted capacity.
Ensure Cleaning Solution Compatibility
Ensure that the equipment in the cleanroom can withstand the cleaning solutions that are sometimes harsh. Examine the compatibility of the cleaning solution with the floors, walls, windows, doors, and other utilities in the room.
The wall cleaning solution might not be compatible with the floor so if it drips on the floor, it may cause damage. In fact, most times, the cleaning solutions designed for these two parts (wall and floor) are incompatible.
Check Bio Seals
At pressure and class changes, double-check that all bioseals are intact. Always confirm; during the design review process and the commission process, still confirm.
Mechanical System Layout
The mechanical system layout, which accounts for up to 25% of the overall cost of a conventional cost of a clean room facility, is the most expensive component of the building as it incorporates a lot of parts. Recirculation air, heating and cooling system, process exhaust, and makeup air (MUA) system are all included in this system.
Although the exhaust system accounts for a lesser fraction of the mechanical system budget, it is arguably the most important to a clean room’s operational effectiveness. The design of the makeup air (MUA) system is driven by calculating the proper amounts of exhaust for each clean room and support area. The amount of exhaust is established after a thorough examination of the room, codes, and emergency requirements.
A hazardous production material (HPM) facility’s exhaust system must be built and installed to eliminate any potentially dangerous gas that may escape from the fabrication process.
The makeup air (MUA) system is very important to a good clean room design. It does not only change the air that is expelled from equipment, clean spaces, and support rooms, it also regulates clean zones’ humidity levels. Another function of the MUA system is that it keeps the clean room’s pressure under control.
The clean zones will normally be favorably pressurized in comparison to the surrounding zones, whereas the gas and chemical rooms will be negatively pressurized.
Conclusion
Clean rooms are very important for the manufacturing industry, especially for medical molded products manufacturing. Injection molding in a clean room helps to ascertain that the products coming out can be trusted to be used without causing harm. Professional standards organizations have reemphasized the importance of manufacturing devices in a clean room, and they’ve enacted guidelines that must be followed.
In this post, we’ve explained all that you need to know about a clean room – what it is, why you need it, who needs it more, and the things you need to consider when building a clean room. Also, ensure you follow the guidelines of professional standard organizations that pertain to your industry.