Cleanrooms are the specific areas that cater to the clean packaging and production needs of different businesses like medical, electrical, electronics, semiconductor, aerospace, biotechnology, etc. The exclusive processes like injection molding in the cleanroom can’t bear any single flaw, and hence this calls for dedicated cleanroom maintenance and cleaning process. But maintenance of a cleanroom sounds weird, especially when it comes to cleaning the sensitive equipment or interiors of the cleanroom.
Cleanroom maintenance is necessary for all industries that have dedicated cleanroom areas. However, not all businesses have the expertise in managing their cleanrooms and hence look for dedicated solutions. So today, we bring a detailed piece on cleanroom maintenance. Whether you want to do it independently or go for some service providers, you can understand all about it in detail. Let us start with the cleanroom cleaning procedure.
What isa cleanroom cleaning procedure?
Cleanrooms are making sensitive products or packaging for exclusive use in different industries. However, cleaning the cleanroom in any process like medical plastic injection is crucial and necessary. When it comes to the cleanroom cleaning procedure, some of the common steps that are standardized for any cleanroom include:
- The extended handle tacky rollers can clean the ceiling from top to down. The compatible solvents for ceiling cleaning of cleanrooms include isopropyl alcohol, deionized water, cleanroom-specific cleaners, disinfectants, etc.
- A cleanroom wipe can be used to clean the walls by the airflow. These wipes are made up of polyester knit, lint-free non-woven, etc.
- The cleanroom surfaces can be cleaned using hand wipes. The wipe dispensers are pre-saturated with 30% deionized water and 70% isopropyl alcohol. These wipe dispensers can be installed at different parts in large clean rooms.
- The cleanroom floors can be cleaned using isopropyl and deionized water. The autoclave bucket and wringer are ideal systems that can effectively decontaminate the cleanroom floor.
- Last but not least, businesses can set up Standard Operating Procedures (SOP) for the cleanroom cleaning process. The entire staff can be trained according to these training SOPs to reduce the potential pollutants from the cleanroom.
How to maintain cleanroom?
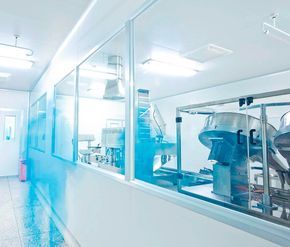
It is essential to understand the different maintenance procedures in cleanrooms when it comes to cleanroom maintenance. There are three central systems in any cleanroom that have specific maintenance needs, namely:
- Air filtration system: Any cleanroom has three filters in the air filtration system, namely, outermost filters, pre-filters, and HEPA filters. Some of the crucial air filtration systems that need maintenance requires:
- Air samplers
- Settle plates to check air quality
- Filter replacement
- Cleanroom equipment: Some of the crucial cleanroom equipment that needs maintenance include:
- Waste-disposal area maintenance
- Gowning room
- Fume hoods
- Boilers
- Replacing pre-filters
- Repairing any cleanroom furniture
- Cleanroom HVAC system: The effective running of the cleanroom HVAC system is mandatory to ensure that particles amount remains within the prescribed limit. It should meet the humidity, temperature, and pressure requirements. This HVAC system maintenance can be done bi-annually. The essential tasks include:
- Thermostat and control checking
- Heating elements check
- Lubricating moving parts
- Fan motor maintenance
- Electrical connections
- Gas or fluid leaks
- Cleaning coils and drain lines
How often should maintenance be carried out?
You know the procedure for cleanroom maintenance now, but how soon do you have to repeat this cleaning process? The needs of different cleanrooms are different based on their ISO guidelines or types of products manufactured by the medical molding company. For example, the ISO cleanrooms of classes 6 to 9 can go for annual checking, while the ISO cleanrooms of classes 1 to 5 can go for semi-annual checks according to the ISO 14644 and VDI 2083-9.1 guidelines. These guidelines specify the intervals of cleanroom inspection. Further, it is essential to look at the daily weekly cleanroom maintenance along with a required basis.
Daily cleanroom cleaning schedule:
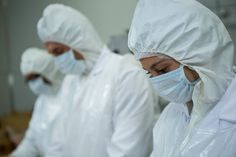
The daily cleanroom cleaning schedule may look like a rigorous process, but it is the primary type of cleaning. All you need to do is ensure that this regular cleanroom cleaning shouldn’t interfere with the facility’s generalized production or packaging processes. Some of the critical methods that can be included in the daily cleanroom cleaning include:
- It is ideal to start with a damp mopping of the floors followed by the HEPA filter vacuum drying of the floors.
- The next step can be to clean the walls using the same HEPA filter vacuum.
- All windows and pass-through in the cleanroom should be thoroughly washed and wiped using the cleanroom-specific cleaning agent only.
- All high-standard cleanrooms should clean the work areas at the end of every shift. It ensures further contamination of any residues or particles that may have accumulated in the production process.
- To ensure zero loss to the facility’s generalized production or packaging processes, it is essential to shift the supplies or products away. It helps obtain zero contamination levels and keeps the essence of cleanroom maintenance and the cleaning process intact.
- Weekly cleanroom cleaning schedule:
Weekly cleanroom cleaning schedule:
The weekly cleanroom maintenance schedule ensures the periodic cleaning of the tools and systems that are not in direct contact with the microinjection molding machineor products. Some of the critical methods that can be included in your weekly cleanroom cleaning include:
- Distilled water and a sponge can be used to wipe the cleanroom walls. It is ideal for vacuuming dry the walls after cleaning walls.
- Once walls are cleaned, the next step is to mop the floors using a high-grade cleanroom-specific detergent, HEPA filter vacuum, and distilled water. Hence, the sanitization of floors is ensured effectively in weekly cleanroom cleaning.
Cleanroom cleaning as required:
It calls for a systematic approach to cleanroom cleaning according to the needs. It may include some of the following processes:
- Replacing the sticky mats that may start leaving residue on the cleanroom floors. Any mat wearing down should be quickly returned to avoid particles in the cleanroom environment.
- Light lenses may start creating issues due to inefficient cleaning. Hence, the damp sponges can wipe off all the light lenses to ensure proper lighting.
- Many times, cleanrooms may develop residues or deposits on the ceilings. This calls for complete cleaning using distilled water and detergents for the clean roof.
Why do you need to maintain the cleanroom?
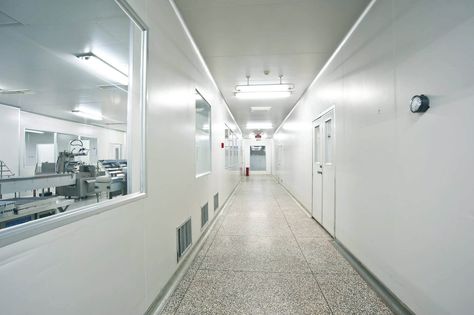
Before going any further, cleanrooms create multiple medical consumables, and it is evident that there is scope for zero error. Furthermore, the use of ISO 7 and ISO 8 cleanroom further stresses adherence to the stringent quality guidelines. Hence, some of the critical reasons that lay stress on the cleanroom maintenance include:
- Irrespective of the type of the cleanroom and its equipment, it is necessary for the dedicated cleanroom maintenance to improve its efficiency. Further, it is essential to ensure the longevity of equipment that is impossible without maintenance.
- Cleanrooms at higher levels of ISO ratings should offer high levels of sanitization. It ensures that contaminants and minute particles are within the prescribed limits. Hence, to ensure the cleanliness standards, ISO ratings, specific layouts, etc., are ideally managed by the cleanroom maintenance.
- Cleanrooms with lower levels of ISO ratings need maintenance and cleaning to ensure productivity and maintain the prescribed standards. However, these cleanrooms may not be highly sensitive to particles or contaminate volume like high ISO rating cleanrooms but still need dedicated maintenance.
- As prevention is better than cure, the prevention of cleanroom is better than crossing the safety and production guidelines to create rejected products. This prevention is best ensured with the regular maintenance of the cleanroom system and the equipment.
- It is of utmost importance for any semiconductor or biotechnology company to ensure regular and proper HVAC system maintenance to eliminate any issues with the products. The preventive maintenance eliminates the possible chances of critical points according to the run time of the cleanrooms. Different filters are part of the HVAC system and include:
- Pre-filters: These filters require replacement after every two months.
- Bag filters: These filters require replacement once in the year.
- HEPA filters: These filters can be replaced once in three years.
- The maintenance of bearings, sheaves, and belts in the cleanroom equipment or system is crucial for effective production or packaging activities in the cleanroom. The pre-maintenance ensures that work frequency doesn’t suffer and replacement can be carried out as quickly as possible.
- For the cleanroom working around the clock, it is necessary to separate the cleanroom maintenance into equipment maintenance and filter maintenance. The equipment maintenance can be supported with the use of pre-stored spared while the filter maintenance ensures the abiding of ISO guidelines as mentioned below:
Cleanroom Classes | Recommended Air Change Rate | Recommended % Ceiling Coverage for HEPA |
Class 1 | 600+ | 100% |
Class 10 | 360 | 100% |
Class 100 | 180 | 50-60% |
Class 1,000 | 90 | 25-30% |
Class 10,000 | 45-60 | 10-12% |
Class 100,000 | 20-30 | NA |
What are cleanroom cleaning supplies/equipment?
Any cleanroom maintenance is necessary to have high-end cleaning equipment. Ideally, all the cleaning equipment is improperly sterilized or unsuitable for a cleanroom environment. Hence, these cleaning supplies or cleaning equipment should be cleanroom-specified only. Further, all the equipment or tools like mops, brooms, cleaning agents, etc., should be brought into the cleanroom before starting the process. There should be at one time only that reduces the possibility of contamination.
Let us have a quick look at the top supplies or cleaning equipment to keep in mind for your cleanroom:
- Five-star cleanroom stairs: Any cleanroom maintenance and cleaning process is incomplete without using an elevated platform or ladder to reach the glove boxes, laminar flow hoods, or ceiling modules. Hence, all such stairs should be safe to use, facilitating the carrying of tools or replacement parts. It is ideal to go for stairs with a large footprint work platform for comfortable standing and organizing supplies/ parts.
The steep stairs of perforated electropolished stainless steel are ideal for ISO 4 cleanrooms. It offers a non-slip walking surface to ensure precise cleaning. There is no space for the particles to reside on the cleanroom stairs with sealed connections, continuous seam welds, and ultra-clean smooth surfaces. The wipe-down processes are streamlined, and it further helps eliminate surface contaminants.
When it comes to the mobility of the five-star cleanroom stairs, the all-stainless-steel mobile casters safely retract on the weight application. It can compensate for the uneven floors using non-sloughing nylon leveling feet on every corner of the stairs. It is easy to keep these stairs out of the way after completing the cleaning or maintenance process.
- Cleanroom- specified cleaning agents: It is necessary to select the cleanroom-established cleaning agents while mopping or wiping the cleanroom or its parts. Hence, these solvents or chemical agents must be neutral and non-ionic. It is ideal to go for the non-foaming ones to eliminate buildups on the equipment surfaces. Further, it should be taken care that all high ISO cleanrooms like ranks of ISO 5-7 must use sterilized disinfectants only. It eliminates the chances of infections from these cleaning agents that can worsen the cleanroom maintenance process.
- Corrode-free rugs: The rugs or scrubs that can shed or corrode surfaces are a strict no in the cleanrooms cleaning. The ideal products can be woven polyesters designed for cleanroom use only. It eliminates any corrosion from the rugs or scrubs that can work in the opposite direction for the cleanrooms.
- Contamination-free mopping system: After the list of equipment and cleaning agents, it comes down to the system that uses these tools and agents. Hence, the contamination-free mopping system should never scratch or contaminate the walls/ floors, etc. Always go for the mopping system to separate clean water and dirty water. Further, a detailed mopping protocol for cleaning the cleanroom using a mopping system can help solve the issues of adherence to ISO guidelines.
- Staff training: Last but not least is imparting training to staff for the different types of cleanroom cleaning processes. The properly trained staff eliminates any inefficiency in the cleanroom maintenance and cleaning process, ensuring optimized results. For example, the team should be taught about their positioning during cleaning as they may inadvertently restrict the HEPA filters used in the cleaning. Further, the staff should be trained about placing furniture and extensive equipment at the right place before starting the cleanroom cleaning process.
Further, all the staff and janitors should be trained on general equipment maintenance, environmental sterilization practices, and growing procedures. A thorough understanding of the ideal methods ensures that all maintenance activities yield effective results.
Conclusion
It takes no rocket science to understand that cleanroom maintenance and cleaning are as essential as creating sterile products using these places. Therefore, it is crucial to understand the entire cleaning procedure for your sensitive area and implement these steps at your place. Further, it is essential to know the essential timings or intervals your cleanroom should be maintained.
Whether it is about ensuring adherence to prescribed guidelines or molding medical products in the cleanroom, it is impossible without dedicated cleanroom maintenance. Last but not least is that all the cleanroom systems should be under constant and strict supervision for air quality, particle levels, temperature, humidity, etc., based on the ISO specifications. It doubly ensures the earlier detection of any possible issues in the cleanroom ecosystem.