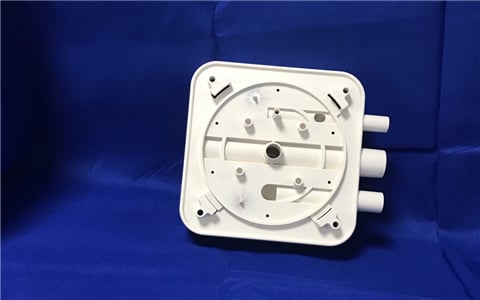
PSU and PPSU are commonly used plastics in medical devices. Also is the one of common injection molding resin in SeaskyMedical molding plant. Let us understand more for PPSU and PSU, then you will know it helps you for your medical device.
Because of its transparency and heat resistance to hot water, steam, ethanol and health characteristics, it can be used to make gas masks, contact eye sterilizers, endoscope parts, artificial heart valves, artificial dentures, etc. Polyphenylsulphone can be made into artificial breathing apparatus, blood pressure tube, dental mirror bracket, syringe and so on. Polysulfone and polyethersulfone can also be made into ultrafiltration membranes and reverse osmosis membranes. Once you read below, you will understand PSU and PPSU how it works under different temperature.
The thermal deformation temperature of PSU is 175℃, and it can be used for a long time between -100℃ and 150℃, and it has excellent aging resistance at high temperature. PSU is one of the most excellent varieties of heat-resistant engineering plastics. Its heat resistance can be comparable with thermosetting high temperature resistant polyimide, load deformation temperature is 275℃, long-term use temperature is 275℃, in -240℃- 260℃ can maintain good mechanical properties and electrical insulation performance
Challenge of PPSU and PSU injection molding
Lots of injection molding factory and worker do not hear PSU and PPSU before as it is not common plastic. Also it is times more expensive compare the other engineering resin such as PC, ABS and nylon. So it is easy to make mistake on mold making and plastic molding for PSU and PPSU. Both of PPSU and PSU is one of high temperature resin, the natural color is light yellow, or we maybe call it light brown. The injection barrel temperature is 360℃-℃.
Lots of injection machine is 350 ℃ max. injection barrel temperature, also for lots old injection machine is not stable for the barrel injection temperature. This is very bad for PPSU and PPSU injection molding. Sometime it is not possible to short out the product. Anyhow the quality is quite not sable.
Also if there is no experience to make injection mold for PSU and PPSU, it is usually to use prehard steel to save cost. But this will kill the project due to the soft steel can not against high mold temperature, finally the mold will be crash.
Our Solution
SeaskyMedical work for a few large and small PSU and PPSU parts such as medical valve , cup ,canister and cover. We use harden steel for core and cavity of mold. Also we have high temperature injection machine. We work closely with our resin suppliers to understand different type of PSU resin performance. All of engineer, mold maker and injection guys are trained for different type of resin. Then we can save cost and time for your new medical device plastic part development.