The world of low volume manufacturing is vast and ever-evolving. With the rapid strides in technology and changing consumer demands, the methods we employ to produce goods must also adapt. Among the plethora of manufacturing methods, injection molding has emerged as a dominant force, especially in the realm of plastic parts production. But, as with everything, the nuances matter. Not every product demands mass production of parts. Sometimes, the need is for fewer, specialized parts without compromising on quality. Enter the realm of low volume injection molding—a specialized niche that caters to specific project goals. This guide aims to shed light on the intricacies of low volume injection molding, its benefits, and its significance in today’s manufacturing landscape.
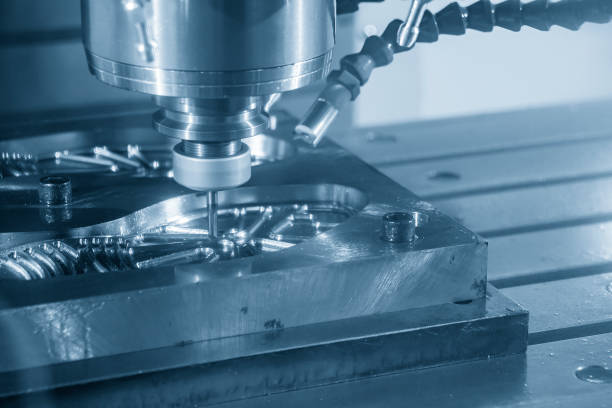
What is Low Volume Injection Molding and Why It Matters
Low-volume injection molding is a refined manufacturing process tailored for the fabrication of limited quantities of plastic components. This method contrasts with high-volume or mass production techniques which generate extensive batches of uniform components. The growth in demand for bespoke, specialized products, coupled with the burgeoning emphasis on rapid prototyping in product evolution, underscores the pivotal role of low-volume injection molding in contemporary manufacturing.
This process allows companies to produce parts efficiently, adhering to tight tolerances, and ensuring the implementation of best practices for a better surface finish, even when the quantities are limited. Such flexibility is invaluable, especially during the early stages of product development or when introducing a new product to the market. By employing low volume injection molding, companies can test the waters, gather feedback, and make essential modifications before diving into mass production. In essence, it offers a bridge between initial design considerations and full-scale production, ensuring that products are market-ready and meet the desired quality standards. Low volume injection molding is a great option for businesses looking to produce plastic parts and products in smaller quantities. Using this technique, you can save time and money on production costs while still maintaining quality.
Key Advantages of Low Volume Injection Molding
Reduced Upfront Costs
Contrary to the significant capital expenditures required for mass production, largely due to tooling and setup costs, low-volume molding presents a cost-effective alternative. This approach refines the supply chain, yielding significant cost efficiencies and augmented adaptability. Such merits are particularly advantageous for nascent enterprises and entities with constrained financial resources, enabling them to fabricate premium-quality components without overextending their budgetary provisions.
Flexibility in Design
Low volume injection molding grants the liberty to make design alterations between production batches. Such adaptability is indispensable, especially when incorporating feedback or aligning with market dynamics. With a limited number of components in each batch, design modifications are both more feasible and economical.
Shorter Lead Times
In today’s fast-paced market landscape, time is of the essence. Focusing on smaller production batches, low volume injection molding inherently leads to reduced lead times. This translates to accelerated product launches and the capability to rapidly adapt to market demand fluctuations.
Quality Assurance
Given the fewer components produced, there is an amplified focus on quality assurance. This guarantees that every component aligns with established benchmarks and maintains stringent tolerances. Such rigorous precision is vital, especially in sectors where meticulous accuracy is non-negotiable.
Low Volume vs. High Volume Injection Molding
When it comes to plastic injection molding, understanding the difference between low volume and high volume is pivotal for decision-making. Below is a comparative table highlighting the key distinctions:
Criteria | Low Volume Injection Molding | High Volume Injection Molding |
Production Quantity | Smaller batches, typically ranging from a few dozen to thousands of units. | Large batches, often in the range of thousands to millions of units. |
Costs | Lower upfront costs due to reduced tooling and setup needs. | Higher initial investment in molds and setup. |
Flexibility | Allows for design changes between batches, ideal for prototyping and testing. | Design is typically fixed after the initial setup for mass production. |
Lead Time | Shorter lead times due to fewer parts being produced. | Longer lead times owing to the vast number of parts produced. |
Quality Assurance | More focused quality control on smaller batches ensures higher consistency. | Continuous quality control, but issues may take longer to address due to batch size. |
Application | Best suited for prototyping, market testing, and specialized products. | Ideal for established products that have steady, high-volume demand. |
Key Design Considerations in Low Volume Injection Molding
- Material Assessment:
Ensure the chosen material aligns with low-volume production requirements. Certain specialty or bespoke materials may not be accessible in limited quantities or might incur significant costs.
- Tooling Considerations:
Material: For productions in limited quantities, utilizing materials such as aluminum is frequently more economically advantageous compared to hardened steel. This is attributed to aluminum’s machinability and cost-effectiveness, notwithstanding its comparatively reduced longevity.
Design Simplification: It is advisable to choose tools that are either single-cavity or have minimal cavities, as opposed to multi-cavity options. Doing so contributes to a reduction in both expenses and fabrication timeframes.
- Part Design:
Uniformity in Wall Thickness: Maintain a uniform wall thickness throughout to mitigate potential issues such as sink marks or voids. Introduce modifications in thickness in a gradual manner.
Structural Reinforcement: Integrate ribs and gussets to enhance structural rigidity without expanding the wall dimensions.
Draft Angle Considerations: Ensure the inclusion of appropriate draft angles to optimize the mold ejection procedure.
- Gate & Runner System Design:
Aim for a streamlined gate and runner configuration to achieve quicker production cycles and minimize material wastage.
- Dimensional Accuracy:
While it’s feasible to obtain precise tolerances, it might be beneficial both in terms of practicality and budget to allow for slightly relaxed tolerances in low-volume batches, given the project permits.
- Flow Analysis for Molds:
Even for limited productions, executing a mold flow assessment is instrumental in pinpointing potential complications such as weld lines or air entrapments.
- Post-Production Measures:
Assembly Considerations: If the component is to be integrated with others, prioritize its ease of assembly during its design stage.
Surface Specifications: Should a specific texture or finish be mandated, it’s imperative that the mold’s design encapsulates these requirements.
Choosing the Right Low Volume Injection Molding Services
Selecting an optimal low volume injection molding service is of paramount importance. Please consider the following critical factors when making your decision:
- Domain Expertise: It is imperative for the chosen service provider to exhibit an advanced mastery in low volume injection molding, along with a comprehensive understanding of its intricate methodologies.
- Material Selection: A reputable service provider should offer informed guidance on the best selection of thermoplastic resins tailored to your project, taking into consideration vital attributes such as thermal stability and wall criteria.
- Mold Design Proficiency: The design of the mold is foundational to this process. Therefore, the provider should demonstrate unmatched expertise in crafting molds, factoring in detailed parameters such as precise internal angles, tooling impressions, and the strategic positioning of ejector pins.
- Lead Time: Engaging with service providers recognized for their swift lead times is advantageous, guaranteeing your products an immediate market introduction.
- Budget: While cost-effective solutions hold significant appeal, the quest for affordability must not compromise the quality of the product. Balancing cost and quality is of utmost importance.
Custom Injection Molding From SeaskyMedical
Your search for a trusted partner in custom medical injection molding is realized with SeaskyMedical. As an ISO-certified establishment in medical injection molding, we consistently maintain unparalleled standards of excellence. Utilizing only certified materials, our products have garnered extensive trust within the medical industry. All our manufacturing, assembly, and packaging procedures are meticulously conducted in an ISO 8 cleanroom, equipped with the most advanced injection molding apparatus.
SeaskyMedical is distinctively recognized for our steadfast commitment to quality. It is our assurance that every product not only aligns with but exceeds industry standards, achieved through stringent quality controls. Our portfolio encompasses medical enclosures, intricate equipment components, prosthetics, and a diverse range of plastic medical and laboratory disposables.
Beyond mere molding, SeaskyMedical offers holistic solutions. Our expertise encompasses product design, development, material consultation, mold creation, injection mold design, and an array of supplementary services. Our reputation as a leading medical device injection molding firm is anchored in our ability to custom-craft injection molded components while strictly adhering to medical industry protocols.
Conclusion
Low-volume injection molding plays a pivotal role in contemporary manufacturing due to its adaptability, cost efficiency, and superior quality. Collaborating with esteemed partners such as SeaskyMedical ensures a commitment to excellence. Whether introducing a novel product or searching for a reliable production ally, the implementation of low-volume injection molding offers significant