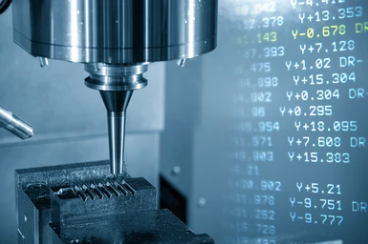
The injection molding process, though sophisticated and extensively used for manufacturing parts with complex geometries, can sometimes lead to certain defects. Understanding and addressing these defects is crucial to maintain the quality and efficiency of the process. In this article, we will explore common injection molding defects, their causes, and troubleshooting techniques, with a special emphasis on injection pressure regulation and low pressure injection molding.
Common Injection Molding Defects: Causes and Solutions
Short Molding
Short molding is a prevalent issue encountered in the injection molding process. It occurs when the mold cavity is not adequately filled prior to the cooling and ejection phases. Several factors contribute to this problem, including insufficient material available for injection and the premature solidification of the material. One key factor that determines the occurrence of short molding is the injection pressure exerted during the process. Maintaining optimal injection pressure, such as hold pressure, is crucial to ensuring complete cavity filling and preventing short molding defects, such as short shot. Thin layers of material can also contribute to short molding, as they may not fill the cavity completely. To address issues of short molding, consider these measures: Confirm that the injection pressure is adequate to adequately fill the surface of the component.
- Opt for a more substantial capacity machine
- Enhance the speed of injection
- Raise the mold and material temperature to slow down cooling
- Boost the injection pressure
Sink and Void Issues
Sink and void issues are common defects that occur in injection molded parts. These defects are characterized by areas where the molding material cools and shrinks at different rates than the surrounding material, resulting in depressions on the part surface or internal hollow areas and gaps. Sink marks appear as shallow or deep depressions on the exterior of the part, causing an uneven or blemished surface. These sink marks typically occur in thicker sections of the part where cooling takes longer, or in areas where there is inadequate material flow during the injection process. Voids, on the other hand, are internal hollow areas or gaps within the part. They can be caused by trapped air or gas, inadequate material flow, or design issues such as insufficient draft angles or uniform wall thickness. To address shrinkage, sink and void problems, consider deformation.
- Elevating the injection pressure
- Extending the cooling time
- Prolonging the hold time
- For design issues, design ribs instead of thick sections for uniform cooling
Delamination
Delamination is a defect in injection molded parts where the plastic resin fails to properly bond or set, resulting in peelable surface layers. It occurs when there is a lack of adhesion between different layers of the molded part. This defect can compromise the integrity of the plastic part and lead to performance issues. To address this issue, there are several remedies available that can be used to improve adhesion and prevent weld lines tonnage delamination.
One common cause of delamination is the presence of contaminants in the material or mold. Contaminants such as dirt, oil, or residue from previous processing can prevent proper bonding between the resin layers, leading to the formation of foreign material. Another cause of delamination is improper gate size, which can lead to uneven flow of the resin and result in weak bonding between the layers.
Excessive moisture can also cause delamination in injection molded parts. Moisture can be absorbed by the plastic resin during storage or processing, and if not properly dried, it can lead to incomplete bonding between the layers. Solutions to delamination include using molten plastic with a higher melt flow index or increasing the injection speed to achieve lower viscosity and melt temperature.
- Purging and cleaning the mold and tool
- Drying the material
- Increasing the material or mold temperature
Flashing
Flashing, in the context of molding processes, is a common phenomenon that occurs when surplus material forms along the dividing lines, or parting line, of a manufactured part. When there is an excess of material seeping out from these lines, what results is what is termed as “flashing”. Though not a cause for part rejection, it does require trimming, which adds to production time and costs. Typically, flashing occurs as a result of misaligned mold parts or due to the mold being forced open under pressure. To rectify flashing, consider adjusting the mold wall alignment or increasing the clamping force. Another way to prevent flashing is to ensure that the flow lines are smooth and free of any obstructions.
- Realigning, flattening, and cleaning mold faces
- Increasing clamping pressure
- Prolonging the fill time, hence decreasing the fill rate
Troubleshooting Techniques for Solving Injection Molding Defects
Examination of the Part and Process
Before diving into troubleshooting a specific problem, it’s crucial to thoroughly examine the part, both internally and externally, to identify any other possible defects. This holistic approach can help to quickly isolate the main cause of the problem.
Documentation Review and Creation
Good documentation practices throughout the production process can prevent many issues from arising. Any adjustments made to remedy a molding issue should be systematically documented to provide valuable information for future operations. It is important to maintain high-quality documentation to ensure that the information is accurate and accessible when needed.
Consideration of Process Relationships
When performing troubleshooting, it’s vital to consider how adjusting one process may impact another. Remember, nothing occurs in a vacuum in injection molding; changing one aspect of the process is bound to affect numerous other aspects.
Preventive Measures for Avoiding Injection Molding Defects
Machine Outputs Documentation
Besides documenting machine inputs during troubleshooting, it’s also beneficial to document outputs, including the cooling process. This will provide a clearer understanding of the actual results of the standard process inputs and how they affect the quality of end products.
Regular Mold and Tool Maintenance
Regular purging and cleaning of the mold and tool can prevent issues like delamination and flashing. It can help to eliminate contaminants and ensure the proper functioning of the vent molding equipment. Proper maintenance of the mold and tool is crucial for part design and to ensure that the final product meets the required specifications.
Appropriate Handling and Shipping
Rough handling and bypass during shipping can lead to defects like chipping. Hence, proper handling during shipping should be ensured to avoid such defects.
Injection molding is an intricate operation that mandates meticulous attention to details. However, by implementing the right troubleshooting techniques and preventive measures, you can significantly reduce the occurrence of molding defect and optimize your injection pressure regulator to decrease mold temp, ensuring effective low pressure plastic injection molding with nozzle. This will not only save time and money but also minimize material wastage, leading to a more efficient and cost-effective injection molding process with mold design.
At Seaskymedical we are committed to ensuring our parts are defect free. Our primary objective is to swiftly and effectively detect and resolve any challenges that may arise. To learn more about our molding services, please don’t hesitate to reach out to us today.