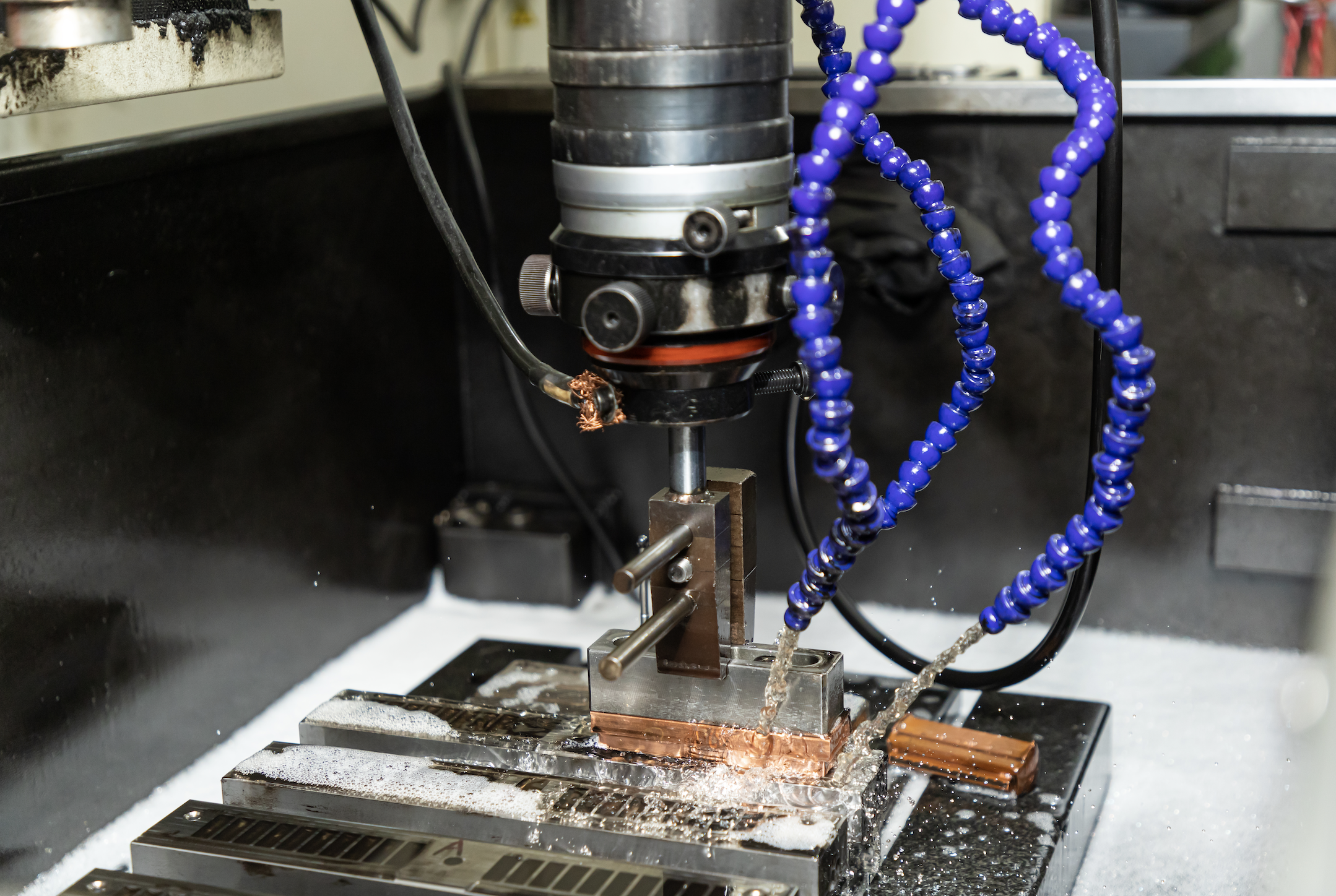
In the nexus of healthcare, engineering, and innovation, medical injection molding has charted a pivotal role for itself. This specialized manufacturing process, whereby medical-grade material is injected into a mold to create intricate, high-precision medical components, has become instrumental in revolutionizing patient care and healthcare services. From common medical devices in use every day to life-saving surgical equipment, medical injection molding is integral in crafting the essential tools of the modern healthcare sector.
What is Medical Injection Molding?
Medical injection molding is the process of creating medical devices and components using plastic injection molding technology. It’s a cost-effective, efficient way to produce high-quality medical equipment, such as syringes, IV tubes, and respiratory masks, that meet industry regulations and standards.
In this comprehensive guide, we delve into the intricacies of medical injection molding. We explore its role in healthcare, the variety of materials used, its numerous advantages, and its impact on patient care. We investigate quality control measures, compliance with strict regulatory frameworks, and its impressive evolution over the years. Additionally, we discuss the challenges the industry faces and the exciting future trends that are set to drive this dynamic field forward. The information provides insights for those looking to choose a medical injection molding partner, ensuring a productive and fruitful collaboration.
What is the Role of Medical Injection Molding in Healthcare?
Medical injection molding has revolutionized the healthcare industry by providing a fast, efficient, and reliable method for producing intricate medical devices and equipment. This process, which involves injecting molten materials into a mold to create parts of various shapes and sizes, is relied upon heavily by the medical sector.
From surgical instruments to prosthesis components, medical injection molding has a wide range of applications. Its high degree of accuracy makes it an ideal method for creating intricate products with tight tolerances, which are often required in the medical field.
The influence of medical injection molding extends to patient care as well. By offering a way to produce affordable and high-quality medical equipment, it allows medical institutions to deliver better quality care. This goes to show that the role of medical injection molding extends beyond just manufacturing – it has a direct impact on the lives of patients.
What’s more, medical injection molding also fosters innovation in healthcare. As technologies advance, the process is continually adapted and fine-tuned, enabling the production of emerging medical devices. Indeed, without medical injection molding, many modern medical advancements would not have been possible.
Understanding the Medical Injection Molding Process
The medical injection molding process, at its core, involves heating the material – usually plastic or metal – to a liquid state and then injecting it into a mold under high pressure. This mold is custom-made to match the exact dimensions of the part to be produced.
The molten material is left to cool and harden within the mold, taking the shape of the cavity. Once hardened, the product is ejected from the mold – what you have now is a precise, robust, and high-quality medical component.
While the process might seem straightforward, the complexity lies in the details. Each phase – from choosing the appropriate material and designing the mold to setting the correct parameters for injection and cooling – needs meticulous attention. Engineers must consider factors such as the product’s purpose, its required strength and flexibility, interfacing with other components, sterilization techniques, and many others.
In the medical world, there is no room for error. Even a slight mistake can render a device ineffective or, worse, hazardous. Hence, proper understanding and execution of the medical injection molding process are critical for ensuring the production of safe and effective medical devices that equip healthcare professionals to deliver top-notch care.
Types of Materials Used in Medical Injection Molding
A substantial part of the medical injection molding process is the selection of the right material. Given the vast number of applications and strict regulations in the medical field, this step is essential for creating a product that is functional, safe, and compliant with industry standards.
Among commonly used materials are medical-grade plastics, such as Polypropylene (PP), Polycarbonate (PC), and Polyether ether ketone (PEEK). Selected for their high strength-to-weight ratios, these plastics exhibit excellent thermal and chemical resistance. Importantly, they are biocompatible, meaning they can interact with the human body without causing adverse reactions – a crucial factor in medical applications.
Besides plastics, silicones are also widely utilized in medical injection molding, especially for products that must be flexible or transparent. Silicones are highly biocompatible and resistant to sterilization processes, making them ideal for long-term implantable devices.
Metals, too, have a place in medical injection molding, more specifically in Metal Injection Molding (MIM). These materials are ideal for components that require superior strength, such as surgical instruments and orthopedic implants.
Advantages of Medical Injection Molding in Device Production
Medical Injection molding offers several advantages that make it a favored technique in device production.
Efficiency and Scalability: Medical injection molding excels in producing large volumes of identical parts. Once the mold is created, it can produce thousands to millions of parts, each as precise as the last, making it highly efficient for large-scale production.
Complexity and Precision: The process allows for high complexity in part design. It can create parts with intricate geometries and a high degree of detail that would be difficult, if not impossible, to achieve through other means. This precision is essential in medical device production, where every micrometer can make a difference.
Cost-Effective: Over the long run, medical injection molding can be very cost-effective. The upfront cost for mold creation can be high, but when distributed over a large run of parts, the price per unit becomes significantly low.
Consistency and Quality: The high repeatability of the process ensures each part is consistently produced to the exact specifications, leading to high-quality components. This consistency is critical in the medical field, where deviations could compromise patient safety.
These advantages solidify medical injection molding’s position as the backbone of medical device production. It presents an optimal balance of precise, efficient, consistent, and cost-effective manufacturing to meet the evolving needs of the healthcare sector.
The Impact of Medical Injection Molding on Patient Care
The influence of medical injection molding on patient care is profound. As a process that allows precision, consistency, and cost effectiveness in the creation of medical devices, it directly affects the quality of treatment patients receive.
Complex devices and equipment manufactured through this process play a pivotal role in diagnosing, treating, and managing a wide range of health issues. From insulin pens for diabetes to implants for joint replacements, these items directly impact the lives of patients, offering them better and often, more comfortable treatment options.
Furthermore, the durability and reliability of these devices are crucial. Patients can depend on the safety and performance of these products, as they’re made to strict quality standards. This reliability brings peace of mind to both patients and healthcare professionals, knowing that the devices will perform as expected without failure.
Overall, medical injection molding contributes significantly to the advancement of patient care, enabling the development of superior medical devices that save lives, improve quality of living, and propel modern medicine forward.
Precision and Efficiency: The Hallmarks of Medical Injection Molding
One of the key attributes of medical injection molding is its ability to create highly precise and detailed components efficiently. The method is capable of manufacturing highly complex parts that could be beyond the scope of other techniques. This precision is integral in medical applications, where even the smallest deviation can have significant consequences.
The process functions by injecting material into a meticulously crafted mold, which allows every minute detail to be accurately captured in the finished product. This high precision, coupled with the process’s repeatability, ensures a consistent level of quality across large production volumes – an essential factor for medical products where each part must meet critical safety and functionality requirements.
The efficiency in medical injection molding also lies in its high volume production capability. Once the initial setup is completed, the process can produce a vast number of parts quickly, making it exceedingly cost-efficient for large production runs. Additionally, advancements in automation have further streamlined the process, reducing manual intervention and increasing productivity.
In essence, the inherent precision and efficiency of medical injection molding have made it a cornerstone in the production of medical devices, offering unrivaled capabilities in the manufacture of life-changing, and life-saving, medical products.
Quality Control in Medical Injection Molding Operations
Quality control is indispensable in medical injection molding operations. Given the critical nature of medical devices and the strict industry regulations, ensuring products are of the highest quality is paramount.
Quality control in medical injection molding encompasses a variety of practices. It begins with the inspection of raw materials to ensure they meet necessary medical standards, including biocompatibility and sterilization requirements. The design and manufacturing of the molds themselves are also subject to intensive scrutiny, as a single flaw can lead to a whole batch of faulty parts.
Moreover, the production process is monitored to comply with predefined parameters such as temperature, pressure, and cycle time that ensure each part is formed correctly. Advanced technologies, such as machine vision systems and automated measuring instruments, are used for real-time quality checks.
Upon production, a range of tests are performed on the parts, including dimensional analysis, strength testing, and in some cases, biocompatibility testing. The goal is to ensure every single piece coming off the production line meets the rigorous standards set by both the company and regulatory agencies.
Complying with Regulatory Frameworks in Medical Injection Molding
The medical field is one of the most heavily regulated industries worldwide, and rightly so given that patient safety and health are at stake. Medical injection molding operations must strictly comply with a multitude of regulations to ensure that products are safe, effective, and of the highest quality.
Regulations concerning medical injection molding revolve around materials, manufacturing processes, hygiene, and product testing. Standards imposed by the Food and Drug Administration (FDA) in the United States and the European Medicines Agency (EMA) in the EU are particularly influential.
For example, only certain types of plastic classified as “medical grade” can be used, and stringent standards apply to their processing. The manufacturing environment must follow Good Manufacturing Practices (GMP) that ensure cleanliness and prevent contamination. The end products must be subjected to rigorous testing to verify they meet all design and safety requirements.
Compliance with these frameworks is not just about legality but is also part of a moral and ethical obligation to provide patients with the safest, most reliable medical devices.
Medical Injection Molding: The Evolution Over the Years
The field of medical injection molding has witnessed significant developments over the years. From the early materials and primitive machines to today’s sophisticated polymers, high-precision equipment, and stringent quality control, this industry has constantly evolved to meet the dynamic needs of modern healthcare.
Initially, the process and materials used were quite basic, primarily focusing on mass production of simple parts. However, as the medical field advanced, the demand grew for complex parts, stringent safety, and high precision. This drove the need for sophisticated tools, advanced materials, and rigorous quality management systems.
The introduction of Computer-Aided Design (CAD) and Computer-Aided Manufacturing (CAM) revolutionized product design and improved the precision and repeatability of molds. Automation and robotics further improved the efficiency, precision, and scalability of production lines, minimizing human error.
The progress in material science brought forth medical-grade materials with improved properties, including biocompatibility, durability, and resistance to sterilization. Additionally, improvement in process control systems and digitalization allowed for enhanced quality control, traceability, and regulatory adherence.
Challenges and Solutions in Medical Injection Molding
Despite its many advantages, medical injection molding is not without its challenges. Stringent regulatory standards, advancing technologies, material complexity, and micro-molding requirements all present complex hurdles in this field.
Regulatory compliance is one of the major challenges, requiring significant efforts and resources to keep up with constantly changing standards. Here, investing in specialized compliance expertise, ongoing training, and quality management systems can ensure lawful, safe, and efficient operations.
Material selection also poses a challenge due to the variety of medical-grade materials and their specific processing requirements. Collaboration with material scientists, and thorough inquiries with material suppliers can help identify the best materials for a specific application.
Micro-molding, or the creation of increasingly minute components, necessitates extreme precision and control. Solutions lie in technological advancements such as high-precision molding machines, micro-inspection systems, and expert technicians skilled in micro-molding processes.
By proactively addressing these challenges, medical injection molding companies can continue to deliver high-quality, innovative medical components while maintaining regulatory compliance and operational efficiency.
Future Trends: What’s Next for Medical Injection Mold?
Given the rapid pace of technological and biomedical advancements in the medical industry, the future of medical injection molding and the production of plastic parts hold exciting prospects.
One potential trend is the rise of bio-absorbable materials in the field of plastic injection molding. These materials, often used in prosthetics, dissolve harmlessly inside the body once they’ve fulfilled their purpose, eliminating the need for device removal surgeries. With these developments, the necessity for material innovation, including polyethylene, silicone and resin becomes critical. The medical injection process, respected for its preciseness in measurements, even down to millimeters and microns, will play a pivotal role in molding these materials into functional and durable medical parts.
Advanced automation, reduced vibration, and an increase in insert molding, will be another area where the industry may expand. As automation technology continues to evolve, incorporating more AI and machine learning capabilities, we can expect even greater precision in plastic molding, efficiency, and increases in productivity for injection molding services in medical injection molding operations.
Sustainable and green production are also likely to become a more prominent concern within the medical molding field. Efforts will be geared towards reducing waste, energy consumption, and overall environmental impact, while maintaining heat resistance, sterility, and the mechanical properties necessary for patients’ safety.
How to Choose the Right Medical Injection Molding Partner for Tooling and Product Development
When developing a prototype, selecting the right medical injection molding partner is a crucial business decision that directly impacts the quality of your products, including test tubes and casings, and the satisfaction of your customers. Many factors must be considered to understand the specific needs of your project.
Firstly, potential partners should operate under strict quality control processes and adhere to all relevant FDA regulations and certifications. Companies with strong track records of compliance with medical device manufacturing standards from organizations like the FDA and ISO should be prioritized.
A prospective partner’s technological capabilities should be thoroughly examined. Do they have the state-of-the-art machinery necessary to manufacture plastic injection medical parts with the required precision and quality? Is their facility equipped to handle orthopedics and other medical molding challenges your project may present?
One must also assess their knowledge of material science and their ability to perform tests to guarantee no breakage under pressure. The right partner should guide you about the best materials for your medical product, considering performance, safety, durability, and cost.
Finally, a potential partner’s level of customer service and communication skills should be considered. The best partners foster a strong working relationship with clients, maintaining open channels of communication and providing regular updates.
Choosing the right medical injection molding partner ultimately hinges on finding a company that aligns with your business values, product development requirements, and quality standards. When looking for a top-tier medical injection molding manufacturer, look no further than SeaSky Medical. We uphold your business values, meet your product development requirements, and exceed quality standards. Our expert team ensures uncompromised compliance with medical standards, offering precise, reliable medical parts and robust customer service. SeaSky Medical is more than a manufacturer; we’re your partner in enhancing healthcare. Trust us to take your medical product development to the next level.