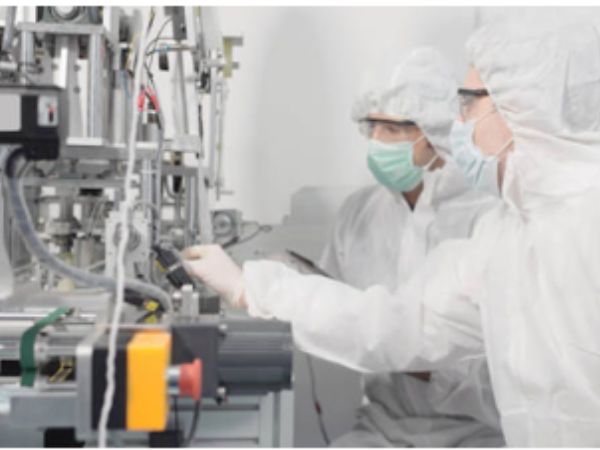
Injection molding technology has revolutionized the world of manufacturing, enabling the mass production of complex and intricate plastic parts across various industries. This technology offers unparalleled precision, efficiency, and cost-effectiveness, making it the go-to solution for producing plastic components. This article examines various injection molding methods, the significance of proper maintenance, strategies to decrease production time, and emerging trends in the injection molding industry.
What are the different types of injection moulding techniques?
There are several injection molding techniques that cater to different needs and applications. Here are six common types of injection molding technology:
Thin Wall Molding
Thin wall molding is a manufacturing technique that produces plastic components with extremely thin wall thicknesses. This technique is commonly used to make electronics, testing equipment, containers, tubes, and other enclosures.
To make thin wall parts without problems, plastic molders have to be very careful in how they design the part, design the mold, and set up the manufacturing process.
The wall thickness has to be just right – thick enough to be sturdy but thin enough to meet specifications. It is necessary for the mold to uniformly disperse the molten polymer material throughout all regions of the mold cavity. And the process settings like temperature, speed, and pressure have to be precisely controlled and balanced.
If any of these things are off, the thin walls can end up with flaws like bubbles, sink marks, warping, or cracking. It takes skill and experience to get thin wall molding right. But when it’s done well, it can produce high volumes of very lightweight, affordable parts with an almost delicate level of detail.
The key challenges are really managing the flow of the liquid plastic and controlling how quickly it cools. If the plastic doesn’t fill the mold fully before hardening, or if it cools at different rates in different areas, the thin walls suffer. Close attention to these dynamics is what separates an expert thin wall molder from an amateur.
Gas-assisted Injection Molding
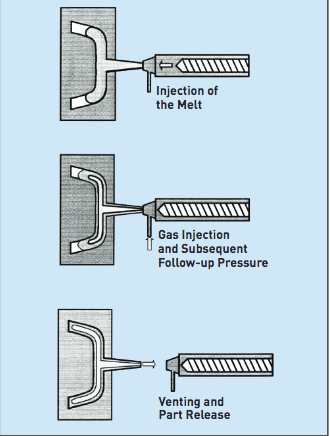
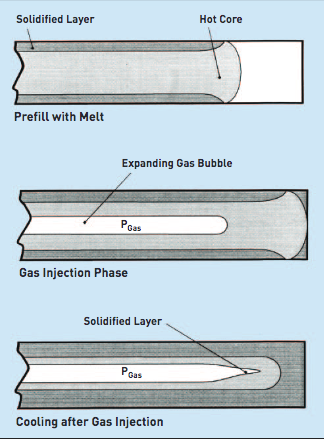
Regular plastic injection molding can have problems when making thick parts. As the thick parts cool down, they often warp or bend out of shape. This is because the outer parts of the mold cool first, while the inner parts are still hot and pliable.
Gas-assisted injection molding fixes this issue. It works by shooting gas into the mold after it’s been filled with molten plastic. Gas is injected within the internal section of the part, where the plastic is kept at an elevated temperature. It creates air pockets or a hollow space in the middle of the thick part.
This helps the part hold its shape as it cools for a couple of reasons:
First, the hollow inner section cools at the same rate as the outer section, so you don’t get uneven cooling.
Second, the overall part is lighter with the hollow inside, so it’s less prone to deformation.
The end result is you can make thick parts with more detail and tighter tolerances. You also save money because you can use less plastic. The outer surface of the part still looks smooth and solid, while the inner section is porous or hollow.
Gas-assisted injection molding requires some tricky control and timing to get right, but it’s a very useful tool for molders. It allows you to get all the benefits of a thick, robust part design without the headache of distortion and quality issues during manufacturing.
The gas is a clever trick that provides structure and support, even though it’s essentially just air. This process helps open up more possibilities for creative and impactful plastic part designs.
Metal Injection Molding
Plastic is by far the most popular material used in injection molding. But metal can also be injection molded, even though it’s a more specialized and expensive process. Metal injection molding is mainly used for niche or high-end applications.
For example, metal injection molding is sometimes used in cell phones to shield electronics from radio waves and microwaves. The dense, conductive properties of the metal are good at blocking electromagnetic interference. So phone makers will use metal injection molded parts in strategic locations within the phone case.
Metal injection molding also produces very durable parts with tight tolerances. So it’s good for applications where high strength and precision are important. Parts like medical implants, industrial tooling, and aerospace components are well-suited for metal injection molding.
However, metal injection molding is costlier than plastic injection molding for a few reasons:
- Metal materials themselves are more expensive than plastics.
- Higher temperatures are required to melt metals, so more energy is needed.
- Metal molds are more expensive to make and maintain due to the higher heat and forces.
- Post-processing like grinding and polishing is often required for metal parts, adding additional cost.
- Metal part designs typically require tighter tolerances, increasing the cost and complexity.
So while the high performance of metal injection molded parts is appealing, the economics really only work for high-value, niche products. For most standard injection molding jobs, plastic still reigns supreme thanks to its low cost, flexibility, and ease of processing. But it’s good to know metal injection molding exists as an option when the application really demands it.
Liquid Silicone Injection Molding
The predominant plastic injection molding process utilizes thermoplastic materials. This means the plastic material starts out cold and is injected into a hot mold. It then hardens permanently in the shape of the mold cavity. Once cooled and cured, thermoset parts cannot be melted down again.
However, for some applications that require high heat resistance or chemical resistance, thermoplastic injection molding is used instead. This uses plastics that can be melted and re-solidified multiple times. Liquid silicone is a popular thermoplastic for injection molding.
Thermoplastic injection molding is good for a few reasons:
- The parts can withstand high temperatures that would normally melt thermoset plastics. This is useful for things like automotive components under the hood, industrial parts, and some medical devices.
- The parts are chemically inert and non-reactive. Silicone in particular resists oils, solvents, and other chemicals that break down most plastics. This makes it good for gaskets, seals, and other parts exposed to chemicals.
- The parts can be re-melted, so excess material from the molding process can be recycled and reused. Thermoset plastics cannot be re-melted, so any excess has to be discarded.
- Thermoplastic parts tend to be more flexible and rubbery. Silicone parts, in particular, have a very flexible, rubber-like feel.
So in summary, thermoplastic injection molding offers some unique benefits where heat and chemical resistance are priorities. But for most standard injection molded parts, the lower cost and higher rigidity of thermoset plastics still dominate. The type of material and process used ultimately comes down to the specific application and performance requirements.
3D Printing
3D printing is an important tool for injection molding because it’s great for making prototypes. By 3D printing a physical prototype of a part before mass production, manufacturers can evaluate and improve the design much more thoroughly than just looking at a 3D rendering on a screen.
3D printing is also used to create injection molds. Plastic or metal 3D printers can produce molds that are then used to make injection molded parts.
However, 3D-printed molds today still lack the precision and tight tolerances of machined steel molds. The 3D printed molds work for some basic low-volume production, but they can’t achieve the same quality as traditional molds.
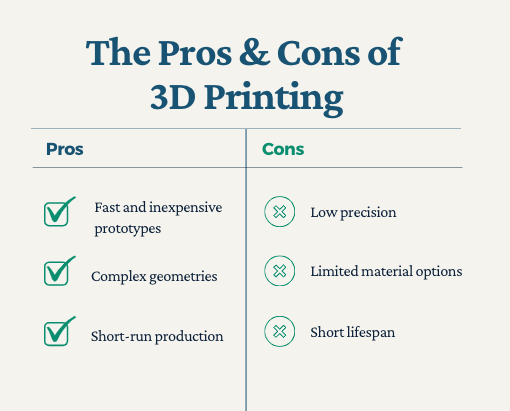
While 3D printing brings a lot of opportunities to injection molding, traditional manufacturing methods still dominate large-scale production where precision and quality are critical.
3D printing is an ideal complement for prototyping, low-volume jobs, and pushing the limits of design complexity. But steel molds and high-end CNC machines remain essential for the vast majority of injection molding.
Unique Material Formulations
While not a traditional “technology,” the use of unique material formulations advances molding capabilities. For instance, injection molding companies might use carbon or mineral fillers, blowing agents, and lubricity additives to enhance a part’s properties.
These unique materials must be carefully processed, considering the mold and plastic material temperatures, to achieve the best results.
How important is maintenance in injection molding technology?
Proper maintenance of injection molding machines is crucial to their performance, efficiency, and longevity. Older machines may suffer from variable or inconsistent injection pressure and speed (also known as fill time), leading to longer injection times and more rejected parts. Consequently, cycle times are extended, and overall production costs increase.
Investing in regular maintenance and timely repairs ensures that your injection molding machines operate at peak performance. Additionally, training and empowering experienced engineers to identify and address potential issues can further optimize your injection molding process.
How can you reduce injection molding cycle time?
The process of injection molding comprises three primary stages
Stages | Process |
Injection stage | Heated material is fed via pressure into the mold and cavities |
Holding or packing stage | Continued pressure is applied to ensure cavities are completely filled and to address any potential shrinkage of the material as it cools |
Cooling stage | The material cools to a solid form, and the pieces are ready to be ejected |
Each of these stages presents opportunities for improving efficiency and reducing cycle time.
Techniques to reduce the Injection Molding Cycle time
Make the Walls Thinner:
Use the minimum wall thickness needed for your part to work well. Thinner walls mean less plastic is needed to fill the mold, so injection takes less time. Follow the rules for minimum wall thickness while still making strong enough walls.
Optimize Your Machine
Make sure your injection molding machine is running well and can inject plastic fast enough with enough pressure. Regular service and fixes are needed to avoid problems.
Invest in Your People
Experienced injection molding engineers can find small changes to things like how fast plastic is injected, how much extra is added, and how long it’s held in the mold. These small changes can improve quality and cut cycle times. Help engineers share what they know to improve the process.
Choose Materials Carefully
Some plastics can be injected and fill the mold faster with higher pressure. Check different plastics to find ones that can cut cycle time without hurting part quality.
Improve Cooling
Cooling the mold often takes the longest in cycle. A good mold design spreads water and air, the most common coolants, well. Proper insulation keeps heat from the hot runners out of the mold, keeps cooling consistent, and avoids part defects.
What are some new trends in injection molding technology?
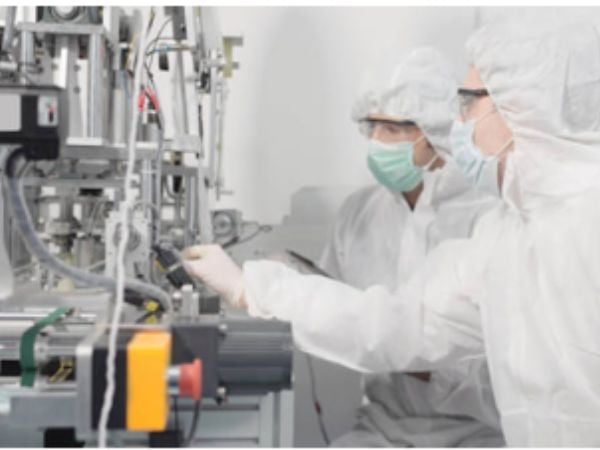
Innovation is constantly driving the evolution of injection molding technology. Here are some emerging trends to watch:
- Automation and robotics: The integration of automation and robotics in the injection molding process can increase efficiency, productivity, and precision while reducing cycle times and labor costs.
- Sustainable materials: The growing demand for eco-friendly products has led to the development of biodegradable and recycled materials for injection molding.
- Smart manufacturing and Industry 4.0: Advanced sensors, data analytics, and IoT technologies are being incorporated into injection molding machines, enabling real-time monitoring, predictive maintenance, and process optimization.
Conclusion
Injection molding has progressed rapidly and keeps improving with new methods, materials, and trends. Manufacturers can optimize their injection molding process by understanding the different injection molding techniques, prioritizing maintenance, and implementing ways to decrease cycle time. This helps them meet the increasing demand for high-quality, affordable plastic components.
By staying up-to-date with the latest trends and adopting new technologies, injection molding will likely see more improvements, greater efficiency, and more opportunities for both manufacturers and consumers.
Manufacturers that keep up with innovations in injection molding can take advantage of these advances to produce plastic parts more quickly and cheaply while maintaining quality. Consumers, in turn, benefit from the lower costs and higher availability of plastic goods.
The future looks bright for injection molding as technology and innovation continue to push the industry forward. Manufacturers embracing these new tools and techniques will be poised to succeed.
If you have any other questions regarding what type of injection molding may be needed for your component, Seaskymedical would be happy to help.