Selecting the proper tool steel for injection mold can significantly impact the creation of injection molds. Unwise decisions can result in catastrophes that fly in the face of countless arduous hours of labor. For instance, utilizing the incorrect tool steel for an injection mold could result in a broken core or cavity and premature wear and tear.
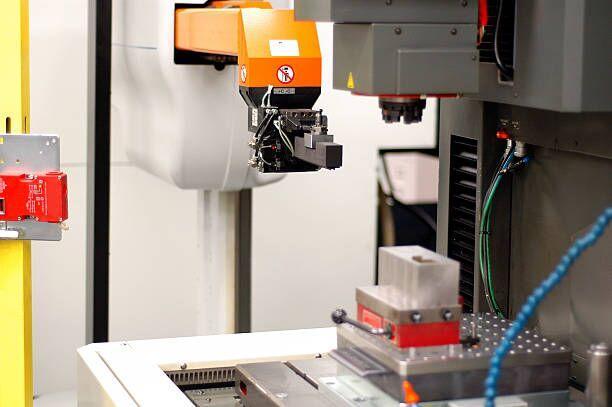
A plastic injection mold-producing manufacturer and contractor must make careful selections because the steel quality of the molding components directly affects mold quality and service life, as well as the look and grade of a plastic injection molded product. Learn more about the many kinds of injection mold steel material and how to choose one by reading on.
What is Injection Mold Steel?
A crucial part of the injection molding process is the mold. The importance of each component of the injection molding machine is equal. Yet the mold is the component where the final product is created. Another crucial element is the material used to make the mold. The precision, gloss, and pace of plastic cooling are all influenced by the material selection for mold making.

The best material for injection molds is steel. The choice of plastic mold steel grades is based on the type of mold material and geometry. Steel must meet certain specifications for the mold. The service life, ease of processing, and precision of the mold are significantly impacted by how well the steel is chosen.
The specifications change depending on the mold’s design, lifespan, type of plastic product, and the finished product’s functionality, aesthetics, and dimensional correctness.
Popular Tool Steel Materials for Injection Mold Making
Further details are provided below regarding the most popular plastic mold steel grades used in injection molding.
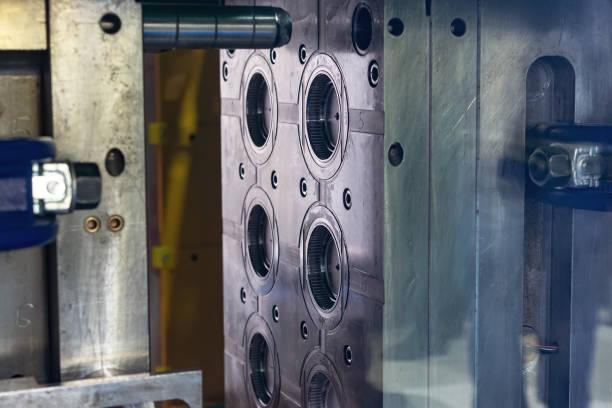
- P20 Pre-Hardened Tool Steel
The most popular mold steel for plastic injection molding is P-20 Steel, which has strong wear resistance and is reasonably priced. It is a pre-hardened injection mold steel material, which implies it is prepared for usage in the mold when it leaves the factory hardened to a certain hardness. P-20 is perfect for applications requiring high production volumes and shallow cavity molds.
Features:
- After machining, it makes heat treatment easier.
- Because of its pre-hardening, it provides stability and strength.
- The thermal stability of P20 is good.
- It offers exceptional resilience to wear and tear.
- It has good features for polishability.
- For plastic injection molds and die casting, P20 is preferable.
- H13 Tool Steel
A type of hot work tool moulding steel called H-13 Steel is made to withstand wear and thermal fatigue. It is perfect for high-heat applications and deep cavity molds since it is substantially harder than P-20 steel. Additionally, more costly than P-20 steel, it is typically employed in big-volume manufacturing.
H13 is employed in numerous cold work tooling applications due to its high toughness and excellent heat treatment resilience. The steel H-13 is a multipurpose material with exceptional tensile characteristics, surface texturing, abrasion resistance and hardness.
Features:
- H13 makes welding more convenient.
- It offers good resistance to abrasion.
- Moreover, it is quite machineable.
- It has strong thermal change wear resistance.
- S7 Pre-Hardened Tool Steel
S7 Steel is a shock-resistant tool steel designed to endure significant impacts and vibrations. It is frequently employed in die-cast molds and other purposes that require high stress and vibration resistance.
Features:
- It has outstanding shock resistance.
- It possesses qualities of wear resistance.
- High toughness is a characteristic of S7 tool steel.
- It can resist extremely hot temperatures.
- 420 Stainless Steel
A corrosion-resistant and heat-treatable variety of stainless steel is called 420 Steel. Because of its low cost and resistance to corrosion, it is frequently used by medical plastic injection molding producer and food-grade plastic injection molding producer. Compared to other mould materials, it is softer and good for high-volume manufacturing.
Features:
- It provides maximum corrosion resistance following complete hardening.
- Outstanding edge retention and wear resistance.
- Among all grades of stainless steel, it is the hardest mould material.
- It’s not too difficult to machine 420 stainless steel.
- Customized injection molding is possible.
Factors to Consider When Choosing Injection Mold Steel Material
There are a few things to take into account when choosing the proper steel for plastic injection molds.

- Hardness
Steels are typically subjected to a certain amount of hardening to improve the tool’s capacity to handle increased output rates or abrasive materials. A material’s resistance to abrasion and indentation is referred to as its hardness.
Hardened steels are perfect for high production quantities because they offer improved wear resistance and lower long-term maintenance costs. Pre-hardened steels have short turnaround times since you may quickly start the injection molding medical devices manufacturing process after cutting your tool’s detail radiant to size.
- Wear Resistance
A mold tool steel may receive wear resistance in several ways, most frequently by hardening the metal or adding alloying components that change the metal’s properties. The most crucial characteristics of mold steel are wear and abrasion resistance, which have a big impact on the post-processing of mold life, accuracy management, overflow removal, etc.
The number of alloy components and the presence of internal stress affect wear resistance. Hardness and wear resistance are typically inversely correlated. As a result, the surface of the cavity becomes harder, which can help with the wear resistance issue. Steel with a strong level of wear resistance must be utilized to increase the mold’s lifespan.
Businesses should use hardened tool steel if they require steel that is resistant to wear. In the long run, this will save maintenance expenditures while initially increasing the tooling prices.
- Toughness
The material’s toughness is important to the mold designer because of the service conditions experienced during injection molding, i.e., reasonably high compression cyclical loadings. High compressive loads must be applied to the materials without causing them to split or crack.
The most significant factors affecting a material’s finishing qualities are its composition and surface toughness. With an injection mold, the product’s surface is directly impacted by the surface roughness of the mold cavity. The optimum mold material should be strong and durable enough to resist structural damage but ductile sufficient to withstand impact loadings and breaking.
- Machinability
Take into account the machinability of the steel mold material. Steel with a low hardness that can be cut using conventional machining is the best choice. Yet, it is challenging to guarantee the mold’s longevity and cavity precision with this steel.
As a result, in real work, the mold insert is frequently made of pre-hardened steel that is easy to machine. Nitriding treatment can be applied to the surface of cores and cavities of precision and long-lasting molds to increase wear resistance.
Seaskymedical: Reliable Manufacturer of Steel Mold Tooling
In short, it is crucial to choose the best kind of steel for your materials and applications. Let Seaskymedical assist you if you need assistance selecting the appropriate plastic injection molding steel tool for your project.
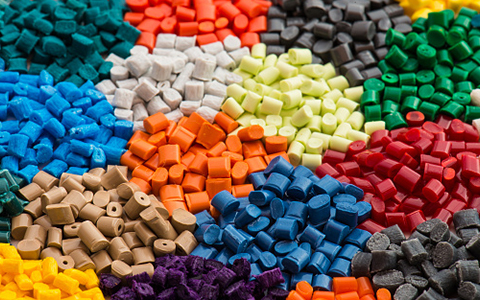
Creating molds, analyzing mold designs, and producing plastic parts are all services offered by Seaskymedical, a plastic molding manufacturer. We can assist you in making premium injection molds that will result in robust and dependable plastic molded products. Its engineering staff is qualified and knowledgeable to provide the best injection molding solution and customized injection molding.
To produce precise plastic molding tools for high-quality product manufacturing, we use robust materials like steel. Injection molding facilities are used to create standard designs following client requests. Moreover, Seaskymedical offers the prototype of the mold construction for usage later on during injection molding. Using streamlined solutions, the mold tooling procedure is made simpler.
Mold size and tolerance customization allow for clean room injection molding manufacturing and high-quality documentation. As a reputable mold manufacturer, Seaskymedical analyzes the design’s flow to enhance the usefulness and compatibility of the mold tooling. To get the best-quality injection molding tool for your next project, contact Seaskymedical.
Conclusion
You can make an informed choice when choosing the right tool steel for your plastic injection molding project by being aware of the distinctive qualities of each type of injection mold steel. It’s crucial to seek the advice of an expert to guide you in selecting the finest option for your product, depending on its unique specifications. Do not hesitate to contact Seaskymedical if you require expert advice on your choice of injection molding steel.