One of the most widely used methods of manufacturing plastic parts is injection molding. And this is because of the many benefits it offers, such as the support of large volume production and cost-effective production of identical parts. Because of this, it’s often preferred over other manufacturing methods like CNC machining, die casting, and urethane casting.
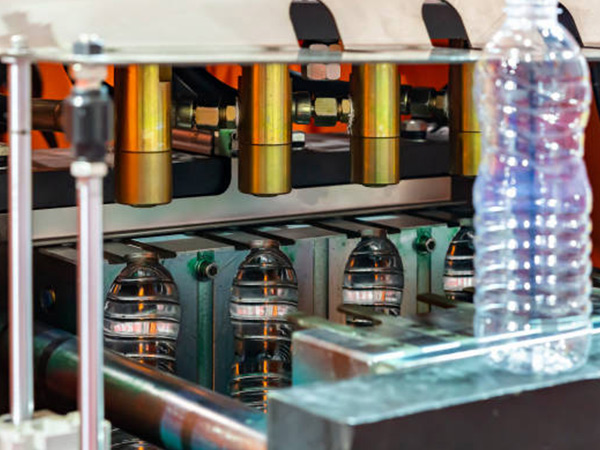
Customized injection molding is facilitated by means of single or multi cavity mold. While these two mold types have the same operation model, they are used to meet different demand or timeline requirements. Choosing between single cavity vs. multi cavity mold is crucial to the success of any project. This article highlights the properties, advantages, and disadvantages of each.
What is Cavity Injection Molding?
Cavity injection molding involves a series of events during the manufacture of plastic parts by injecting molten plastic material into a mold. The mold has one or more cavities that are shaped like the desired part, and the molten plastic material is forced into these cavities using high pressure. Once the plastic has solidified inside the cavity, the mold is opened and the part is ejected.
Function of Cavity in Injection Molding
The cavity is a negative space that defines the outer shape of the part being produced. Its function is to shape the molten plastic material into the desired form. The cavity determines the final shape and size of the plastic part. The most common types are single cavity and multi cavity.
In a single cavity, the mold has only one cavity that produces a single part at a time. This process is used for producing small quantities of parts or parts that are complex and require close attention to detail, such as injection molding medical devices.
In a multi cavity, the mold has more than one cavity, which produces multiple parts simultaneously. This process is more efficient and cost-effective for producing large quantities of parts.
Differences Between Single Cavity and Multi Cavity Molds
Highlighted below are the key differences between the single injection molding cavity and multi cavity injection molding.
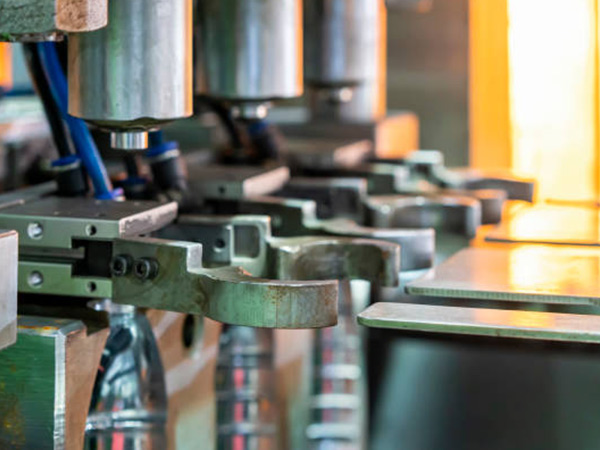
Advantages of Single Cavity Mold
- Better control over the molding process and quality of the part.
- Useful for producing larger or more complex parts that require more time to cool and solidify.
- More flexibility to make adjustments or changes to the mold design or material during production.
Advantages of Multi Cavity Mold
- Higher production efficiency, as multiple parts can be produced in a single molding cycle.
- Lower cost per part, as the cost of the mold can be spread across multiple parts.
- Useful for producing smaller, simpler parts that require less time to cool and solidify.
Disadvantages of Single Cavity Mold
- Lower production efficiency, as only one part is produced per molding cycle.
- Higher cost per part, as the cost of the mold is not spread across multiple parts.
- Longer lead time for production, as each part requires its own mold.
Disadvantages of Multi Cavity Mold
- Less control over the molding process and quality of the part, as variations in the molding conditions can affect all parts in the mold.
- Limited flexibility to make adjustments or changes to the mold design or material during production, as any changes would affect all parts in the mold.
Cycle Time of Single Cavity Mold
- Longer cycle time, as each part requires its own molding cycle.
Cycle Time of Multi-Cavity Mold
- Shorter cycle time, as multiple parts can be produced in a single molding cycle.
Shot Guarantee of Single Cavity Mold
- The shot guarantee refers to the ability to produce a single part with consistency and accuracy. Since only one part is produced at a time, the shot guarantee is relatively high.
Shot Guarantee of Multi-Cavity Mold
- The shot guarantee is generally lower than that of single cavity molding, as there are more variables to consider when producing multiple parts simultaneously.
Productivity of Single Cavity Mold
- The productivity is relatively low compared to multi-cavity molding. This is because only one part is produced at a time.
Productivity of Multi-Cavity Mold
- The productivity is higher than single cavity molding. This is because multiple parts can be produced simultaneously.
When to Use a Single Cavity or a Multi-Cavity Mold
Single cavity mold is best suitable for low-volume production of plastic parts, as well as those with complex geometries. On the other hand, multi cavity mold is preferred for making high-volume production.
How to Choose from Single-Cavity vs. Multi-Cavity Molds?
Here are the key factors that a plastic molding manufacturer examines when examining a single cavity vs. multi cavity mold. With these factors, you will be able to make an informed decision.
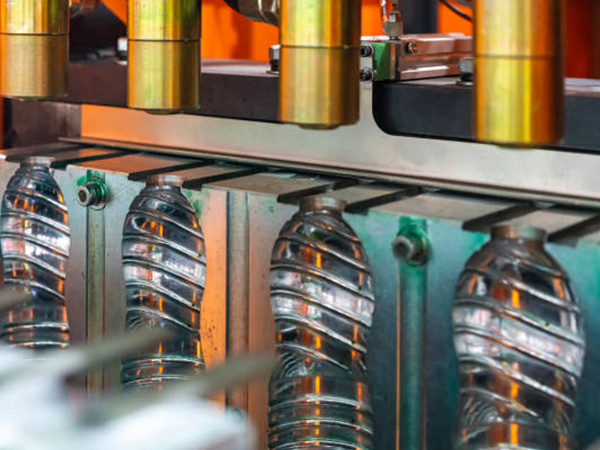
- Production Volume: If the production volume is low, a single cavity mold is the most suitable option. However, if the production volume is high, a multi-cavity mold would be the most efficient option.
- Part Quality: If the part requires a high level of quality control, a single cavity mold may be more appropriate as it allows for more consistent production. However, if the parts have simple geometries, multi-cavity molds may produce parts with consistent quality.
- Mold Cost: Single-cavity molding is less expensive compared to multi-cavity molds. If the production volume is low and the mold cost is a significant consideration, a single cavity mold may be the best option.
- Lead Time: If the production schedule is tight and the lead time is short, a multi-cavity mold may be the better option, as it can produce multiple parts simultaneously.
- Maintenance: Single cavity only has only one mold so the maintenance requirements and risk are low. Plastic multi-cavity moulds, on the other hand, have high maintenance and risk factors. If one cavity is faulty, the entire mold may become useless, which can severely affect the turnaround time to meet market demands.
Seaskymedical: Custom Plastic Molding for All Your Needs
Seaskymedical is a specialized medical plastic injection molding producer with extensive expertise in handling every injection molding process, including product design & development, mold design & building, and material selection. Thanks to our professional staff with more than 10 years of experience, we cater to all client’s demands with strict adherence to the stated specifications. We work with you to ensure the success of your project.
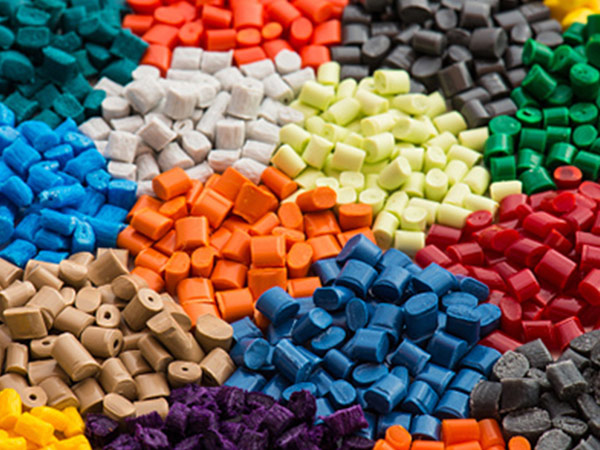
We offer various designs of custom plastic molds, including single cavity mold and multi-cavity mold. They are fabricated consciously to encapsulate your requirements and produce the desired plastic part. Using premium raw materials and cutting-edge machinery, the molds are manufactured to be very durable, functional, and capable of countless injection cycles without deformity or inconsistency with production.
Seaskymedical is a one-stop manufacturer, that provides all the services you need. Our other expertise includes various types of injection molding processes, such as cleanroom injection molding, micro injection molding, medical insert molding, and medical overmolding.
Final Thoughts
It’s always beneficial to know your market and have a solid understanding of their demand, so you can design and manufacture to suit their needs and by doing so, eliminate unnecessary costs. Proper utilization of the time and substantial cost needed to create a mold for making plastic parts includes selecting between single cavity vs multi cavity mold, which must be done with due diligence to the demand of the marketplace and the best mold type.
At Seaskymedical, we specialize in all things plastic injection molding, including mold design and development. If you need professional assistance with the perfect mold for your application, contact us for further guidance.
Frequently Asked Questions
Another popular type of injection molding cavity is family mold cavity. Explained below are the advantages, and disadvantages of family mold, as well as its comparison with multi-cavity mold.
What is the Difference Between Family Mold and Multi Cavity Mold?
Multi-cavity mold and family mold are both used in plastic injection molding to create multiple identical parts in one cycle. However, they differ in their design and functionality.
- A multi-cavity mold is a type of mold that produces multiple identical parts in a single shot, but each cavity produces a different part. It is typically used when different parts need to be produced in the same cycle.
- A family mold, on the other hand, is a type of mold that produces multiple identical parts in one cycle, but each cavity produces the same part. It is commonly used when a part requires different features, such as holes or threads, and those features can be produced simultaneously in one cycle.
What are the Advantages of Family Mold?
The benefits of a family mold include reduced cycle time, lower tooling costs, and improved consistency of parts. Family molds require less floor space and support the manufacture of two or more identical parts in one injection cycle, hence increasing productivity.
What are the Disadvantages of Family Mold?
The downsides include longer lead times for design and tooling, difficulty in making design changes, and the risk of having to discard the entire mold if one cavity becomes damaged or requires maintenance. Additionally, family molds may not be suitable for certain complex parts that require specialized features or production techniques.