The injection molding gate system functions by directing the molten plastic from the molding machine’s nozzle. This means that if the gate injection molding is bad, the molten plastic won’t flow properly, which will lead to a potential defect in the plastic part. And this is very catastrophic when dealing with vital products like medical device injection molding, as the plastic parts are used to save human lives, hence they must be of top quality.
Understanding injection molding gate design is very important as it decides the outcome of the components produced. This guide will shed light on all you need to know about this and how to make the best use of it.
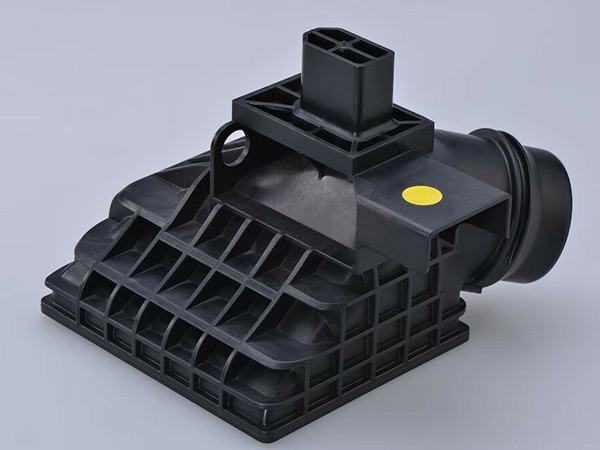
What is Gate Injection Molding?
Gate injection molding is a manufacturing process used to create plastic parts with high precision and accuracy. It involves melting plastic pellets in a heated barrel and injecting them under pressure into a closed mold. The molten plastic flows through a gate to fill the cavity of the mold and takes its shape. The success of this process, which is usually used for medical plastic injection molding, is determined by the gate design.
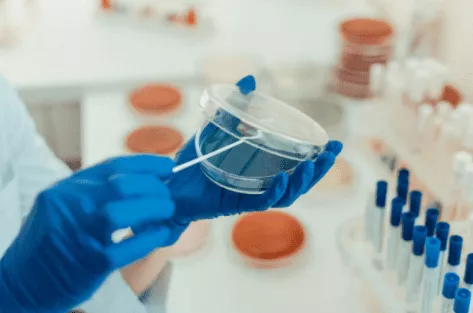
What are the Different Components of a Gate?
The functionality of injection molding gates encompasses different components and effects that are designed to support the free flow of the molten plastic.
- Sprue: This is the channel that connects the injection molding machine’s nozzle to the runner. It also serves as a reservoir for the molten plastic and helps maintain a consistent flow of plastic during the injection molding process.
- Runner: This is the part that directs the molten plastic from the sprue to the mold cavity. The size and shape of the runner can affect the plastic flow and the quality of the finished part. The runner gate design can be in various configurations, such as a single runner or multi-cavity runner.
- Auto-Degating: This is a process through which the molded parts are automatically separated from the runner and sprue during ejection. This is done using an automated system, which reduces the need for manual labor and increases the production efficiency.
- Manual Degating: This is the inverse of auto-dating. It involves manually separating the molded parts from the runner and sprue using a cutting tool or a similar device. It’s best for parts with complex geometries or where there is a risk of damage during auto-dating.
- Gate Vestige: This refers to the residual mark or protrusion left on the molded part after the gate is removed. While it’s a natural effect of the injection molding process, it can be reduced using an appropriate runner and gate design, as well as post-processing methods like sanding and polishing.
What are the Different Types of Gates in Injection Molding?
Gates come in different types and designs, each of which has its peculiarity. It is important to know this so as to choose the best option for your customized plastic injection molding process.
- Edge Gate: Also known as standard gate, this is a type of injection mold gate design where the molten plastic enters the mold cavity through a thin edge. The gate’s cross-section is a rectangle shape and it can be tapered between the part and the runner. It’s commonly used for parts with simple geometries and can be easily removed after molding.
- Pinpoint Gate: This is a small gate that is ideal for parts that require high precision. The pin point gate design is used with fast-flowing plastic and when the part’s appearance is very important. It’s typically used with plastic parts that cannot have vestiges on the sides of the parting line.
- Sub Gate: This is an injection mold gate design where the molten plastic enters the mold cavity through a small opening located below the parting line of the mold. It’s commonly used for parts with complex geometries and it can help hide gate blemishes.
- Cashew Gate: The shape of this gate molding design resembles a cashew nut. This type of gate is typically used for molding larger plastic parts as it helps to distribute the flow of molten plastic evenly throughout the mold cavity.
- Diaphragm Gate: With this gate design, the molten plastic enters the mold cavity through a thin, flat diaphragm. This type is commonly used for round or cylindrical parts that require concentricity. The diaphragm gate is hard to remove and costly to trim.
- Direct or Sprue Gate: This is a minimally trimmed gate that helps to produce a form of symmetrical filling of single cavity molds. It’s often used for creating large cylindrical parts, as it supports the injection of a high volume of plastic into the mold cavity.
How Does Injection Molding Gate Design Affect the Part’s Quality?
All types of gate injection molding designs have the same working process. They force molten plastic into the mold cavity using high pressure, which accelerates the speed and increases the plastic heat. This process may lead to several effects on the plastic part and because of this. Discussed below are the two most common effects that could occur:
Jetting
This occurs when the molten plastic flows into the mold cavity at high velocity through a small gate. A gate that’s too small makes the pressure drop as the molten plastic moves into the cavity, causing the plastic to deflect off the cavity surface and create a visible pattern effect on the molded part. This also happens when using amorphous materials with high melt flow rates or when the gate is located far from the thickest part of the component.
With jetting, rather than the plastic flowing smoothly into the core, it sprays the core. This leads to a wavy distortion that manufacturers call “worming.” It also results in appearance defects like flow marks, weld lines, or sink marks, and it also compromises the strength and structural integrity of the part.
This effect is more noticeable with clean room injection molding as it disrupts the whole sterility process. Therefore, it’s essential to optimize the injection mold gate design to minimize the jetting effect and achieve a smooth and uniform filling of the cavity.
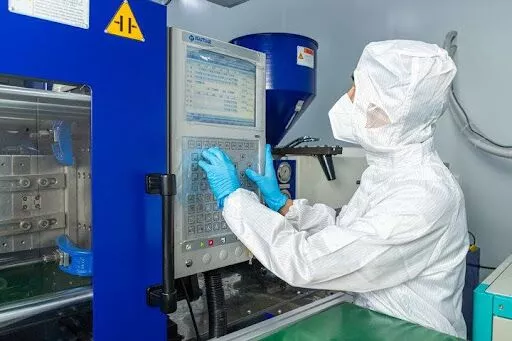
Overheating
A high injection speed of the molten plastic through the gate causes friction. And when the heat becomes too much, it can lead to the thermal degradation of the polymer.
However, reducing the speed of the injection to avoid the polymer’s decay may lead to other defects like poor mechanical properties, discoloration, or even burn marks on the part’s surface. And a slower cycle time results in the production of fewer parts per hour, which increases processing costs.
To avoid overheating, it is necessary to use a mold gate design that allows for a smooth and gradual filling of the mold cavity, which will reduce shear stress and minimize the generation of heat. And if a small gate is to be used, it’s advisable to divide the resin over a number of separate gate openings. This will help to dissipate pressure and avoid overheating, however, it creates many flow fronts which may cause weld lines and gas traps where the fronts meet in the cavity.
Why is Gate Molding Design Important?
Injection molding gates play a critical role in the production of high-quality parts. The gate is the point of entry for molten plastic into the mold cavity and its design affects the filling pattern, cooling time, and the pressure and temperature conditions experienced by the molten plastic during the injection molding process.
The gate design determines how the plastic flows into the mold cavity and how it cools and solidifies, which can significantly affect the molded part’s dimensional accuracy, surface quality, and mechanical properties. A well-designed gate ensures that the plastic fills the mold cavity uniformly, without creating turbulence or high shear stress that can lead to defects or structural weakness.
A gate molding design optimized for the specific plastic material being used helps to avoid injection molding defect issues like flow marks, burn marks, warpage, or even part failure, which can result in production delays, waste, and increased costs.
Tips for Injection Mold Gate Design
There are certain important factors you need to consider when designing injection molding gates. You need to pay attention to some things that could influence the functionality of the gate.
- Number: The number of gates required depends on the geometry and size of the part, the required production volume, and the type of material being used. More gates can help to reduce cycle time by allowing for faster filling of the mold cavity, but too many gates can increase the complexity and cost of the mold.
- Location: The location of the gate should be carefully selected to ensure that the molten plastic can flow evenly throughout the part. The gate should be placed in the deepest cross-section as this reduces sinking and voids. You should not place the gate close to pins, cores, or other obstructive components.
For complete filling and cooling, the gates should be the closest to the thick-wall areas. And it should be positioned to minimize the appearance of visible gate marks or blemishes on the finished part.
- Size: The size of the gate determines the rate at which the molten plastic enters the mold cavity. A gate that is too small can result in incomplete filling of the part or insufficient packing pressure, while a gate that is too large can cause excessive shear stress and warping of the part. So, the mold gate design must be appropriate; not too large or too small.
- Shape: The gate must be designed to minimize turbulence and pressure drop, and it should be shaped to match the geometry of the part. Common gate shapes include rectangular, circular, and trapezoidal, and the selection of the shape will depend on the specific requirements of the part and the molding process.
Seaskymedical: High-caliber Plastic Injection Mold Manufacturer
Seaskymedical is an all-in-one plastic molding company with extensive capability in handling all kinds of medical plastic injection molding projects starting from the design and development stage till completion. As an ISO-certified plastic injection manufacturer, we make use of approved raw materials and carry out the injection molding process in our ISO 8 clean room using reliable machines.
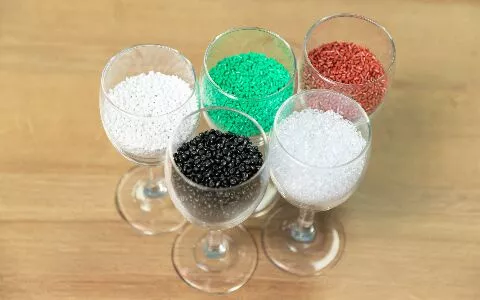
With over 10 years experience, a R&D team that has rich knowledge and ability to deal with various medical grade plastics, as well as the capability of conducting different types of injection molding, such as clean room injection molding, micro injection molding, medical insert injection molding (Check: 101 Injection Molding Runner Design Guideline), and medical overmolding.
As a professional manufacturer, all our productions are made of mold gate designs that support the smooth flow of molten plastic, ensuring that the final piece comes out as desired. Having a wide range of expertise, we make use of different types of injection mold gate design with due diligence of the factors needed to ensure that the project is a success.
Conclusion
Gate molding design is a crucial part of the injection molding process that must be gotten right, or else the quality of the molded part will be compromised. Determining variables like the number of gates, the location, the sizes, and the shapes must be considered when designing the gates to ensure production efficiency.
Having a solid understanding of the gate injection molding designs helps us in offering the best injection molding services. You can contact us to get more professional insights.