When it comes to injection molding, hot runner vs cold runner are two of the most popular techniques. Businesses in the manufacturing industry must decide which one will be best for their product. Understanding the distinction between the two is key to making an informed decision when selecting the ideal injection molding process.
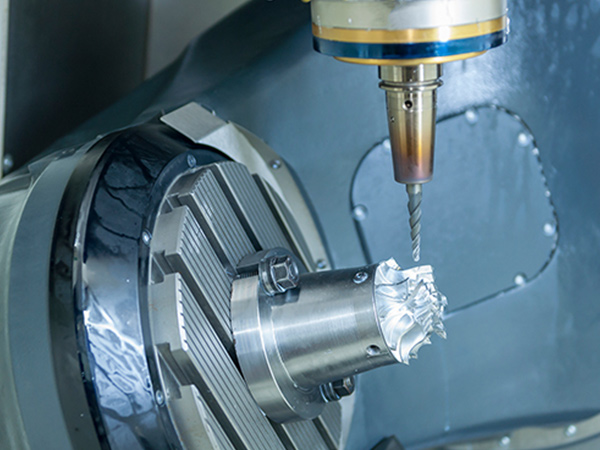
Hot runner technology has become popular in recent years due to its versatility and ability to reduce cycle times, while cold runner systems remain favored due to their cost-effectiveness and simpler design. By understanding both processes, businesses can make educated decisions.
The Basic Intro to Cold Runner vs Hot Runner
Injection molding is widely used by some plastic molding company for producing complex plastic parts. In this process, plastic is melted and inserted into a mold where it cools down and solidifies to form the desired shape. Two common types of injection molding systems are a cold runner and hot runner systems (Knowledge: 101 Injection Molding Runner Design Guideline)..
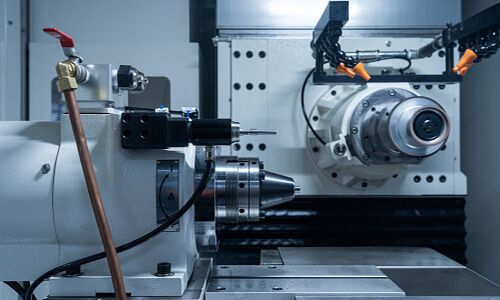
Cold Runner System in Injection Molding
Cold runner system is one of the traditional methods of runner injection molding, which uses a separate runner to deliver the molten plastic from the machine nozzle to the mold cavities. It has been used for decades and is a simple, yet effective method of injection molding.
- Definition
The cold runner system is an injection molding system that uses a separate channel or runner to deliver molten plastic from the machine nozzle to the mold cavities. The runner is typically made of the same material as the part and is cooled along with the part before being ejected.
The cold runner system is simple and easy to use but generates waste material, which needs to be disposed of or recycled. The runner is typically made of the same material as the part being molded, and it is cooled along with the part before being ejected from the mold. The cooling process solidifies the plastic in the runner.
- Types of Cold Runner
- Two-plate cold runner system
- Three-plate cold runner system
- Insulated runner system
- Valve gate cold runner system
Hot Runner System in Injection Molding
Hot runner system in injection molding is an advanced and efficient method that has gained popularity in many industries, including medical device manufacturing who offers medical device injection molding.
- Definition
The hot runner system is an injection molding system that uses a heated manifold and hot nozzles to deliver molten plastic directly into the mold cavities, without the need for a separate runner. The hot runner system keeps the plastic in a molten state throughout the process.
The heat from the manifold and nozzles keeps the plastic in a molten state, which eliminates the need for a cold runner and reduces material waste. The injection molding hot runner is more complex and expensive than the cold runner system, but it has several advantages, including improved part quality, reduced cycle times, and reduced material waste.
- Types of Hot Runner
- Open gate hot runner system
- Valve gate hot runner system
- Insulated runner system
- Sequential valve gate hot runner system
Hot Runner vs Cold Runner: Which Is Better for Your Product?
Choosing between a hot runner vs cold runner injection molding can be a challenging decision. Both systems have their benefits and drawbacks, and the choice ultimately depends on the product’s specific requirements, production volume, and budget. In this section, explore the differences between hot runner and cold runner systems and this will help determine which system is better for a product.
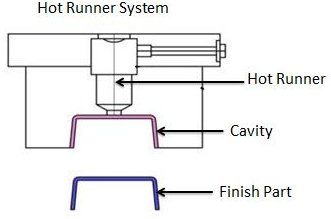
The Pros of Hot Runner
The hot runner system has several advantages over the cold runner system, including:
- Faster Cycle Time: In plastic injection molding, cycle time describes the total amount of time it takes to finish one cycle of the molding process. This includes the time it takes to inject the plastic into the mold, cool the mold, and remove the finished product.
The hot runner system is a type of injection molding system that eliminates the need for the runner to cool down, resulting in a faster cycle time. Since the hot runner system eliminates the need for the runner to cool down, the cycle time is reduced, resulting in a higher production rate.
- More Cost-Effective: The hot runner system has a higher starting cost; however, it has the potential to be more cost-effective in the long run due to the decreased amount of material waste, the quicker cycle times, and the improved part quality.
- Automated Injection Molding Process: In an automated injection molding process, the various stages of the process are performed by machines and equipment, rather than relying on human labor. By integrating the hot runner system with an automated process, the entire injection molding process can be streamlined, resulting in improved production efficiency and reduced labor costs.
- Flexibility in injection mold design: The hot runner system uses a heated manifold that distributes the molten plastic directly to the mold cavity, without the need for a separate runner channel. This eliminates material waste and reduces cycle time, allowing for more efficient and cost-effective production.
The Cons of Hot Runner
Despite its advantages, the hot runner system also has some disadvantages, including:
- Higher initial investment: The cost of the hot runner system is higher than the cost of the cold runner system because the hot runner system requires more complicated equipment and additional components.
- Required high-end equipment: It could happen that the specialized, high-end equipment needed for the hot runner system will not be easily accessible, which will result in an increase in the system’s original cost.
The Working Principle of Hot Runner
The hot runner system consists of a series of heated channels, nozzles, and gates that deliver molten plastic directly to the mold cavity. The system is typically controlled by a temperature controller that monitors and adjusts the temperature of the heating elements.
Here’s how the hot runner system works:
- The plastic material is fed into the heated manifold through a feed opening.
- The manifold heats up the plastic, keeping it in a molten state.
- The molten plastic flows through heated channels, which are designed to maintain the plastic’s temperature and prevent it from solidifying.
- The plastic then enters the mold cavity through a nozzle and a gate, where it cools and solidifies.
- After the part is formed, the mold opens, and the part is ejected.
The Advantages of Cold Runner
When asking what is the difference between hot runner and cold runner, they have different pros and cons that need to be considered. The cold runner system also has several advantages over the hot runner system, including:
- Lower Investment Cost: The cold runner system requires fewer components and less complex equipment than hot runner systems, resulting in lower upfront costs. With cold runner systems, the molten plastic is injected into a runner, which is a channel that connects the injection molding machine nozzle to the cavities.
The runner is typically made of the same material as the mold and is ejected along with the part after the molding process is complete.
- Less Inspection and Maintenance: The design of a cold runner system is simpler compared to a hot runner system. A cold runner is essentially a simple channel that connects the injection molding machine nozzle to the cavities, whereas a hot runner system has more complex components such as manifolds, nozzles, and temperature controllers that require careful installation and maintenance.
As a result, cold runner systems require less frequent inspection and maintenance. Since the runner in a cold runner system is typically made of the same material as the mold and is ejected along with the part, there is no need to remove it and clean it between molding cycles.
- Suitable for Thermally Sensitive Polymers: The cold runner system is suitable for processing thermally sensitive polymers, such as some engineering plastics, that may be affected by the high temperatures used in the hot runner system.
The Disadvantages of Cold Runner
The cold runner system also has some disadvantages, including:
- Material Wastage: In the cold runner system, the runner is necessary to deliver the molten plastic from the injection molding machine to the mold cavity. The runner material is the same as the part being molded, and it solidifies and cools down during the injection process. This cooling and solidification of the runner material leads to a waste of material that must be removed and recycled, resulting in higher material costs.
- Slower Cycle Time: Cold runner systems typically require longer cooling times for the plastic material in the runners to solidify before the part can be ejected from the mold. This can increase the overall cycle time of the molding process, resulting in reduced production efficiency and higher costs.
One way to deal with this issue is to use specialized cooling techniques, such as conformal cooling, to reduce the cooling time of the mold and improve production efficiency. Additionally, using hot runner systems or other advanced molding techniques can eliminate the need for a runner system altogether, further reducing cycle times and improving efficiency.
The Working Principle of Cold Runner
The cold runner system works by delivering plastic material from the injection molding machine’s nozzle into a runner system that distributes the plastic into multiple cavities. The runner system is typically unheated and acts as a channel to transport the molten plastic to the mold cavities.
Here’s how the cold runner system works:
- The plastic material is fed into the injection molding machine’s hopper, where it is heated and melted.
- The molten plastic is injected into the runner system through the nozzle of the machine.
- The plastic flows through the unheated runner system and into the mold cavities.
- After the part is formed, the mold opens, and the part is ejected.
Factors to Consider When Choosing between Hot and Cold Runner
Learning the difference between cold runner and hot runner, and deciding which is better for customized plastic injection molding is still not easy that is why buyers should also know the several factors to consider which include:
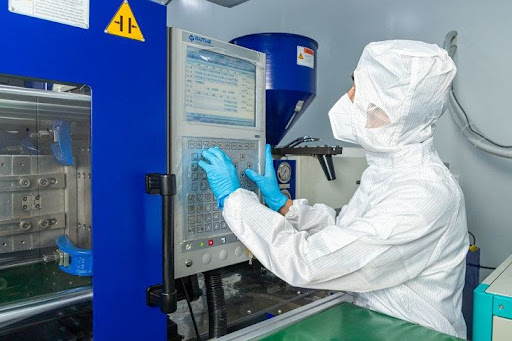
- Part Complexity: Hot runner systems are generally more suitable for complex parts with multiple cavities and intricate geometries due to their ability to fill complex mold cavities. Cold runner systems, on the other hand, are better suited for simpler parts with fewer cavities.
- Material Requirements: Hot runner systems can process a wider range of materials than cold runner systems, making them ideal for customized plastic injection molding projects that require specific materials that are sensitive to temperature changes.
- Production Volume: Hot runner systems are ideal for high-volume production runs due to their faster cycle times. However, cold runner systems may be more suitable for lower-volume production runs, where the reduced waste from the runner system can offset the longer cycle times.
- Cost: Cold runner systems have a lower initial cost than hot runner systems, making them a more attractive option for customers who are cost-sensitive. However, their higher material waste and longer cycle times can result in higher overall production costs.
- Maintenance Requirements: Hot runner systems require more maintenance than cold runner systems, which can lead to higher maintenance costs. Customers who prioritize lower maintenance costs may prefer a cold runner system.
- Design Flexibility: Hot runner systems offer more design flexibility than cold runner systems due to their ability to fill complex mold cavities and produce intricate part geometries. This can be an important consideration for customers who require unique or complex parts.
Overall, the choice between hot runner and cold runner systems for customized plastic injection molding will depend on the specific requirements of the project. A thorough understanding of these factors is necessary to make an informed decision about which system to use.
Conclusion
The choice between hot runner vs cold runner systems for medical plastic injection molding, for example, depends on various factors. Each system has its own positive and negative aspects, and choosing the right system for a project requires careful consideration of these factors.
Seaskymedical, a top medical device plastic injection manufacturer, weighs the pros and cons of each system and considers our unique needs, then consider the cleanliness requirements of our production process and must follow strict hygiene and cleanliness standards to meet regulatory requirements. Clean room injection molding is used by Seaskymedical to meet these criteria.
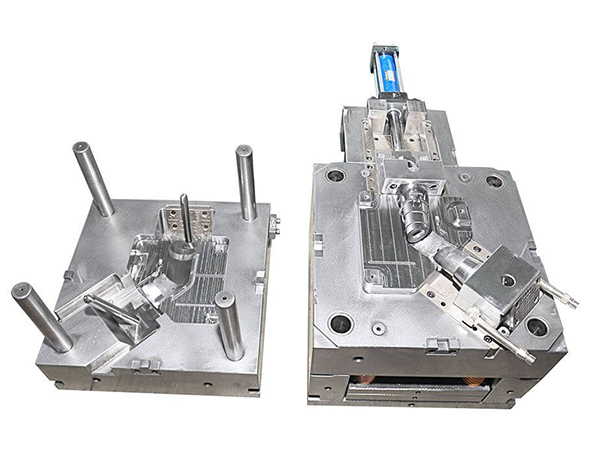
By considering the unique cleanliness requirements of our production process in addition to other factors, Seaskymedical can make informed decisions about which injection molding system to use for each product, ultimately delivering high-quality, safe medical devices to our customers. Contact us today to get a quote!