All businesses have numerous techniques to select from when designing a product that requires molded plastic parts based on the sort of application and part they want to make. Injection molding is a popular method for producing high-quality, cost-effective plastic products.
Injection molding is a manufacturing process used to produce items in high quantities ranging from thousands to millions. The method is highly adaptable and can create a wide range of parts for various applications suitable for different enterprise applications. Injection molding is also used in the medical sector. For injection molding needs, contact SeaSky for all molding requirements.
Common Injection Molding Products
Plastic injection molding uses span practically every industry, from medical to household items, automotive, and more. Here are a few injection molding examples:
- Medical Device Parts
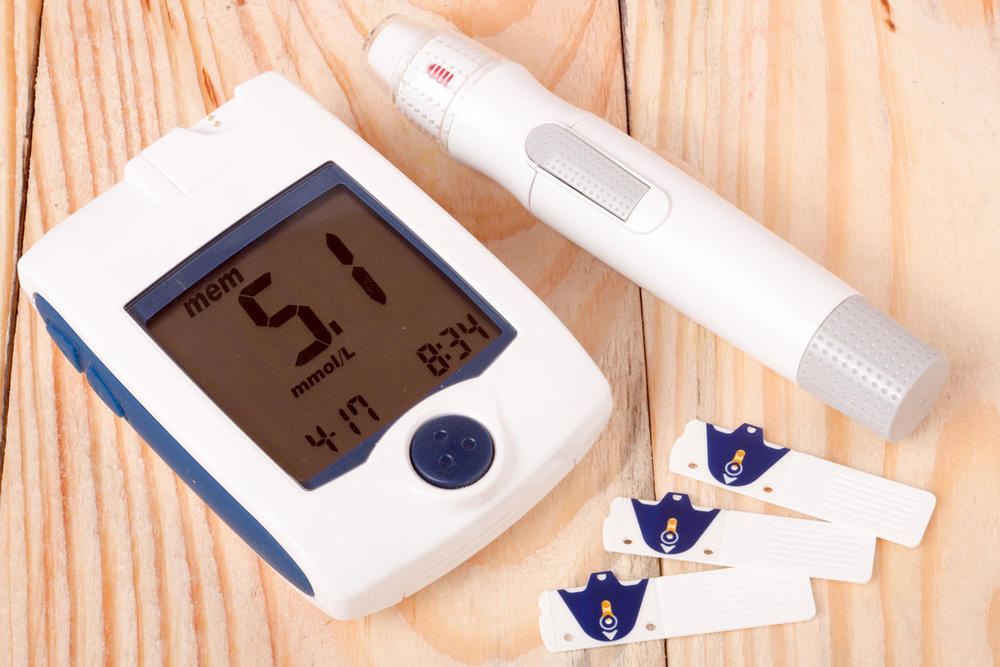
Injection molding is a popular production technology in the medical business, with several benefits for many applications. Medical component manufacturers utilize medical-grade plastic injection molding for various applications, including medical devices, laboratory equipment, and more. Plastic injection molding medical parts, components, and devices have been discovered to be one of the most successful ways for medical providers to achieve the quality and requirements they require cost-effectively and efficiently.
Thanks to their wide range of possible qualities, plastics are perfect for use in the medical industry. There are many alternatives because of the enormous selection of industrial plastics currently available as foundational materials for projects. Numerous plastics have been created to be used in the medical industry. These materials provide the required durability and usage while withstanding sterilizing treatments without harboring germs. There is no room for failure in high-risk applications. The durability of injection molding products in these high-stakes settings has been repeatedly demonstrated.
- Plastic Medical Disposables
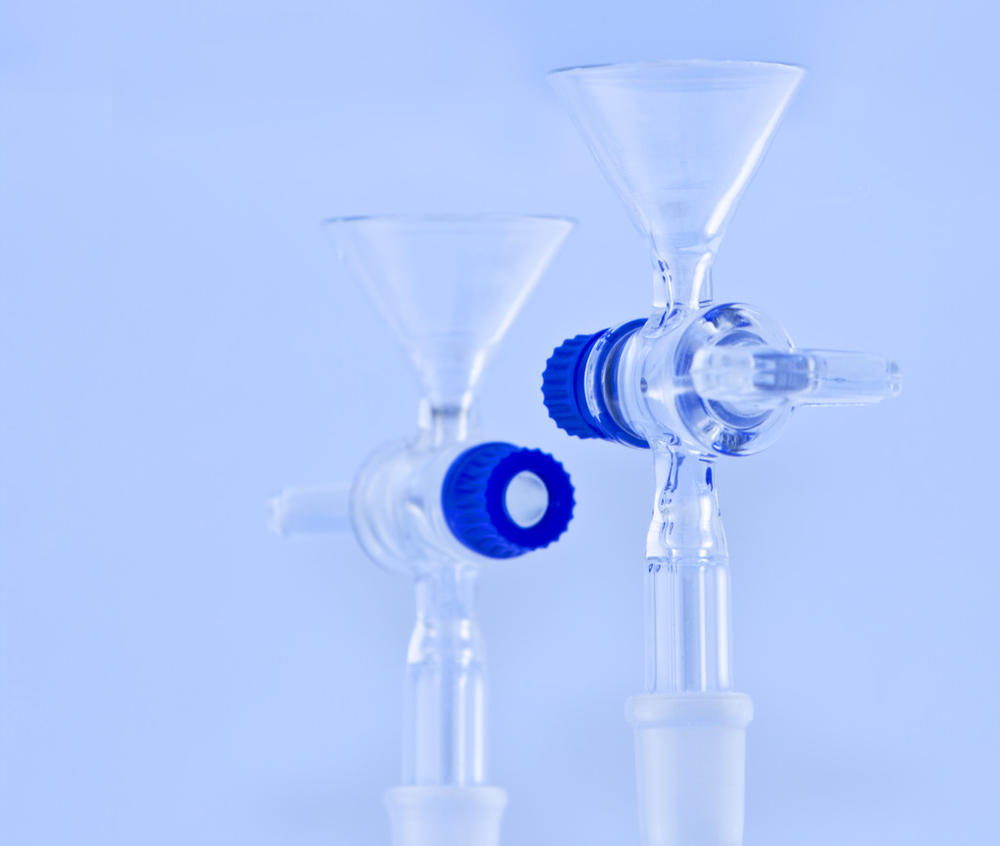
Thousands of goods in the healthcare industry are manufactured using the injection molding method. The healthcare business relies significantly on versatile plastic products that can be mass-produced, as there are many single-use products and throwaway items used to preserve sterility or to prevent the transmission of germs or diseases. Injection molding is what allows medical personnel to get their duties done. From plastic injections to throwaway surgical items, injection molding is excellent for such needs. Many medical plastic injection molding companies provide the best services and products.
- Electronics Enclosure
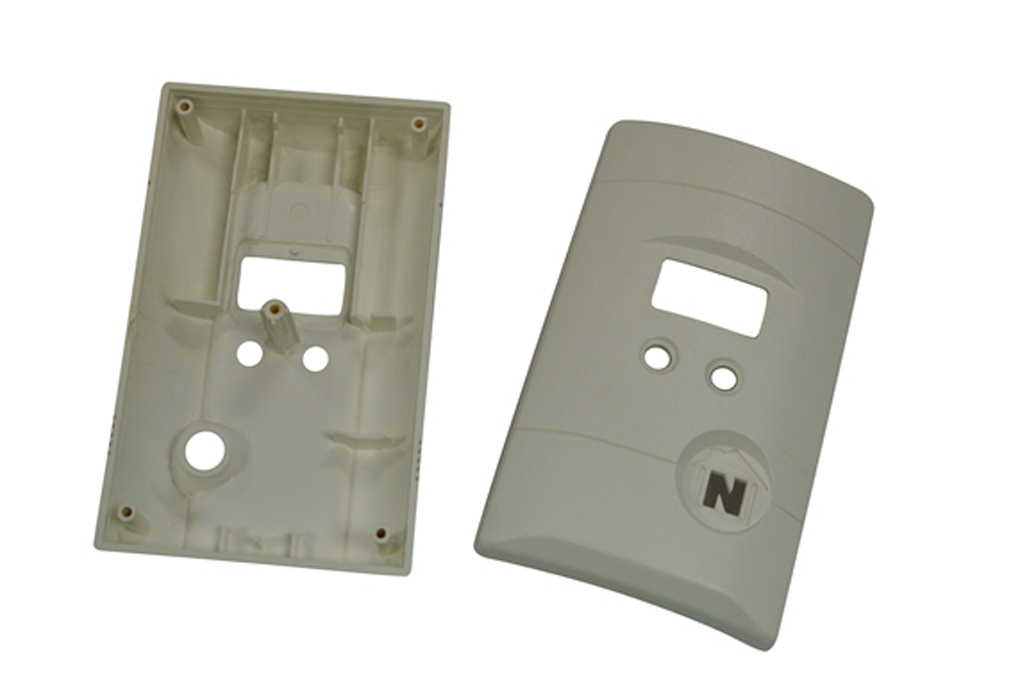
Plastic is a versatile material used in much electronic equipment. It can be constructed from conductive or non-conductive plastic resin, paired with waterproof sealing, UV resistant, and utilized in rigid or flexible applications, in various colors, with design options that extend beyond metal and other materials. Because custom plastic injection molding produces plastic molding for structural applications like switch components, boards, and supports for finished systems, electronic components are used in a wide range of applications.
- Machinery and Plastic Automobile Parts
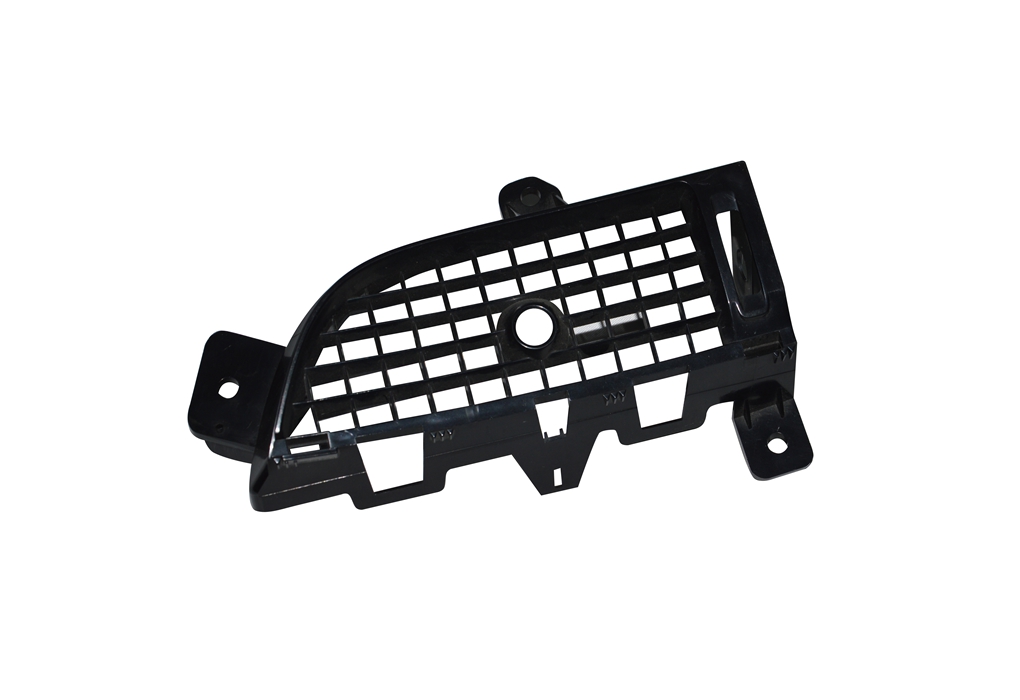
Plastic injection molding products are used in various automotive parts and machinery.. These are examples of such components: Dashboards, radio controls, bumpers, cup holders, car bumpers, and truck stairs. Plastic injection molded parts are prized for their long life and UV resistance. Plastic components are also lightweight, which helps vehicles run more efficiently.
Producing metal parts is more expensive and uses more energy than injection-molded plastics. This is why using components made of plastic injection molding is now standard practice in the car industry. To start with, plastic components are affordable to create, lightweight, and durable. Additionally, high-quality vehicle parts may be mass-produced via injection molding at a very cost-effective price.
- Plastic Chair: While the traditional wooden chair has a place in the house, many modern pieces of furniture, particularly chairs, are now made entirely of plastic. To ensure consistency across manufacturing runs, injection molds can make these parts to accurate tolerances. Making molds large enough to make full-sized furniture or components that the user at home will assemble is also simple.
- Home Appliances: Many consumer devices use electronic housings built from plastic injection molding. Injection molding, for example, produces typical household devices such as televisions, remote controls, laptops, and other items. Many electronics’ internal components are protected and insulated by injection molding products.
Many everyday home objects, such as containers, soap dispensers, and plastic kitchenware, are mass-produced using injection molding. Because of the technique’s versatility, or the flexibility that most shapes can be created due to the procedure, more complicated designs for household products are not a problem.
- Consumer Goods: Injection molding has traditionally been the preferred production method for most plastic consumer products due to its ability to create big volumes fast and cost-efficiently.
- Aerospace: Aerospace plastic injection molding has numerous advantages, making it a perfect process for producing the majority of components used in the aerospace sector. Designers can investigate part consolidation by applying injection molding to an aircraft’s interior components. This is accomplished by emphasizing design flexibility. This molding process may manufacture a variety of aircraft components.
- Food and Beverage Wares: Containers and other items in the food and beverage industry are carefully regulated to ensure they meet safety standards. As a result, manufacturers develop and construct parts using food-grade plastic materials, including plastic injection molding. Plastic injection methods can produce complicated, similar objects with minimal mistakes.
As a result, plastic is becoming a more popular alternative to metal, with distinct advantages in terms of food and beverage safety. For food and beverage products, the processing of products should be squeaky clean. Therefore, businesses have an option of clean room injection molding, a technology for manufacturing products in a safe and germ-free environment.
- Bottle: Each year, billions of plastic bottles of various shapes and sizes are produced. They are typically used to store potable water and other beverages and are composed of polyethylene terephthalate (PET), a robust and lightweight polymer. Injection molding is a standard method of producing plastic bottles. These are the most common products made by injection molding. Plastic injection molding is helpful for huge orders and mass production, and as a result, it is frequently utilized in the production of bottles.
- Bottle Caps: Each year, billions of plastic bottles are produced, as are billions of bottle caps. Bottle caps are necessary for a wide range of items, including water, soft drinks, liquid soap, and shampoo. Injection molded caps, both basic and complicated, are commonly used. From basic standard bottle caps to customized liquor bottle caps, they may all be products made from injection molding.
- Flower Pots: Clay pots look lovely, but they are pricey. Plastic flowerpots provide the same secure environment for plants to thrive, preventing breakage and lasting significantly longer. Because of the tooling design, these everyday objects and garden products also come out of injection molds since it is simple to make the requisite shape while keeping drainage holes at the bottom with few to no additional production costs.
- Building and Construction: Construction materials are created from various long-lasting polymers, each with unique properties that make them appropriate for various uses. They are frequently used in constructing floors, windows, roofing, and pipes. They are also used to make components and assemblies for numerous types of construction equipment. Injection molding is used to make molding products such as concrete beam conduits, roofing vents, insulation, and railing gaskets.
Additionally, any specification may be met while producing components for the construction industry utilizing plastic injection molding. This contains much larger pieces and very minute components that can be incorporated into complex constructions and designs. In other words, the plastic components can either fit into the smallest piece of machinery or be crucial to maintaining the stability of a structure or large-scale construction project.
- Agricultural Components: Plastic is replacing metal components in the agricultural business as a low-cost alternative. Plastic injection molded goods are more resistant to collisions, dampness, and harsh temperatures. UV compounds also help to protect plastic parts from severe weather and corrosive substances. Agricultural equipment parts must meet stringent performance, durability, and dependability requirements.
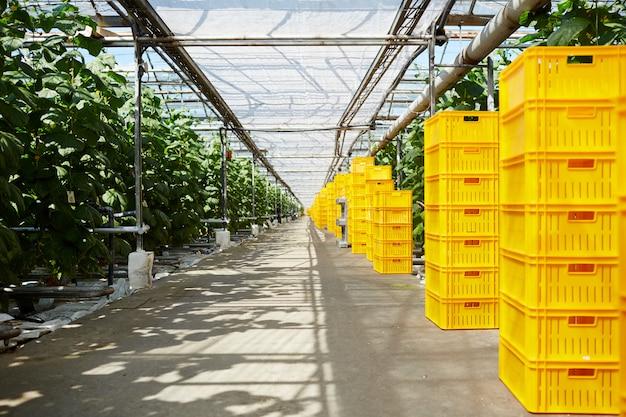
There are many uses for plastic injection molding products and components, including numerous farming applications. Food goods, irrigation system parts, water tanks, and variously utilized containers like tubs and bins can all be found in high-quality injection molding. Many different agricultural equipment types are assembled using various parts and spares produced by injection molding. As a result, the agricultural industry now relies heavily on high-quality injection moulded items, parts, and components that may be applied to various agricultural tasks.
Raw Materials Used In Injection Molding Products
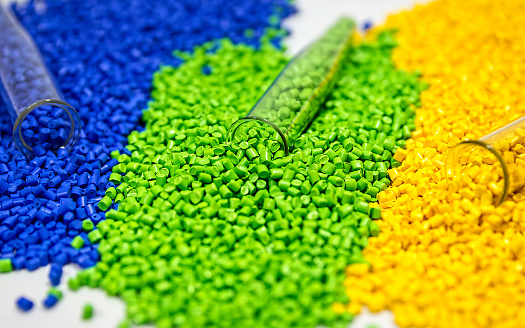
Injection molding is a typical method of thermoplastic production. Material selection is challenging, despite the fact that numerous common plastics can be used for injection molding.
Plastic injection molding materials come in a variety of shapes and sizes, each having a different purpose.
- Acrylic
Acrylic is a durable, transparent thermoplastic that is lighter and more shatter-resistant than glass. This material also has exceptional optical clarity, allowing a high percentage of light to pass through. Furthermore, acrylic is resistant to UV light and weather. Acrylic, unlike some polymers, can survive water exposure. This injection molded material used for molding products is also capable of maintaining tight tolerances.
- Silicone
Silicone components and parts are a suitable alternative when flexibility is required. It has outstanding biocompatibility and durability while remaining cost-effective for mass-producing goods via medical injection molding parts.
- Nylon
Nylon is used to make sturdy mechanical elements such as bushings and gears. It’s widely used in automotive applications since, in addition to being robust, it helps to minimize weight and production costs when compared to metal analogs. You should be warned that it tends to absorb water despite being a durable plastic.
- Acrylonitrile Butadiene Styrene (ABS)
ABS resin is an engineering-grade plastic that is an opaque thermoplastic polymer and has excellent use in plastic molding products. The use of ABS has numerous advantages. It is robust, dimensionally stable, resistant to impacts and scratches, and challenging to break. Furthermore, the low melting temperature facilitates molding. It’s widely used to make electronic equipment. What is the reason for this? Because ABS is a good insulator, it will not conduct electricity or emit smells if burned.
- High-Density Polyethylene (HDPE)
HDPE is the best material to utilize when a complex, heat-resistant plastic is required. Polyethylene is often used in kitchenware, storage containers, and refrigerator shelving since it is a food-grade plastic. HDPE is also excellent for storing chemical-based items like cleaning chemicals, bleach, and shampoo.
- Polycarbonate (PC)
PC is exceptionally robust, shatter-resistant, and impact resistant. It appears to be transparent. It also has the desirable property of retaining mechanical qualities and aesthetics throughout an extensive temperature range. As a result, it performs effectively in high-temperature conditions.
PC is also highly thermoplastic, which means it can be melted, cooled, and reheated without material degradation. This enables it to be easily injection molded and then recycled. Because it is a relatively pliant substance, it may be formed at room temperature without splitting or breaking. Because they are amorphous, they gradually soften rather than instantly converting from a solid to a liquid.
- Polypropylene (PP)
Because of its toughness and endurance, medical component manufacturers use PP. Polypropylene has chemical solid bonding, making it a better material for medical devices such as beakers and test tubes. Because of its moldability, polypropylene (PP) is one of the most commonly used materials for injection molding. It is adaptable, has a wide range of applications, and has a variety of unique qualities that make it an appealing alternative.
Despite its semi-crystalline structure, PP has a low melt viscosity, allowing it to flow easily. This allows manufacturers to fill the mold considerably faster, reducing production time for each shot. PP is also a low-cost material, making it cost-effective. It is very resistant to moisture, has exceptional chemical resistance and high impact strength, and is an excellent electrical insulator. Medical injection molding parts are created using injection molding in clean room.
Advantages Of Injection Molding For Molded Parts
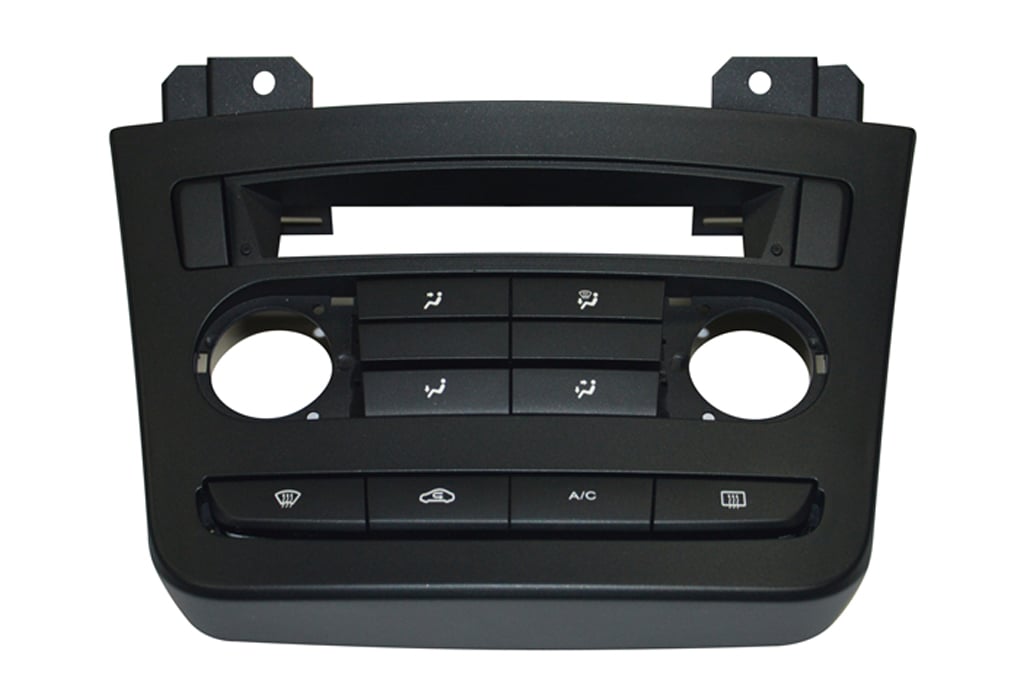
There’s a reason why plastic injection molding is quickly becoming the most preferred method for producing various plastic parts. It is a procedure that has various advantages over all other methods for producing plastic parts. The following are the primary advantages of outsourcing plastic injection molding to skilled professionals:
- Efficiency
This procedure is the most efficient method for making plastic parts, exceptionally when executed by experienced injection molding companies. Advanced mold design ensures that production issues are kept to a minimum throughout the cycle. In addition, cycle times are short, allowing for the manufacturing of a more significant number of components in the same amount of time.
- Offers Great Flexibility
The plastic injection molding part offers a great deal of design versatility. The technique’s flexibility allows clients to build bespoke designs based on their needs, which is an incredible advantage over the traditional molding approach.
It enables users to select numerous materials selections at the same time with accurate designs and color flexibility, which is one of the main benefits for clients in need of plastic parts. With the advancement of current technology, businesses can utilize numerous coloration processes and multiple finish appearances, such as the matte finish or distinctive textures that can be added to plastic using the plastic injection molding process.
- Increases Strength Of The Product
Plastics have evolved over the years. All industries require increased strength, durability, and precision. Even in the harshest settings, lightweight but robust plastic parts are now used. Unlike traditional equipment, plastic injection molding allows fillers to be added inside the injection molds.
Fillers contain various strength-enhancing elements such as silica, calcium carbonate, clay, etc. The fillers are specifically chosen to increase the material’s strength and stiffness. These fillers function by lowering the density of the plastic when it is in the molding process. This increases the strength of the molded pieces. Additionally, some additives improve the heat resistance of the polymers.
- Economical
One of the reasons for lower prices is the capacity of the plastic injection molding process to mass produce plastic parts with the least amount of time input and a high output ratio. Once the mold has been meticulously manufactured, it can be mass-produced for a longer run.
The procedure is mechanized, with little human participation, which decreases the possibility of human error and saves money on supervision. Because of automation, computers and robotics perform the majority of the job. They are the sole operators and can oversee and supervise the manufacturing process, which indirectly helps to reduce labor costs.
- Complex Designs
Plastic injection molding processes allow for the creation of complicated designs and the addition of numerous features to the pieces. Because the injection molds are used in high-pressure conditions, the plastics are squeezed harder, allowing for the creation of complicated designs.
This allows for creating complicated design details within plastic objects with perfect precision, which is unattainable with traditional molding equipment. Any plastic part can be manufactured with an accuracy level of 0.0001 inches. Furthermore, because the process is automatic, it can create the most complicated designs. Also, it is pretty affordable to produce molding products.
- Wider Selection Of Materials
Plastic injection molding materials are abundant. Antistatic plastic, chemical-resistant polymers, thermoplastic rubber, and other common materials are available. With masterbatch coloring or color compounding, there are virtually limitless color options.
Various polymers have different qualities that make them appropriate for various industrial operations. The capacity to use multiple types of plastics simultaneously is a superior feature of plastic injection molding. This is essential in circumstances where basic plastic qualities such as elasticity, color, density, texture, and other mechanical properties of the material must be altered. Injection molding allows you to utilize a variety of resins to manufacture the desired material. Furthermore, using different polymers helps to reduce total material costs.
- Fully Automated
The capacity to produce plastic parts in large quantities with full automation makes it one of the best methods to save money and time. This is one of the main reasons why the plastic injection molding method has lower labor costs. Furthermore, the molding machinery is designed to require as little supervision as possible.
The self-gating technology streamlines operations and manufacturing while requiring minimal human participation. Automation decreases the possibility of human error, which adds to the long list of advantages.
- Customization
High-complexity items can be designed using injection molding to meet customer requirements. Even if there are several design best practices for injection molding that guarantee effective production and adequate part quality and reliability, the options within these best practices are rather varied. Even when sticking to standards like rounded corners, tapered walls, and gradually changing wall thickness, designers and toolmakers for injection molding can satisfy even the most challenging specifications.
Injection molding also assures that the items produced require less after-production work. This is due to the fact that after being evacuated from the injection molds, the pieces have a more or less polished appearance. Plastic injection molding is now a low-impact method. Plastic scrap created during the manufacturing process is reused. As a result, relatively little trash is produced during the process.
Challenges Facing In Plastic Molding Products
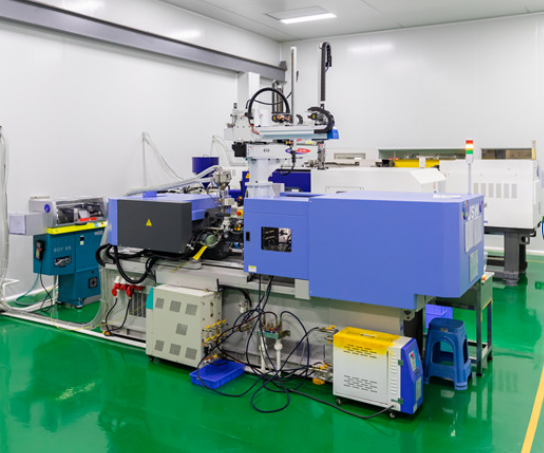
Incredible production speed, high efficiency, forms, and size flexibility are all advantages of plastic injection molding for manufacturing component methods. Furthermore, injection molding goods are precise in size and simple to replace, and mold parts can be molded into complex shapes. This environmentally friendly technology is appropriate for molding processing industries such as mass manufacturing and complex shape items.
Despite the operators’ familiarity with specialized equipment and operational abilities in the molding process of plastic components, numerous rapid injection molding faults on mold design and materials are unavoidable. The purpose of this section is to discuss plastic injection molding challenges.
- One of the few challenges of injection molding is the expensive initial tool and machinery cost.
- Small batches of parts may be less cost-effective if you wish to make parts in low numbers.
- It’s crucial to realize that there are some design constraints for plastic injection molding, but by working with an experienced design team, you should be able to overcome any initial challenges.
Conclusion
Although injection molding appears to be a complicated process, it is the most prevalent production method due to its versatility and efficiency to make a wide range of everyday objects. Injection molding is among the most cost-effective methods for producing working prototypes and finished items. All manufacturing businesses can decide on the best injection molding company by contacting SeaSky Medical.