A process that uses molten plastic injection molding is a popular manufacturing process that is very complex. A plastic molding company uses specialized electric and hydraulic machines to perform the difficult tasks of melting and molding. All these manufacturing companies take care of one thing for sure, the quality of plastic components used, and the results are high-quality products, ready to be supplied to the markets.
There is a reason injection molding is becoming more and more popular with days, and that is the high volume of production one can expect. It can produce volumes of parts made of materials like plastic, rubber, or even metal and glass. This complex manufacturing process enables abundant supply in much less time. But there remains this question, how does injection molding work? Well, the whole process relies on plastic that is converted into liquid form, and this melted plastic is further poured into the mold and pressed with hydraulic pressure.
What Is Injection Molding?
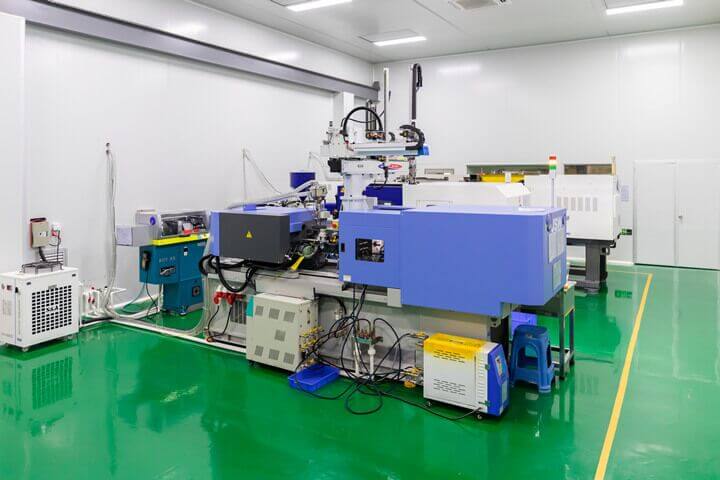
In general, injection molding is a complex manufacturing process involving turning raw materials into a liquid form, pouring them into a mold, and applying excessive pressure to give shape according to the mold design. This manufacturing process is used to produce various parts made of materials like rubber, plastic, metals, and glass.
Injection molding is a unique manufacturing way of injecting molten liquid into molds and shaping them. It is a very efficient mass-production process that involves solidifying the molten raw materials into valuable parts.
How Does Injection Molding Work?
The mechanism of injection molding machines may sound simple, but deep down, it is very complex. It is not easy to explain how does injection molding work or how different it is from other methods of manufacturing. However, injection molding has been regarded as a cost-effective method of manufacture that helps businesses cut down on their labor costs.
Plastic is the most common material selected in injection molding, but how does plastic injection moldingwork? Injection molding machines are extremely powerful and use hydraulic pressure to deliver parts. This machine consists of three components that are main functional parts; these parts include the heated barrel, the screw, and the feed hopper.
The manufacturing process begins with powdered plastic, converted into a molten liquid with the help of excess heat and eventually injected into the part, which is much like a mold cavity. This is the part where the molten liquid solidifies and gets its shape. Even if the manufacturing process of an injection molding machine may seem complicated, they promise excellent results and enhanced productivity. You can also discover about clean room injection molding and how benificial it is.
Reasons Why Injection Molding Is Good
There are many reasons why medical device injection molding is an efficient process and why many industries primarily rely on these machines. Here are the four most significant reasons behind their popularity:
Product ability Is High
The most significant quality of these machines is their ability to boost productivity. With the help of such powerful machines, various plastic parts can be manufactured in one go, meaning you get an assured voluminous production. This high predictability rate is undoubtedly the biggest reason industries profit.
Cost Efficient
Even if the manufacturing process is complicated, it is cost-effective. Since, in a single cycle, the raw materials are converted into finished plastic parts, many other costs attached to the production, such as labor and cleaning room charges, can be eliminated.
Less Tooling Needs
A complex injection molding machine simplifies the manufacturing process by eliminating the need for additional tools. Almost no engineer maintenance is required on a regular basis.
The Product Is Durable
Since reputed manufacturing companies use high-quality plastic components, the finished products are durable. The other main reason behind the durability of these plastic parts is their process of manufacture and the huge pressure and temperature conditions they have to go through.
An Eco-Friendly Process
Factory waste during product development is one of the major headaches and a significant cause of environmental pollution. Luckily, for injection molding machines, the manufacturing waste is minimal; hence, it is more eco-friendly. The scraps discarded by the machine during the manufacturing process are collected, recycled, and reused in molding.
Why Choose Seskymedical For Injection Molding Service?
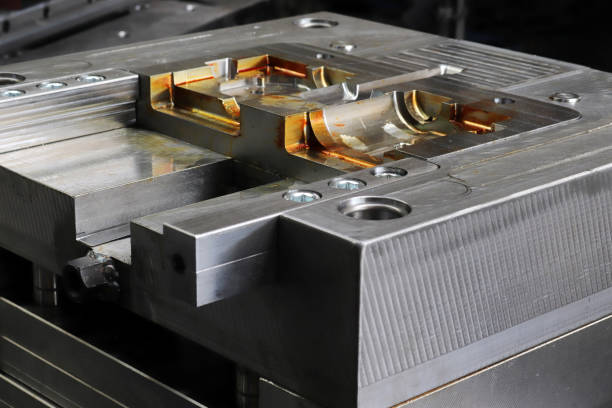
Among thousands of choices, finding an ideal injection molding company that promises quality products and services is incredibly challenging. Seskymedical is a leading common and medical plastic injection molding companywhose primary focus is to serve clients with high-quality molded products at affordable rates.
Now the biggest question arises, out of thousands of companies, why would you choose Sesky medical? And the reasons are not just one; there are many to count on. From using the most advanced technology to providing quality assurance, Seskymedical is one of those accredited and trustworthy molding companies.
This ISO-certified company based in China delivers top-notch customized injection molding products and has more than ten years of expertise in dealing with the needs of small or large industries. The best part about relying your faith on Seskymedical is their quick delivery time and paying attention to the needs of the clients. They use certified raw materials to make sure the quality of every molded plastic product.
Seskymedical can help you with mold making, 3D printing and prototype, mold design, material selection, and much more.
Final Words
Injection molding technology is essential in manufacturing vital medical, automotive, and aerospace parts. Since these advanced injection molding machines offer a lot of flexibility and a faster manufacturing process, they help in boosting the supply chain. Dealing with molten raw materials like plastic and metals can be risky; an injection molding machine eliminates the fear of injuries by fully automating the molding process. The manufacturing process requires minimal labor, which is why industries prefer these machines. If your business need common or medical plastics manufacturer, you can contact us here.