Rapid production of complicated and simple plastic components is a key advantage of injection molding, making it a popular manufacturing technique. In any medical plastic injection molding company, an injection mold is the central part of an injection molding process, as it is this mold that determines the shape of the part’s core and cavity and provides the area for the plastic to flow.
It takes a lot of practice and careful thought to select the right mold type and create the perfect mold. Injection molds made from plastic fall into a wide variety of categories. The two most frequent types of molds used by medical molding companies are known as cold runners and hot runners. Hot runners are typically more expensive than cold runners, but they also last longer and perform better.
A standard injection mold gating system allows for classification into three distinct categories:
- Two-plate mold
- Three-plate mold
- Hot runner mold
These three basic mold types eventually gave rise to other plastic molds, such as the side core pulling mechanism and the core-unscrewing de-molding mechanism.
What Is Two Plate mold?
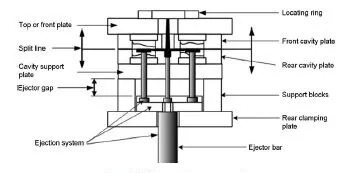
The most common and basic type of injection mold used by a medical plastic injection molding company is a two-plate mold, often known as a single-parting surface mold. P/L separates the two halves of the 2-plate mold into a movable half and a stationary half. The cavity side of the mold remains stationary, while the core side moves. The primary runner is positioned on the split surface, and the runner is located in the fixed mold.
Injection molding is unique in that the object being molded and the runner both remain in the same mold half and are expelled from the same parting surface. Furthermore, ejection mechanisms are installed in the movable mold half for releasing the products.
The mold for a two-plate mold has only one plane of separation. The gate and runner of a multi-cavity, two-plate mold are located in the mold’s splitting plane. When the mold breaks, the gate and runner will be ejected at the same time.
Advantages Of Two Plate Mold
The primary benefits of a two-plate mold are as follows:
- It’s easier to manage and run in production, which makes it more attractive. And because of that, its production costs are lower than those of competing molds.
- It also has a few operating issues, which bodes well for its longevity and ease of upkeep.
- Because of its shorter run distance and fewer constraints, the injection molding machine’s parameters can be easily set by the operator.
- The reduced cycle time offered by a two-plate mold is yet another major perk that can assist in bringing down product costs and boosting production throughout.
Disadvantages Of Two Plate Mold
A two-plate mold has the following major drawbacks.
- Both the dividing line and the gate must be in proper alignment.
- Getting the runner out of the way requires its own step-by-step procedure.
- In the event of a multi-cavity mold, the issue of short-shot
- Making a surface seem good can be expensive.
- False for components requiring a high degree of accuracy
Two Plate Mold Design
Two-plate mold design is one of the simplest injection mold architectures and offers a number of benefits despite its seeming simplicity. The A and B halves of a two-plate mold are its primary components. While side B is free to move, side A is held stationary and fixed when the injection machine is under stress, allowing for the injection molding of items.
Two Plate Mold Diagram
The two-plate mold has a two-part structure. One section of the mold tool design is immobile while the other is in constant motion. The mold’s cavity side stays put, while the core side rotates. A runner, located on the mold’s separating surface, is a fixed component of the tool. The injection-molded product and the runner remain in the movable mold section after the molding process is complete. Afterward, the runner and injection component is taken off the cutting edge.
Key components of Two Plate Mold
Components of the two-plate mold design include the following:
- The ejector pin is retracted into the mold and the mold is closed thanks to the return pin. Injection-molded products are safe from harm as well.
- Injects molten material into the cavity on the spurs.
- In order to ensure precise ejection, the ejector Guide Pin is used as a guide.
- When it comes to guiding, nothing is more reliable than a guide pin or bushing.
- Finding the hole between the spur and injection nozzle is easy with the help of this ring.
- Typically, S55C is used to make it.
What Is Three Plate mold?
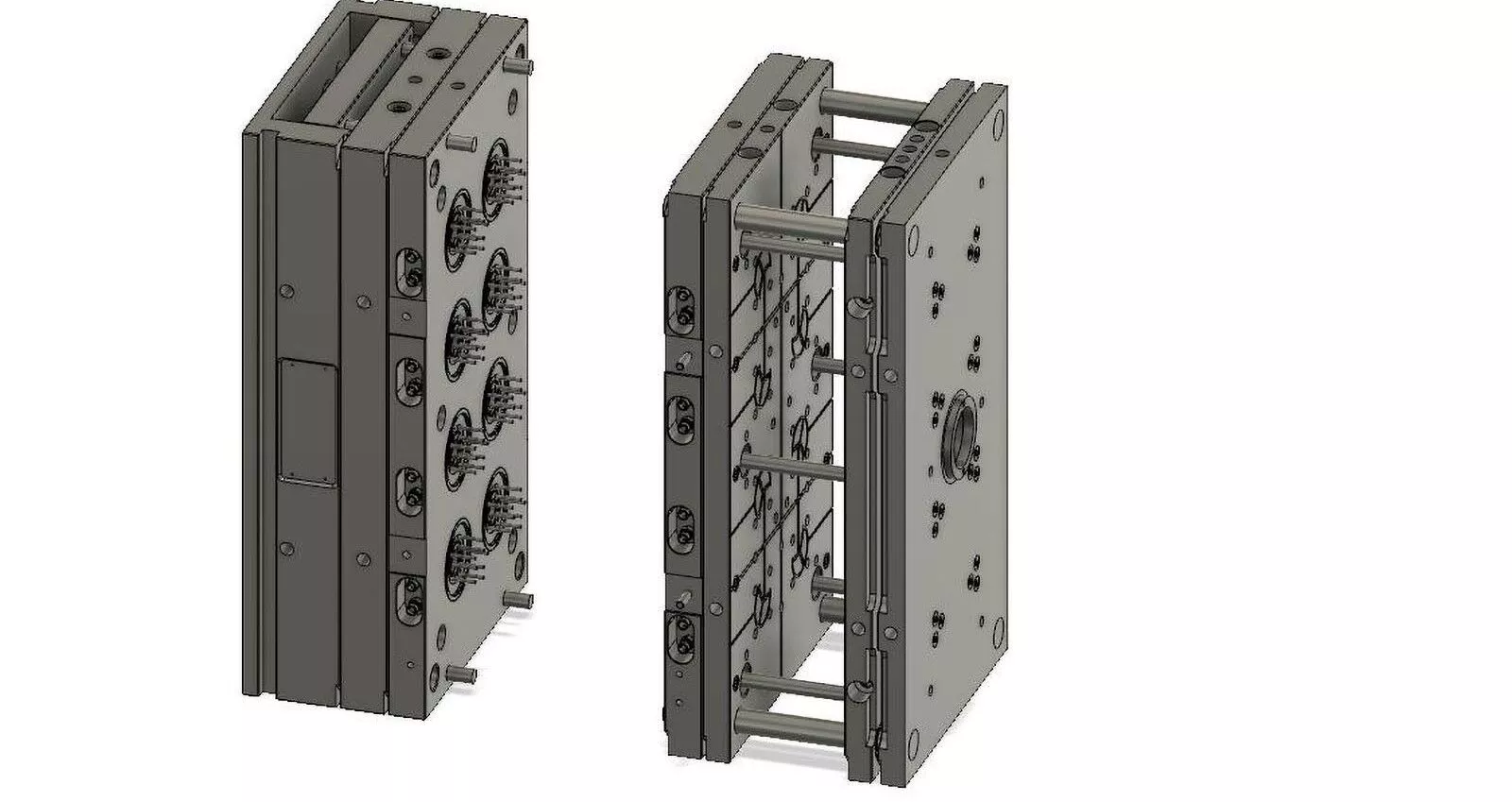
Often referred to as a “double parting surface mold,” a 3-plate mold serves multiple purposes.
A runner stripper plate is inserted between the top clamping plate and the cavity plate, creating a three-piece mold. When the part is too large for a two-plate mold, or when many injection locations are required, a three-plate mold is used. The gate can be better situated in a three-plate mold design. Products that cannot have gate marks along the sidewalls, or those with a big projection area and a need for multiple point gates, will benefit from this design.
One distinguishing feature of this mold design is the use of a very small gate. This mold requires an additional distance parting mechanism due to its complex structure. There are two types of three-plate mold: the standard mold and the simplified mold. Unlike more complex four-plate molds, simplified three-plate molds only use two guide pins to separate the two halves.
Advantages Of Three Plate Mold
The primary benefits of a two-plate mold are as follows:
- The gate can be better situated in a three-plate mold design.
- This enables pin-point gates and the possibility of a gate being placed in the exact centre of a plastic component.
- Three-plate molds have fewer moving parts and are less expensive to manufacture than hot-runner molds and two-plate molds.
- Some thermally sensitive materials are less likely to deteriorate.
Disadvantages Of Three Plate Mold
A two-plate mold has the following major drawbacks.
- Longer cycle times and further run distances are needed for three-plate molds.
- Therefore, a more capacious injection molding apparatus is required.
- Furthermore, while a three-plate mold might assist cut production costs, the runner trash can add extra material costs.
- To remove the sprue, a sprue puller is required.
Three Plate Mold Design
The three-plate mold is an economical and reliable backup plan. Round items molded with three plates of advanced prototype molding need to have uniform filling to avoid cracking. Check that the spaced gates are evenly distributed and filled all around that area.
Plates A and B are held together by releasable plate locks while the three-plate mold unfolds. The gate separates from that section when the sprue has been released. This time, the sprue is restrained in a floating plate by pins with undercuts. A series of stop bolts are activated when the A-side tooling is struck. They follow one another in rapid succession.
Afterwards, the pins are removed from the Sprue and the A and B portions of the part are separated, allowing the part to fall from the mold. After the mold is opened, the component can be removed exactly like any other two-plate plastic injection product.
Three Plate Mold Diagram
The three-plate mold’s three cavities are filled by a pinpoint gate in the mold’s centre. Typically, there are three distinct areas of the mold:
- This assembly’s first component is the feed plate.
- The core plate assembly is the third component, and the intermediate or cavity plate is the second.
- The opening sequence of the molded product is the basic design principle for the three-plate mold.
Knowing how a mold works requires an understanding of its design in its entirety. There are three distinct phases of mold release.
- First, the machine’s plates separate, separating the intermediate plate from the feed plate assembly. By holding on to the runner in this manner, one may break the gate with the help of all the other parts. The term “breaking initial stage” describes this period perfectly.
- The second phase sees the gates detach from the mold and full daylight reach the runner clearance. The second step, runner stripping and ejection, is subsequently performed on the molded product.
- In the third and final stage, the core is opened, and the molding is ejected. When the intermediate and feed plate assemblies stop moving, this is what happens. At this point, the mold can be manually expelled or peeled off the core to let in enough light.
Accurately setting the movement is also necessary to achieve the correct mold opening sequence. The closing operation of the molding machine is what achieves the closing of the mold.
Key Components of Three Plate Mold
More complicated than a two-plate mold is a three-plate mold, often known as a small gate mold. With its separate runner plate between the top clamp plate and cavity plate, the runner scrap and plastic molded pieces can be released independently.
Difference Between 2-plate and 3-plate mold
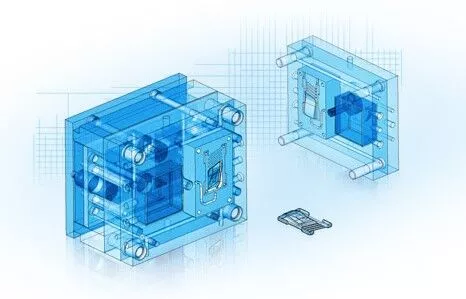
The two-plate mold and the three-plate mold are illustrated, showing their respective architectures. The following are the dissimilarities between the two.
Contrasting Forms
Guide pins and guide sleeves on the runner ejection plate; A separation mechanism with a fixed distance. The fixed distance splitting mechanism is what ensures the order and spacing of mold releases.
Variety of Mold Gate Methods
Precise gates are frequently utilised, and they can be placed anywhere in the cavity of a three-plate injection mold. The two-plate mold is often gated on the side and fed from the cavity’s exterior. There is also the option of feeding the product from the inside, which is useful when the product is either huge or has a large hole in the centre.
The cavity also allows for the cutting of the submerged gate. It is easier to achieve fully automated manufacturing with a three-plate mold, as the runner system and product are automatically severed during the production process, but in a two-plate mold, the runner system and product must be removed by hand.
Distinctive Breaking Line
Throughout the whole 2-plate mold injection molding process, there is just one PL. Product and injection system components are both extracted through the same opening. But in the three-plate mold injection molding process, the product and the injection system are removed through separate openings.
Cost Variability in Production
The production time and cost of a three-plate mold are both higher. Three-plate molds are more costly and time-consuming to produce because they necessitate extra steps in the manufacturing process. Due to the varied surface finish molds using three plates instead of two are more efficient and result in smoother surfaces.
Theory of Action Variation
During production, the gate can be removed without any human intervention thanks to the three-plate mold’s clever design. Good quality products may be made from a mold, and automation is possible. The quality of the finished product suffers because the gate of a two-plate mold must be trimmed by hand.
Variations in Sizing
The size range of a three-plate mold is greater than that of a two-plate mold. The mold failure possibility is significant, though, because of the intricate structure. There are variations in molding cycles, the cycle time of the three-plate mold is greater than that of the two-plate mold.
Conclusion
There are advantages and disadvantages to both two-plate and three-plate molds. Depending on the procedure and components, one could use any of these. The quantity of components that must be produced is another critical consideration. Any desired surface appearance and level of precision may be achieved in a three-plate mold, making them the standard for molding parts with defined appearance surfaces and high precision requirements.
Two-plate molds are more cost-effective and straightforward than their three-plate counterparts. Three-plate mold is not commonly used because of its drawbacks. It’s not only that there’s a lot more going on structurally, but there’s a lot more going wrong mechanically, and the scrap rate is considerably greater. Since the run distance is greater compared to a 2-plate mold, it is not optimal for high-volume manufacturing due to the longer cycle time and larger injection molding machine. Cooperating with Seasky Medical can help you solve all the problems encountered in the injection molding process, and the finished products of Sesky injection molding will definitely satisfy you.