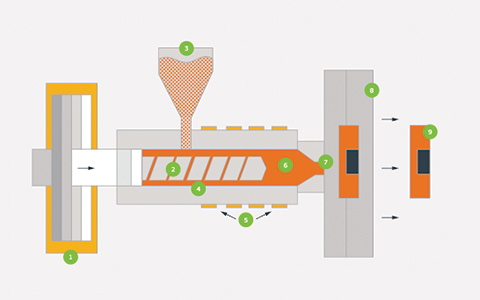
A typical plastic injection molding procedure is overmolding. In overmolding, a product is made from two or more materials. For instance, overmolding enables the creation of a plastic toothbrush with a plush handle. The exterior layer is referred to as the overmold material, while the center, typically the tougher portion is referred to as the substrate.
The substrate and the overmold material are frequently physically interlocked as well as chemically linked while making an over-molded component. This makes it more likely that the components will be assembled as a single unit. Many medical molding companies use overmolding for their benefit.
What is Overmolding?
An existing molded object can have a second layer of resin added to it using the tpu injection moulding technique known as overmolding to provide a combination of properties that no one material can. One of the most popular uses is to place a TPE (thermoplastic elastomer) layer of soft, useful, and hand-friendly rubber-like material over a hard substrate.
Another is to overmold material of a different color or finish to an item in order to alter or improve its look or “cosmetics.” Anything from toothbrushes to medical equipment(like medical plastic injection molding producer), hand tools, and assembly gaskets and seals can be made with overmolded materials.
How Does Overmolding Work?
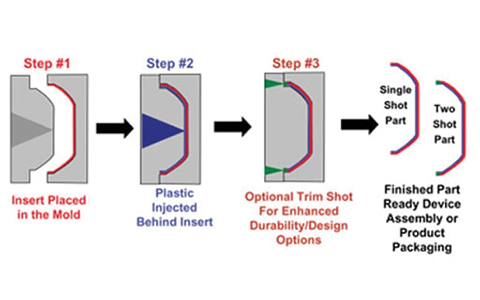
A machine part or component made by fusing two or more materials together is the end product of the overmolding process. Either the same materials or alternative materials can be used. There are essentially no limits to the material combinations.
We must comprehend the two elements of the process in order to have a better understanding of how it functions. Each overmolding job is divided into two components. The substrate is the first step in the process, while the overmold is the second.
The substrate serves as your starting point. Any of a huge range of materials could be used. Your overmold is the auxiliary substance. You want to “mold over” the substrate with this substance. There may be two or more overmolds present in some circumstances. The amount of overmolds is entirely dependent on the final product that is sought and the manufacturer’s creativity.
Complete Overmolding Process
Two or more components are molded on top of one another during the multi-step injection molding process known as overmolding. Due to the fact that overmolding is a two-step procedure, it is occasionally referred to as two-shot molding. A base component often referred to as a substrate, is first molded and given time to cure. Substrates for overmolding are frequently composed of plastic. To produce a single, solid component, a second layer is then directly formed on top of the first.
The process of overmolding is frequently employed to create plastic components with rubber handles. For instance, in the two-shot method of overmolding a toothbrush, a base layer for the plastic handle and a top layer of rubber are formed (to make the toothbrush less slippery to hold).
What Materials are Commonly Used in Injection Molding?
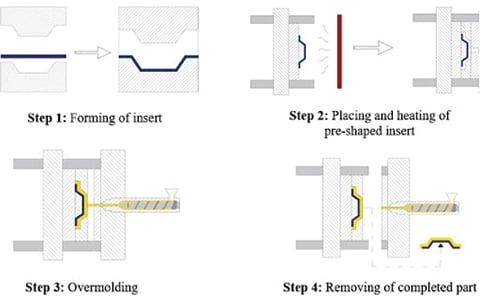
Making thermoplastics is frequently accomplished through the use of injection molding. While there are several popular plastics that can be used for clean room injection molding, material selection can be challenging. There are many distinct types of plastic injection molding materials, each with a specific function.
- Acrylonitrile Butadiene Styrene (ABS)
Acrylonitrile butadiene styrene is known as ABS. This type of thermoplastic injection molding material is commonly found in pipes, car body pieces, and keyboards. In addition to its beneficial qualities, ABS also offers a number of advantages. For instance, the material’s excellent impact resistance makes it difficult to break because it is strong yet lightweight. Additionally, it is heat- and temperature-resistant.
However, one drawback is that it is readily scratched, making it very sensitive to use. Furthermore, because it is made of oil and emits hot plastic vapors during production, it has the potential to be extremely harmful to the environment.
- Nylon
Due to its diverse nature, nylon, also known as polymer fabric, is one of the most adaptable injection molding materials. Along with fishnet and insulators, it is utilized in fish tires, automotive tires, and many types of clothing.
As an injection molding material, nylon has various benefits. One is that it is durable and elastic in nature due to its superior abrasion resistance. On the other hand, the material’s tendency to melt easily is a drawback. This makes using the material in its liquid condition difficult. Additionally, it directly or indirectly collects water from the air’s moisture.
- High-Density Polyethylene (HDPE)
High-density polyethylene is a thermoplastic that is used in injection molding and is mostly used to make plastic bottles, shampoo bottles, toys, and recycling bins, and flower pots. The key benefit of choosing HDPE is that it is both reasonably priced and made of rigid, highly durable material.
The drawbacks of HDPE include its high flammability and lack of biodegradability, which makes it difficult to dispose of. High-density polyethylene also has poor weathering and cannot be assembled.
- Low-Density Polyethylene (LDPE)
Low-density polyethylene is a lot softer and more flexible than high-density polyethylene. Bottles, plastic bags, and wraps, as well as playground slides, are all made with low-density polyethylene using the injection molding process. The resistance to chemicals and moisture of this material is advantageous. Additionally, it is affordable and of a high enough quality to be used in food, making it safe.
Low density also has the drawback of being potentially flammable and having weak temperature capability, making it risky near a fire. Additionally, it can be challenging to connect and has weak weather resilience.
- Polycarbonate (PC)
Transparent polycarbonate is a robust, durable injection molding material used in engineering. Bulletproof glass, safety hamlets, compact discs, and other electrical and telecommunication technology all contain PC.
The perks include its superb quality and practically intolerable bullet resistance. It also guards against discoloration, however prolonged UV light exposure might cause it to turn yellow. Additionally, it can be scratch-sensitive.
- Polyoxymethylene (POM)
POM, often known as acetal, is a robust, hard plastic injection molding substance that is made of polyoxymethylene. Automotive parts can be made using acetal. Acetal is also used in the manufacture of zippers, fan wheels, door handles, lock mechanisms, and insulin pens. The benefits include its high gloss finish and resistance to organic solvents and chemicals, with the exception of phenols.
The inability to bind well, low acid resistance, and UV sensitivity are its drawbacks.
- Acrylic Poly (Methyl Methacrylate) (PMMA)
Acrylic is one of the materials listed for injection molding that comes in a thin sheet and is frequently used as an alternative to glass. PMMA makes use of a wide variety of goods, including windows, eyeglass lenses, and car taillights. The benefits of acrylic include its high sheen, strong abrasion resistance, and ability to withstand weathering. However, it only has a limited heat resistance and is brittle under pressure, which is its drawback.
- Thermoplastic Polyurethane (TPU)
TPU offers a wide range of characteristics, including flexibility, transparency, and resistance. Its soft and hard portions are its characteristics. This kind of plastic is primarily used to make footwear, keyboard covers, and phone cases.
The benefit is that polyurethane has exceptional toughness and flexibility, is resistant to impacts like tearing, and is resistant to lubricants like grease and oil. Due to its low reactivity to tearing over time, it has good dimensional stability. However, one drawback is that, compared to other options, it is not cost-effective. It has a limited shelf life, too.
- Thermoplastic Rubber (TPR)
Elastomer, often known as thermoplastic rubber, is another substance used in injection molding. Rubber and plastic parts are mixed together in it. used in other applications as a home appliances and for automotive parts like wire and cable insulation. The benefits include the flexibility to stretch and recover to its original shape.
Because it doesn’t contain recyclable, non-toxic plastics, it is also less harmful to the environment. Additionally, obtaining this material might be rather expensive. The material can withstand high temperatures, although doing so could cause it to lose its rubbery quality.
- Polypropylene (PP)
Polypropylene, also known as polypropene, is the final material we will examine for injection molding. A thermoplastic polymer with a wide range of uses, polypropene is expected to have the highest revenue share in 2020, at 34.2 percent. Due to the fact that it doesn’t combine chemicals with food goods, it is most frequently used in the food storage and packing business. This material’s excellent impact strength and good moisture resistance are further advantages.
The drawbacks are that it can be weakened by UV and lose 70% of its power when exposed to sunlight. Additionally, it may be combustible because of the chemical it contains.
Overmold Material Compatibility Chart
OVERMOLD MATERIAL | ABS LUSTRAN | ABS/PC CYCOLO C2950-111 | PC LEXAN940-701 | PBT VALOX357-1001 | PP PROFAX 6323 | NYLON 66ZYTEL 103 HSL NC010 |
TPU – Texin983-000000 | C | C | C | C | M | M |
TPV – Santoprene101-87 | M | M | M | M | C | M |
TPE – Santoprene101-64 | M | M | M | M | C | M |
LSR – Elastosil3003/30 A/B | – | – | M | M | – | M |
TPC – Hytrel 3078 | C | C | C | C | M | M |
TPE-Versaflex OM1060X-1 | C | C | C | M | M | M |
TPE-Versaflex OM6240-1/td> | M | M | M | M | M | C |
TPE-Versaflex OM6258-1 | M | M | M | M | M | C |
TPE-Versaflex OM1040X-1 | C | C | C | M | M | M |
M = mechanical bond recommended
C = chemical bond
Advantages/ Features of Overmolding
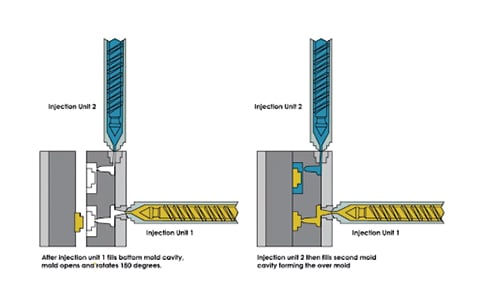
Increased Material Flexibility
Overmolding necessitates the assemblage of several components. Utilizing all of the advantages of the materials used increases the part’s flexibility. Additionally, producers can increase flexibility by using the overmolding design guide.
Elimination of Adhesives
Overloading does not require adhesives since overmolding allows diverse parts to fuse together naturally. As a result, the products’ durability improves. The cost of production has decreased overall as well.
Better Product Performance
Including additional high-quality materials improves a product’s performance greatly. Overmolded items have two material advantages over standard products utilized in industries. Because of this, overmolded items perform better.
Custom Plastic Parts
Overmolding has the benefit of enabling the design and production of unique plastic components for virtually any business. Overmolded items with high dimensional quality can be produced by manufacturers using a plastic-plastic or metal-plastic combination.
Almost any type of consumer or industrial object can be produced using the overmolding technique, including grips, handles, knobs, electronic components, moldings, bottle caps, and automotive parts. Customers are free to create their own overmolded goods as long as the resins and raw materials they employ are compatible.
Reduced Manufacturing Cost
Overmolding is completed in one cycle of operation. As a result of the lack of two- or multi-part assembly, the procedure is accelerated. They can lower their manufacturing costs and accelerate the entire process because overmolding eliminates the post-assembly stage.
Because of this, distribution periods for the finished product to various manufacturers and suppliers at different levels for OEM or aftermarket usage are shortened. The injection molding business can enhance production capacity with decreased manufacturing expenses.
Disadvantages of Overmolding
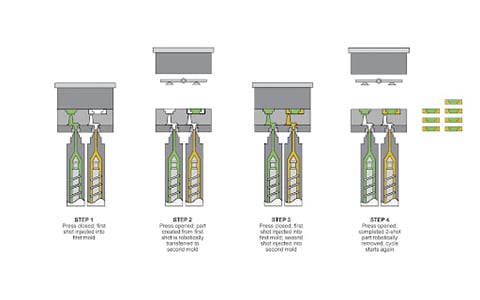
Multiple Production Methods
The production procedure involving overmolding involves two processes, lengthening the part cycle time. When you need to mold multiple parts in a single process, the cost of production tends to rise. Additionally, because overmolding is a two-step operation, it takes more tools than a single molding.
Debonding
If two different pieces are bonded together in an injection mold, there is a possibility of delamination. When the ideal temperature range fluctuates, delamination will happen. When the materials cannot be properly bonded together with the heat available, mechanical interlocks are required.
Applications of Overmolding
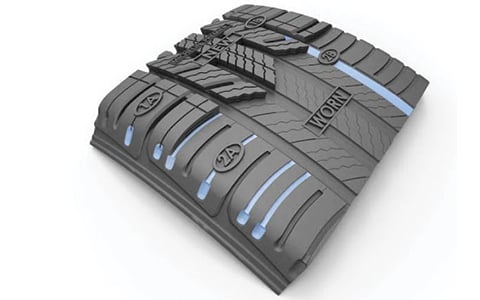
Hardware Tools
In many hardware tools, overmolding is perfectly illustrated. These might include blades, pocket knives, pliers, wrenches, hammers, tape measures, and other similar tools.
The primary machining components for these materials are typically composed of tool steel, which can be used for cutting, bending, drawing, punching, and other sorts of fabricating processes. But before the steel can be used, it must be handled safely and ergonomically by the end-user; this is where overmolding comes in.
Surgical Products
Precision and product safety are important factors in the medical sector. When employing various kinds of surgical tools, professionals like doctors, surgeons, nurses, and medical equipment parts manufacturers and medical device contract manufacturing companies should also be able to rely on safe plastic materials. Additionally, in order to avoid infection, this equipment should be sterile and simple to clean.
Having said that, overmolding has also been widely utilized in this business. Overmolding is a process used to make a variety of medical products, including housing for equipment and surgical instruments, to produce a final portion that facilitates use. Syringes, patient monitors, lab consumables, needles, catheters, dilators, soft-touch buttons, and many more are a few examples.
Common Household Items
As was previously noted, one benefit of overmolding is that it enhances grip, use, and cleanliness in numerous products. In addition to these, overmolding uses components to increase a product’s chemical resistance, vibration dampening, sound insulation, and many other properties.
It should come as no surprise that many common home objects, including toothbrushes, kitchen utensils, portable electric fans, mirrors, pens, multi-port chargers, shampoo bottles, reusable food containers, and the like, are created from overmolding.
Car Trim
The pieces that are located in various regions of the automobiles, such as the door edge, side body, fender, bumper, wheel, and other areas in the interior, are referred to as car trims or car moldings. Car trims have certain practical advantages, particularly in lowering the weight of the vehicle, despite the fact that they are frequently fitted for their visual appeal.
The customer’s desired colors can be used to create custom or pre-set automotive trims. In order to be molded with additional materials, such as steel, chromium, or any type of metal plating, these overmolded trims can also go through a different procedure known as insert molding.
Cookware
Plastic must always be food-safe when used to make things like cookware, food containers, and kitchen utensils. Given this, it should come as no surprise that overmolding should be a crucial process used in the production of cookware parts and components.
Overmolding is used in cookware for a variety of purposes, such as spatula handles, pot covers, strove trimmings, knives, cutting boards, and more. These products use high-grade polymers that won’t compromise the flavor or freshness of food, boosting consumer safety.
Overmolding Design Guide: What Factors Need To Be Considered?
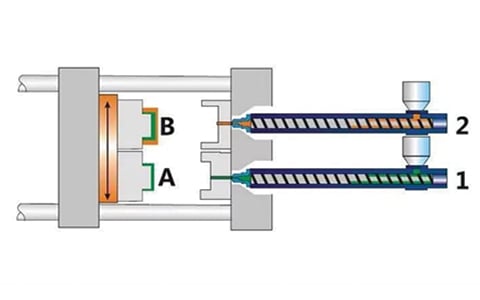
- Avoid edges that are too thin or that taper to a point. The adhesion between the substrate and overmolding may suffer during injection as a result of the flow slowing and subsequent cooling.
- Maintain a steady thickness for the overmolding: the overmolding should stay within the range of 1.5 to 3 millimeters (0.060 to 0.120 inches).
- Avoid sharp changes in thickness if you need portions of varying thicknesses, and smooth out surfaces as much as you can.
- Many overmolding materials are elastic, so you can add smooth bumpoffs into the design.
- Keep the overmolding layer thinner than the underlying substrate to assist prevent warping.
- In order to ensure good attachment in the overmolding cavity, take substrate shrinkage into consideration.
- Another important decision that must be made throughout the design phase is the choice of materials. A variety of materials can be used with overmolding. To obtain the desired qualities, the substrate is typically made of tougher plastic or a combination of plastics. Thermoplastic Elastomers (TPEs) are used most frequently for overmolding because they have good physical characteristics.
2k Molding Vs Overmolding
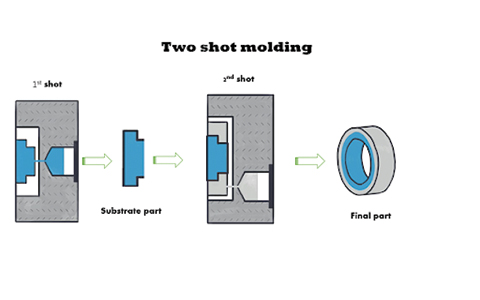
Plastic overmolding is the process of producing two different types of plastic parts in one (or two different colors of plastic parts in one solid part) using a standard single-nozzle injection molding machine. The over-molded process entails moving the first part (the substrate part) or melting inserts (insert molding) to the subsequent mold (the over-mold) and molding to obtain the final part.
Utilizing a 2K injection molding machine, 2K injection molding is the process of producing two or three different materials (colors) as one solid part. Although the molding process is complex, it is quick, effective, and of high quality, and 2K molding units are less expensive than plastic overmolding.
In comparison to plastic overmolding and 2K injection moulding, 2K injection moulding has higher quality and greater production efficiency; however, because the 2K injection moulding machine is more expensive, over-molding is occasionally used to replace it. However, plastic overmolding can be produced using any standard injection moulding machine, making it more cost-effective for low-volume, two-color moulding.
Co-molding Vs Overmolding
Overmolding is another name for co-molding. It speaks of the joining of two plastic materials, typically a hard material like ABS and a soft material like TPE. Nevertheless, depending on the melting temperature, two identically hard materials might be able to join together.
Overmolding Vs Insert Molding
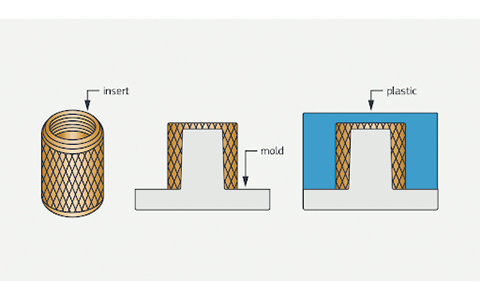
Injecting plastic into a mold that already has an insert in place is known as insert molding. This insert aids in the part’s shaping. The pre-placed insert inside the mold is the only distinction between insert moulding and regular injection moulding. This insert may be constructed from metal or a variety of plastic materials.
On the other hand, overmolding refers to the process of creating a single part or product from more than one material. Insert molding is shown in the portion of the figure above where the substrate is injected over the bolt. Overmolding, a technique for enhancing grip for parts, is the term for the additional rubber layer that is placed around the nail.
Conclusion
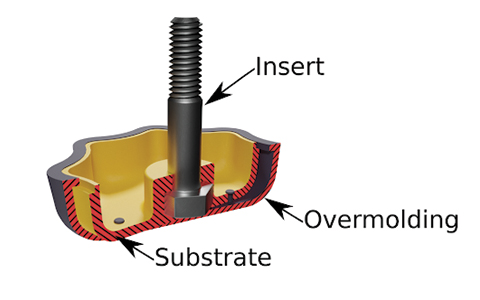
Overmolding can be a powerful tool in product design, but it necessitates extreme care and consideration when the design is being developed. Overmolding can increase expenses during the design and development stage, but it can also save long-term production costs and increase the value of the final product.
We have a team of experts at SeaSkyMedical who can assist you with including overmolding in both your design and manufacturing phases with the help of our overmolding factories, so be sure to contact us. If overmolding is too expensive for you, we are pleased to assist you to find an alternative route that will produce comparable results.