Plastic hollow objects can be produced using the moulding technique known as blow moulding. It uses heated, liquid material that is pressed under pressure into a mould cavity, just as in other moulding methods. However, blow moulding is a unique kind of moulding that makes use of the characteristics of conventional glassblowing and abs molding.
What is Blow Moulding?
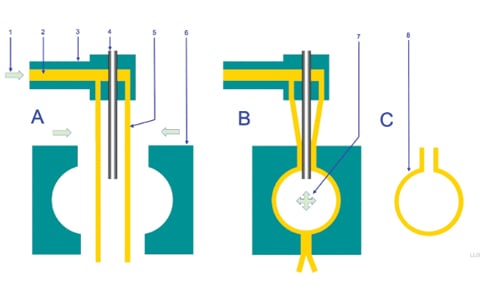
A hollow object is created by the blowing of hot plastic into a mould cavity during the moulding process known as blow moulding, also known as blow moulding in the UK. The employment of a blow moulding to produce hollow things is its distinctive feature. After being heated, raw plastic is turned into a parison. The top of the mould is then fastened with the plastic parison. The plastic parison was then stretched across the inside walls of the mould chamber by air being forced down onto it.
Types of Blow Moulding
The many types of blow moulding are numerous.
Extrusion Moulding
Blow moulding by extrusion can be continuous or sporadic. A parison will be continuously supplied into the mould during continuous extrusion blow moulding, and each form will be cut off with a blade as it forms. The new plastic is fed into the mould only after the old plastic has been ejected in intermittent extrusion blow moulding. Each new plastic is released from the metal mould when it has cooled.
Extrusion blow moulds may be made in much less time and are typically far less expensive than injection blow moulds. For shorter runs, extrusion blow moulding is ideal. Shorter production times and lower tooling costs are advantages; on the other hand, poorer control over wall thickness and a higher level of scrap is typically negatives.
Spin Trimming
Due to the nature of the moulding process, products frequently have extra material that must be removed by rotating a knife around the container and cutting the excess material away. After that, the extra plastic is recycled to make new mouldings.
PVC, HDPE, and PE+LDPE are just a few of the materials that can be cut with spin trimmers. Different types of materials’ physical properties have an impact on trimming. Amorphous material mouldings are substantially more challenging to trim than crystalline material mouldings. Blades with titanium coatings have a longer lifespan than those made of regular steel.
Injection Blow Moulding
The least frequently utilised of the three blow moulding techniques is injection blow moulding. IBM is used to mass-produce hollow plastic (or glass) objects, usually single-serve and miniature medical bottles. Three steps make up the procedure: injection, blowing, and ejection. A polymer is first injected onto a core pin, which is then rotated to a blow moulding station where it is inflated and chilled.
An extruder barrel and screw assembly used in the injection blow moulding machine melts the polymer. The molten polymer is injected through nozzles into a heated cavity and core pin after being supplied into a hot runner manifold. The preform’s internal shape is created by a core rod that is clamped around the cavity mould, which creates the outward shape. The preform resembles a test tube with a threaded neck because it comprises of a fully formed bottle or jar neck with a thick polymer tube connected that will serve as the body.
The core rod turns and clamps into the hollow, cooled blow mould as the preform mould opens. The core rod’s open end allows compressed air to enter the preform, inflating it to the shape of the finished product. The blow mould opens and the core rod rotates to the ejection position following a cooling period. The final product is removed from the core rod and, if desired, is leak-tested before being packaged. Depending on the size of the needed output and the number of cavities, the preform and blow mould might contain anywhere from three to sixteen cavities. Three different sets of core rods enable simultaneous preform injection, blow moulding, and ejection.
Often with the help of cleanroom injection molding several laboratory consumables, pet injection molding etc are done which is highly used by medical device component manufacturers and several medical contract manufacturing companies.
Injection Stretch Blow Moulding
Bottles for soda are often made using an injection stretch blow moulding process. An injection-moulded component is used to start the process. Typically, a stretch blow moulding machine uses pre-heating, stretching in the axial direction, and blowing to give the product its final shape.
Once more divided into three-station and four-station machines are single-stage processes. The plastic is initially moulded into a “preform” using the injection moulding technique in the two-stage injection stretch blow moulding procedure. The bottles’ necks, complete with threads (the “finish”) on one end, are used to create these preforms.
What is The Blow Moulding Process?
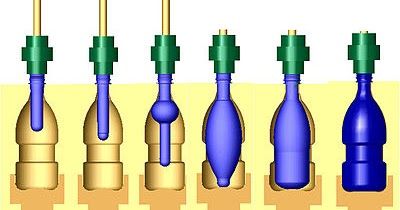
Here, we’ll go over the basic blow moulding procedure. The steps in the process of blow moulding are melting, homogenising, extruding, moulding (blowing), cooling, and ejection. Additional procedures can be used by various manufacturing facilities, such as synthesising chemicals and colourants and adding additional cooling or heating cycles. These additional procedures are influenced by the final product’s design and intended use.
- Plastic feeding: Also known as charging, is the initial step in the blow moulding process. The plastic pellets are transported into the extruder hopper to do this. Pellets are transferred into the raw material silos or hoppers by vacuum pumps after being drawn from large bags or bulk containers. The rate of feeding into the plastifier or extruder is managed by a rotary feeder at the bottom of the silo.
- Plasticizing or Melting: The plastic resin is continuously heated and kneaded as it enters and travels through the extrusion machine. To supply heat for melting the polymer, electric heating elements or heating bands are wrapped around the extruder barrel. The many portions of the extruder screw each have a distinct function. These include metering, feeding, and compressing. The extruder screw is made to offer adequate shearing and compression so that the plastic can be homogenised and extruded.
- Preform Injection or Parison Extrusion: This procedure prepares the preform or parison for inflation. This is accomplished by injecting or free-extruding the plastic into a preform mould.
- Sealing or Clamping: In sealing or clamping, the preform is captured by a split die. With the exception of one hole, often the container entrance, where compressed air will be supplied, the ends of the parison (extrusion blow moulding) are sealed.
- The plastic is given shape during this stage through inflation or blow moulding. In the preform, compressed air is added. This expands the preform until it is moulded to the die’s profile.
- Ejecting and chilling: The cooling procedure comes next. Usually, as soon as the plastic contacts the die, it begins to cool at a set rate, stabilising the product’s dimensions. The mould opens and releases the product after cooling.
- Trimming: In extrusion blow moulding, flashing is typically visible. As the dies grip the preform, the majority of blow moulding machines offer auto deflashing features. Flash, however, can occasionally be seen at the top and bottom of the product, particularly at the orifice where compressed air is introduced. A spinning knife trims this extra material.
- The standard quality control procedure used in the production of bottles or packaging materials is the leak test. Either vacuum or compression is created inside the container during this process. The gadget will then monitor the pressure to see if the air is getting into or getting out of the container. If the container detects a leak, the signal is rejected and transmitted back into the system.
What Type of Plastic is Used in Blow Moulding?
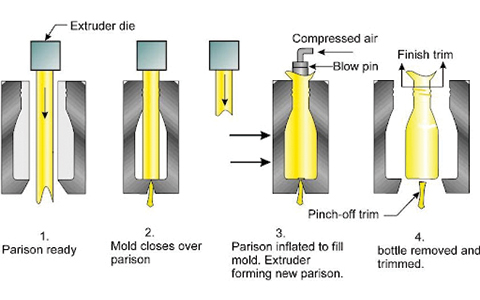
Polyethylene (High Density, Low Density, and Linear Low Density), Polypropylene, Polyethylene-Terephthalate (PET), and PVC are among the materials used in blow moulding.
- Polyethylene: The most used blow moulding material is polyethylene. Numerous favourable qualities of polyethylene include its low cost, ease of processing, toughness, and flexibility that are maintained even at low temperatures, lack of odour and toxins, outstanding clarity, good water barrier capabilities, and electrical insulation properties. High-density polyethylene (HDPE) and low-density polyethylene are its two primary varieties (LDPE).
- High-density Polyethylene (HDPE): In terms of market share, HDPE is the type of polyethylene that is most prevalent as a raw material. Because of its linear molecule structure and lack of branching, it has stronger intermolecular forces. HDPE’s high specific strength is a result of this.
- Low-density Polyethylene (LDPE): The intermolecular forces in LDPE, which comprises a branching polymer chain, are weak. Lower barrier qualities and tensile strength are the results of this. It nonetheless outperforms HDPE in terms of impact strength and resilience.
- Polyethylene Terephthalate (PET): PET, more precisely biaxially oriented PET, is a polymer recognised for having a low carbon dioxide permeability. This makes the substance desirable for use in the manufacture of carbonated beverage bottles. PET’s affinity for water, however, is a drawback of the technology. As a result, the processing is challenging since the resin needs to be dried before extrusion. It has a tendency to absorb water.
- Polypropylene (PP) is a polymer whose molecular weight, shape, crystalline structure, additives, and copolymerization can result in a wide range of properties. It can be used to create polymers with a high degree of crystallinity, which results in materials that are harder and have a tensile strength that is comparable to HDPE. They can also sustain higher temperatures without weakening or degrading. The use of PP has drawbacks due to its oxidation and UV degradation vulnerability.
- Another adaptable material is polyvinyl chloride (PVC), which can be made with a variety of stabilisers, plasticizers, impact reducers, processing aids, and other additives. By changing the number of plasticizers, they can be transformed into hard or flexible plastics. Additionally, they provide greater clarity than other multipurpose plastics like PP. PVCs can, however, produce poisonous poisons, acids, and pollutants when being processed or degraded. FDA, EPA, and other bodies are now regulating its compounded ingredients.
- Nylon or Polyamide (PA): Polyamide is a type of engineering plastic that has high levels of toughness, impact resistance, solvent resistance, strong abrasion resistance, and the ability to be changed to have high levels of heat resistance. The majority of PA output is used to make fibres. The volume of PA produced is only utilised in plastic forming operations to the extent of roughly 10%. Blow-molded PA is frequently used for gasoline tanks and automotive parts.
- Polycarbonate (PC): The most widely used moulding techniques for polycarbonate are injection moulding and sheet extrusion. Bottle manufacture is the typical use in blow moulding. High impact strength, heat resistance, superior electrical insulation, transparency, good water barrier qualities, and intrinsic flame retardancy are all attributes of polycarbonates.
- Copolyesters are substances that exhibit exceptional clarity, great thermal oxidation stability, built-in flame resistance, chemical inertness, and favourable mechanical qualities. It may be quickly moulded into containers with thin walls. It is also moldable because to its inherent lubricity and non-stick qualities.
- COC – Cyclic Olefin Copolymer: The COC family of totally amorphous polymer resins is sought after because it has qualities similar to PVC without the drawbacks. Due to its low water vapour permeability, it is most suitable for the fabrication of food packaging, pharmaceutical bottles, and vials. The creation of particular polyolefin blends can change the characteristics of COC. Its elasticity, transparency, vapour transmission rate, and coefficient of friction are a few of the characteristics that are modifiable.
- Acrylonitrile Butadiene Styrene (ABS) is a common plastic with good stiffness and hardness as well as some degree of toughness. They can have a very good surface polish when blow moulded, making them appropriate for the production of consumer items. Due to their inadequate resistance to most acids and alkalis and low resistance to UV, protective coatings are typically used.
What is Blow Moulding Used For?
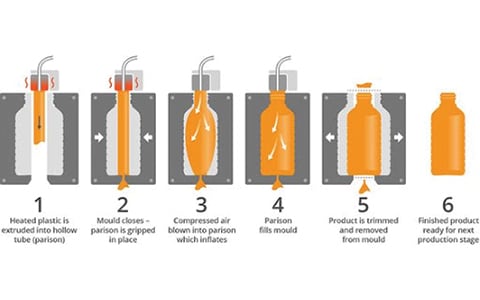
Blow moulding is a technique that can be used to create nearly any hollow plastic container; however, it is not just applicable to bottles. Here are a few items that are frequently blow-molded:
- Stadium seating
- coolers
- fan housing
- construction barriers
- toys and sporting goods
- watering troughs
The design and mass manufacture of auto parts are made simple and affordable by the use of blow moulding, which is also widely employed in the automotive sector. These are hugely used in medical molding companies also. Here are a few typical automotive blow-molded components:
- Liquid Reservoirs
- Consoles
- Storage Systems
- Mud Guards
- Fenders
- Automotive Ductwork
- Seating
- Paneling
- Electrical Covers
In conclusion, blow moulding offers a wide range of applications and is an excellent technique to make a big number of parts at a low cost.
Advantages/ Features of Blow Moulding

The blow moulding process has a lot of benefits over other ways to make plastic products, which is why it is greatly used by medical plastic manufacturers as well.
- Injection moulding is more expensive, whereas blow moulding is more affordable because both manufacturing and equipment are often less expensive.
- Products that are made from a single piece operate well with blow moulding. It can create objects that don’t need to be put together or have their halves connected. In light of this, outside threading is particularly effective for containers.
- Flash is also lessened by blow moulding. Flash refers to the tiny plastic bleeds or bursts that appear around product seams. Before an item can be transported, more finishing work is needed to sand off or remove the surplus plastic from the manufacturing process. Faster turnaround times for blow-molded products are achieved via blow moulding procedures that produce little or no flash.
- This technology is constantly evolving in order to produce plastic on a global scale. Manufacturers are now able to create larger quantities in a shorter amount of time because to the huge boost in manufacturing capability that has been made possible. A production cycle has been sped up by using equipment that supports 3D moulding.
- When the Japanese Placo X-Y machine was created, it was elevated to new heights and gave rise to 3D blow moulding. This is essentially an automated production technology that allows for minimal flash (extra polymer around the material), seamless part inclusion, and faster production because of the accurate receptacle it provides.
Disadvantages of Blow Moulding
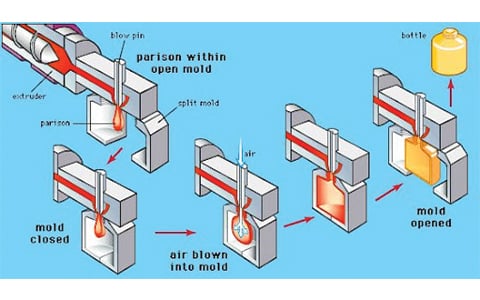
- The blow moulding industry, like the gas industry, depends on millions of gallons of petroleum to be able to manufacture plastic goods. Since oil is a crucial component of thermoplastics, which are becoming mechanised and more streamlined, the technology has turned into a persistent danger to the world’s declining oil supply.
- This technology is essential to the production of polymers and is heavily reliant on petroleum. Because of this, there is a significant risk of environmental harm. In addition to contributing to the depletion of oil reserves, it produces plastic that does not biodegrade. Although it can enhance plastic output, it cannot eliminate the threats to the environment that it poses.
- Even though this technology employs a variety of production techniques, it has drawbacks. We must eliminate correspondence from the process because it would require additional resources and could not be streamlined.
- Only hollow shapes, such as bottles and plastic containers, can be blown moulded. Although it would have less applications, the air pressure is likewise crucial to the process. For instance, it will struggle with wall thickness, which is tough to control.
- Although this technology currently only produces hollow forms in large quantities, it already makes use of automation. It can result in material being wasted when manufacturing containers with certain dimensions because thickness should be accurate. Even when thermoplastic is stretched to conserve material, this practise can result in subpar goods.
Blow Moulding Design: What Factors Need To Be Considered?
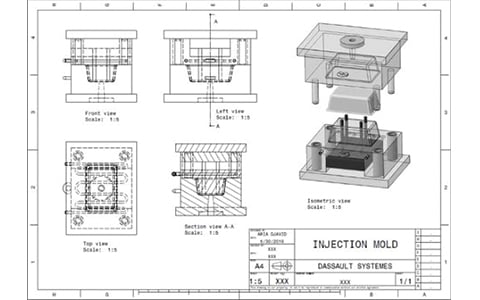
Although there are tens of thousands of designers that create parts for blow moulders, there is a small elite group inside this vast industry. Before all the parts are finally documented and given to a moulder for manufacturing, the design of a blow-molded object goes through several stages of development. The most crucial stage of development occurs at this point since it is the last opportunity for design adjustments or improvements to be made without drastically increasing project costs or delaying it.
- Steel safe areas
- Secondary operations and fixtures
- Texturing and draft
- Gate location
- Scheduling of critical start-up phases
- Sink marks
- Critical tolerances
- Material options and consequences
- Draft angle orientation
- Shut-off angles
Since choosing a moulder is frequently delayed until the design is finished and released for official quoting by the purchasing department, it can be challenging for designers and engineers to establish this relationship early in the design process. Additionally, a lot of moulders won’t offer any suggestions unless they are certain they will be given the assignment.
Due to the impasse, designers are unable to implement these suggestions, which frequently causes unacceptably long delays or cost overruns due to complicated tooling or lengthy cycle times. Long-term cost effectiveness is compromised by these regulations’ severe negative effects on product development efficiency.
Rotational Molding vs Blow Moulding
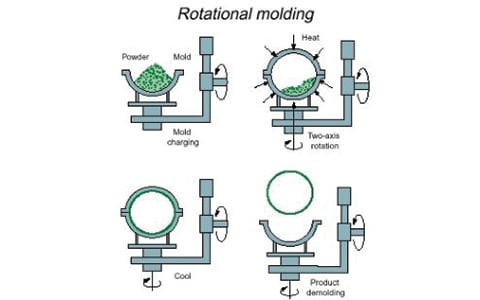
Both blow moulding and rotational moulding are frequently used techniques for producing hollow plastic objects, however, the two techniques differ greatly from one another. Despite the fact that they frequently yield outcomes that are comparable, blow moulding is frequently a preferable option due to changes in the procedures.
- Cost: Rotational moulds need to be replaced frequently whereas blow moulding uses moulds that last for a long time. Rotational moulding can be more expensive over the course of several years, solely in terms of tooling, than blow moulding. If you use blow moulding, you can make a lot more products for the same expenditure thanks to its considerably faster rate.
- Time: Rotational moulding takes a long time to complete. Occasionally, a single station will only create two items per hour. With blow moulding, you can accomplish a lot more without sacrificing quality.
- Weight: Rotationally moulded items are frequently significantly heavier than their blow-molded equivalents as a result of the manufacturing method.
- Void: The final project’s porousness is another effect of the rotational moulding model. Although it is intended to keep the mould moving until every wall is equally coated, in reality, this is not achievable, leading to minute perforations in the finished product. This issue is avoided by blow moulding, which creates the entire component from a single, precisely sized plastic tube.
- Productivity: The production of blow moulding is at least 5-8 times more than that of rotomolding. For a 2000L tank, it might be able to make 8–9 pieces every hour. HDPE is typically used in blow moulding as the material. previously moulding The blow moulding method is efficient and quick. The object has finished moulding. The performance and internal quality are consistent. The output of a 2000L tank of rotomolding is only 1-2 pieces per hour. Additionally, the rotomolding material needs to be crushed and pulverised. There is a lengthier processing cycle. increase cost Therefore, mass production is not appropriate for it. Additionally, there are fewer plastic materials available.
For the majority of items, particularly in high-volume runs, we advise blow moulding over rotational moulding due to its numerous significant benefits. A long lifespan, wearability, strength, durability, good impact resistance, good low-temperature resistance, etc. are additional benefits of blow-moulded items.
Conclusion
The art of glass blowing, in which a craftsman heated the glass to its melting point and then blew air through a tube to inflate it, is where the origins of blow moulding may be found. As far back as the 1800s, this method has been in use. Using celluloid polymer in the method is depicted in a patent from the era. These primitive techniques weren’t appropriate for mass production.
They created industrial equipment for the production of blow-molded bottles in the 1930s, enabling mass production. With the development of low and high-density polyethylene, blow moulding surged into industrial predominance. The soft drink bottling industry and the car industry were two of the many industries that underwent a transformation as a result.Apart from blow molding, plastic injection molding is also popular, if you want the best-in-class injection molding products then contact us.